2024 IECC Residential Proposed Changes — original pdf
Backup
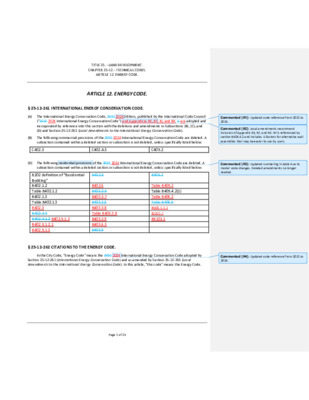
TITLE 25. - LAND DEVELOPMENT. CHAPTER 25-12. - TECHNICAL CODES. ARTICLE 12. ENERGY CODE. ARTICLE 12. ENERGY CODE. § 25-12-261 INTERNATIONAL ENERGY CONSERVATION CODE. (A) The International Energy Conservation Code, 2021 2024 Edition, published by the International Code Council ("2021 2024 International Energy Conservation Code") and Appendices RE, RF, RJ, and RK, is are adopted and incorporated by reference into this section with the deletions and amendments in Subsections (B), (C), and (D) and Section 25-12-263 (Local Amendments to the International Energy Conservation Code). (B) The following commercial provisions of the 2021 2024 International Energy Conservation Code are deleted. A subsection contained within a deleted section or subsection is not deleted, unless specifically listed below: Commented [A1]: Updated code reference from 2021 to 2024. Commented [A2]: Local amendments recommend inclusion of Appendix RE, RF, and RK. RF is referenced by section R405.4.2 and includes U-factors for alternative wall assemblies that may be easier to use by users. C402.3 C402.4.3 C405.2 (D) The following residential provisions of the 2021 2024 International Energy Conservation Code are deleted. A subsection contained within a deleted section or subsection is not deleted, unless specifically listed below: R402.5 R405.2 Commented [A3]: Updated numbering in table due to model code changes. Deleted amendments no longer needed. R202 definition of "Residential Building" R402.1.2 Table R402.1.2 R402.1.3 Table R402.1.3 R402.3 R402.4.4 R402.4.1.2 R402.5.1.2 R402.5.1.2.1 R402.5.1.3 R402.6 R403.3.5 R403.3.7 R403.3.6 R403.3.8 Table R403.3.8 R403.3.9 R403.6.3 R403.9 § 25-12-262 CITATIONS TO THE ENERGY CODE. Table R405.2 Table R405.4.2(1) Table R406.2 Table R406.5 R503.1.1.1 RJ101.1 RK101.1 In the City Code, "Energy Code" means the 2021 2024 International Energy Conservation Code adopted by Section 25-12-261 (International Energy Conservation Code) and as amended by Section 25-12-263 (Local Amendments to the International Energy Conservation Code). In this article, "this code" means the Energy Code. Commented [A4]: Updated code reference from 2021 to 2024. Page 1 of 25 § 25-12-263 LOCAL AMENDMENTS TO THE INTERNATIONAL ENERGY CONSERVATION CODE. (C) The following provisions are local amendments to the residential provisions to the 2021 2024 International Energy Conservation Code. Each provision in this subsection is a substitute for an identically numbered provision deleted by Section 25-12-261(D) or an addition to the Energy Code. Commented [A5]: Updated code reference from 2021 to 2024. Commented [A6]: Updated to align number of stories with R202 General Definitions. Residential Buildings. R101.2 Scope. This code applies to the design and construction of detached one- and two-family dwellings and multiple single-family dwellings (townhouses) and Group R-2, R-3 and R-4 buildings three four stories or less in height above grade plane. R201.3 Terms defined in other codes. Terms not defined in this code that are defined in the Building Code, Electrical Code, Fire Code, Mechanical Code, the Plumbing Code, Residential Code, and Chapter 25-12, Article 3 (Flood Hazard Areas) have the meaning ascribed to them as in those codes. R202 General Definitions. Residential Building. For this code, includes detached one- and two-family dwellings and multiple single-family dwellings (townhouses) as well as Group R-2, R-3 and R-4 buildings four stories or less in height above grade plane. R302.2 Exterior Design Conditions. The design parameters in Table 302.2 shall be used for calculations under this code. TABLE R302.2 EXTERIOR DESIGN CONDITIONS CONDITION VALUE Wintera , Design Dry-bulb (°F) 30 Summera , Design Dry-bulb (°F) 100 Summera , Design Wet-bulb (°F) 74 Climate Zone 2A For SI: deg C=[(°F)-32]/1.8 a Adjustments shall be permitted to reflect local climates, which differ from the tabulated temperatures, or local weather experience determined by the building official. R402.1.2 Insulation and fenestration criteria. The building thermal envelope shall meet the requirements of Table R402.1.2(1) for existing buildings and Table R402.1.2(2) for new construction. Assemblies shall have a U-factor or F-factor equal to or less than that specified in Table R402.1.2(1) for existing buildings and Table R402.1.2(2) for new construction. Fenestration shall have a U-factor and glazed fenestration SHGC equal to or less than that specified in Table R402.1.2(1) for existing buildings and Table R402.1.2(2) for new construction. Commented [A7]: Updated to match model code update to include F-factors for slab foundations. TABLE R402.1.2(1) MAXIMUM ASSEMBLY U-FACTORSa,b AND FENESTRATION REQUIREMENTS FOR EXISTING BUILDINGS Commented [A8]: 2024 IECC model code updated table format from horizontal to vertical. CLIMA TE ZONE FENESTRA TION U- FACTOR SKYLIG HT U- FACTO R GLAZED FENESTRA TION SHGCd CEILI NG U- FACT OR ATTIC ROOFLI NE U- FACTO R MASS WALL U- FACT ORc FLOO R U- FACT OR BASEM ENT WALL U- FACTOR CRA WL SPAC E WALL U- FACT OR WOO D FRA ME WALL U- FACT OR Page 2 of 25 2 0.40 0.60 0.25 0.045 0.165 0.06 0.36 0.477 0.02 6 0.07 5 4 a The values in this table apply to additions having an area no more than 40% of the existing construction. b Non-fenestration U-factors shall be obtained from measurement, calculation or an approved source. c Mass walls shall be in accordance with Section R402.2.5. Where more than half the insulation is on the interior, the mass wall U-factors shall not exceed 0.14 in Climate Zone 2. d The SHGC row applies to all glazed fenestration. Exception: In Climate Zone 2, skylights shall be permitted to be excluded from glazed fenestration SHGC requirements provided that the SHGC for such skylights does not exceed 0.30. CLIMATE ZONE VERTICAL FENESTRATION U-FACTOR SKYLIGHT U-FACTOR GLAZED VERTICAL FENESTRATION SHGC SKYLIGHT SHGC CEILING U-FACTOR ATTIC ROOFLINE U-FACTOR WOOD FRAME WALL U-FACTOR MASS WALL U-FACTOR c FLOOR U-FACTOR BASEMENT WALL U-FACTOR d UNHEATED SLAB F-FACTOR e HEATED SLAB F-FACTOR e CRAWL SPACE U-FACTOR For SI: 1 foot = 304.8 mm. a The values in this table apply to additions having an area no more than 40% of the existing construction. b Non-fenestration U-factors and F-factors shall be obtained from measurement, calculation or an approved source. c Mass walls shall be in accordance with Section R402.2.6. Where more than half the insulation is on the interior, the mass wall U-factors shall not exceed 0.14 in Climate Zone 2. d In Warm Humid locations as defined by Figure R301.1 and Table R301.1, the basement wall U-factor shall not exceed 0.360. e F-factors for slabs correspond to the R-values of Table R402.1.3(1) and the installation conditions of Section R402.2.10.1. 2 0.40 0.60 0.25 0.28 0.026 0.030 0.045 0.075 0.165 0.064 0.360 0.73 0.74 0.477 Commented [A9]: 2024 IECC model code amended Ceiling U-factor to reflect associated change in R-value from R49 to R38. Local amendment made to mirror that change. Commented [A10]: 2024 IECC model code added additional assembly requirement for “Insulation Entirely Above Roof Deck.” Local amendment already exists for this assembly in “Attic Roofline” insulation, which includes above and below deck insulation R-value. No change is recommended for the existing local amendment for the U- factor to allow for above and below deck differences. TABLE R402.1.2(2) MAXIMUM ASSEMBLY U-FACTORS AND FENESTRATION REQUIREMENTS FOR NEW CONSTRUCTIONa CLIM ATE ZONE FENESTRA TION U- FACTOR SKYLI GHT U- FACT OR GLAZED FENESTRA TION SHGCd CEILI NG U- FACT OR ATTIC ROOFL INE U- FACTO R WO OD FRA ME WAL L U- FLOO R U- FACT OR MASS WALL U- FACT ORb BASEM ENT WALL U- FACTO R CRA WL SPAC E WAL L U- Commented [A11]: 2024 IECC model code updated table format from horizontal to vertical. Commented [A12]: Table name updated to align with model code. Page 3 of 25 0.02 6 FACT OR 0.06 6 4 FACT OR 0.47 7 2 0.35 0.60 0.25 0.045 0.165 0.06 0.36 a Non-fenestration U-factors shall be obtained from measurement, calculation or an approved source. b Mass walls shall be in accordance with Section R402.2.5. Where more than half the insulation is on the interior, the mass wall U-factors shall not exceed 0.14 in Climate Zone 2. c The SHGC row applies to all glazed fenestration. Exception: In Climate Zone 2, skylights shall be permitted to be excluded from glazed fenestration SHGC requirements provided that the SHGC for such skylights does not exceed 0.30. CLIMATE ZONE VERTICAL FENESTRATION U-FACTOR SKYLIGHT U-FACTOR GLAZED VERTICAL FENESTRATION SHGC SKYLIGHT SHGC CEILING U-FACTOR ATTIC ROOFLINE U-FACTOR WOOD FRAME WALL U- FACTOR b MASS WALL U-FACTOR FLOOR U-FACTOR BASEMENT WALL U- FACTOR c UNHEATED SLAB F-FACTOR d HEATED SLAB F-FACTOR d CRAWL SPACE U-FACTOR For SI: 1 foot = 304.8 mm. 0.28 0.026 0.030 0.045 0.066 2 0.35 0.60 0.25 0.165 0.064 0.360 0.73 0.74 0.477 a Non-fenestration U-factors and F-factors shall be obtained from measurement, calculation, or an approved source or Appendix RF where such appendix is adopted or approved. b Mass walls shall be in accordance with Section R402.2.6. Where more than half the insulation is on the interior, the mass wall U-factors shall not exceed 0.14 in Climate Zone 2. c In Warm Humid locations as defined by Figure R301.1 and Table R301.1, the basement wall U-factor shall not exceed 0.360. d F-factors for slabs correspond to the R-values of Table R402.1.3(2) and the installation conditions of Section R402.2.10.1. R402.1.3 R-value alternative. Assemblies with R-value of insulation materials equal to or greater than that specified in Table R402.1.3(1) for existing buildings and Table R402.1.3(2) for new construction shall be an alternative to the U-factor or F-factor in Table R402.1.2(1) for existing buildings and Table R402.1.2(2) for new construction, respectively. Commented [A15]: Updated to match model code update to include F-factors for slab foundations. TABLE R402.1.3(1) INSULATION MINIMUM R-VALUES AND FENESTRATION REQUIREMENTS BY COMPONENTa,b FOR EXISTING BUILDINGS Commented [A16]: 2024 IECC model code updated table format from horizontal to vertical. Page 4 of 25 Commented [A13]: 2024 IECC model code amended Ceiling U-factor to reflect associated change in R-value from R49 to R38. Local amendment made to mirror that change. Commented [A14]: 2024 IECC model code added additional assembly requirement for “Insulation Entirely Above Roof Deck.” Local amendment already exists for this assembly in “Attic Roofline” insulation, which includes above and below deck insulation R-value. No change is recommended for the existing local amendment for the U- factor to allow for above and below deck differences. CLIM ATE ZONE FENESTR ATION U- FACTORc SKYLI GHT U- FACTO Rc FLOO R R- VALU E BASE MENT WALL R- VALUE SLAB R- VALUE & DEPTH CRAWL SPACE WALL U- FACTOR 2 0.40 0.60 49 13 0 0 0 GLAZE D FENEST RATIO N SHGCc 0.25 CEILIN G R- VALUE d,g ATTIC ROOFLIN E R- VALUEd,g 25&0ci or 0&20ci MAS S WALL R- FACT ORh 4/6 WOOD FRAME WALL R- VALUEe ,f 15, 13&2ci, or 0&10ci a The values in this table apply to repairs, renovations, or additions that increase the conditioned floor area by no more than 40 percent. All other construction shall use the values for new construction in Table R402.1.3(2). b R-values are minimums. U-factors and SHGC are maximums. When insulation is installed in a cavity which is less than the label or design thickness of the insulation, the installed R-value of the insulation shall not be less than the R-value specified in the table. c The fenestration U-factor row excludes skylights. The SHGC row applies to all glazed fenestration. Exception: Skylights may be excluded from glazed fenestration SHGC requirements in Climate Zones 2 where the SHGC for such skylights does not exceed 0.30. d Air-impermeable insulation of R-25&0 or greater may be used if mechanical equipment and air distribution system are located entirely within the building thermal envelope. "Air-impermeable" shall be defined as having an air permeance not exceeding 0.02 L/s-m2 at 75 Pa pressure differential tested according to ASTM E 2178 or ASTM E 283. e First value is cavity insulation, the second value is continuous insulation (ci) or insulated siding. Therefore, as an example, "13&2ci" means R-13 cavity insulation plus R-2 continuous insulation or insulated siding. Where R-13&2ci is used, non- insulated structural sheathing shall cover no more than 25% of the exterior. f Total-fill cavity insulation will be deemed as meeting the R-15 requirement. g R-0&20ci continuous insulation can be used where the insulation is completely above the roof framing and sub-roofing. h Mass walls shall be in accordance with Section R402.2.5. The second R-value applies where more than half of the insulation is on the interior of the mass wall. CLIMATE ZONE 2 0.40 0.60 0.25 0.28 49 38 25&0ci or 0%20ci 0&25ci 15, 13&2ci, or 0&10ci 4/6 13 OR 7&5ci or 0&10ci 0 0 R-5ci edge and R-5 full slab 0 VERTICAL FENESTRATION U-FACTOR SKYLIGHT U-FACTOR GLAZED VERTICAL FENESTRATION SHGC SKYLIGHT SHGC CEILING R-VALUE ATTIC ROOFLINE R-VALUE c,d,g,h,i WOOD FRAME WALL R-VALUE c,d,g MASS WALL R-VALUE j i FLOOR R-VALUE c, d BASEMENT WALL R-VALUE f UNHEATED SLAB R-VALUE & DEPTH e HEATED SLAB R-VALUE & DEPTH c,d,e CRAWL SPACE WALL R-VALUE c,d For SI: 1 foot = 304.8 mm NR = Not Required. ci = continuous insulation. a The values in this table apply to repairs, renovations, or additions that increase the conditioned floor area by no more than 40 percent. All other construction shall use the values for new construction in Table R402.1.3(2). b R-values are minimums. U-factors and SHGC are maximums. When insulation is installed in a cavity which is less than the label or design thickness of the insulation, the installed R-value of the insulation shall not be less than the R-value specified in the table. c “5ci or 13” means R-5 continuous insulation (ci) on the interior or exterior surface of the wall or R-13 cavity insulation on the interior side of the wall. "10ci or 13" means R-10 continuous insulation (ci) on the interior or exterior surface of the wall or R-13 cavity insulation on the interior side of the wall. "15ci or 19 or 13&5ci" means R-15 continuous insulation (ci) Page 5 of 25 Commented [A17]: 2024 IECC model code amended R- value from R49 to R38. Local amendment made to mirror that change. Commented [A18]: 2024 IECC model code added additional assembly requirement for “Insulation Entirely Above Roof Deck.” Local amendment already exists for this assembly in “Attic Roofline” insulation, which includes above and below deck insulation R-value. Local amendment made to mirror change in above deck R-value. Commented [A19]: Local amendment deleted as no longer needed. TABLE R402.1.3(2) INSULATION MINIMUM R-VALUES AND FENESTRATION REQUIREMENTS BY COMPONENTa FOR NEW CONSTRUCTION Commented [A20]: 2024 IECC model code updated table format from horizontal to vertical. on the interior or exterior surface of the wall; or R-19 cavity insulation on the interior side of the wall; or R-13 cavity insulation on the interior of the wall in addition to R-5 continuous insulation on the interior or exterior surface of the wall. d The first value is cavity insulation, the second value is continuous insulation (ci) or insulated siding. Therefore, as an example, "13&2ci" means R-13 cavity insulation plus R-2 continuous insulation or insulated siding. Where R-13&2ci is used, non-insulated structural sheathing shall cover no more than 25% of the exterior. e Slab insulation shall be installed in accordance with Section R402.2.10.1. f Basement wall insulation is not required in Warm Humid locations as defined by Figure R301.1 and Table R301.1. g Total-fill cavity insulation will be deemed as meeting the R-15 requirement. h g Air-impermeable insulation of R-25&0 or greater may be used if mechanical equipment and air distribution system are located entirely within the building thermal envelope. "Air-impermeable" shall be defined as having an air permeance not exceeding 0.02 L/s-m2 at 75 Pa pressure differential tested according to ASTM E 2178 or ASTM E 283. i h R-0&25ci continuous insulation can be used where the insulation is completely above the roof framing and sub-roofing. j i Mass walls shall be in accordance with Section R402.2.6. The second R-value applies where more than half of the insulation is on the interior of the mass wall. CLIMA TE ZONE FENESTRA TION U- FACTORb SKYLIG HT U- FACTO Rb GLAZED FENESTRA TION SHGCb CEILIN G R- VALUE d,g FLOOR R- VALUE MASS WALL R- VALUE h BASEM ENT WALL R- VALUE SLAB R- VALUE & DEPTH c CRA WL SPAC E WALL R- VALU E 0 ATTIC ROOFL INE R- VALUE d,g 25&0ci or 0&20ci WOOD FRAM E WALL R- VALUE e,f 19, 15&2ci , 13&3ci , or 0&15ci 2 0.35 0.60 0.25 49 4/6 13 0 0 a R-values are minimums. U-factors and SHGC are maximums. When insulation is installed in a cavity which is less than the label or design thickness of the insulation, the installed R-value of the insulation shall not be less than the R-value specified in the table. b The fenestration U-factor column excludes skylights. The SHGC column applies to all glazed fenestration. Exception: Skylights may be excluded from glazed fenestration SHGC requirements in Climate Zone 2 where the SHGC for such skylights does not exceed 0.30. c R-5 insulation shall be provided under the full slab area of a heated slabs in addition to the required slab-edge insulation R-value for slabs as indicated in the table. The slab edge insulation for heated slabs shall not be required to extend below the slab. d Air-impermeable insulation of R-25 or greater may be used if mechanical equipment and air distribution system are located entirely within the building thermal envelope. "Air-impermeable" shall be defined as having an air permeance not exceeding 0.02 L/s-m2 at 75 Pa pressure differential tested according to ASTM E 2178 or ASTM E 283. e First value is cavity insulation, the second value is continuous insulation (ci) or insulated siding, so "13&5ci" means R-13 cavity insulation plus R-5 continuous insulation or insulated siding and "10ci" means R-10 continuous insulation. Where R- 15&2ci or R-13&3ci is used, non-insulated structural sheathing shall cover no more than 25% of the exterior. f Total-fill cavity insulation in a 2x4 wall will be deemed as meeting the R-15 requirement. g R-0&20ci continuous insulation can be used where the insulation is completely above the roof framing and subroofing. h Mass walls shall be in accordance with Section R402.2.5. The second R-value applies where more than half of the insulation is on the interior of the mass wall. CLIMATE ZONE VERTICAL FENESTRATION U-FACTOR SKYLIGHT U-FACTOR GLAZED VERTICAL FENESTRATION SHGC 2 0.35 0.60 0.25 Page 6 of 25 0.28 49 38 25&0ci or 0%20ci 0&25ci 19, 15&2ci, 13&3ci, or 0&15ci 4/6 13 OR 7&5ci OR 0&10ci 0 0 R-5ci edge and R-5 full slab 0 SKYLIGHT SHGC CEILING R-VALUE ATTIC ROOFLINE R-VALUE b,c,f,g,h WOOD FRAME WALL R-VALUE b,c,f MASS WALL R-VALUE h i FLOOR R-VALUE b,c BASEMENT WALL R-VALUE b,e UNHEATED SLAB R-VALUE & DEPTH d HEATED SLAB R-VALUE & DEPTH b,c,d CRAWL SPACE WALL R-VALUE b,c For SI: 1 foot = 304.8 mm NR = Not Required. ci = continuous insulation. a R-values are minimums. U-factors and SHGC are maximums. When insulation is installed in a cavity which is less than the label or design thickness of the insulation, the installed R-value of the insulation shall not be less than the R-value specified in the table. b “5ci or13” means R-5 continuous insulation (ci) on the interior or exterior surface of the wall or R-13 cavity insulation on the interior side of the wall. "10ci or 13" means R-10 continuous insulation (ci) on the interior or exterior surface of the wall or R-13 cavity insulation on the interior side of the wall. "15ci or 19 or 13&5ci" means R-15 continuous insulation (ci) on the interior or exterior surface of the wall; or R-19 cavity insulation on the interior side of the wall; or R-13 cavity insulation on the interior of the wall in addition to R-5 continuous insulation on the interior or exterior surface of the wall. c The first value is cavity insulation, the second value is continuous insulation (ci) or insulated siding. Therefore, as an example, "13&2ci" means R-13 cavity insulation plus R-2 continuous insulation or insulated siding. Where R-13&2ci is used, non-insulated structural sheathing shall cover no more than 25% of the exterior. d Slab insulation shall be installed in accordance with Section R402.2.10.1. e Basement wall insulation is not required in Warm Humid locations as defined by Figure R301.1 and Table R301.1. f Total-fill cavity insulation will be deemed as meeting the R-15 requirement. f g Air-impermeable insulation of R-25&0 or greater may be used if mechanical equipment and air distribution system are located entirely within the building thermal envelope. "Air-impermeable" shall be defined as having an air permeance not exceeding 0.02 L/s-m2 at 75 Pa pressure differential tested according to ASTM E 2178 or ASTM E 283. g h R-0&25ci continuous insulation can be used where the insulation is completely above the roof framing and sub-roofing. h i Mass walls shall be in accordance with Section R402.2.6. The second R-value applies where more than half of the insulation is on the interior of the mass wall. R402.6 R402.3 Radiant Barriers. A roof radiant barrier with an emittance of 0.05 or less as tested in accordance with ASTM C-1371 or ASTM E-408 is required. The radiant barrier shall be installed according to the manufacturer's instructions Radiant barriers shall be installed in accordance with ASTM C1743. A roof radiant barrier is not required for: Exceptions: 1. 2. 3. 4. 5. Roofs covered with clay or concrete tile having a solar reflectance of 0.40 or greater. Roofs covered with other materials having a solar reflectance of 0.50 or greater. Residential buildings with sealed attics. Residential buildings with mechanical equipment and all ductwork located wholly within the conditioned space. Existing construction where there is no modification to the roof framing structure. R402.4.1.2 Testing R402.5.1.2 Air Leakage Testing. The building or each dwelling unit or sleeping unit in the building shall be tested for air leakage. The maximum air leakage rate for any building or dwelling unit under any compliance path shall not exceed 5.0 air changes per hour or 0.28 cubic feet per minute (CFM) per square foot [0.0079 m3 /(s × m2 )] of dwelling unit enclosure area. Testing shall be conducted in accordance with Page 7 of 25 Commented [A21]: 2024 IECC model code amended R- value from R49 to R38. Local amendment made to mirror that change. Commented [A22]: 2024 IECC model code added additional assembly requirement for “Insulation Entirely Above Roof Deck.” Local amendment already exists for this assembly in “Attic Roofline” insulation, which includes above and below deck insulation R-value. Local amendment made to mirror change in above deck R-value. Commented [A23]: Local amendment deleted as no longer needed. Commented [A24]: 2024 IECC model code added requirements for Radiant Barrier where installed. Local amendment was updated to reflect updated ASTM standard and moved to align with model code citation number. Existing requirement for Radiant Barrier and exceptions remain. Commented [A25]: 2024 IECC model code updated with citation renumbering, clarifying language, inclusion of sampling, and reducing the air leakage targets. Local amendments made to mirror model code. Sampling requirement amended to refer users to existing Batch testing requirements in R403.3.13. ANSI/RESNET/ICC 380, ASTM E 779, or ASTM E 1827 or ASTM E3158 and reported at a pressure differential of 0.2 inches w.g. water gauge (50 Pascals). Where required by the code official, testing shall be conducted by an approved independent third party. A written report of the results of the test shall be signed by the party conducting the test and provided to the code official. The report shall include address of the residence, building permit number, name and employer of the technician performing the test, and date of the test. Testing shall be performed at any time after creation of all penetrations of the building thermal envelope have been sealed. During testing: 3. 4. 5. 6. Exceptions: 1. 2. Exterior windows and doors, fireplace and stove doors shall be closed, but not sealed, beyond the intended weatherstripping or other infiltration control measures. Dampers including exhaust, intake, makeup air, backdraft and flue dampers shall be closed, but not sealed beyond intended infiltration control measures. Interior doors, where installed at the time of the test, shall be open. Exterior or interior terminations for continuous ventilation systems shall be sealed. Heating and cooling systems, where installed at the time of the test, shall be turned off. Supply and return registers, where installed at the time of the test, shall be fully open. 1. Existing construction where the volume of the conditioned area is unchanged and additions that cannot be physically separated from the existing construction. 2. When testing individual dwelling units, an air leakage rate not exceeding 0.30 cubic feet per minute per square foot [0.008 m3 /(s × m2 )] of the dwelling unit enclosure area, tested in accordance with ANSI/RESNET/ICC 380, ASTM E 779 or ASTM E 1827 and reported at a pressure of 0.2 inch w.g. (50 Pa), shall be an accepted alternative permitted in all climate zones for: Attached single-family and multiple-family building dwelling units. Buildings or dwelling units that are 1,500 square feet (139.4 m2 ) or smaller. a. b. 2. For heated, attached private garages and heated, detached private garages accessory to one- and two-family dwellings and townhouses not more than three stories above grade plane in height, building thermal envelope tightness and insulation installation shall be considered acceptable where the items in Table R402.5.1.1, applicable to the method of construction, are field verified. Where required by the code official, an approved third party independent from the installer shall inspect both air barrier and insulation installation criteria. Heated, attached private garage space and heated, detached private garage space shall be thermally isolated from all other habitable, conditioned spaces in accordance with Sections R402.2.13 and R402.4.5, as applicable. 3. Where tested in accordance with Section R402.5.1.2.1 R403.3.13, testing of each dwelling unit or sleeping unit is not required. Mechanical ventilation shall be provided in accordance with Section M1505 of the International Residential Code or Section 403.3.2 of the International Mechanical Code, as applicable, or with other approved means of ventilation. R402.5.1.3 Maximum Air Leakage Rate. Where tested in accordance with Section R402.5.1.2, the air leakage rate for buildings, dwelling units or sleeping units shall be as follows: Commented [A26]: New 2024 IECC model language splitting the air leakage testing and rate requirements. 1. Where complying with Section R401.2.1, the building, dwelling units or sleeping units in the building shall have an air leakage rate not greater than 4.0 air changes per hour in Climate Zones 0, 1 and 2, 3.0 air changes per hour in Climate Zones 3 through 5, and 2.5 air changes per hour in Climate Zones 6 through 8. 2. Where complying with Section R401.2.2 or R401.2.3, the building, dwelling units or sleeping units in the building shall have an air leakage rate not greater than 4.0 air changes per hour, or 0.22 cfm/ft2 (1.1 L/s x m2) of the building thermal envelope area or testing unit enclosure area, as applicable. Commented [A27]: FYI: Prescriptive path Commented [A28]: FYI: Performance or ERI path Page 8 of 25 Exceptions: 1. Where dwelling units or sleeping units are attached or located in an R-2 occupancy and are tested without simultaneously testing adjacent dwelling units or sleeping units, the air leakage rate is permitted to be not greater than 0.27 cfm/ft2 (1.35 L/s x m2) of the testing unit enclosure area. Where adjacent dwelling units or sleeping units are simultaneously tested in accordance with ASTM E779, the air leakage rate is permitted to be not greater than 0.27 cfm/ft2 (1.35 L/s x m2) of the testing unit enclosure area that separates conditioned space from the exterior. 2. Where buildings have 1,500 square feet (139.4 m2) or less of conditioned floor area, the air leakage rate is permitted to be not greater than 0.27 cfm/ft2 (1.35 L/s x m2). R402.5 R402.6 Maximum Fenestration U-factor and SHGC. The area-weighted average maximum fenestration U- factor permitted using trade-offs from Section R402.1.5 or R405 shall be 0.50. The area-weighted average maximum SHGC permitted using tradeoffs from Section R405 fenestration facing East, South and West shall be 0.30. The SHGC of fenestration facing within 45 degrees of East and West shall be no greater than 0.25, unless the projection factor multiplier in Table R402.5.1 R402.6.1 is applied. Glazed fenestration facing within 45 degrees of North shall not be included in the area-weighted SHGC calculation. TABLE R402.5.1 R402.6.1 SHGC MULTIPLIER FOR CERTAIN FENESTRATION Projection Factor 0.10 - 0.25 0.26 - 0.50 0.51 - 0.75 0.76 - 1.00 > 1.00 SHGC Multiplier (Glazed fenestration from 135 to 225 degrees) SHGC Multiplier (Glazed fenestration from 45 to 135 degrees and 225 to 315 degrees) 0.85 0.75 0.60 0.40 0.20 0.75 0.60 0.40 0.20 0.10 Exception: The maximum U-factor and solar heat gain coefficient (SHGC) for fenestration shall not be required in storm shelters complying with ICC 500. R402.6 Radiant Barrier. A roof radiant barrier with an emittance of 0.05 or less as tested in accordance with ASTM C-1371 or ASTM E-408 is required. The radiant barrier shall be installed according to the manufacturer's instructions A roof radiant barrier is not required for: 1. 2. 3. 4. 5. Roofs covered with clay or concrete tile having a solar reflectance of 0.40 or greater. Roofs covered with other materials having a solar reflectance of 0.50 or greater. Residential buildings with sealed attics. Residential buildings with mechanical equipment and all duct work located wholly within the conditioned space. Existing construction where there is no modification to the roof framing structure. Commented [A29]: Local amendment updated citation and reference numbering. Commented [A30]: See R402.3 Radiant Barrier above R402.7 Attic Ventilation. Attic ventilation shall be installed in accordance with the Residential Code or Mechanical Code, respective to the building type. Ventilation shall not be provided where it introduces unconditioned air into the thermal envelope of the building. Commented [A31]: Local amendment deleted as no longer needed. Page 9 of 25 R403.1.1.1 Thermostat Connectivity to Internet. The thermostat controlling the primary heating or cooling system of the dwelling unit shall be capable of connecting to the internet via either a cable or WiFi connection and allow cooling and heating set points to be altered remotely. Exception: Heating and cooling systems with proprietary thermostats or controls that don't allow connection to the internet. R403.3.5 R403.3.7 Duct System Testing. Each duct system shall be tested for air leakage in accordance with ANSI/RESNET/ICC 380 or ASTM E1554. Total leakage shall be measured with a pressure differential of 0.1 inch water gauge (25 Pa) across the duct system and shall include the measured leakage from the supply and return ductwork. A written report of the test results shall be signed by the party conducting the test and provided to the code official. Duct system leakage testing at either rough-in or post-construction shall be permitted with or without the installation of registers or grilles. Where installed, registers and grilles shall be sealed during the test. Where registers and grilles are not installed, the face of the register boots shall be sealed during the test. Ducts shall be pressure tested in accordance with ANSI/RESNET/ICC 380 or ASTM E1554 to determine air leakage by one of the following methods: 1. 2. Rough-in test: Total leakage shall be measured with a pressure differential of 0.1 inch w.g. (25 Pa) across the system, including the manufacturer's air handler enclosure if installed at the time of the test. All registers shall be taped or otherwise sealed during the test. Post-construction test: Total leakage shall be measured with a pressure differential of 0.1 inch w.g. (25 Pa) across the system, including the manufacturer's air handler enclosure. All registers shall be taped or otherwise sealed during the test. Exceptions: A duct air-leakage test shall not be required for ducts serving ventilation systems that are not integrated with ducts serving heating or cooling systems. A written report of the results of the test shall be signed by the party conducting the test and provided to the code official. 1. Testing shall not be required for duct systems serving ventilation systems that are not integrated with duct systems serving heating or cooling systems. 2. Testing shall not be required where there is not more than 10 feet (3.03 m) of total ductwork external to the space conditioning equipment and both the following are met: 2.1. The duct system is located entirely within conditioned space. 2.2. The ductwork does not include plenums constructed of building cavities or gypsum board. 3. Where the space conditioning equipment is not installed, testing shall be permitted. The total measured leakage of the supply and return ductwork shall be less than or equal to 3.0 cubic feet per minute (85 L/min) per 100 square feet (9.29 m2) of conditioned floor area. 4. Where tested in accordance with Section R403.3.9 R403.3.13, testing of each duct system is not required. R403.3.6 R403.3.8 Duct System Leakage. The total measured duct system leakage shall not be greater than the values in Table R403.3.8, based on the conditioned floor area, number of ducted returns, and location of the duct system. For buildings complying with Section R405 or R406, where duct system leakage to outside is tested in accordance with ANSI/RESNET/ICC 380 or ASTM E1554, the leakage to outside value shall not be used for compliance with this section but shall be permitted to be used in the calculation procedures of Section R405 and R406. The total leakage of the ducts, where measured in accordance with Section R403.3.5 R403.3.7, shall be as follows: 1. Rough-in test: The total leakage shall be less than or equal to 4.0 cubic feet per minute (113.3 L/min) per 100 square feet (9.29 m2 ) of conditioned floor area where the air handler is installed at the time of the test. Where the air handler is not installed at the time of the test, the total leakage shall be less than or equal to 3.0 cubic feet per minute (85 L/min) per 100 square feet (9.29 m2 ) of conditioned floor area. Page 10 of 25 Commented [A32]: Local amendment renumbered, aligned clarifying language with model code, and updated citation for reference to batch testing. Commented [A33]: 2024 IECC model code updated with clarifying language and updated duct system leakage targets. Local amendment updated to include the clarifying language however existing more stringent duct system leakage targets were not changed. Since the existing more stringent targets have been required for more 10 years, there is no compelling reason to allow less stringent duct leakage. Additionally, allowances for more duct system leakage may inhibit successful air balancing testing results that is also required by the City of Austin. Post-construction test: Total leakage shall be less than or equal to 4.0 cubic feet per minute (113.3 L/min) per 100 square feet (9.29 m2 ) of conditioned floor area. Test for ducts within thermal envelope: Where all ducts and air handlers are located entirely within the building thermal envelope, total leakage shall be less than or equal to 4.0 cubic feet per minute (113.3 L/min) per 100 square feet (9.29 m2 ) of conditioned floor area. In dwelling units served by a single system with a condenser rated at 1.5 tons or less cooling capacity, total leakage shall be no more than 42 cubic feet per minute. TABLE R403.3.8 MAXIMUM TOTAL DUCT SYSTEM LEAKAGE 4 (113) 30 (850) 42 (1189) Total leakage cfm/100 ft2(LPM/9.29 m2) Total leakage cfm (LPM) 3 (85) Space conditioning equipment is not installed b,c All components of the duct system are installed c Space conditioning equipment is not installed, but the ductwork is located entirely in conditioned space c,d All components of the duct system are installed and entirely located in conditioned space c a. A ducted return is a duct made of sheet metal or flexible duct that connects one or more return grilles to the return-side inlet of the air-handling unit. Any other method to convey air from return or transfer grille(s) to the air-handling unit does not constitute a ducted return for the purpose of determining maximum total duct system leakage allowance. b. Duct system testing is permitted where space conditioning equipment is not installed, provided the return ductwork is installed, and the measured leakage from the supply and return ductwork is included. c. For duct systems to be considered inside a conditioned space, where the ductwork is located in ventilated attic spaces or unvented attics with vapor diffusion ports, duct system leakage to outside must comply with Item 2.1 of Section R403.3.4. d. Prior to the issuance of a certificate of occupancy, where the air-handling unit is not verified as being located in conditioned space, the total duct system leakage must be re-tested. 2. 3. 4. R403.3.8 R403.3.10 Balancing of Air Distribution System. Volumetric airflow in cubic feet per minute (CFM) shall meet the design/application requirements. Airflow testing shall be performed by an independent third-party testing contractor approved by the building official, with all interior doors closed and all blowers operating at cooling speed. The airflow at each supply register shall be measured. Supply registers with a design airflow exceeding 35 CFM shall have a measured airflow of within ±20% of design airflow. Supply registers with design airflow below 35 CFM but having a measured airflow 60 CFM or higher shall be balanced to bring measured airflow to within ±20% of design airflow. Documentation shall verify that actual total system airflow is within ±10 percent of total system design airflow. All documentation shall be submitted with the final mechanical Code compliance package and provided to the code official. Measurement of supply airflow shall be performed using a balometer (flow hood) per the manufacturer's instructions. Documentation shall include the following: Address of building. a. b. Name and company of technician performing the testing. Page 11 of 25 Commented [A34]: The criteria for Independence for approved third-party inspection agencies is now included in R107.4.1.1 c. Date of final test. Exceptions: Ductless systems. 1. 2. 3. 4. a. b. c. d. e. 1. 2. 3. 4. Existing construction with no modification of or addition to the existing ductwork. An addition of 200 square feet or less of conditioned space to existing construction. Systems with a Manual J recommended sizing of 4.5 tons or other size not typically available from manufacturers must be balanced to within ±20% of design air flow as indicated on the Manual J for that building. It is the responsibility for the HVAC contractor to communicate the lack of availability of a properly sized system to the third-party testing contractor. R403.3.9 R403.3.11 Pressure Differential. The pressure difference between each bedroom and adjacent interior area (i.e. hallway) shall not exceed 5 Pascals. The pressure difference between the interior area in the vicinity of the return side of the air handling equipment and the outside of the building does not exceed -5 Pascals. Testing shall be performed by an independent third-party testing contractor approved by the building official, with all interior doors closed and all blowers operating at cooling speed. Exception: Ductless systems where the supply and return airflow are handled by a single unit within the room. R403.3.10 R403.3.12 System Static Pressure. Total system static pressure with filters installed shall not exceed 0.8 inch water column on gas furnaces and 0.6 inch water column on electric air handlers. Static pressure testing using a digital manometer or magnehelic shall be performed by an independent third-party testing contractor approved by the building official. Documentation verifying static pressure testing results within the allowed ranges shall be submitted with the final mechanical code compliance package and provided to the code official. Documentation shall include the following: Address of building. Name and company of third-party testing contractor performing the testing. Date of final test. Procedure used for the test. Results of the test listing static pressure for applications tested. Exceptions: Ductless systems. Existing construction with no modification of or addition to the existing ductwork, or replacement of mechanical equipment. Systems where the air handler equipment is housed within the return plenum. Air handlers for systems having a rated cooling capacity above 55,000 Btu per hour. R403.3.11 R403.3.13 Batch Testing. For buildings having three eight or more dwelling units or sleeping units, a minimum of 15% of the dwelling units in each building must seven or 20 percent of the dwelling units or sleeping units, whichever is greater shall be tested as required by Sections R402.4.1.2 R402.5.1.2, R403.3.5 R403.3.7, R403.3.6 R403.3.8, R403.3.8 R403.3.10, R403.3.9 R403.3.11, R403.3.10 R403.3.12, and R403.6.3. If each tested dwelling unit or sleeping unit within the batch meets code requirements, then all dwelling units or sleeping units in the batch are considered to meet code. The third-party testing contractor shall perform all required tests on at least three consecutive dwelling units or sleeping units. Test results must meet code requirements before batch testing is allowed. Initial testing is required for each new multifamily project. Dwelling units or sleeping units must be within the same building to qualify for inclusion in a batch. Page 12 of 25 Commented [A35]: 2024 IECC model code added sampling code language for air and duct system leakage and mechanical ventilation testing. Existing local amendments require more system testing and allow sampling for all testing. Consolidating sampling protocols is deemed more valuable than separating for each system testing requirement. Local amendment updated with updated citation and reference numbering and alignment with more stringent model code language for number of units in a batch and minimum percentage of dwelling units to test. Batch Identification and Sampling The builder shall identify a "batch" which is a building where the dwelling units or sleeping units are completed and ready for testing. The third-party testing contractor randomly selects at least 15% of the dwelling units and/or sleeping units from a batch for testing. A batch shall include a top floor dwelling unit, a ground floor dwelling unit, a middle floor dwelling unit, and the dwelling unit with the largest conditioned floor area. Where buildings have fewer than eight dwelling units or sleeping units, each dwelling unit or sleeping units shall be tested. All dwelling units or sleeping units within the batch must be ready for testing (drywall complete, interior door jams installed, HVAC system installed, and final air sealing completed) before the third-party testing contractor can select the units to be tested. Failure to Meet Code Requirement(s) a. b. c. If any dwelling units or sleeping units within the identified batch fail to meet a code requirement as a result of testing, the builder will be directed to fix the cause(s) of failure, and 30% of the remaining dwelling units or sleeping units in the batch will be randomly selected for testing regarding the specific cause(s) of failure. If any failures occur in the additional dwelling units or sleeping units, all remaining dwelling units or sleeping units in the batch must be individually tested for code compliance. A multifamily project with 3 failures within a 6-month period is no longer eligible to use the sampling protocol in that community or project until successfully repeating "Initial Testing." Sampling can be reinstated after at least 3 consecutive dwelling units or sleeping units are individually verified to meet all code requirements. d. No dwelling unit or sleeping units in a batch may be issued a Certificate of Occupancy until testing has been performed and passed on the dwelling units or sleeping units selected for testing. R403.3.12 Filtration for Air Distribution Systems. Filters installed in air distribution systems shall have a minimum efficiency reporting value (MERV) rating of 6 or greater. Filters shall be located to prevent unfiltered air from passing through the mechanical equipment. Filters shall be installed prior to operation of the air handling unit. R403.5.4 Demand Response of Electric Resistance Water Heating. Electric resistance water heaters shall be controlled by a preprogrammed water heater timer. The timer shall be preprogrammed to turn the water heater off between the hours of 3:00 p.m. and 7:00 p.m. from June 1 to September 30. The timer shall have a readily accessible override, as defined by the building official, capable of restoring power to the water heater for one hour when activated. The timer shall be permanently programmed by the manufacturer or locked to prevent alteration of the programming by the building occupants. Buildings that are accessory to a residential building are considered residential buildings for the purposes of this section. a. Heat pump water heater installed where electric resistance is the secondary means of heating. b. Water heater installed with an OpenADR certified communications module or ANSI/CTA-2045 certified port allowing for remote management or other demand response capability as approved by the code official. R403.6.3 Testing. Mechanical ventilation systems shall be tested and verified to provide the minimum ventilation flow rates required by Section R403.6, in accordance with ANSI/RESNET/ICC 380. Where required by the code official, testing shall be conducted by an approved third party. A written report of the results of the test shall be signed by the party conducting the test and provided to the code official. Exceptions: Exceptions: 1. Kitchen range hoods that are ducted to the outside with ducting having a diameter of 6 inches (152 mm) or larger, a length of 10 feet (3048 mm) or less, and not more than two 90-degree (1.57 rad) elbows or equivalent shall not require testing. Page 13 of 25 Commented [A36]: 2024 IECC model code added demand response code language for electric storage water heaters in Appendix RJ. Local amendment already existed. Local amendment, R403.5.4 deleted and updated to mirror model code in Appendix RJ. Allowance added for timers in the exceptions. Commented [A37]: 2021 IECC model code introduced mechanical ventilation testing. Updates in the 2024 IECC include adding the RESNET 380 standard, updating allowed exceptions, and adding an allowance for sampling. Local amendment made to include mechanical ventilation testing in existing sampling requirements in R403.3.13. 2. A third-party test shall not be required where the ventilation system has an integrated diagnostic tool used for airflow measurement, and a user interface that communicates the installed airflow rate. 3. Where tested in accordance with Section R403.6.4 R403.3.13, testing of each mechanical ventilation system is not required. R403.7.1 R403.7.2 Documentation of Heating and Cooling Equipment Sizing. Documentation verifying the methodology and accuracy of heating and cooling equipment sizing shall be submitted with final mechanical code compliance package. Documentation shall include the following information: a. Address of residence. b. Name of individual performing load calculations. c. Name and version of load calculation software. d. Design temperatures (outdoor and indoor) according to the Air Conditioning Contractors of America's (ACCA) Manual J, ACCA Manual N, American Society of Heating, Refrigeration and Air-Conditioning Engineers, U.S. Department of Energy standards, or other methodology approved by the City of Austin. e. Area of walls, windows, skylights and doors within ± 10% of architectural plans or actual building. f. Orientation of windows and glass doors, infiltration rate, duct loads, internal gains, insulation values, and Solar Heat Gain Coefficient of windows. g. Heating and cooling load calculations. h. Design supply airflows for each room. R403.9 R403.14 Space Heating. The use of electric resistance as a primary source of space heating is prohibited in all dwelling units or sleeping units having a conditioned floor area in excess of 500 square feet. Exception: Buildings where dwelling units are cooled using chilled water. R405.2 Simulated Building Performance-based Compliance. Compliance based on total simulated building performance requires that a building proposed design meets all of comply with the following: 1. 2. 3. The requirements of the sections indicated within Table R405.2. The proposed total building thermal envelope thermal conductance (TC) shall be greater less than or equal to the required total building thermal envelope TC using the prescriptive U-factors and F-factors from Table R402.1.2(1) for existing buildings and Table R402.1.2(2) for new construction multiplied by 1.08 in Climate Zone 2 in accordance with Equation 4-2 and Section R402.1.5. The area-weighted maximum fenestration SHGC permitted in Climate Zone 2 shall be 0.30. levels of efficiency and solar heat gain coefficients in Table R402.1.1 or R402.1.3 of the 2012 International Energy Conservation Code as amended by Ordinance No. 20130606-091. Equation 4-2: TCProposed design ≤ 1.08 x TCPrescriptive reference design Annual energy use that is less than or equal to the annual energy use of the standard reference design. For each dwelling unit with one or more fuel-burning appliances for space heating, water heating, or both, the annual energy cost use of the dwelling unit shall be less than or equal to 80 percent of the annual energy cost use of the standard reference design. For all other dwelling units, the annual energy cost use of the proposed design shall be less than or equal to 85 percent of the annual energy cost use of the standard reference design. For each dwelling unit with greater than 5,000 square feet (465 m2) of living space located above grade plane, the annual energy cost use of the dwelling unit shall be reduced by an additional 5 percent of annual energy cost use of the standard reference design. Exception: Fenestration U-factor of 0.50 is allowed if offset by cooling and/or heating system efficiency. Exceptions: Page 14 of 25 Commented [A38]: Updated to include sleeping units in alignment with other 2024 IECC model code updates. Commented [A39]: 2024 IECC model code updated R405.2 by changing the backstop methodology, increased the savings above baseline requirement, and updated source energy factors. In the 2021 IECC the savings above baseline was an option within the R401.2.5 Additional Energy Efficiency requirement. The 2024 IECC has tried to simplify by only include a savings above baseline in the R405 pathway. R408 will only apply to prescriptive path users. Local amendments recommend using the new 2024 language and retain the existing energy use requirement as allowed in Exception 1. Commented [A40]: Table updated to match model code updates, retain prior local amendments and include new local amendments. 1. The energy use based on source energy expressed in Btu or Btu per square foot of conditioned floor area shall be permitted to be substituted for the energy cost. The source energy multiplier for electricity shall be 2.51. The source energy multipliers shall be 1.09 for natural gas, 1.15 for propane, 1.19 for fuel oil, and 1.30 for imported liquified natural gas. 2. The energy use based on site energy expressed in Btu or Btu per square foot of conditioned floor area shall be permitted to be substituted for the energy cost. Table R405.2 REQUIREMENTS FOR TOTAL SIMULATED BUILDING PERFORMANCE SECTIONa R401.2.5 R401.3 General TITLE Additional energy efficiency Certificate Building Thermal Envelope R402.1.1 R402.1.6 R402.2.3 R402.2.4 R402.2.4.1 R402.2.5.1 R402.2.10.1 R402.2.11 R402.3 R402.5.1.1 R402.4 R402.5.1.2 R402.5.1.3 R402.5.2 R402.5.3 R402.5.4 R402.5.5 R402.5 R402.6 R402.6 Mechanical R403.1 R403.2 R403.3, except Sections R403.3.2, R403.3.3, R403.3.11 R403.4 R403.5 R403.5.1 except Section R403.5.2 R403.5.3 R403.5.4 R403.6 R403.7, except Section R403.7.1 R403.8 R403.9 Page 15 of 25 Vapor retarder Rooms containing fuel burning appliances Eave baffles Attic knee wall Eave baffle Access hatches and door insulation installation and retention Crawl space wall insulation installations Slab-on-grade floors Crawl space walls insulation installations Radiant barriers Installation Testing Air leakage testing Maximum air leakage rate Fireplaces Fenestration air leakage Recessed lighting Air-sealed electrical and communication outlet boxes Maximum fenestration U-factor and SHGC Radiant Barrier Controls Hot water boiler temperature reset Ducts systems and Additional HVAC Testing Mechanical system piping insulation Service hot water system Heated water circulation and temperature maintenance systems Drain water heat recovery units Demand Response of Electric Resistance Water Heating Mechanical ventilation Equipment sizing and efficiency rating Systems serving multiple dwelling units Space heating TABLE R405.4.2(1) SPECIFICATIONS FOR THE STANDARD REFERENCE AND PROPOSED DESIGNS STANDARD REFERENCE DESIGN PROPOSED DESIGN Commented [A41]: Table updated to match model code updates, retain prior local amendments and include new local amendments. Energy consumption of pools and spas Portable spas Residential pools and permanent residential spas Gas fireplaces Snow melt and ice system controls Electrical Power and Lighting Systems Lighting equipment Interior lighting controls Residential Solar Ready Electric Vehicle Power Transfer Demand Responsive Controls Electric Readiness R403.10 R403.11 R403.12 R403.13 R403.15 R404.1 R404.2 Chapter 7 [RE] Appendix RE Appendix RJ Appendix RK a Reference to a code section includes all the relative subsections except as indicated in the table. BUILDING COMPONENT Above-grade walls Basement and crawl space walls Above-grade floors Ceilings Roofs Attics Type: mass wall if proposed wall is mass; otherwise wood frame Gross area: same as proposed U-factor: from Table R402.1.2(2) Solar reflectance absorptance = 0.75 0.25 Emittance = 0.90 Type: same as proposed Gross area: same as proposed U-factor: from Table R402.1.2(2), with insulation layer on interior side of walls. Type: wood frame Gross area: same as proposed U-factor: from Table R402.1.2(2) Type: wood frame Gross area: same as proposed U-factor: from Table R402.1.2(2) Type: composition shingle on wood sheathing Gross area: same as proposed Solar reflectance absorptance = 0.75 0.25 Emittance = 0.90 Radiant barrier per R402.6 R402.3 Type: vented with an aperture of 1 ft2 per 300 ft2 of ceiling area. As proposed As proposed As proposed As proposed As proposed As proposed As proposed As proposed As proposed As proposed As proposed As proposed As proposed As proposed As proposed As proposed As proposed As proposed As proposed As proposed Page 16 of 25 Commented [A42]: Accidentally not added in 2021. Added now to align with model code. As proposed As proposed As proposed As proposed As proposed As proposed As proposed As proposed As proposed As proposed Interior shade fraction: 0.92 – (0.21 x SHGC as As proposed As proposed As proposed As proposed The measured air leakage exchange rate.a The mechanical ventilation rateb shall be in addition to the air leakage rate and shall be as proposed. Foundations Type: same as proposed Opaque doors Vertical fenestration other than opaque doors Skylights Thermally isolated sunrooms Air exchange leakage rate Foundation wall extension area above and below grade: same as proposed. Foundation wall or slab perimeter length: same as proposed. and Soil characteristics: same as proposed Foundation wall U-factor and slab-on-grade F-factor: as specified in Table R402.1.2(2) Area: 40 ft2 Orientation: North U-factor: same as fenestration from Table R402.1.2(2) Total areah = 15% of conditioned floor area Orientation: equally distributed to four cardinal compass orientations (N, E, S & W) U-factor: area-weighted average of 0.35 SHGC: 0.25 Interior shade fraction: 0.92 – (0.21 x SHGC for the standard reference design) External shading: none None None For detached one-family dwellings, the The air leakage rate at a pressure of 0.2 inch w.g. water gauge (50 Pa) shall be 5 4 air changes per hour. For detached one-family dwellings that are 1,500 ft2 (139.4 m2) or smaller and attached dwelling units or sleeping units, the air leakage rate at a pressure of 0.2 inch water gauge (50 Pa) shall be 0.27 cfm/ft2 of the testing unit enclosure area. The mechanical ventilation rate shall be in addition to the air leakage rate and shall be the same as in the proposed design, but not greater than 0.01 x CFA + 7.5 x (N + 1) where: CFA = conditioned floor area, ft2 . N = number of bedrooms. The mechanical ventilation system type shall be the same as in the proposed design. Energy recovery shall not be assumed for mechanical ventilation. Page 17 of 25 Mechanical ventilation rate The measured mechanical ventilation rateb , Q, shall be in addition to the measured air leakage rate and shall be as proposed. Mechanical ventilation fan energy As proposed Where mechanical ventilation is not specified in the proposed design. None Where mechanical ventilation is specified in the proposed design, the annual vent fan energy use, in units of kWh/yr, shall equal (1/e f ) x [0.0876 x CFA + 65.7 x (N br + 1)] Where: e f = the minimum exhaust fan efficacy, as specified in Table R403.6.2, corresponding to the system type at a flow rate of 0.01 x CFA + 7.5 x (N br + 1) CFA = conditioned floor area, ft2 N br = number of bedrooms The mechanical ventilation rate shall be in addition to the air leakage rate and shall be the same as in the proposed design, but not greater than B x M where: B = 0.01 × CFA + 7.5 × (Nbr + 1), cfm. M = 1.0 where the measured air leakage rate is ≥ 3.0 air changes per hour at 50 Pascals, and otherwise, M = minimum (1.7, Q/B) Q = the proposed mechanical ventilation rate, cfm. CFA = conditioned floor area, ft2 Nbr = number of bedrooms. The mechanical ventilation system type shall be the same as in the proposed design. Heat recovery or energy recovery shall be modeled for mechanical ventilation where required by Section R403.6.1. Heat recovery or energy recovery shall not be modeled for mechanical ventilation where not required by Section R403.6.1. Where mechanical ventilation is not specified in the proposed design: None Where mechanical ventilation is specified in the proposed design, annual vent fan energy use, in units of kWh/yr, shall equal: (8.76 x B x M)/ef where: B and M are determined in accordance with the air exchange mechanical ventilation rate row of this table. e f = the minimum exhaust fan efficacy, as specified in Table R403.6.2, corresponding to the system type at a flow rate of B x M IGain, in units of Btu/day per dwelling unit, shall equal 17,900 + 23.8 × CFA + 4,104 × Nbr where: Page 18 of 25 Internal gains Same as standard reference design. Same as standard reference, plus any additional mass specifically designed as a thermal storage elementc but not integral to the building thermal envelope or structure As proposed CFA = conditioned floor area, ft2. Nbr = number of bedrooms. Internal Mass An internal mass for furniture and contents of 8 pounds per square foot of floor area Structural mass Heating systemsd, e, j, k Cooling systemsd, f, k Service water heatingd, g, k For masonry floor slabs, 80% of floor are covered by R-2 carpet and pad, and 20% of floor directly exposed to room air. For masonry basement walls: as proposed, but with insulation as specified in Table R402.1.3, located on the interior side of the walls. For other walls, for ceilings, floors, and interior walls, wood frame construction. Prevailing federal minimum efficiency Fuel Type: Same as proposed design Capacity: same as proposed design and in accordance with Section R403.7 Product class: Same as proposed design Efficiencies: Heat pump: Complying with 10 CFR §430.32 Fuel gas and liquid fuel furnaces: Complying with 10 CFR §430.32 Prevailing federal minimum efficiency Fuel Type: Electric Capacity: same as proposed design and in accordance with Section R403.7 Efficiencies: Complying with 10 CFR §430.32 As proposed. Use, in units of gal/day = 25.5 + (8.5 x N br ) Where N br = number of bedrooms As proposed As proposed As proposed As proposed As proposed As proposed As proposed As proposed As proposed As proposed Use, in units of gal/day = (25.5 + (8.5 x N br ))*(1-HWDS) Where: Nbr = number of bedrooms. HWDS = factor for the compactness of the hot water distribution system Compactness ratioi factor 1 story HWDS Factor 2 or more stories > 30% > 15% to ≤ 30% 0 0.05 > 60% > 30% to ≤ 60% Page 19 of 25 Commented [A43]: Coord with Christian and PH on proposed changes Thermal distribution systems > 7.5% to ≤ 15% ≤ 7.5% 0.10 0.15 > 15% to ≤ 30% ≤ 15% As proposed As proposed As proposed As proposed Same as standard reference design Duct insulation: as proposedm. As tested or, where not tested, as specified in Table R405.4.2(2) Duct location: as proposedl Fuel Type: Same as proposed design Rated Storage Volume: Same as proposed design Draw Pattern: Same as proposed design Efficiencies: Uniform Energy Factor complying with 10 CFR §430.32 Tank Temperature: 120° F (48.9° C) Duct insulation: in accordance with Section R403.3.1 Section R403.3.3. A thermal distribution system efficiency (DSE) of 0.88 shall be applied to both the heating and cooling system efficiencies for all systems other than tested duct systems. Duct location: same as proposed design. Exception: For nonducted heating and cooling systems that do not have a fan, the standard reference design thermal distribution system efficiency (DSE) shall be 1. For tested duct systems, the leakage rate shall be 4 cfm (113.3 L/min) per 100 ft2 (9.29 m2 ) of conditioned floor area at a pressure of differential of 0.1 inch w.g. (25 Pa). Duct location: Basement or condition ed crawl space 75% inside conditione d space 25% unconditi oned attic Foundatio n Type Slab on grade Duct location (supply and return) One-story building: 100% in unconditio ned attic. All other: 75% in unconditio ned attic and 25% inside conditione d space Unconditio ned crawl space One-story building: 100% in unconditio ned crawlspace . All other: 75% in unconditio ned crawlspace and 25% inside Page 20 of 25 conditione d space Duct system leakage to outside: For duct systems serving > 1,000 ft2 (92.9 m2) of conditioned floor area, the duct leakage to outside rate shall be 4 cfm (113.3 L/min) per 100 ft2 (9.29 m2) of conditioned floor area. For duct systems serving ≤ 1,000 ft2 (92.9 m2) of conditioned floor area, the duct leakage to outside rate shall be 40 cfm (1132.7 L/min). Duct System Leakage to Outside: The measured total duct system leakage rate shall be entered into the software as the duct system leakage to outside rate. Exceptions: 1. Where duct system leakage to outside is tested in Accordance ANSI/ RESNET/ICC 380 or ASTM E1554, the measured value shall be permitted to be entered. 2. Where total duct system leakage is measured without the space conditioning equipment installed, the simulation value shall be 4 cfm (113.3 L/ min) per 100 ft2 (9.29 m2) of conditioned floor area. Distribution System Efficiency (DSE): For hydronic systems and ductless systems, DSE shall be as specified in Table R405.4.2(2). Distribution System Efficiency (DSE): For hydronic systems and ductless systems a thermal distribution system efficiency (DSE) of 0.88 shall be applied to both the heating and cooling system efficiencies. Thermostat Type: Programmable, cooling temperature setpoint = 75°F Heating temperature setpoint = 72°F Same as standard reference design. Dehumidistat Where a mechanical ventilation system with latent Same as standard reference design. heat recovery is not specified in the proposed design: None. Where the proposed design utilizes a mechanical ventilation system with latent heat recovery: Dehumidistat type: Manual, setpoint = 60% relative humidity. Dehumidifier: whole-home dwelling with integrated energy factor = 1.77 liters/kWh. Page 21 of 25 R406.2 ERI Compliance. Compliance based on the Energy Rating Index (ERI) requires that the rated design and as- built dwelling unit meet meets all of the following: Commented [A44]: Amendment deleted as no longer needed. Commented [A45]: Table updated to match model code updates, retain prior local amendments and include new local amendments. 1. The requirements of the sections indicated within Table R406.2. 2. Maximum ERI value indicated in of Table R406.5. Table R406.2 REQUIREMENTS FOR ENERGY RATING INDEX TITLE General Additional energy efficiency Certificate Building Thermal Envelope SECTIONa R401.2.5 R401.3 R402.1.1 R402.1.6 R402.2.3 R402.2.4 R402.2.4.1 R402.2.5.1 R402.2.10 R402.2.10.1 R402.2.11 R402.3 R402.5.1.1 R402.4 R402.5.1.2 R402.5.1.3 R402.5.2 R402.5.3 R402.5.4 R402.5.5 R402.5 R402.6 R402.6 R406.3 Vapor retarder Rooms containing fuel burning appliances Eave baffle Access hatches and doors insulation installation and retention Slab-on-grade floors Crawl space walls insulation installations Radiant barriers Installation Air Leakage testing Maximum air leakage rate Fireplaces Fenestration air leakage Recessed lighting Air-sealed electrical and communication outlet boxes (air sealed boxes) Maximum fenestration U-factor and SHGC Radiant Barrier Building thermal envelope Mechanical system piping insulation Service hot water systems Heated water circulation and temperature maintenance systems Drain water heat recovery units Demand Response of Electric Resistance Water Heating Mechanical ventilation Equipment sizing and efficiency rating Systems serving multiple dwelling units Space heating Energy consumption of pools and spas Portable spas Residential pools and permanent residential spas Mechanical R403.1 R403.2 R403.3, except Sections R403.3.2, R403.3.3, R403.3.10 Ducts systems and Additional HVAC Testing R403.4 R403.5 R403.5.1 except Section R403.5.2 Controls Hot water boiler temperature reset R403.5.3 R403.5.4 R403.6 R403.7, except Section R403.7.1 R403.8 R403.9 R403.10 R403.11 R403.12 Page 22 of 25 R403.14 Electrical Power and Lighting Systems Gas fireplaces R404.1 R404.2 R406.3 Chapter 7 [RE] Appendix RE Appendix RJ Appendix RK a Reference to a code section includes all the relative subsections except as indicated in the table. Lighting equipment Interior lighting controls Building thermal envelope Residential Solar Ready Electric Vehicle Power Transfer Demand Responsive Controls Electric Readiness R406.3.2 On-site renewables are included. Where on-site renewable energy is included for compliance using the ERI analysis of Section R406.4, the building thermal envelope shall be greater than or equal to the levels of efficiency and SHGC in Table R402.1.2 or Table R402.1.4 of the 2015 International Energy Conservation Code as amended by Ordinance No. 20160623-099. Commented [A46]: Amendment deleted as content is now covered by model code. Backstop updated in model code to no longer refer to a prior code. R406.4 Energy Rating Index. The Energy Rating Index (ERI) shall be determined in accordance with RESNET/ICC 301 except for buildings covered by the International Residential Code, the ERI Reference Design Ventilation rate shall be in accordance with Equation 4-2. The ERI shall consider all energy used in the residential building. Commented [A47]: Amendment deleted as no longer needed. Ventilation rate, CFM = (0.01 × total square foot area of house) + [7.5 × (number of bedrooms + 1)] Energy used to recharge or refuel a vehicle used for transportation on roads that are not on the building site shall not be included in the ERI reference design or the rated design. For compliance purposes, any reduction in energy use of the rated design associated with on-site renewable energy shall not exceed 5 percent of the total energy use. TABLE R406.5 MAXIMUM ENERGY RATING INDEX CLIMATE ZONE 2 ENERGY RATING INDEX 59 R503.1.1.1 Replacement fenestration. Fenestration Alterations. Where new fenestration area is added to an existing building, the new fenestration shall comply with Section R402.4. Where some or all of an existing fenestration unit is replaced with a new fenestration product, including sash and glazing, the replacement fenestration unit shall meet the applicable requirements for U-factor and SHGC as specified in Table R402.1.3(1). Where more than one replacement fenestration unit is to be installed, an area-weighted average of the U-factor, SHGC or both of all replacement fenestration units shall be an alternative that can be used to show compliance. CHAPTER 7 [RE] Residential Solar Ready R701.1 Residential Solar Ready. New Residential Buildings must have a Solar-Ready Zone. A Solar-Ready Zone is a section or sections of the roof or building structure designated and reserved for future installation of a solar photovoltaic or solar thermal system. The Solar-Ready Zone must not include areas shaded by parts of the building or other obstructions. Commented [A48]: Amendment deleted to revert to model code requirements. Commented [A49]: Updated to match model code updates. Points to new fenestration requirements when new fenestration is being installed in an alteration. Commented [A50]: Definition for solar-ready zone now exists in Definitions section in Chapter 2. R701.2 Construction document requirements for Solar-Ready Zone. Construction documents must indicate the Solar-Ready Zone on a roof plan. Commented [A51]: This requirement is now included in R105.2.2 with other Construction Documents requirements. R701.3 R701.2 Obstructions. Solar-Ready Zones must be free from and not shaded by obstructions, including but not limited to vents, chimneys, parapets and roof-mounted equipment. Commented [A52]: Renumbering due to deletion of R701.2 R701.4 R701.3 Electrical Service Reserved Space. The main electrical service panel must have a reserved space to allow installation of a dual pole circuit breaker for future solar electric installation and must be labeled "For Solar Electric." The reserved space must be positioned at the opposite (load) end from the input feed location or main Page 23 of 25 circuit location. Wall area must have a reserved space to allow installation of an Austin Energy PV meter per the Austin Energy Design Criteria manual. R701.5 R701.4 One-family and Two-family Dwellings. New detached one-family or two-family dwellings must have a total Solar-Ready Zone area of not less than 240 square feet (22.3 m2 ) per dwelling, exclusive of required access or setback areas. The Solar-Ready Zone must be oriented between 90 and 300 degrees of true North. The Solar-Ready Zone must comprise areas not less than six feet (1.83 m) on one side and at least one area of not less than 100 square feet (9.29 m2 ) exclusive of any required access or set back areas. Exceptions: 1. A Building with less than 800 square feet (74.32 m2 ) of roof area per dwelling unit. 2. A Building with a Solar-Ready Zone that is shaded by trees or adjacent structures for more than 50 3. A Building Site on which the applicant has demonstrated, through documentation, existence of a unique percent of annual daylight hours. hardship preventing compliance. 4. New residential buildings with a permanently installed on-site renewable energy system with an output of not less than one watt per square foot (0.092 m2 ) of conditioned floor area, or an on-site renewable energy system with a total output of at least two kilowatts. R701.6 R701.5 Townhomes Townhouses. Townhomes New Townhouses must have a total Solar-Ready Zone area of not less than 160 square feet (14.86 m2 ) per dwelling townhouse unit, exclusive of required access or setback areas. The Solar-Ready Zone must be oriented between 90 and 300 degrees of true North. The Solar-Ready Zone must comprise areas not less than six feet (1.83 m) on a side and at least one area of not less than 100 square feet (9.29 m2 ) exclusive of required access or set back areas. 1. Dwellings Townhouses with less than 600 square feet (55.74 m2 ) of roof area per dwelling townhouse 2. A building with a Solar-Ready Zone that is shaded by trees or adjacent structures for more than 50 percent 3. A Building Site on which the applicant has demonstrated, through documentation, existence of a unique of annual daylight hours. hardship preventing compliance. R701.7 R701.6 Multifamily Buildings. New multifamily buildings of four stories or fewer must have a Solar-Ready Zone that is not less than 35% of the total roof area of the building. 1. A building with a Solar-Ready Zone that is shaded by trees or adjacent structures for more than 50 percent 2. A Building Site on which the applicant has demonstrated, through documentation, existence of a unique of annual daylight hours. hardship preventing compliance. RJ101.1 Demand Responsive Water Heating. Electric storage water heaters with a rated water storage volume of 40 gallons (150 L) to 120 gallons (450 L) and a nameplate input rating equal to or less than 12 kW shall be provided with demand responsive controls in accordance with Table RJ101.1. Exceptions: unit. Exceptions: Exceptions: 1. Water heaters that are controlled by a preprogrammed water heater timer. The timer shall be preprogrammed to turn the water heater off between the hours of 3:00 p.m. and 7:00 p.m. from June 1 to September 30. The timer shall have a readily accessible override, as defined by the building official, Page 24 of 25 Commented [A53]: Added requirement for the reservation of wall space to be ready for future installation of PV meter. Commented [A54]: Updated "townhome" lang to "townhouse: since it is a defined term in Ch2 Commented [A55]: Updated "townhomes" and "dwellings" to "townhouses" as townhouses is a defined term. Added "New" to align with R701.4 and R701.6. Commented [A56]: 2024 IECC model code added demand response code language for electric storage water heaters in Appendix RJ. Local amendment already existed. Local amendment, R403.5.4 deleted and updated to mirror model code in Appendix RJ. Allowance added for timers in the exceptions. capable of restoring power to the water heater for one hour when activated. The timer shall be permanently programmed by the manufacturer or locked to prevent alteration of the programming by the building occupants. Buildings that are accessory to a residential building are considered residential buildings for the purposes of this section. 2. Water heaters that are capable of delivering water at a temperature of 180°F (82°C) or greater. 3. Water heaters that comply with Section IV, Part HLW or Section X of the ASME Boiler and Pressure Vessel Code. 4. Water heaters that use 3-phase electric power. Exceptions: 1. 2. RK101.1 Electric readiness. Water heaters, household clothes dryers and cooking appliances that use fuel gas or liquid fuel shall comply with Sections RK101.1.1 through RK101.1.4 RK101.1.5. RK101.1.5 Water Heater Space. A space that is at least 3 feet (0.91 m) by 3 feet (0.91 m) wide by 7 feet (2.13) high shall be available surrounding or within 3 feet (0.91 m) of the installed water heater. Installed heat pump water heaters. Installed tankless water heaters on the exterior of the dwelling unit. 3. Water heaters serving multiple dwelling units in a R-2 occupancy. Commented [A57]: Updated to include additional requirement, RK101.1.5. Commented [A58]: Local amendment to include water heater space requirement originally included in code proposal from DOE. Water heater space requirement included in DOE Zero Energy Ready Home, California Title 24, Massachusetts Specialized Stretch Code, and New York State Energy Code. Water heater space requirement requested by Austin Electric Utility Commission. Page 25 of 25