5.3 - 6301 Bluff Springs Rd - Sebron Sneed - 2015 Staff report — original pdf
Backup
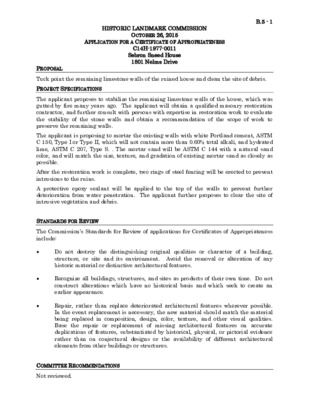
HISTORIC LANDMARK COMMISSION OCTOBER 26, 2015 APPLICATION FOR A CERTIFICATE OF APPROPRIATENESS C14H-1977-0011 Sebron Sneed House 1801 Nelms Drive B.5 - 1 PROPOSAL PROJECT SPECIFICATIONS Tuck point the remaining limestone walls of the ruined house and clean the site of debris. The applicant proposes to stabilize the remaining limestone walls of the house, which was gutted by fire many years ago. The applicant will obtain a qualified masonry restoration contractor, and further consult with persons with expertise in restoration work to evaluate the stability of the stone walls and obtain a recommendation of the scope of work to preserve the remaining walls. The applicant is proposing to mortar the existing walls with white Portland cement, ASTM C 150, Type I or Type II, which will not contain more than 0.60% total alkali, and hydrated lime, ASTM C 207, Type S. . The mortar sand will be ASTM C 144 with a natural sand color, and will match the size, texture, and gradation of existing mortar sand as closely as possible. After the restoration work is complete, two rings of steel fencing will be erected to prevent intrusions to the ruins. A protective epoxy sealant will be applied to the top of the walls to prevent further deterioration from water penetration. The applicant further proposes to clear the site of intrusive vegetation and debris. STANDARDS FOR REVIEW The Commission’s Standards for Review of applications for Certificates of Appropriateness include: • Do not destroy the distinguishing original qualities or character of a building, structure, or site and its environment. Avoid the removal or alteration of any historic material or distinctive architectural features. Recognize all buildings, structures, and sites as products of their own time. Do not construct alterations which have no historical basis and which seek to create an earlier appearance. Repair, rather than replace deteriorated architectural features wherever possible. In the event replacement is necessary, the new material should match the material being replaced in composition, design, color, texture, and other visual qualities. Base the repair or replacement of missing architectural features on accurate duplications of features, substantiated by historical, physical, or pictorial evidence rather than on conjectural designs or the availability of different architectural elements from other buildings or structures. • • COMMITTEE RECOMMENDATIONS Not reviewed. B.5 - 2 STAFF COMMENTS This site has been deteriorating for years; the applicant is proposing to correct the conditions on the site and preserve the ruins as the centerpiece of a proposed housing development surrounding the ruins. The applicant’s formula for tuck-pointing the limestone walls is in conformance with the repointing standards promulgated by the City of Austin and the Texas Historical Commission for historic structures. STAFF RECOMMENDATION Approve the application for repointing and sealing the tops of the limestone walls for stability and the prevention of further deterioration, but reserve the right to determine any further stabilization measures necessary for the long-term preservation of the walls, especially in light of the proposed housing development that will surround the ruins in the future. Staff further recommends that any fallen rock found on the site be retained on the site and re-used to the greatest extent possible, but that the remaining vegetation and debris on the site be cleared. In addition, staff recommends that the applicant follow the directives from a preservation professional regarding the repairs and stabilization of the walls: • This project should not, under any circumstances, take its cues from a Quikcrete AtHome video. This is not an appropriate project for that product or skill set. If a Quikcrete repair mix is used, it will do more harm than good. In fact, this video is for cosmetic, non-structural repairs - that is certainly not what we are dealing with here. It uses a “sanded acrylic caulk” - also not appropriate or in accord with the other specifications. The type of repair illustrated in this video is not applicable to this project in any way. • The original mortar does not have Portland cement in it- that is for certain. The city’s weaker mortar formula may be OK, but the architect’s specs don’t identify a mortar mix. Portland cement, if used at all, should be Type I, non-staining, white, complying with ASTM C 91 for not more than 0.03% water soluble alkali. • Quicklime should not be used - this is a temperamental material that requires careful handling. Slaking of quicklime takes 60-90 days - impractical for this project. • There needs to be a mortar analysis completed to determine the character of the original mortar. The sand likely does not include 'marble, granite, or other sound stone' in the aggregate, unless it’s small chunks of limestone. Cates Lab in Dallas will do a helpful analysis of a good-sized original mortar sample for $250. It will identify the proportions of aggregate to binder, the character of the binder (lime), and isolate the sand so that it can be matched in color and grain size. The sand used originally was likely harvested from a nearby waterway. Matching sand will hopefully be found from a local supplier without much trouble. • They need to define a "qualified masonry restoration subcontractor.” I’d recommend someone with at least 10 years demonstrated experience in working with historic, load bearing masonry structures. They will also need insurance. • The definition of “Tuck pointing” to a mason means that only the outer 3/8” of mortar requires replacement. That is not the case in this project. The walls need structural repointing, and many joints may require several lifts of mortar to complete the work. The term “repointing” should be used. Some full reconstruction may be needed at the tops of the existing walls, depending on the level of deterioration likely at these very exposed areas. B.5 - 3 • Neither the city spec nor the architect’s spec address joint preparation for repointing. Proper joint preparation needs to include manual removal of loose and unsound mortar from the joints (no power tools). Given the extent of deterioration, proper joint preparation will surely require supplemental structural bracing in order to safely perform the work. New mortar is installed in lifts no more than 3/8” thick at a time. Once a lift has cured for a few days, another lift is installed. This could take several passes in the more deteriorated areas. • The finished mortar joints should be tooled to avoid overrun on the stone, or • “feathering". You don’t want the mortar to be so thin at the edges that it will separate from the stone and create new pathways for water to enter the wall. The surface of the stone should be cleaned of any excess mortar prior to curing. I strongly recommend and support structural bracing of the walls. Many of them have inadequate support and, without a doubt, require structural bracing. This needs to be carefully and sensitively designed for practicality, durability, maintenance, and aesthetics. • Scaffolding will be required to complete the work. There needs to be some discussion about how to stage that scaffolding, and that they cannot be allowed to attach scaffolding to the ruins. The installation of scaffolding needs, also, to be coordinated with the structural shoring that will remain in place after the project is complete. • Many fallen stones will need to be relocated on site so that the scaffold can be installed. This process needs to be thought out, and completed in a way that does not damage the stone. • The epoxy coating of the cap stones is not appropriate or reversible. The epoxy would be much harder than the stone, and would surely cause the stone to delaminate over time, allowing water to re-enter the wall and conceal eventual internal deterioration. I’d recommend a lime-based sacrificial coating instead. Further research is needed to determine the best treatment for this situation. • The directive to ‘apply/inject epoxy where deem required’ needs to be reconsidered in consultation with a structural engineer and restoration architect. As stated above, epoxy is much harder and stronger than stone (http://www.epoxy.com/strength.aspx). It has a different coefficient of expansion as well, which could accelerate deterioration of this very exposed wall. B.5 - 4 MASONRY REPOINTING PROCEDURES FOR HISTORIC BUILDINGS HIRING A MASON: All repointing work should be performed by a firm with not less than five years satisfactory experience performing masonry work, and at least three (3) prior projects performing repointing work on historic buildings or structures. Require the contractor to provide a list of completed projects, and written agreement to follow these specifications. PROJECT CONDITIONS: Do not repoint mortar joints or repair masonry unless air temperatures are between 40° F and 80° F and will remain so for at least 48 hours after completion of work. B.5 - 5 Prevent mortar used in repointing and repair work from staining surface of surrounding masonry and other surfaces. Immediately remove mortar in contact with exposed masonry and other surfaces. Protect sills, ledges and projections from mortar droppings. SEQUENCING/SCHEDULING: Perform masonry restoration in the following sequence: Rake out existing mortar from joints indicated to be repointed. Remove mortar using hand tools only. Do NOT use electric or pneumatic chisels. Do not spall or chip masonry. Any damaged masonry must be repaired. Clean joints with water rise with maximum 100-psi pressure. Masonry joint should be damp but without standing water. Perform field test of repointing work on masonry (a 3' X 3' area on the least visible masonry facade). Contact City Historic Preservation Office for approval of field test prior to continuing with work. See additional information below. Repoint existing mortar joints for remainder of structure or building, or as specified by project. See additional information below. Clean existing masonry surfaces. Clean mortar from masonry face promptly to prevent staining. After 24 hours of set time, scrub and wash surface to remove laitance. Do not use muriatic, hydrochloric or hydrofluoric acid for cleaning. Do not use wire brushes. MORTAR MATERIALS: CEMENT: ASTM C 150, Type II, white. For stonework and other masonry indicated, provide non-staining white cement complying with staining requirement of ASTM C91 for not more than 0.03% water-soluble alkali. HYDRATED LIME: ASTM C 207, Type S, high plasticity, (not air entrained). AGGREGATE: ASTM C 144, unless otherwise indicated. SAND: Use natural sand, clean, sound and washed. Provide sands that will produce final mortar color and texture to match the existing, and with aggregate type and grading similar to existing mortar. The color of the sand shall be the primary factor used to make mortars which match original. WATER: Clean, free of oils, acids, alkalis, and organic matter. No antifreeze compounds or other admixture shall be used. MORTAR MIXES: MEASUREMENT AND MIXING: Measure cementitious and aggregate material in a dry condition by volume or equivalent weight. Do not measure by shovel, use known measure. Mix materials in a clean mechanical batch mixer. MIXING POINTING MORTAR: Thoroughly mix cementitious and aggregate materials together before adding any water. Then mix again adding only enough water to produce a damp, unworkable mix that will retain its form when pressed into a ball. Maintain mortar in this B.5 - 6 dampened condition for 1-2 hours. Add remaining water in small portions until mortar of desired consistency is reached. Use mortar within 30 minutes of final mixing; do not retemper or use partially hardened material. ADMIXTURES: Do not use admixtures of any kind in mortar. Tools: Use a pointing tool sized and shaped to the proper width for the joint being pointed. Match the profile and tooling of the existing joints exactly. Apply mortar using wooden trowel to simulate the original mortar coating. MORTAR PROPORTIONS: Specifications NEW POINTING MORTAR MUST MATCH ORIGINAL IN COLOR, COMPOSITION, TEXTURE, AND TOOLING. The original mortar should be carefully analyzed by a person trained in this field. MIX PROPORTIONS BELOW ARE EXAMPLES ONLY AND MUST BE REVISED TO SUIT PROJECT REQUIREMENTS ONCE EXISTING MORTAR HAS BEEN ANALYZED. THE FINAL MORTAR MIX SHALL HAVE NO MORE THAN 20% OF THE TOTAL VOLUME OF THE LIME AND PORTLAND CEMENT - COMBINED - OF PORTLAND CEMENT . TO RANGE OF ACCEPTABLE POINTING MORTAR: 1/10 part white Portland cement 3 parts lime 12 parts natural sand Water TEST SAMPLE: Prepare one test sample at inconspicuous location. Test sample shall be approximately 9- square feet in size, and let cure at least 72 hours. Protect test sample from dirt and moisture. Contact the City Historic Preservation Office to review the test sample once sample has cured, and only proceed with project once City Historic Preservation Office is obtained. Revised 10/14/02 Dear Steve, 1 part white Portland cement 4 parts lime 15 parts natural sand Water Thank you for your time meeting with Mr. Saeed Minhas, the project owner, and me, the Architect o n Record, for the stone restoration of the subject project. We would like to propose that the owner will immediately undertake the process of obtaining a qualified Masonry Restoration Contractor to begin the preservation work. B.5 - 7 Upon such time of selecting the Contractor, we will explore and consult with persons with expertise in these restoration areas: we will evaluate the stability of the stone walls with a detailed Observation Report, and obtain a Recommendation of the scope of work. Mortar specification is based on Sec. 04902 - 1.1 MORTAR MATERIALS Add specific requirements to suit Project. A. Portland Cement: ASTM C 150, Type I or Type II. 1. Provide white cement containing not more than 0.60 percent total alkali when tested according to ASTM C 114. 2. Low-Alkali Cement: Portland cement for use with limestone shall contain not more than 0.60 percent total alkali when tested according to ASTM C 114. B. Hydrated Lime: ASTM C 207, Type S. Product below must be slaked before it is used. C. Quicklime: ASTM C 5, pulverized lime. D. Factory-Prepared Lime Putty: Screened, fully-slaked lime putty, prepared from pulverized lime complying with ASTM C 5. E. Mortar Sand: ASTM C 144, unless otherwise indicated. 1. Color: Provide natural sand[ or ground marble, granite, or other sound stone]; of color necessary to produce required mortar color. 2. For pointing mortar, provide sand with rounded edges. 3. Match size, texture, and gradation of existing mortar sand as closely as possible. Blend several sands, if necessary, to achieve suitable match. If known, indicate source of sand and size and gradation. G. Water: Potable. The main effort of restoration will be concentrated in the stabilization of the "Ruins", by ways of "Tuck Pointing" with specified Tuck-pointing Mortar (referencing to the Video: B.5 - 8 http://quikrete.com/AtHome/Video-Tuckpointing-Mortar- Joints.asp?gclid=CO36tfK30sgCFQmJaQod3F8ACw ) , and apply/inject epoxy where deem required. Structural Bracing is not considered at this point. Please note the Limit of Restoration will be as shown on the attached Ruin Site, and the Structure -35'-0" x 58'-7". After such restoration work is completed, two rings of steel fencing, surrounding the "Ruins" will be erected to prevent intrusions. We thank you for your time and consideration. Please let us know if any other measures you would like to explore. Sincerely, Tracy T. Chen, NCARB Principal Tchen Architects 11908 Anderson Mill Road, #325 Austin, Texas 78726 C. 512.351.1801 F. 512.870.9427 http://www.tchenarch.com "A Cheerful heart is good medicine, crushed spirit dries up bones."