C.13.1 - 1616 Northumberland Rd - plans — original pdf
Backup
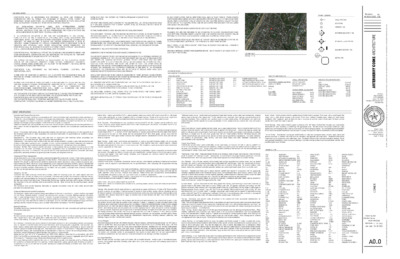
GENERAL NOTES CONTRACTOR SHALL BE RESPONSIBLE FOR PROVIDING ALL WORK AND MATERIALS IN CONFORMANCE WITH ALL CODE(S) AND GUIDELINES OF FEDERAL, STATE, COUNTY AND MUNICIPALITY HAVING JURISDICTION. ALL APPLICABLE REQUIREMENTS IN THESE REGULATIONS SHALL BE FOLLOWED THE SAME AS IF NOTED ON THE DRAWINGS, INCLUDING: INTERNATIONAL 2021 CONSERVATION CODE, 2015 Uniform PLUMBING CODE, 2015 Uniform MECHANICAL CODE, 2017 NATIONAL ELECTRICAL CODE, AND THE 2015 INTERNATIONAL FIRE CODE WITH STATE AND LOCAL AMENDMENTS AS ADOPTED BY THE LOCAL JURISDICTION. RESIDENTIAL IF THE CONTRACTOR ASCERTAINS AT ANY TIME THAT REQUIREMENTS OF THIS CONTRACT CONFLICTS WITH, OR ARE IN VIOLATION OF, APPLICABLE LAWS, CODES, REGULATIONS AND ORDINANCES, HE SHALL NOT PROCEED WITH WORK IN QUESTION, EXCEPT AT HIS OWN RISK, UNTIL ARCHITECT HAS BEEN NOTIFIED IN WRITING AND WRITTEN DETERMINATION IS MADE BY ARCHITECT. WHERE COMPLETED OR PARTIALLY COMPLETED WORK IS DISCOVERED TO BE IN VIOLATION WITH APPLICABLE LAWS, CODES, REGULATIONS AND/OR ORDINANCES, THE CONTRACTOR SHALL BE REQUIRED TO REMOVE THAT WORK FROM THE PROJECT AND REPLACE WITH ALL NEW COMPLYING WORK AT NO ADDITIONAL COST TO OWNER. CONTRACTOR SHALL PROVIDE PUBLIC PROTECTION AS REQUIRED PER GOVERNING AGENCY AND CODE REQUIREMENTS. CONTRACTOR SHALL BE RESPONSIBLE FOR INSTALLING ANY TEMPORARY SHORING AND BRACING TO INSURE THE SAFETY OF THE WORK. THE CONTRACTOR SHALL COORDINATE ALL REQUIREMENTS OF THE AUTHORITIES HAVING JURISDICTION FOR SIDEWALKS, DRIVEWAYS, CURBS, GUTTERS, STREETLIGHTS, EASEMENTS, UTILITIES, FENCES, SIGNS, BARRICADES, ETC. ADJACENT TO THE PROPERTY, AND SHALL OBTAIN ALL NECESSARY PERMITS AND APPROVALS. CONTRACTOR SHALL COORDINATE ALL MECHANICAL, PLUMBING, ELECTRICAL, AND ARCHITECTURAL WORK. NOISE, DUST, DIRT, FIRE HAZARDS AND POTENTIAL PROBLEMS CAUSED BY SUCH CONSTRUCTIONS. PROPERTY AND PREMISE LINES ADJACENT TO THE BUILDING SHALL BE ESTABLISHED IN THE FIELD BY A LICENSED SURVEYOR AND A SURVEY REPORT SHALL BE AVAILABLE ON SITE PRIOR TO FOUNDATION INSPECTION. FUTURE OWNER IMPROVEMENTS REQUIRE SEPARATE BUILDING PERMITS. THIS DOCUMENT, THE IDEAS, AND THE DESIGNS INCORPORATED HEREIN, AS AN INSTRUMENT OF PROFESSIONAL SERVICE, IS THE PROPERTY OF THE ARCHITECT AND IS NOT TO BE USED IN WHOLE OR IN PART, FOR ANY PROJECT WITHOUT THE WRITTEN AUTHORIZATION OF THE ARCHITECT. LARGER SCALE DRAWINGS SHALL HAVE PRECEDENCE OVER THOSE OF SMALLER SCALE. WHERE DISCREPANCIES ARE FOUND BETWEEN THE ARCHITECTURAL DRAWINGS AND THOSE OF OTHER CONSULTANTS, THE ARCHITECTURAL DRAWINGS SHALL GENERALLY BE ASSUMED TO GOVERN. DIMENSIONS SHALL HAVE PREFERENCE OVER SCALE. DIMENSIONS ARE TO FINISHED SURFACES UNLESS OTHERWISE NOTED. IN NEW CONSTRUCTION SMOKE DETECTORS SHALL RECEIVE THEIR PRIMARY POWER SOURCE FROM THE BUILDING WIRING AND SHALL BE EQUIPPED WITH BATTERY BACK UP AND LOW BATTERY SIGNAL. SMOKE DETECTORS SHALL BE LOCATED IN EACH SLEEPING ROOM & HALLWAY OR AREA GIVING ACCESS TO A SLEEPING ROOM, AND ON EACH STORY AND BASEMENT FOR DWELLINGS WITH MORE THAN ONE STORY. PROVIDE CARBON MONOXIDE ALARM OUTSIDE EACH SLEEPING AREA PLUMBING FIXTURES ARE REQUIRED TO BE CONNECTED TO SANITARY SEWER.KITCHEN SINKS, LAVS, BATHTUBS, SHOWERS, BIDETS, LAUNDRY TUBS, AND WASHING MACHINE OUTLETS SHALL BE PROVIDED WITH HOT AND COLD WATER AND CONNECTED TO APPROVED WATER SUPPLY. EXTEND THROUGH ROOF FLUES AND VENTS UP THROUGH ROOF IN ACCORDANCE WITH THE IRC TO ACHIEVE REQUIRED CLEARANCES. FLASH AND SEAL ALL ROOF PENETRATIONS. NEWLY INSTALLED BATHROOM EXHAUST FANS SHALL BE ENERGY STAR AND SHALL TERMINATE OUTSIDE THE BUILDING. PROVIDE EMERGENCY EGRESS FROM SLEEPING ROOMS. MIN 24" CLEAR HT, 20" CLEAR WIDTH, 5.7 SQFT AND 44" MAX TO SILL) VICINITY MAP SCALE : N.T.S. THE ARCHITECT HEREBY STATES THAT SHE HAS NO KNOWLEDGE OF ANY POSSIBLE EXISTENCE OF HAZARDOUS MATERIALS AT THIS SITE AND THAT SHE CANNOT AND WILL NOT BE HELD LIABLE FOR ANY UNSEEN OR UNKNOWN HAZARDOUS MATERIAL RELATED CONDITIONS THAT MAY ARISE DURING THE WORK. IF SUCH CONDITIONS SHOULD BE DISCOVERED THE CONTRACTOR SHALL STOP ALL WORK IMMEDIATELY AND NOTIFY THE OWNER OF SUCH. THE OWNER SHALL BE RESPONSIBLE FOR MAKING ARRANGEMENTS FOR THE SAFE AND LEGAL REMOVAL OF HAZARDOUS MATERIAL AND REMEDYING ANY HAZARDOUS CONDITIONS AS REQUIRED BY THE GOVERNING AUTHORITIES. THE CONTRACTOR SHALL NOT BE EXPECTED TO RESUME WORK UNTIL SUCH REMOVALS ARE EFFECTED IN A SAFE AND LEGAL MANNER. SYMBOL LEGEND Revisions By #1 05-01-2022 MJS X X X X AX.X TP X AX.X BT X AX.X WALL TYPE TAG DOOR TAG WINDOW TAG EXTERIOR ELEVATION TAG LF RT INTERIOR ELEVATION TAG BUILDING SECTION TAG X AX.X DETAIL TAG WHERE WORK OR EQUIPMENT IS INDICATED N.I.C. SUCH WORK AND OR EQUIPMENT SHALL BE PROVIDED BY OTHERS. CONTRACTOR SHALL COORDINATE AND COOPERATE TO EFFECT SUCH INSTALLATION. DETAILS NOT SHOWN ARE TO BE SIMILAR IN CHARACTER TO THOSE DETAILED. WHERE SPECIFIC DIMENSIONS, DETAILS OR DESIGN INTENT CANNOT BE DETERMINED, OBTAIN CLARIFICATION FROM THE ARCHITECT BEFORE PROCEEDING WITH THE WORK. INFORMATION CONTAINED IN THESE DOCUMENTS WHICH DESCRIBE OR LOCATE EXISTING SITE AND BUILT ELEMENTS, IS BASED ON INFORMATION (DRAWINGS, NOTES, SURVEYS, ETC.) SUPPLIED BY THE OWNER AND/OR HIS ARCHITECTS, AND LIMITED SITE OBSERVATION. THE CONTRACTOR/OWNER'S SUBCONTRACTORS SHALL VERIFY ALL DIMENSIONS AND FINISH CONDITIONS APPLICABLE TO THE WORK DESCRIBED HEREIN. THE CONTRACTOR IS TO SURVEY EXISTING SITE CONDITIONS AS REQUIRED FOR COORDINATION WITH EXISTING UTILITIES AND THEIR CONNECTIONS. WHERE DISCREPANCIES ARE FOUND, THE CONTRACTOR SHALL ADVISE THE OWNER AND THE ARCHITECT. THE CONTRACTOR SHALL TAKE PROTECTION MEASURES THAT WILL BE UTILIZED DURING CONSTRUCTION TO PROTECT ADJOINING AND NEARBY PROPERTIES (PUBLIC AND PRIVATE) FROM ALL DRAWINGS AND NOTES ARE COMPLEMENTARY, AND WHAT IS CALLED FOR BY ANY ONE WILL BE AS BINDING AS IF CALLED FOR BY ALL. SUBSTITUTION OF ACCEPTABLE EQUIVALENTS WILL BE PERMITTED AS APPROVED BY THE ARCHITECT AND/OR OWNER PRIOR TO BID (UNLESS NOTED OTHERWISE) ALL INSULATING MATERIAL SHALL COMPLY WITH THE FLAME SPREAD AND SMOKE DENSITY REQUIREMENTS OF THE 1997 UNIFORM BUILDING CODE. DISSIMILAR METALS SHALL BE EFFECTIVELY ISOLATED FROM EACH OTHER TO PREVENT GALVANIC ACTION. SCOPE OF WORK new single family residence and pool DRAWING INDEX A0.0 A0.1 A0.2 A0.3 A0.4 A0.5 A0.6 A1.0 A1.1 A1.2 A1.3 A2.0 A2.1 A2.2 A3.0 A3.1 COVER WALL TYPES WINDOW TYPES DOOR TYPES WINDOW/DOOR DETAILS FINISH SCHEDULES FIXTURE SCHEDULES SITE PLAN ZONING EXHIBITS SETBACK PLANES SETBACK TENTS FIRST FLOOR PLAN SECOND FLOOR PLAN ROOF PLAN EXTERIOR ELEVATIONS EXTERIOR ELEVATIONS A3.2 A3.3 A4.0 A4.1 A4.2 A4.3 A5.0 A5.1 A5.2 A5.3 A5.4 A6.0 A6.1 A6.2 A7.0 A7.1 EXTERIOR ELEVATIONS EXTERIOR ELEVATIONS BUILDING SECTIONS BUILDING SECTIONS BUILDING SECTIONS BUILDING SECTIONS WALL SECTIONS WALL SECTIONS WALL SECTIONS WALL SECTIONS WALL SECTIONS DETAILS DETAILS DETAILS INTERIOR ELEVATIONS INTERIOR ELEVATIONS PROJECT INFORMATION A7.2 E1.0 E1.2 M1.0 M1.1 INTERIOR ELEVATIONS FIRST FLOOR ELECTRICAL PLAN SECOND FLOOR ELECTRICAL PLAN FIRST FLOOR MECHANICAL PLAN SECOND FLOOR MECHANICAL PLAN 1616 NORTHUMBERLAND ROAD AUSTIN, TX 78703 LOT 27* & E 25 FT OF LOT 26 PLEASE ESTATES SEC 3 ADDRESS LEGAL DESCRIPTION PROJECT SQUARE FOOTAGES: ZONING SF-3 LOT AREA 9,374 SQFT .215 ACRES DEVELOPMENT REGULATION MAX HEIGHT: FRONT SETBACK: REAR SETBACK: SIDE SETBACK: BUILDING AREA: IMPERVIOUS AREA: 32 FT 25 FT 10 FT 5 FT 40% 45% LOT: FIRST FLOOR: SECOND FLOOR: ATTIC: GARAGE/CARPORT: COVERED FRONT PORCH: COVERED BACK PORCH: COVERED BALCONY: 9,374 SF 2,552 SF 869 SF 854 SF 529 SF 14 SF 578 SF 132 SF Execution and Closeout Requirements The execution of all work shall be in strict accordance with these specifications and manufacturer's written specifications or Material's Institute Standards. Contractor to investigate proposed product substitutions and determine that they are equal or superior in all respects to products specified. Coordinate installation of accepted substitutions into the Work, making such changes as may be required for the Work to be complete in all respects. Where the manufacturer's recommended details are used, the manufacturer shall be responsible for the performance of their product. All work not specifically mentioned that is required to make the work complete and operational shall be included. Codes - Construction shall comply with all applicable national, state and local building codes. It is the responsibility of the Contractor and Owner to insure compliance with said codes and modify the specifications as needed to comply with such codes. Measurements - The Contractor shall check and verify all dimensions and conditions before proceeding with construction. Do not scale drawings. Noted dimensions take precedence. Workmanship - Workmanship shall conform to the best and highest standards of quality in each trade and shall include all items of fabrication, construction and installation. All work shall be completed by skilled tradesmen and mechanics. Installation of all equipment and materials shall be in strict accordance with manufacturers recommendations. Insurance - Builders Risk Insurance shall be maintained by the contractor during the course of construction until final acceptance by the owner. All bonding and insurance requirements shall be coordinated with the Owner prior to beginning construction. All contractors shall provide and be solely responsible for necessary barricades and safety precautions, and strictly adhere to all governing codes on safety, including the OSHA Act. Cleaning and Waste Management Construction site to be in a clean and orderly condition throughout the construction process. Clean interior spaces prior to the start of finish painting and the application of other finishes. At the conclusion of construction, the project shall be cleaned. This should include but not be limited to; cleaning the interior and exterior glass, surfaces exposed to view, remove temporary labels, stains and foreign substances, polish transparent and glossy surfaces, vacuum carpeted and soft surface areas, sweep and mop all tiled surfaces, etc. Replace filters of operating equipment. Clean equipment and fixtures to a sanitary condition. Clean exterior such as debris from roof, gutters, landscape areas, driveways and walks, etc. Remove all waste and store surplus materials. Temporary Facilities Contractor shall make necessary connection to existing utilities for temporary power and water supplies and shall coordinate such use with the Owner prior to connection. Contractor shall provide and maintain in a neat and sanitary condition such accommodations for the use of his employees as will comply with laws and regulations. Temporary toilet facilities may consist of portable toilets. Toilet facilities shall be kept supplied and clean and in sanitary condition until the completion of the work and then shall be removed from the site. Upon removal, the site shall be properly cleaned and graded. The Contractor shall provide temporary barricades to separate construction areas for public safety around entire perimeter of construction area. Protecting Materials and Installed Construction The Contractor shall provide a material storage area adjacent to the area of construction. Location shall be coordinated with the Owner. Materials shall be protected from rain and other sources of moisture. Building materials with visible signs of water damage shall not be installed. Contractor to protect all installed construction. If products or materials come with a protective coating, contractor shall maintain protective coating until construction is complete. Contractor shall replace any items that become defective or damaged. All ducts and other related mechanical supply and return openings shall be covered with tape, plastic, or sheet metal until the final startup of the HVAC Equipment. Existing Conditions Contractor shall review construction documents and provide necessary site work, excavation and grading as required to construct said project. Crawlspace Provide covered crawlspace ventilation per IRC 408. The minimum net area of ventilation openings shall be not less than 1 square foot for each 150 square feet of under floor area. One ventilation opening shall be within 3 feet of each corner of the building. Provide a 24” x 48” minimum access door to crawlspace. Brick Masonry - Contractor shall review construction documents and provide labor and materials pertaining to masonry work as required in said documents and as specified herein, while complying with all applicable building codes. Dry brush masonry surface at the end of each day's work and after final pointing using wire brushes to remove mortar but exercise care not to scratch or damage work. Final cleaning of masonry to occur minimum 7 days after masonry work is completed. Comply with recommendations of manufacturers of chemical cleaners for protecting building surfaces, landscape, persons and property against damage from exposure to their products. Mortar shall be Type “M” or “S” in accordance with ASTM C270, 2500 psi. Grout shall be in accordance with ASTM C270, Type M, 2500 psi concrete using pea gravel for coarse aggregate with a maximum aggregate size of 3/8” and an 8” minimum to 11” maximum slump. Mortar joints thickness and profile to match existing Continuous flashing shall be installed at the bottom of the wall, above grade, with weepholes at 32" oc. Flashing should be installed at the heads and sills of all openings. Provide weep-holes, spaced approximately 32 inches on center in vertical joints of first course and over all counter flashing and through wall flashing on exterior walls. Units with size, color and shape TBD. Interior Walls - Interior walls shall be 2”x4” or, where plumbing stacks are present, 2"x6" wood studs at 16" oc, with single bottom plates and double top plates throughout; refer to structural drawings. Provide solid blocking at mid-height of all walls which exceed 9'-0” in height and additional blocking as shown on these drawings or required by code. Finish Carpentry - All architectural trim and woodwork shall be primed FJ pine No. 1 grade material suitable for paint finishes. Wood that will be stained shall be clear of knots with concealed joints. Provide and install interior wood trim as shown on interior drawings/schedule. Wood Stairs - Generally the vertical dimension of each riser should be no more than 7.5" and the horizontal dimension of each tread will be 11". A minimum of 6'-8” clear headroom is required, measured from the front edge of the tread to a line parallel to the stair run. Stair treads shall be constructed of 5/4” thick finish grade lumber, risers shall be constructed of 3/4” finish grade lumber structural stair stringers shall be constructed of 2”x12”s. Glue and nail stair assembly together. Metal Railings - Install metal hand railings and guardrails to meet all applicable building codes, with appropriate detailing and patterns as shown in construction documents. Metal shall be shop built, welded together, cleaned thoroughly and painted with two coats of an anti-rust primer. After installation, apply an additional coat and anti-rust primer in preparation for finish coats. Exterior Moldings - High-density, durable, non-water absorbing, polyurethane polymer comparable to kiln-dried white pine millwork, with higher skin density. Provide units with manufacturer's standard barrier coat and shop-applied primer to receive field applied finish paint coating. Fasteners, joint compound and adhesive sourced and installed as recommended by manufacturer. Thermal and Moisture Protection Contractor shall review construction documents and provide labor and materials pertaining to thermal and moisture protection work as required in said documents and as specified herein, while complying with all applicable building codes. Dampproofing and Waterproofing - Over studs and sheathing, install one layer of approved moisture barrier overlapped a minimum of 6” except at stucco finish, provide 2 layers. All joints and penetrations in walls, floors, and roofs shall be made watertight using approved methods and materials. Waterproofing and dampproofing recommendations contained herein are minimum, check with local code officials for additional requirements. Thermal Protection - Effective R values shall be in accordance with local and state energy codes. All plumbing chases shall be insulated with batt insulation for sound attenuation. Exterior Walls - Min wail insulation shall be R value of 19. Interior Walls - Install R-11 batt-insulation at bath rooms, plumbing chases, laundry rooms and otherwise specified for sound attenuation. Ceilings - Attic insulation shall be open cell foam w/ vapor barrier (or equal) and have min R-value of 38. Provide baffles at eaves to provide for ventilation. At flat roofs provide 2" closed cell foam in direct contact with roof sheathing with min 10" densely packed, 3.5 lbs/cuft density, blown cellulose between roof/ceiling joists, held in place with breathable mesh suspended from structure (Insulweb or equal) as needed, and in direct contact with foam. Use of Min R-Value of combination is R38. Low-Slope Bituminous Roof System -All roof areas shall be designed and installed to drain without holding water on the roof surface. All roofs shall have an overflow system adjacent to drains or scuppers to collect and direct water off the roof should one or more water collection device fail. All surfaces to which the modified bitumen system is to be installed must be smooth, dry, free from dust or debris, free from settling or distortion, and free from cracks, knotholes, or other defects. Metal flashings must also be primed with a suitable asphalt primer for metal, and primer must be thoroughly dry and any solvents evaporated prior to application of membrane flashing. In angles of roof deck and vertical surfaces, the roofing contractor shall furnish and install an approved cant strip with a minimum 3" face. Multi-ply system consisting of base sheet mechanically attached through insulated substrate, two self-adhered modified interply sheets and self-adhered modified cap sheet. Install per manufacturer's requirements, including fasteners, adhesives, and flashings. Supply min 25yr manufacturer's warranty. Asphalt Shingles Laminated dimensional shingle with Lifetime Warranty. Granule surfaced, self-sealing asphalt shingle. UL 790 Class A rated with UL 997 Wind Resistance Label; ASTM D 7158, Class H; ASTM 3161, Type 1; ASTM D 3018, Type 1; ASTM D 3462; AC438 compliant CSA 123.5-98; Texas Dept of Insurance Approved. Installed over #30 Roofing Underlayment and, at ridges, valleys, and eaves, over Leak Barrier. Provide and install all required accessories. system includes membrane, adhesives, fasteners, prefabricated corners, flashings, and other manufacturer approved products. Support roof system with joist/rafter system or pre-engineered truss system to meet dead and live load requirements as specified by manufacturer, also see structural. Coordinate installation with flashings and other components. Low Slope Metal Roof Install 50 year warranty low-slope metal roof system with concealed fasteners. Install a layer of fire-retardant paper between roof structure and metal. Standing seam above front porch, back patio and roof overhang across back of house. Color TBD Preformed metal coping - Install preformed galvanized sheet steel coping, splice plates and mechanically fastened anchor plates to the top of the parapet wall. Provide mitered corners, expansion joints, and any special accessories for complete installation. Finish selected from standard colors to match metal roofing. All self-locking rivets and other suitable fasteners shall be supplied by coping manufacturer. All joint sealant to be approved by the metal roof system manufacturer Stucco Install metal lath over 2 layers weather resistive barrier. Apply weep screed at base, Stucco should be held min 6" from adjacent horizontal surface. Lath shall be self-furring or applied with furring nails. Minimize lath lapping; secure lath uniformly with open ends secured tightly. Control joints shall be as specified by manufacturer, but minimally, at windows and doors, at lengths over 16', and areas greater than 150 sqft. Install LaHabra FastWall 100 Stucco System (OR EQUAL) including base coat, acrylic primer, and acrylic finish coat as specified by manufacturer. Complete installation with sealants at penetrations, weep screeds, joint and corner beads and other installation accessories as recommended by the manufacturer. Interior Wood - Wood surfaces shall be sanded smooth before finish is applied. Putty areas with a wood based filler where nails or other defects appear in the surface. Prime wood surfaces including faces, edges and ends before installation. After installation, apply at least one coat of wood primer and two coats of finish paint. Surfaces shall be sanded before each finish layer is applied. Finish Grading - Keep exterior finished grade a minimum of 6 1/2” below finished floor elevation (see construction documents for exact locations) by backfilling with appropriate soils. Provide swales with positive outfall and slope grade away from building to allow water to drain away from the building foundation. Do not backfill against foundation until project is completely framed and roof structure is in place. Soil type of fill shall be specified by Structural Engineer. Termite Control - Foundations shall be pre-treated under all slabs and crawlspace areas between vapor barrier and granular sub-base to conform with HUD minimum standards and applicable building codes. Treatments shall not be made when soil is excessively wet or after heavy rains. Contractor shall provide a one-year renewable warranty. At pier and perimeter foundations, install continuous flashing on all sides and top surface to prevent sub-terrain termites from penetrating the wood structure. Exterior Wood Panels Install 30-year warranty exterior grade overlaid MDO, smooth panel siding, min thickness 1/2" With no patching. Install PT 1x4 corner trim, and trim stops. Paneling and trim shall be dry, straight grain, factory primed and sealed at all ends. Install over 7/16" rainscreen and polyethylene vapor. Ensure joints meet on studs, blocking or furring strips with the nail penetrating solid wood at least 1¼ inches. Caulk joints; Paint siding. ABBREVATIONS Flashing and Sheet Metal - Install appropriate flashing at all chimneys, joints of walls, vent pipes and other connection points to prevent the infiltration of water. Flashing shall be assembled of 26 gauge minimum galvanized, corrosion resistant sheet metal. Keep flashing concealed except where exposed on vertical surfaces or counter flashing. Joint Sealants - Use a 50 year warranty silicon based caulk at high expansion/compression areas, such as around chimneys, tile, ceramic, and around enamel and pre-fabricated tubs and showers. Caulk and seal around all window and door frames and between wall sole plates and floors and at exterior siding joints. For exterior windows, door frames, interior trim, woodwork and other paintable surfaces use a clear Latex based caulk. Color shall match paint. Openings - Manufactured doors and windows shall be certified and labeled in compliance with the appropriate infiltration standards listed in the Residential Energy Code. Site-constructed doors and windows, exterior joints, and openings in the building envelope shall be caulked, gasketed, weatherstripped or otherwise sealed, except fire rated doors or windows, and unframed glass doors. See A0.4 for additional requirements and schedules. Contractor shall provide access panels as required by plumbing, mechanical and other trades, and as required by codes, location(s) and type(s) to be approved by the Owner. Gypsum Board - Gypsum board must be held firmly against the framing while fastening to avoid later movement of gypsum board on the shank of the nails or screws. Sheath walls with 1/2” gypsum wallboard, and ceilings with 5/8” gypsum wall board, either vertically with long edges parallel to framing, or horizontally with long edges at right angles to framing members. Square corners. Apply one layer to all wall surfaces. Offset joints between layers at least 10”. Wall and ceiling finish level 5, smooth texture. In garages, around gas water heaters and as required by applicable building codes, install 5/8” Type “X” fire-rated gypsum wallboard; Finish level 2. Around showers, tubs, whirlpools, or as required by applicable building codes, install 1/2” water resistant fiber cement board, Finish level 2 Flooring - Contractor shall properly clean all surfaces to be covered and install appropriate underlayment per manufacturers recommendations. Tiling - Tile shall be appropriate grade and finish in accordance with applicable building codes and owner requirements. Installation should be carried out over appropriate underlayment with a slow setting cement adhesive, well mixed per manufacturer recommendations. Grouting of control joints can be executed either with cement based grout or with resin based organic materials. Tile at bathrooms Wood Flooring - Install a single layer of 15 lb felt vapor barrier between sub-floor decking and hardwood floors. When installing hardwoods over a concrete slab install a layer of 3/4” plywood as underlayment over 6 mil polyethylene. Along walls and permanent objects, install a 1” quarter round molding to conceal expansion area. Wood flooring shall be tongue and groove construction and true square edged for a flat smooth surface. Wood flooring can be fastened with appropriate nails, staples or glue. Check specific manufacturer's recommendations. Exterior Painting - All nail heads shall be set below the surface and finished smooth. If mildew is evident, the mildew must be removed and surface treated to inhibit further mildew growth. Exterior walls shall receive a primer coat and two coats of flat or semi-gloss paint. Pre-prime the edges and ends of lumber and siding prior to construction. When staining, pre-prime with the same product as specified for the final coat. Sand and putty wood surface smooth before finish is applied. Surfaces shall be sanded before each finish layer is applied. Prime wood surfaces including faces, edges and ends before installation. After installation, apply at least one coat of wood primer and two coats of finish paint. Allow 4 color scheme. Interior Painting - All nail heads shall be set below the surface and finished smooth. Joints should be taped and covered with a suitable drywall joint compound. Sand the spackled nail heads and joint compound smooth and dust well before priming. Interior walls shall receive a primer coat and two coats of flat or semi-gloss paint. Surfaces shall be sanded before each finish layer is applied. Allow color scheme ADJ. A.B. A.C.T. A.F.F. ALUM. ANOD. APPROX. BD. BOT. BRG. C.H. CHNL. C.I.P. CLG. C.J. CLR. C.M.U. COL. CPMPR. CONC. CONT. CPT. C.T. DBL. DEMO. DIA. DIM. DN. DR. D.W. DWG. EA. E.J. ELEC. ELEV. EXIST. EXT. F.D. F.E. F.E.C. F.F. FIN. FIX. FLR. FLSH. FND. - - - - - - - - - - - - - - - - - - - - - - - - - - - - - - - - - - - - - - - - - - - - - - ADJACENT ANCHOR BOLT ACOUSTIC CEILING TILE ABOVE FINISHED FLOOR ALUMINUM ANODIZED APPROXIMATE BOARD BOTTOM BEARING CEILING HEIGHT CHANNEL CAST IN PLACE CEILING CONTRACTION JOINT CLEAR CONCRETE MASONRY UNIT COLUMN COMPRESSIBLE CONCRETE CONTINUOUS CARPET CERAMIC TILE DOUBLE DEMOLITION DIAMETER DIMENSION DOWN DOOR DISH WASHER DRAWING EACH EXPANSION JOINT ELECTRICAL ELEVATION EXISTING EXTERIOR FLOOR DRAIN FIRE EXTINGUISHER FIRE EXTINGUISHER CABINET FINISH FLOOR FINISH FIXTURE FLOOR FLASHING FOUNDATION F.V. GA. G.B. GALV. GYP. HOC. HGT. HC. HDWR. HR. H.M. HVAC. INSUL. INT. JAN. JT. LAM. LAV. M.O. MAT'L. MAX. M.C. MK. MECH. MEMBR. MIN. MIRR. MTL. M.T. M.W.I. N.I.C. NO. N.T.S. O.C. O.F.C.I. O..R.D. O.H. OPP. OP'NG. P.C.C. P.D. PNL. PATT. PEN. PERF. PLUMB. - - - - - - - - - - - - - - - - - - - - - - - - - - - - - - - - - - - - - - - - - - - - - - FIELD VERIFY GAUGE GRAB BAR GALVANIZED GYPSUM HOLLOW CORE HEIGHT HANDICAP HARDWARE HOUR HOLLOW METAL AIR CONDITION INSULATION INTERIOR JANITOR JOINT LAMINATED LAVATORY MASONRY OPENING MATERIAL MAXIMUM MEDICINE CABINET MARK MECHANICAL MEMBRANE MINIMUM MIRROR METAL MARBLE THRESHOLD MILLWORK ITEM NOT IN CONTRACT NUMBER NOT TO SCALE ON CENTER OWNER FURNISHED CONTRACTOR INSTALLED OVERFLOW ROOF DRAIN OVER HEAD OPPOSITE OPENING PRE-CAST CONCRETE PAPER DISPENSER PANEL PATTERN PENETRATION PERFORATED PLUMBING P.H. PLT. PLAS. PLYD. P.T. P.T.D. PNT. R. RBR. R.C.P. - - - - - - - - - - - R.D. - REINF. - REQ'D. - REF. - RM. - SCHDL. - S.C. - S.D. - SIM. - SPEC. - SPK. - S.S. - STL. - STRUC. - T&G - TELE. - TLT. - T.B. - T.B.R. - T.H. - T.O.C. - T.O.P. - T.O.S. - TEMP. - THRES. - TK. - T.S. - TYP. - UR. V.C.T. - TILE V.W.C. - - W/ - W.C. - WD. - WOLM. - W.W.M PAPER HOLDER PLATE PLASTIC PLYWOOD PRESSURE TREATED PAPER TOWEL DISPENSER PAINT RADIUS RUBBER REFLECTED CEILING PLAN ROOF DRAIN REINFORCED REQUIRED REFERENCE ROOM SCHEDULE SOLID CORE SOAP DISH SIMILAR SPECIFICATION SPRINKLER STAINLESS STEEL STEEL STRUCTURAL TONGUE AND GROOVE TELEPHONE TOILET TOWEL BAR TO BE REMOVED TOWEL HOOK TOP OF CONCRETE TOP OF PLATE TOP OF STEEL TEMPERED THRESHOLD THICK TRANSITION STRIP TYPICAL URINAL VINYL COMPOSITION VINYL WALL COVERING WITH WATER CLOSET WOOD WOLMANIZED WELDED WIRE MESH . I I I E R U T C E T H C R A E K O O C Y R R E B R E T R A F O T N E S N O C N E T T R W T U O H T W D E R A P E R P N E E B E V A H Y E H T H C H W R O F T C E J O R P D E F C E P S E H T N A H T R E H T O K R O W Y N A H T W N O T C E N N O C N I I I I I I I D E S U R O D E P O C E B L L A H S F O E R E H T T R A P O N I S T C E T H C R A E K O O C Y R R E B R E T R A F O Y T R E P O R P E H T E R A S N O T A C F C E P S D N A S G N W A R D E S E H T I I I I I S T C E T H C R A E K O O C Y R R E B R E T R A © T H G R Y P O C I I E R U T C E T H C R A E K O O C Y R R E B R E T R A R E V O C Architect: Alice Arterberry 2416 Vista Lane Austin, TX 78703 alice@arterberrycooke.com 323.236.5182 0 5/0 1/2 0 2 2 Project Owner: Lisa Tsai and Tim Notzon Project Address: 1616 Northumberland Rd Austin TX 78703 MJS AA drawn by: checked by: scale: first issue: NO SCALE 01-04-2022 plot date: 05-12-2022 A0.0 POOL AND SPA: POOL: SPA: TOTAL: 340 SF 30 SF 370 SF EXTERIOR ROOFED AREA: FRONT PORCH: COVERED REAR PATIO: COVERED BALCONY: 14 SF 578 SF 134 SF SUB-TOTAL: 726 SF GROSS FLOOR AREA: FIRST FLOOR: SECOND FLOOR: (W/O ATTIC) GARAGE: (200 SF EXEMPTION) 2,552 SF 866 SF 329 SF SUB-TOTAL: 3,747 SF TOTAL: 4,473 SF MAXIMUM ALLOWABLE BUILDABLE AREA: 0.40 x AREA = 0.40 x 9374 = 3,750 SF BUILDABLE AREA: BUILDING AREA / SITE AREA = 3,747 SF / 9374 SF = .399 PROPOSED BUILDABLE AREA = 39.9% 1 LOT 9 LOT 8 LOT 7 HEDGES HEDGES U E U E S60°11'23"E 75.00' 5'-0" PUE 10'-0" REAR YARD SETBACK 10'-0" ELECTRICAL CLEARANCE SETBACK L P O T " 8 5 ' 8 - 9 1 R 2 C.R.Z. 6'-0" 1 / 2 R C 1 . 3 R '- . 0 " Z . " 2 1 ' 8 - 9 1 ' 0 0 . 5 2 1 W " 8 3 6 4 ° 9 2 S ' E U 3 9 5 5'-33 E U 4" A/C #1 E U E U A/C #2 E U E U E U E U E U E U E U E U E U K C A B E T U E S D R A Y E U " 0 E - U ' 5 2 9 5 6704 POOL SPA LEDGE F.F.E. = 94.5 1 / 4 C R 6 ' - 6 " . R . Z . 1 9 5 R E T N A L P 0 9 5 " 8 3 1 1 - 9 5 ' K C A B T E S D R A Y " 0 - 5 ' 11'-31 2" 10'-0" TO PL ' 6 9 . 4 2 1 E " 9 3 6 4 ° 9 2 N ' PROPOSED 2-STORY SINGLE-FAMILY RESIDENCE ELECTRIC METER LOCATION U E 4 9 5 EM EXTERIOR VISITIBALE ROUTE POINT OF ORIGIN GARAGE DOOR #8 (3'-0" X 8'-0") 5'-0" TO PL PROPOSED 2-STORY SINGLE-FAMILY RESIDENCE FIN. FLR. ELEV. = 95.0 STUCCO WALL 5'-0" 11'-31 2" STRIP DRIVEWAY A F.F.E. = 94.75 25'-0" FRONT YARD SETBACK PROPOSED SPOILS AREA LOT 28 PROTECTIVE FENCING SEE TREE NOTES LOT 26 1 / 4 R C . R 8'- 9 " . Z . LOT 27 2'-0" 2'-0" 2'-0" 3'-0" 3'-0" 3'-0" 3'-0" " 2 1 ' 8 - 9 2 L P O T " 0 - 5 2 ' 5 9 5 R 1 8 ' - 0 " 4 9 5 PROPOSED STAGING AREA PT GAS GAS GAS GAS GAS GAS N60°09'45"W 75.00' SITE ACCESS 18'-0" GAS S S R 5'-0" E P O L S 28'-0" brick 1 P M U D " 0 - 0 1 ' R 5'-0" S S NORTHUMBERLAND RD (50' R.O.W.) W W W W W W W W 6701 G A S R 5 ' - 7 1 2 " " 3 1'- 1 R R22'-6" 1/2 C.R.Z. R17'-6" C . R . Z . R 3 5 ' - 0 " L L A W K C R B I " 0 - 4 2 ' B 3 9 5 2 9 5 0 20'-0" 40'-0" N STAGING AREA ROOF OUTLINE SETBACK / EASEMENT PROPERTY LINE FENCING OVERHEAD LINE DUMP DUMPSTER / SPOILS WASHOUT(S) PT PORTABLE TOILET SS SS SS WASTE WATER GAS GAS GAS GAS LINE WW WW WW WATER LINE UE UE UE UNDERGROUND ELEC OVERHEAD POWER PROTECTIVE MULCHING There is no cut or fill within the 1/4 critical root zones. No A minimum of 50 percent of the critical root zone must be Prior to construction, 5' high chain-link mesh, protective fencing There is no cut or fill 4" or greater within the ½ critical root zone TREE ORDINANCE Notes: * preserved at natural grade, with natural ground cover. * impacts are permitted within the 1/4 critical root zone. * is required around all trees within the LOC. When the protective fencing cannot incorporate the entire ½ critical root zone, an 8” layer of mulch within the entire available root zone area is required for all trees which have any disturbance indicated within any portion of the critical root zone. Additionally, min 2x4 or greater size planks (6' tall minimum) to be strapped securely around a protected tree's trunk and root flare when protective fencing doesn't incorporate the entire 1/2 CRZ for any reason at any time in the project. * of protected trees. Only piers are allowed within ½ critical root zone and piers must be air-spaded. * accomplished with hand tools. * within an annual growing season, and that the percentage and distribution of foliage to be removed shall be adjusted according to the plant's species, age, health, and site. If any pruning is required, a Certified Arborist must perform the pruning and pruning may only happen once during the project duration. This should occur prior to construction to avoid damaging the trees during construction. A “paid in full” receipt from a Certified Arborist, for the work, will be required from the Final Tree Inspector. If 25% or more of the canopy is desired to be removed, the Certified Arborist must provide a written report to us to seek a permit, BEFORE performing this work.) Not more than 25 percent of the crown should be removed Demolition within the 1/2 critical root zone must be (NO PRUNING IS ANTICIPATED.) Avoid the 1/2 Critical Root Zones of protected trees with any Portable Toilet, Concrete Washout and Paint Washout may not Access routes, Material Staging, Dumpster and Spoils may not * be placed within a protected tree's 1/2 CRZ * be placed within a protected tree's FULL CRZ * newly proposed utility work. If trenching within the ½ CRZ of protected trees cannot be avoided, the trenches will be air spaced by a Certified Arborist for the top 30” to avoid cutting roots 1.5”+ in diameter and the paid receipt for the work will be required by the Final Tree Inspector. * of protected trees, provide 3/4" plywood over 2x4 lumber over 12″ layer of mulch to bridge over the roots and prevent soil/root compaction. After construction is completed, spread mulch around site to leave a max layer of 3″ within root zones. If heavy equipment will be rolling over any area of the full CRZ PROJECT SPECIFIC NOTES: * 6704 C.R.Z. IMPACT AREA NEW CONSTRUCTION 543 SQFT FULL C.R.Z. 2123 SQFT IMPACTED AREA 35.5% B C.R.Z. IMPACT AREA NEW CONSTRUCTION 126 SQFT FULL C.R.Z. 3848 SQFT IMPACTED AREA 3.27% CRITICAL ROOT ZONE IMPACT AREA not to scale " 0 - 1 ' " 6 - 9 ' " 0 - 0 4 ' " 6 - 2 2 ' " 0 - 7 ' 4'-0" 15'-0" 15'-0" 10'-0" I E N L Y T R E P O R P SITE PLAN Scale 1" = 10'-0" (TABLOID:Scale 1" = 20'-0") 1 POWER POLE CLEARANCE DIAGRAM 2 Scale NOT TO SCALE Revisions By #1 05-01-2022 MJS Architect: Alice Arterberry 2416 Vista Lane Austin, TX 78703 alice@arterberrycooke.com 323.236.5182 0 5/0 1/2 0 2 2 Project Owner: Lisa Tsai and Tim Notzon Project Address: 1616 Northumberland Rd Austin TX 78703 I E R U T C E T H C R A E K O O C Y R R E B R E T R A N A L P E T I S MJS AA drawn by: checked by: scale: first issue: AS SHOWN 01-04-2022 plot date: 05-12-2022 A1.0 . I I I E R U T C E T H C R A E K O O C Y R R E B R E T R A F O T N E S N O C N E T T R W T U O H T W D E R A P E R P N E E B E V A H Y E H T H C H W R O F T C E J O R P D E F C E P S E H T N A H T R E H T O K R O W Y N A H T W N O T C E N N O C N I I I I I I I D E S U R O D E P O C E B L L A H S F O E R E H T T R A P O N I S T C E T H C R A E K O O C Y R R E B R E T R A F O Y T R E P O R P E H T E R A S N O T A C F C E P S D N A S G N W A R D E S E H T I I I I I S T C E T H C R A E K O O C Y R R E B R E T R A © T H G R Y P O C I 4 A4.3 6'-0" 3" 3" 3" " 0 1 1 3" .75:12 L A T E M " 0 1 3" " 0 - 1 ' 2 1 : 4 1 SHINGLES SHINGLES 2 1 : 4 1 2 1 : 3 METAL METAL 2 1 : 5 7 . 3" " 0 1 10" " 3 " 0 1 3" " 3 METAL SHINGLES SHINGLES 2 1 : 3 2 1 : 4 1 2 1 : 4 1 2 1 : 3 " 3 " 0 - 1 ' 1'-0" 10" 3" " 3 1 " 3 12:12 S E L G N H S I 3:12 L A T E M 12:12 S E L G N H S I METAL 10" " 3 CRICKET " 3 3" 10" " 3 " 2 1 2 - 6 ' 2 A4.1 ROOF LEGEND NEW ASPHALT SHINGLE ROOF NEW LOW SLOPE STANDING SEAM ROOF WALL OUTLINE ATTIC VENTILATION THE NET FREE VENTILATING AREA SHALL NOT BE LESS THAN 1/150 OF THE AREA OF THE SPACE VENTILATED, EXCEPT THAT REDUCTION OF TOTAL AREA TO 1 300 IS PERMITTED PROVIDED AT LEAST 40% AND NOT MORE THAN 50% OF THE REQUIRED VENTILATING AREA IS PROVIDED BY VENTILATORS LOCATED IN THE UPPER PORTION OF THE SPACE (NO MORE THAN 3 FEET BELOW THE RIDGE) WITH THE BALANCE OF THE REQUIRED VENTILATION PROVIDED BY EAVE OR CORNICE VENTS. [2013 CRC R806.2]. OPENINGS FOR VENTILATION SHALL BE COVERED WITH CORROSION-RESISTANT METAL MESH WITH MESH OPENING A MINIMUM OF 1/16" AND NOT EXCEEDING 1/4" INCH (1/8" IN HIGH FIRE HAZARD ZONES). UPPER ROOF AREA = 1195 SQ.FT. REQUIRED NET FREE VENTILATION 573.6 SQ. IN. (3.98 SQ.FT. ), BALANCE BETWEEN RIDGE VENTS AND SOFFITS WITH NO LESS THAN 229 SQ. IN. AND NO MORE THAN 286 SQ.IN. AT RIDGE (NOTE: GABLE VENTS ARE DECORATIVE. NOT OPEN TO ATTIC SPACE. EXEMPT ATTIC ROOF AREA = 615 SQ. FT. REQUIRED NET FREE VENTILATION 295.2 SQ. IN. (2.05 SQ.FT.) BALANCE BETWEEN RIDGE VENTS AND SOFFITS WITH NO LESS THAN 118 SQ.IN., AND NO MORE THAN 147 SQ.IN. AT RIDGE. LOWER ROOF (MASTER) AREA = 999 SQ.FT. REQUIRED NET FREE VENTILATION 479.5 SQ.IN. (3.3 SQ.F.T) BALANCE BETWEEN RIDGE VENTS AND SOFFITS WITH NO LESS THAN 191 SQ.IN. AND NO MORE THAN 239 SQ.IN. AT RIDGE. LOW SLOPE METAL ROOF AREA = 958 SQ.F.T - unvented .75:12 L A T E M 12:12 S E L G N H S I 12:12 S E L G N H S I 1.5:12 L A T E M " 3 " 3 3 A4.2 1'-0" 10" 1 A4.0 IRC: MIN. 3'-0" @ ROOF LINE, AND 2''-0" ABOVE ANY ROOF WITHIN 10'-0" CRICKET ROOF PLAN Scale 1/4" = 1'-0" (TABLOID:Scale 1/8" = 1'-0") " 3 10" 3 MJS AA drawn by: checked by: scale: first issue: AS SHOWN 01-04-2022 plot date: 05-12-2022 A2.2 Revisions By #1 05-01-2022 MJS Architect: Alice Arterberry 2416 Vista Lane Austin, TX 78703 alice@arterberrycooke.com 323.236.5182 0 5/0 1/2 0 2 2 Project Owner: Lisa Tsai and Tim Notzon Project Address: 1616 Northumberland Rd Austin TX 78703 I E R U T C E T H C R A E K O O C Y R R E B R E T R A N A L P F O O R . I I I E R U T C E T H C R A E K O O C Y R R E B R E T R A F O T N E S N O C N E T T R W T U O H T W D E R A P E R P N E E B E V A H Y E H T H C H W R O F T C E J O R P D E F C E P S E H T N A H T R E H T O K R O W Y N A H T W N O T C E N N O C N I I I I I I I D E S U R O D E P O C E B L L A H S F O E R E H T T R A P O N I S T C E T H C R A E K O O C Y R R E B R E T R A F O Y T R E P O R P E H T E R A S N O T A C F C E P S D N A S G N W A R D E S E H T I I I I I S T C E T H C R A E K O O C Y R R E B R E T R A © T H G R Y P O C I 2 A4.1 19 2 ASPHALT SHINGLE ROOF CHIMNEY T.O.P. FASCIA & TRIM MASONRY SILL F.F. " 8 1 7 - 1 ' T.O.P. MASONRY ACCENT COUSES I T H G E H G N D L U B I I " 2 1 ' 9 - 0 3 BRICK VENEER F.F. (95.0') " 0 - 0 1 ' " 0 - 0 1 ' " 4 3 7 - 1 ' 16 1 AVG. ADJ. GRADE ELEV. FLASHING LOW SLOPE METAL ROOF STRUC. ROOF SUPPORTS 1 9 NORTH ELEVATION Scale 1/4" = 1'-0" (TABLOID:Scale 1/8" = 1'-0") 1 17 18 21 4 A4.3 12 12 14 14 ASPHALT SHINGLE ROOF LOW SLOPE METAL ROOF FACIA & TRIM SHIP-LAP HORIZ. SIDING T.O.P. SIDING TRIM FLASHING " 0 - 7 ' " 8 1 7 - 1 ' " 0 - 0 1 ' F.F. T.O.P. FACIA & TRIM 1 BRICK VENEER F.F. (95.0') Revisions By #1 05-01-2022 MJS Architect: Alice Arterberry 2416 Vista Lane Austin, TX 78703 alice@arterberrycooke.com 323.236.5182 0 5/0 1/2 0 2 2 Project Owner: Lisa Tsai and Tim Notzon Project Address: 1616 Northumberland Rd Austin TX 78703 I E R U T C E T H C R A E K O O C Y R R E B R E T R A I S N O T A V E L E R O R E T X E I MJS AA drawn by: checked by: scale: first issue: AS SHOWN 01-04-2022 plot date: 05-12-2022 A3.0 . I I I E R U T C E T H C R A E K O O C Y R R E B R E T R A F O T N E S N O C N E T T R W T U O H T W D E R A P E R P N E E B E V A H Y E H T H C H W R O F T C E J O R P D E F C E P S E H T N A H T R E H T O K R O W Y N A H T W N O T C E N N O C N I I I I I I I D E S U R O D E P O C E B L L A H S F O E R E H T T R A P O N I S T C E T H C R A E K O O C Y R R E B R E T R A F O Y T R E P O R P E H T E R A S N O T A C F C E P S D N A S G N W A R D E S E H T I I I I I S T C E T H C R A E K O O C Y R R E B R E T R A © T H G R Y P O C I LOUVERED METAL ATTIC VENT DECORATIVE ONLY 12 12 ASPHALT SHINGLE ROOF 1 A4.0 CHIMNEY 12 12 12 3 20 12 12 22 12 12 23 ASPHALT SHINGLE ROOF LOW SLOPE METAL ROOF SHIP-LAP HORIZ. SIDING 3 A4.2 3 4 5 6 LOW SLOPE METAL ROOF WEST ELEVATION Scale 1/4" = 1'-0" (TABLOID:Scale 1/8" = 1'-0") 10 2 MASONRY SILL FLASHING 1 ASPHALT SHINGLE ROOF FASCIA & TRIM 12 .75 STRUC. ROOF SUPPORTS T.O.P. F.F. T.O.P. SHIP-LAP HORIZ. SIDING SIDING TRIM F.F. (95.0') " 0 - 7 ' " 8 1 7 - 1 ' " 0 - 0 1 ' LOW SLOPE METAL ROOF T.O.P. FASCIA & TRIM T.O.P. SHIP-LAP HORIZ. SIDING FLASHING " 0 - 7 ' T.O.P. F.F. T.O.P. MASONRY SILL MASONRY ACCENT COUSES BRICK VENEER F.F. (95.0') AVG. ADJ. GRADE ELEV. I T H G E H G N D L U B I I " 2 1 ' 9 - 0 3 " 0 - 0 1 ' " 8 1 7 - 1 ' " 0 - 0 1 ' " 4 3 7 - 1 ' Revisions By #1 05-01-2022 MJS Architect: Alice Arterberry 2416 Vista Lane Austin, TX 78703 alice@arterberrycooke.com 323.236.5182 0 5/0 1/2 0 2 2 Project Owner: Lisa Tsai and Tim Notzon Project Address: 1616 Northumberland Rd Austin TX 78703 I E R U T C E T H C R A E K O O C Y R R E B R E T R A I S N O T A V E L E R O R E T X E I MJS AA drawn by: checked by: scale: first issue: AS SHOWN 01-04-2022 plot date: 05-12-2022 A3.1 . I I I E R U T C E T H C R A E K O O C Y R R E B R E T R A F O T N E S N O C N E T T R W T U O H T W D E R A P E R P N E E B E V A H Y E H T H C H W R O F T C E J O R P D E F C E P S E H T N A H T R E H T O K R O W Y N A H T W N O T C E N N O C N I I I I I I I D E S U R O D E P O C E B L L A H S F O E R E H T T R A P O N I S T C E T H C R A E K O O C Y R R E B R E T R A F O Y T R E P O R P E H T E R A S N O T A C F C E P S D N A S G N W A R D E S E H T I I I I I S T C E T H C R A E K O O C Y R R E B R E T R A © T H G R Y P O C I 2 A4.1 ASPHALT SHINGLE ROOF 4 A4.3 12 14 LOW SLOPE METAL ROOF 12 14 3 A5.1 12 3 25 12 .75 1 SHIP-LAP HORIZ. SIDING 7 8 12 ASPHALT SHINGLE ROOF T.O.P. " 0 - 7 ' " 8 1 7 - 1 ' " 0 - 0 1 ' FASCIA & TRIM F.F. T.O.P. SIDING TRIM F.F. (95.0') STRUC. ROOF SUPPORTS MASONRY SILL BRICK VENEER FLASHING 6 SOUTH ELEVATION Scale 1/4" = 1'-0" (TABLOID:Scale 1/8" = 1'-0") 3 CHIMNEY SHIP-LAP HORIZ. SIDING WOOD COL. REF. STRUC. DWGS. METAL GUARDRAIL UP 36" LOW SLOPE METAL ROOF T.O.P. I T H G E H G N D L U B I I " 2 1 ' 9 - 0 3 F.F. " 8 1 7 - 1 ' T.O.P. STEEL COL. REF. STRUC. DWGS. F.F. (95.0') AVG. ADJ. GRADE ELEV. " 0 - 0 1 ' " 0 - 0 1 ' " 4 3 7 - 1 ' Revisions By #1 05-01-2022 MJS Architect: Alice Arterberry 2416 Vista Lane Austin, TX 78703 alice@arterberrycooke.com 323.236.5182 0 5/0 1/2 0 2 2 Project Owner: Lisa Tsai and Tim Notzon Project Address: 1616 Northumberland Rd Austin TX 78703 I E R U T C E T H C R A E K O O C Y R R E B R E T R A I S N O T A V E L E R O R E T X E I MJS AA drawn by: checked by: scale: first issue: AS SHOWN 01-04-2022 plot date: 05-12-2022 A3.2 . I I I E R U T C E T H C R A E K O O C Y R R E B R E T R A F O T N E S N O C N E T T R W T U O H T W D E R A P E R P N E E B E V A H Y E H T H C H W R O F T C E J O R P D E F C E P S E H T N A H T R E H T O K R O W Y N A H T W N O T C E N N O C N I I I I I I I D E S U R O D E P O C E B L L A H S F O E R E H T T R A P O N I S T C E T H C R A E K O O C Y R R E B R E T R A F O Y T R E P O R P E H T E R A S N O T A C F C E P S D N A S G N W A R D E S E H T I I I I I S T C E T H C R A E K O O C Y R R E B R E T R A © T H G R Y P O C I 1 A4.0 CHIMNEY LOUVERED METAL ATTIC VENT DECORATIVE ONLY 12 12 ASPHALT SHINGLE ROOF 12 12 3 A4.2 ASPHALT SHINGLE ROOF LOW SLOPE METAL ROOF SHIP-LAP HORIZ. SIDING 24 25 26 15 26 20 " 0 - 7 ' STRUC. ROOF SUPPORTS T.O.P. F.F. " 8 1 7 - 1 ' T.O.P. " 0 - 0 1 ' FLASHING 12 .75 1 LOW SLOPE METAL ROOF 9 SIDING TRIM SHIP-LAP HORIZ. SIDING F.F. (95.0') EAST ELEVATION Scale 1/4" = 1'-0" (TABLOID:Scale 1/8" = 1'-0") 4 10 11 13 14 12 .75 STEEL COL. REF. STRUC. DWGS. 12 METAL GUARDRAIL UP 36" FASCIA & TRIM I T H G E H G N D L U B I I " 2 1 ' 9 - 0 3 " 0 - 0 1 ' " 8 1 7 - 1 ' " 0 - 0 1 ' " 4 3 7 - 1 ' MASONRY SILL 12 1.5 MASONRY ACCENT COUSES BRICK VENEER LOW SLOPE METAL ROOF AVG. ADJ. GRADE ELEV. Revisions By #1 05-01-2022 MJS Architect: Alice Arterberry 2416 Vista Lane Austin, TX 78703 alice@arterberrycooke.com 323.236.5182 0 5/0 1/2 0 2 2 Project Owner: Lisa Tsai and Tim Notzon Project Address: 1616 Northumberland Rd Austin TX 78703 I E R U T C E T H C R A E K O O C Y R R E B R E T R A I S N O T A V E L E R O R E T X E I MJS AA drawn by: checked by: scale: first issue: AS SHOWN 01-04-2022 plot date: 05-12-2022 A3.3 . I I I E R U T C E T H C R A E K O O C Y R R E B R E T R A F O T N E S N O C N E T T R W T U O H T W D E R A P E R P N E E B E V A H Y E H T H C H W R O F T C E J O R P D E F C E P S E H T N A H T R E H T O K R O W Y N A H T W N O T C E N N O C N I I I I I I I D E S U R O D E P O C E B L L A H S F O E R E H T T R A P O N I S T C E T H C R A E K O O C Y R R E B R E T R A F O Y T R E P O R P E H T E R A S N O T A C F C E P S D N A S G N W A R D E S E H T I I I I I S T C E T H C R A E K O O C Y R R E B R E T R A © T H G R Y P O C I