B.3.2 - 6301 Bluff Springs Rd - Sneed - applicant email — original pdf
Backup
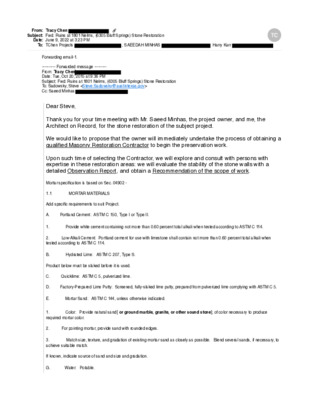
Subject: Fwd: Ruins at 1801 Nelms, (6305 Bluff Springs) Stone Restoration , SAEEDAH MINHAS Harry Karr From: Tracy Chen Date: June 9, 2022 at 3:23 PM To: TChen Projects Forwarding email-1. ---------- Forwarded message --------- From: Tracy Chen Date: Tue, Oct 20, 2015 at 9:36 PM Subject: Fwd: Ruins at 1801 Nelms, (6305 Bluff Springs) Stone Restoration To: Sadowsky, Steve <Steve.Sadowsky@austintexas.gov> Cc: Saeed Minhas Dear Steve, Thank you for your time meeting with Mr. Saeed Minhas, the project owner, and me, the Architect on Record, for the stone restoration of the subject project. We would like to propose that the owner will immediately undertake the process of obtaining a qualified Masonry Restoration Contractor to begin the preservation work. Upon such time of selecting the Contractor, we will explore and consult with persons with expertise in these restoration areas: we will evaluate the stability of the stone walls with a detailed Observation Report, and obtain a Recommendation of the scope of work. Mortar specification is based on Sec. 04902 - 1.1 MORTAR MATERIALS Add specific requirements to suit Project. A. Portland Cement: ASTM C 150, Type I or Type II. B. Hydrated Lime: ASTM C 207, Type S. Product below must be slaked before it is used. C. Quicklime: ASTM C 5, pulverized lime. 1. Provide white cement containing not more than 0.60 percent total alkali when tested according to ASTM C 114. 2. Low-Alkali Cement: Portland cement for use with limestone shall contain not more than 0.60 percent total alkali when tested according to ASTM C 114. D. Factory-Prepared Lime Putty: Screened, fully-slaked lime putty, prepared from pulverized lime complying with ASTM C 5. E. Mortar Sand: ASTM C 144, unless otherwise indicated. 1. Color: Provide natural sand[ or ground marble, granite, or other sound stone]; of color necessary to produce required mortar color. 2. For pointing mortar, provide sand with rounded edges. 3. Match size, texture, and gradation of existing mortar sand as closely as possible. Blend several sands, if necessary, to achieve suitable match. If known, indicate source of sand and size and gradation. G. Water: Potable. The main effort of restoration will be concentrated in the stabilization of the "Ruins", by ways of "Tuck Pointing" with specified Tuck-pointing Mortar (referencing to the Video: http://quikrete.com/AtHome/Video-Tuckpointing-Mortar-Joints.asp? gclid=CO36tfK30sgCFQmJaQod3F8ACw ), and apply/inject epoxy where deem required. Structural Bracing is not considered at this point. Please note the Limit of Restoration will be as shown on the attached Ruin Site, and the Structure -35'-0" x 58'-7". After such restoration work is completed, two rings of steel fencing, surrounding the "Ruins" will be erected to prevent intrusions. We thank you for your time and consideration. Please let us know if any other measures you would like to explore. "A Cheerful heart is good medicine, crushed spirit dries up bones." Sincerely, Tracy T. Chen, NCARB Principal Tchen Architects 11908 Anderson Mill Road, #325 Austin, Texas 78726 http://www.tchenarch.com -- Tracy T. Chen, NCARB Principal Tchen Architect 1303 Elm Forest Drive Cedar Park, Texas 78613 10.20.15.RUINS SITE.pdf Job Description: to pray, to prepare, to present. "A Cheerful heart is good medicine, crushed spirit dries up bones." "Thrusting to make Today better than Yesterday." Be of good cheer, for He has overcome the world. The information contained in this transmission is privileged and confidential information intended for the use of the individual or entity named above. If the reader of this message is not the intended recipient, you are hereby notified that any dissemination, distribution or copying of this communication is strictly prohibited. If you have received this transmission in error, do not read it. Please immediately reply to the sender that you have received this communication in error and delete it. Any unauthorized use of this email, including copying and pasting, reproduction, or forwarding on to an unauthorized 3rd party shall be punishable by the law in the state in which the crime occurred. Copyright 2000 AIA MASTERSPEC 8/00 SECTION 04902 - STONE RESTORATION AND CLEANING PART 1 - GENERAL 1.1 RELATED DOCUMENTS A. Drawings and general provisions of the Contract, including General and Supplementary Conditions and Division 1 Specification Sections, apply to this Section. 1.2 SUMMARY A. This Section includes the following: Repairing stonework, including replacing damaged units. Repointing mortar joints. Removing plant growth. Cleaning exposed stone surfaces. Stone consolidation treatment. B. Related Sections include the following: Division 4 Section "Dimension Stone Cladding" for new stone cladding. Division 4 Section "Stone Veneer Assemblies" for new stone veneer. Division 4 Section "Clay Masonry Restoration and Cleaning." Division 7 Section "Water Repellents" for water repellents applied to cleaned and restored stonework. Division 7 Section "Joint Sealants" for sealing joints in restored stone construction. Division 9 Section "Interior Stone Facing" for new interior stone facing. C. Allowances: Quantity allowances for stone restoration and cleaning are specified in Division 1 Section "Allowances." Perform stone restoration and cleaning work included in quantity allowances only as authorized. Authorized work includes [work required by specifications and] [only] work authorized in writing by Architect. Notify Architect [weekly] <Insert time interval> of extent of work performed that is attributable to quantity allowances. Perform work that exceeds quantity allowances only as authorized by Change Orders. D. Unit Prices: Unit prices for stone restoration and cleaning are specified in Division 1 Section "Unit Prices." Unit prices apply to authorized work covered by quantity allowances. Unit prices apply to additions to and deletions from Work as authorized by Change Orders. 1. 2. 3. 4. 5. 1. 2. 3. 4. 5. 6. 1. 2. 3. 1. 2. STONE RESTORATION AND CLEANING 04902 - 1 Copyright 2000 AIA MASTERSPEC 8/00 1.3 DEFINITIONS A. Low-Pressure Spray: 100 to 400 psi (690 to 2750 kPa); 4 to 6 gpm (0.25 to 0.4 L/s). B. Medium-Pressure Spray: 400 to 800 psi (2750 to 5500 kPa); 4 to 6 gpm (0.25 to 0.4 L/s). C. High-Pressure Spray: 800 to 1200 psi (5500 to 8250 kPa); 4 to 6 gpm (0.25 to 0.4 L/s). 1.4 SUBMITTALS A. Product Data: For each type of product indicated. Include recommendations for application and use. Include test data substantiating that products comply with requirements. B. Shop Drawings: For the following: Replacement stone units. Partial replacement stone units (Dutchmen). Replacement and repair anchors, including drilled-in pins. Include details of anchors within individual stone units, with locations of anchors and dimensions of holes and recesses in stone required for anchors, including direction and angle of holes for pins. C. Samples for Verification: Before erecting mockup, submit samples of the following: Each type of replacement stone. Provide in sets of at least [2] [3] <Insert number> 12- by-12-inch (300-by-300-mm) Samples for each type. Each type of sand used for pointing mortar. a. b. For blended sands, provide Samples of each component and blend. Identify sources, both supplier and quarry, of each type of sand. Each type of pointing mortar in form of sample mortar strips, 6 inches (150 mm) long by 1/2 inch (13 mm) wide, set in aluminum or plastic channels. a. Include with each sample a list of ingredients with proportions of each. Identify sources, both supplier and quarry, of each type of sand and brand names of cementitious materials and pigments if any. Each type of masonry patching compound in form of briquettes, at least 3 inches (75 mm) long by 1-1/2 inches (38 mm) wide. Document each sample with manufacturer and stock number or other information necessary to order additional material. Each type of adhesive. D. Qualification Data: For [restoration specialists] [including field supervisors] [chemical cleaner manufacturer] [and] [consolidant manufacturer]. E. Restoration Program: For each phase of restoration process, provide detailed description of materials, methods, equipment, and sequence of operations to be used for each phase of restoration work including protection of surrounding materials on building and Project site. 1. Include methods for keeping pointing mortar damp during curing period. 1. 2. 3. 1. 2. 3. 4. 5. STONE RESTORATION AND CLEANING 04902 - 2 Copyright 2000 AIA MASTERSPEC 8/00 2. If materials and methods other than those indicated are proposed for any phase of restoration work, provide a written description, including evidence of successful use on comparable projects, and a testing program to demonstrate their effectiveness for this Project. F. Cleaning Program: Describe cleaning process in detail, including materials, methods, and equipment to be used and protection of surrounding materials on building and Project site, and control of runoff during operations. 1. If materials and methods other than those indicated are proposed for cleaning work, provide a written description, including evidence of successful use on comparable projects, and a testing program to demonstrate their effectiveness for this Project. 1.5 QUALITY ASSURANCE A. Restoration Specialist Qualifications: Engage an experienced[, preapproved] masonry restoration and cleaning firm to perform work of this Section. Firm shall have completed work similar in material, design, and extent to that indicated for this Project with a record of successful in-service performance. 1. 2. 3. At Contractor's option, work may be divided between two specialist firms: one for cleaning work and one for repair work. Field Supervision: Restoration specialist firms shall maintain experienced full-time supervisors on Project site during times that stone restoration and cleaning are in progress. Supervisors shall not be changed during Project except for causes beyond control of restoration specialist firm. Restoration Worker Qualifications: Persons who are experienced[ and specialize] in restoration work of types they will be performing.[ When stone units are being patched, assign at least one worker among those performing patching work who is trained and certified by manufacturer of patching compound to apply its products.] Chemical Cleaner Manufacturer Qualifications: A firm regularly engaged in producing masonry cleaners that have been used for similar applications with successful results, and with factory-trained representatives who are available for consultation and Project-site inspection and assistance at no additional cost. Consolidant Manufacturer Qualifications: A firm regularly engaged in producing stone consolidants that have been used for similar applications with successful results, and with factory-trained representatives who are available for consultation and Project-site inspection and assistance at no additional cost. Source Limitations: Obtain each type of material for stone restoration (stone, cement, sand, etc.) from one source with resources to provide materials of consistent quality in appearance and physical properties. Preconstruction Testing Service: [Owner will engage] [Engage] a qualified independent testing agency to test the following. Provide test specimens and assemblies as indicated. B. C. D. E. STONE RESTORATION AND CLEANING 04902 - 3 Copyright 2000 AIA MASTERSPEC 8/00 Replacement Stone: For each proposed type of replacement stone, according to ASTM C 97 for absorption and bulk specific gravity, ASTM C 99 for modulus of rupture, and ASTM C 170 for compressive strength. Existing Stone: For each type of existing stone indicated for replacement, according to ASTM C 97 for absorption and bulk specific gravity, ASTM C 99 for modulus of rupture, and ASTM C 170 for compressive strength. Carefully remove existing stone from locations designated by Architect. F. Mockups: Prepare mockups of restoration and cleaning as follows to demonstrate aesthetic effects and qualities of materials and execution. Prepare mockups on existing walls under same weather conditions to be expected during remainder of the Work. Repair an area [approximately 36 inches (900 mm) high by 48 inches (1200 mm) wide] [as indicated] for each type of stone material indicated to be rebuilt or replaced. Patch three small areas [at least 1 inch (25 mm) in diameter] [as directed] for each type of stone material indicated to be patched. Clean an area [approximately 25 sq. ft. (2.3 sq. m) in area] [as indicated] for each type of stone and surface condition. a. b. Test cleaners and methods on samples of adjacent materials for possible adverse reactions unless cleaners and methods are known to have deleterious effect. Allow a waiting period of not less than seven days after completion of sample cleaning to permit a study of sample panels for negative reactions. Rake out joints in two separate areas [approximately 36 inches (900 mm) high by 72 inches (1800 mm) wide] [as indicated] for each type of repointing required and repoint one of two areas. Apply stone consolidation treatment to an area [approximately 4 sq. ft. (0.4 sq. m) in area] [as indicated]. 1. 2. 1. 2. 3. 4. 5. 1.6 DELIVERY, STORAGE, AND HANDLING A. Deliver stone units to Project site strapped together in suitable packs or pallets or in heavy-duty crates. B. Deliver other materials to Project site in manufacturer's original and unopened containers, labeled with manufacturer's name and type of products. C. D. E. F. Store cementitious materials on elevated platforms, under cover, and in a dry location. Do not use cementitious materials that have become damp. Store hydrated lime in manufacturer's original and unopened containers. Discard lime if containers have been damaged or have been opened for more than two days. Store lime putty covered with water in sealed containers. Store sand where grading and other required characteristics can be maintained and contamination avoided. STONE RESTORATION AND CLEANING 04902 - 4 Copyright 2000 AIA MASTERSPEC 8/00 1.7 PROJECT CONDITIONS A. B. D. E. F. Repoint mortar joints and repair stone only when air temperature is between and 40 and 90 deg F (4 and 32 deg C) and is predicted to remain so for at least 7 days after completion of work. Cold-Weather Requirements: Comply with the following procedures for stone repair and mortar-joint pointing: 1. When air temperature is below 40 deg F (4 deg C), heat mortar ingredients, repair materials, and existing stone to produce temperatures between 40 and 120 deg F (4 and 49 deg C). 2. When mean daily air temperature is below 40 deg F (4 deg C), provide enclosure and heat to maintain temperatures above 32 deg F (0 deg C) within the enclosure for 7 days after repair and pointing. C. Hot-Weather Requirements: Protect masonry repair and mortar-joint pointing when temperature and humidity conditions produce excessive evaporation of water from mortar and patching materials. Provide artificial shade and wind breaks and use cooled materials as required. Do not apply mortar to substrates with temperatures of 90 deg F (32 deg C) and above. Patch stone only when air and surface temperatures are between and 55 and 100 deg F (13 and 38 deg C) and are predicted to remain above 55 deg F (13 deg C) for at least 7 days after completion of work. On days when air temperature is predicted to go above 90 deg F (32 deg C), schedule patching work to coincide with time that surface being patched will be in shade or during cooler morning hours. Clean stone surfaces only when air temperature is 40 deg F (4 deg C) and above and is predicted to remain so for at least 7 days after completion of cleaning. Apply stone consolidation treatment only when surface and air temperatures are between 50 and 90 deg F (10 and 32 deg C) and rain is not expected within 24 hours. 1.8 SEQUENCING AND SCHEDULING A. Order replacement materials at earliest possible date, to avoid delaying completion of the Work. B. Order sand for repointing mortar immediately after approval of [Samples] [mockups]. Take delivery of and store at Project site a sufficient quantity of sand to complete Project. C. Perform stone restoration work in the following sequence: 1. 2. 3. 4. 5. 6. Remove plant growth. Repair existing stonework, including replacing existing stone with new stone materials. Rake out joints that are to be repointed. Point mortar joints. Inspect for open mortar joints and repair before cleaning to prevent intrusion of water and other cleaning materials into the wall. Remove paint. STONE RESTORATION AND CLEANING 04902 - 5 Copyright 2000 AIA MASTERSPEC 8/00 7. 8. 9. Clean stone surfaces. Rake out joints that are to be repointed. Point mortar joints. D. As scaffolding is removed, patch anchor holes used to attach scaffolding. Patch holes in stone to comply with Part 3 "Stone Patching" Article. Patch holes in mortar joints to comply with Part 3 "Repointing Stonework" Article. PART 2 - PRODUCTS 2.1 MANUFACTURERS A. In other Part 2 articles where titles below introduce lists, the following requirements apply for product selection: 1. 2. 3. Available Products: Subject to compliance with requirements, products that may be incorporated into the Work include, but are not limited to, the products specified. Products: Subject to compliance with requirements, provide one of the products specified. Available Manufacturers: Subject to compliance with requirements, manufacturers offering products that may be incorporated into the Work include, but are not limited to, the manufacturers specified. 4. Manufacturers: Subject to compliance with requirements, provide products by the manufacturers specified. 2.2 STONE MATERIALS A. Stone: Provide natural building stone of variety, color, finish, size, and shape to match existing stone. 1. For existing stone that exhibits a range of colors, finishes, sizes, or shapes, provide stone that matches that range rather than stone that matches an individual color, finish, size, or shape within that range. B. Stone: Provide natural building stone of variety, color, and finish to match Architect's sample. Match existing stone in size and shape. 2.3 MORTAR MATERIALS A. Portland Cement: ASTM C 150, Type I or Type II. 1. 2. Provide white cement containing not more than 0.60 percent total alkali when tested according to ASTM C 114. Low-Alkali Cement: Portland cement for use with limestone shall contain not more than 0.60 percent total alkali when tested according to ASTM C 114. B. Hydrated Lime: ASTM C 207, Type S. STONE RESTORATION AND CLEANING 04902 - 6 Copyright 2000 AIA MASTERSPEC 8/00 C. Quicklime: ASTM C 5, pulverized lime. D. Factory-Prepared Lime Putty: Screened, fully-slaked lime putty, prepared from pulverized lime complying with ASTM C 5. E. Mortar Sand: ASTM C 144, unless otherwise indicated. 1. Color: Provide natural sand[ or ground marble, granite, or other sound stone]; of color necessary to produce required mortar color. For pointing mortar, provide sand with rounded edges. 2. 3. Match size, texture, and gradation of existing mortar sand as closely as possible. Blend several sands, if necessary, to achieve suitable match. F. Mortar Pigments: Natural and synthetic iron oxides, compounded for mortar mixes. Use only pigments with a record of satisfactory performance in masonry mortars. G. Water: Potable. 2.4 PAINT REMOVERS A. Alkaline Paste Paint Remover: Manufacturer's standard alkaline paste formulation for removing paint coatings from masonry. 1. [Available ]Products: American Building Restoration Products, Inc.; 800 Brush Grade. Diedrich Technologies Inc.; 606/606X Extra Thick Multi-Layer Paint Remover. Hydrochemical Techniques, Inc.; Hydroclean Heavy Duty Paint Remover (HT- 716). Price Research, Ltd.; Price Heavy Duty Paint Stripper. ProSoCo; [1217 Poultice/Paint Stripper] [or] [Sure Klean Heavy-Duty Paint Stripper]. <Insert manufacturer's name; product name or designation.> B. Covered or Skin-Forming Alkaline Paint Remover: Manufacturer's standard covered or skin- forming alkaline formulation for removing paint coatings from masonry. 1. [Available ]Products: American Building Restoration Products, Inc.; Grip 'N Strip 800 F.A. Diedrich Technologies Inc.; 404 Rip-Strip. Dumond Chemicals, Inc.; Peel Away 1 System. ProSoCo; Enviro Strip #2. <Insert manufacturer's name; product name or designation.> a. b. c. d. e. f. a. b. c. d. e. C. Solvent-Type Paint Remover: Manufacturer's standard water-rinsable, solvent-type gel formulation for removing paint coatings from masonry. 1. [Available ]Products: a. American Building Restoration Products, Inc.; No. 3 Grip 'N Strip. STONE RESTORATION AND CLEANING 04902 - 7 Copyright 2000 AIA MASTERSPEC 8/00 Diedrich Technologies Inc.; 505 Special Coatings Stripper. Dominion Restoration, Inc.; Dominion Multi-Layer Paint & Graffiti Remover. Dumond Chemicals, Inc.; Peel Away 2. Hydrochemical Techniques, Inc.; Hydroclean Solvent Paint Remover (HT-300). Price Research, Ltd.; Price Strip-All. ProSoCo; Sure Klean Fast Acting Stripper. <Insert manufacturer's name; product name or designation.> D. Low-Odor, Solvent-Type Paint Remover: Manufacturer's standard low-odor, water-rinsable solvent-type gel formulation, containing no methanol or methylene chloride, for removing paint coatings from masonry. 1. [Available ]Products: American Building Restoration Products, Inc.; [800 No Lye Grip 'N Strip] [Super Bio Strip Gel] [or] [Super Bio Strip Paste]. Dumond Chemicals, Inc.; Peel Away 6. ProSoCo; [Enviro Klean NMC] [or] [Enviro Strip #3]. <Insert manufacturer's name; product name or designation.> b. c. d. e. f. g. h. a. b. c. d. 2.5 CLEANING MATERIALS A. Water for Cleaning: Potable. B. Hot Water: Heat water to a temperature of 140 to 160 deg F (60 to 71 deg C). C. D. E. Job-Mixed Detergent Solution: Solution prepared by mixing 2 cups (0.5 L) of tetrasodium polyphosphate (TSPP), 1/2 cup (125 mL) of laundry detergent, and 20 quarts (20 L) of hot water for every 5 gal. (20 L) of solution required. Job-Mixed Mold, Mildew, and Algae Remover: Solution prepared by mixing 2 cups (0.5 L) of tetrasodium polyphosphate (TSPP), 5 quarts (5 L) of 5 percent sodium hypochlorite (bleach), and 15 quarts (15 L) of hot water for every 5 gal. (20 L) of solution required. Nonacidic Gel Cleaner: Manufacturer's standard gel formulation, with pH between 6 and 9, that contains detergents and chelating agents and is specifically formulated for cleaning masonry surfaces. 1. [Available ]Products: a. b. c. Price Research, Ltd.; Price Marble Cleaner-Gel. ProSoCo; Sure Klean 942 Masonry Cleaner. <Insert manufacturer's name; product name or designation.> F. Nonacidic Liquid Cleaner: Manufacturer's standard mildly alkaline liquid cleaner formulated for removing mold, mildew, and other organic soiling from ordinary building materials, including polished stone, brick, aluminum, plastics, and wood. 1. [Available ]Products: STONE RESTORATION AND CLEANING 04902 - 8 a. b. c. d. e. a. b. c. d. e. a. b. c. d. e. f. a. b. c. d. e. Copyright 2000 AIA MASTERSPEC 8/00 Dominion Restoration, Inc.; Bio-Cleanse. Dumond Chemicals, Inc.; Safe n' Easy Architectural Cleaner/Restorer. Price Research, Ltd.; Price Non-Acid Masonry Cleaner. ProSoCo; Enviro Klean Restoration Cleaner. <Insert manufacturer's name; product name or designation.> G. Mild Acidic Cleaner: Manufacturer's standard mildly acidic cleaner containing no hydrochloric, hydrofluoric, or sulfuric acid; or chlorine bleaches. 1. [Available ]Products: Diedrich Technologies Inc.; Envirorestore 100. Dominion Restoration, Inc.; DR-60 Stone and Masonry Cleaner. Dumond Chemicals, Inc.; Safe n' Easy Heavy Duty Restoration Cleaner. ProSoCo; Sure Klean Light-Duty Restoration Cleaner. <Insert manufacturer's name; product name or designation.> H. Acidic Cleaner: Manufacturer's standard acidic masonry restoration cleaner composed of hydrofluoric acid blended with other acids, detergents, wetting agents, and inhibitors. 1. [Available ]Products: American Building Restoration Products, Inc.; 801 Heavy Duty Masonry Cleaner. Diedrich Technologies Inc.; [101 Masonry Restorer] [or] [101G Granite, Terra Cotta, and Brick Cleaner]. Hydrochemical Techniques, Inc.; Hydroclean Brick, Granite, Sandstone and Terra Cotta Cleaner (HT-626). Price Research, Ltd.; [Price Heavy Duty Restoration Cleaner] [or] [Price Restoration Cleaner]. ProSoCo; [Sure Klean Heavy-Duty Restoration Cleaner] [Sure Klean 1028 Restoration Cleaner] [or] [Sure Klean Restoration Cleaner]. <Insert manufacturer's name; product name or designation.> I. One-Part Limestone Cleaner: Manufacturer's standard one-part acidic formulation for cleaning limestone. 1. [Available ]Products: American Building Restoration Products, Inc.; X-190 Limestone & Concrete Cleaner. Hydrochemical Techniques, Inc.; Hydroclean Limestone and Marble Cleaner and Brightener (HT-907). Price Research, Ltd.; Price Limestone Restorer. ProSoCo; Sure Klean Limestone Restorer. <Insert manufacturer's name; product name or designation.> J. Two-Part Limestone Cleaner: Manufacturer's standard system consisting of potassium or sodium hydroxide based, alkaline prewash cleaner and acidic afterwash cleaner that does not contain hydrofluoric acid. 1. [Available ]Products: STONE RESTORATION AND CLEANING 04902 - 9 Copyright 2000 AIA MASTERSPEC 8/00 a. b. c. d. e. f. American Building Restoration Products, Inc.; 500 Limestone Prewash Cleaner and 500 Limestone Afterwash. Diedrich Technologies Inc.; Diedrich Limestone Cleaner Prerinse (707) and Neutralizer After-Rinse (707N). Hydrochemical Techniques, Inc.; Hydroclean Limestone and Marble Precleaner (HT-704) and Hydroclean Limestone and Marble Cleaner and Brightener (HT- 907). Price Research, Ltd.; Price Limestone Pre-Wash/Limestone After-Wash System. ProSoCo; Sure Klean 766 Limestone & Masonry Prewash and Afterwash. <Insert manufacturer's name; product name or designation.> 2.6 MISCELLANEOUS MATERIALS A. B. Stone Anchors: Type and size indicated or, if not indicated, to match existing anchors in size and type. Fabricate anchors and dowels from Type 304 stainless steel. Stone-to-Stone Adhesive: [2-part polyester or epoxy-resin stone adhesive with a 15- to 45- minute cure at 70 deg F (21 deg C)] [or] [1-part cementitious stone adhesive], recommended by adhesive manufacturer for type of stone repair indicated, and matching stone color. 1. [Available ]Products: a. Two-Part Polyester or Epoxy: 1) 2) 3) 4) Akemi North America; Akepox. Bonstone Materials, Inc.; A-199-T/B-439-T. Edison Coatings, Inc.; Flexi-Weld 520T. <Insert manufacturer's name; product name or designation.> b. One-Part Cementitious Stone Adhesive: 1) 2) Cathedral Stone Products, Inc.; Jahn Restoration Adhesive. <Insert manufacturer's name; product name or designation.> C. Stone Patching Compound: Factory-mixed cementitious product that is custom manufactured for patching stone, is vapor- and water permeable, exhibits low shrinkage, and develops high bond strength to all types of stone. Formulate in colors and textures to match stone being patched. Provide [number of colors needed] [not less than three colors] to enable matching each piece of stone. 1. [Available ]Products: a. b. c. Cathedral Stone Products, Inc.; Jahn Restoration Mortar. Edison Coatings, Inc.; Custom System 45. <Insert manufacturer's name; product name or designation.> D. Cementitious Crack Filler: An ultrafine superplasticized grout that can be injected into cracks, is suitable for application to wet or dry cracks, exhibits low shrinkage, and develops high bond strength to all types of stone. STONE RESTORATION AND CLEANING 04902 - 10 Copyright 2000 AIA MASTERSPEC 8/00 1. [Available ]Products: a. b. c. Cathedral Stone Products, Inc.; Jahn Injection Grout. Edison Coatings, Inc.; Pump-X 53i. <Insert manufacturer's name; product name or designation.> E. Liquid Strippable Masking Agent: Manufacturer's standard liquid, film-forming, strippable masking material for protecting glass, metal, and polished stone surfaces from damaging effects of acidic and alkaline masonry cleaners. 1. [Available ]Products: a. b. c. d. e. American Building Restoration Products, Inc.; LM 130 Acid Shield. Diedrich Technologies Inc.; Diedrich Acid Guard. Price Research, Ltd.; Price Mask. ProSoCo; Sure Klean Strippable Masking. <Insert manufacturer's name; product name or designation.> F. Stone Consolidation Treatment: Ready-to-use product designed for consolidation of masonry materials that have deteriorated due to weathering and exposure to pollutants. Treatment shall be composed of silicic-ethyl esters, a neutral catalyst, and solvents. 1. [Available ]Products: a. b. ProSoCo; Conservare OH Stone Strengthener. <Insert manufacturer's name; product name or designation.> G. Stone Consolidation and Water-Repellent Treatment: Ready-to-use product designed for consolidation and water-repellent treatment of masonry materials that have deteriorated due to weathering and exposure to pollutants. Treatment shall be composed of silicic-ethyl esters, a neutral catalyst, a silane water repellent, and solvents. 1. [Available ]Products: a. b. c. Edison Coatings, Inc.: System 90-II. ProSoCo; Conservare H Stone Strengthener. <Insert manufacturer's name; product name or designation.> 2.7 MORTAR MIXES A. Preparing Lime Putty: Slake quicklime and prepare lime putty according to appendix to ASTM C 5 and manufacturer's written instructions. B. Measurement and Mixing: Measure cementitious materials and sand in a dry condition by volume or equivalent weight. Do not measure by shovel; use known measure. Mix materials in a clean, mechanical batch mixer. 1. Mixing Pointing Mortar: Thoroughly mix cementitious materials and sand together before adding any water. Then mix again adding only enough water to produce a damp, unworkable mix that will retain its form when pressed into a ball. Maintain mortar in this STONE RESTORATION AND CLEANING 04902 - 11 Copyright 2000 AIA MASTERSPEC 8/00 dampened condition for 15 to 30 minutes. Add remaining water in small portions until mortar reaches desired consistency. Use mortar within one hour of final mixing; do not retemper or use partially hardened material. C. Colored Mortar: Produce mortar of color required by using selected ingredients. Do not alter specified proportions without Architect's approval. 1. Mortar Pigments: Where mortar pigments are indicated, do not exceed a pigment-to- cement ratio of 1:10 by weight. D. Do not use admixtures of any kind in mortar, unless otherwise indicated. E. Mortar Proportions: Mix mortar materials in the following proportions: 1. 2. 3. Pointing Mortar for Stone: [1 part white portland cement, 1 part lime, and 6 parts sand] [1 part white portland cement, 2 parts lime, and 6 parts sand] [1 part white portland cement, 6 parts lime, and 12 parts sand] <Insert required proportions>. a. Add mortar pigments to produce mortar colors required. Rebuilding (Setting) Mortar: 1 part white portland cement, 1 part lime, and 6 parts sand. Rebuilding (Setting) Mortar: Comply with ASTM C 270, Proportion Specification, Type N, unless otherwise indicated, with cementitious material limited to portland cement and lime. 2.8 CHEMICAL CLEANING SOLUTIONS A. Dilute chemical cleaners with water to produce solutions not exceeding concentration recommended by chemical cleaner manufacturer. B. Acidic Cleaner Solution for Unpolished Stone: Dilute with water to produce hydrofluoric acid content of 3 percent or less, but not greater than that recommended by chemical cleaner manufacturer. 1. Use only on unpolished granite, unpolished dolomite marbles, and siliceous sandstone. C. Acidic Cleaner for Polished Stone: Dilute with water to concentration demonstrated by testing that does not etch or otherwise damage polished surface, but not greater than that recommended by chemical cleaner manufacturer. 1. Use only on polished granites and polished dolomite marbles. PART 3 - EXECUTION 3.1 RESTORATION SPECIALISTS A. Available Restoration Specialist Firms: Subject to compliance with requirements, firms that may provide stone restoration and cleaning include, but are not limited to, the following: STONE RESTORATION AND CLEANING 04902 - 12 Copyright 2000 AIA MASTERSPEC 8/00 B. Restoration Specialist Firms: Subject to compliance with requirements, provide stone restoration and cleaning by one of the following: 1. <Insert, in separate subparagraphs, names of preapproved restoration specialist firms.> 3.2 PROTECTION A. Protect persons, motor vehicles, surrounding surfaces of building being restored, building site, plants, and surrounding buildings from harm resulting from stone restoration work. 1. Erect temporary protective covers over walkways and at points of pedestrian and vehicular entrance and exit that must remain in service during course of restoration and cleaning work. B. Comply with chemical cleaner manufacturer's written instructions for protecting building and other surfaces against damage from exposure to its products. Prevent chemical cleaning solutions from coming into contact with pedestrians, motor vehicles, landscaping, buildings, and other surfaces that could be harmed by such contact. 1. 2. 3. 4. 5. 1. 2. 3. 4. 1. Cover adjacent surfaces with materials that are proven to resist chemical cleaners used unless chemical cleaners being used will not damage adjacent surfaces. Use materials that contain only waterproof, UV-resistant adhesives. Apply masking agents to comply with manufacturer's written instructions. Do not apply liquid masking agent to painted or porous surfaces. When no longer needed, promptly remove masking to prevent adhesive staining. Keep wall wet below area being cleaned to prevent streaking from runoff. Do not clean stone during winds of sufficient force to spread cleaning solutions to unprotected surfaces. Neutralize and collect alkaline and acid wastes for disposal off Owner's property. Dispose of runoff from cleaning operations by legal means and in a manner that prevents soil erosion, undermining of paving and foundations, damage to landscaping, and water penetration into building interiors. C. Prevent mortar from staining face of surrounding masonry and other surfaces. Cover sills, ledges, and projections to protect from mortar droppings. Keep wall area wet below rebuilding and pointing work to discourage mortar from adhering. Immediately remove mortar in contact with exposed masonry and other surfaces. Clean mortar splatters from scaffolding at end of each day. D. Remove[ gutters and] downspouts adjacent to stone and store[ where indicated] during stone restoration and cleaning. Reinstall when stone restoration and cleaning is complete. Provide temporary rain drainage during work[ as indicated] to direct water away from building. STONE RESTORATION AND CLEANING 04902 - 13 Copyright 2000 AIA MASTERSPEC 8/00 3.3 UNUSED ANCHOR REMOVAL A. Remove masonry anchors, brackets, wood nailers, and other extraneous items no longer in use unless identified as historically significant or indicated to remain. 1. 2. 3. Remove items carefully to avoid spalling or cracking stone. If item cannot be removed without damaging surrounding stone, cut off item flush with surface and core drill surrounding stone and item as close around item as practical. Patch holes where items were removed unless directed to remove and replace units. 3.4 STONE REMOVAL AND REPLACEMENT A. At locations indicated, remove stone that has deteriorated or is damaged beyond repair. Carefully demolish or remove entire units from joint to joint, without damaging surrounding stone, in a manner that permits replacement with full-size units. B. Support and protect remaining stonework that surrounds removal area. Maintain flashing, reinforcement, lintels, and adjoining construction in an undamaged condition. C. Notify Architect of unforeseen detrimental conditions including voids, cracks, bulges, and loose masonry units in existing masonry backup, rotted wood, rusted metal, and other deteriorated items. D. Remove in an undamaged condition as many whole stone units as possible. E. F. 1. 2. 3. 4. Remove mortar, loose particles, and soil from stone by cleaning with hand chisels, brushes, and water. Remove sealants by cutting close to stone with utility knife and cleaning with solvents. Store stone for reuse, as indicated. Deliver cleaned stone not required for reuse to Owner, unless otherwise directed. Clean stone surrounding removal areas by removing mortar, dust, and loose particles in preparation for replacement. Replace removed stone with other removed stone, where possible, or with new stone matching existing stone, including size. Butter vertical joints for full width before setting and set units in full bed of mortar, unless otherwise indicated. Replace existing anchors with new anchors of size and type indicated. 1. 2. Tool exposed mortar joints in repaired areas to match joints of surrounding existing stonework. Rake out mortar used for laying stone before mortar sets and point new mortar joints in repaired area to comply with requirements for repointing existing stone, and at same time as repointing of surrounding area. 3.5 PARTIAL STONE REPLACEMENT (DUTCHMAN REPAIR) A. At locations indicated, remove rectangular portion of stone units. Carefully remove stone by making vertical and horizontal saw cuts at face of stone and demolishing corner portion of stone STONE RESTORATION AND CLEANING 04902 - 14 Copyright 2000 AIA MASTERSPEC 8/00 unit to depth required for fitting partial replacement (Dutchman). Make edges of stone at cuts smooth and square to each other and to finished surface. Make back of removal area flat and parallel to stone face. B. Remove mortar from joints that abut area of stone removal to same depth as stone was removed. Remove loose mortar particles and other debris from surfaces to be bonded and surfaces of adjacent stone units that will receive mortar by cleaning with stiff-fiber brush. C. Trim partial replacement (Dutchman) to accurately fit area where stone was removed. D. Apply stone-to-stone adhesive to comply with adhesive manufacturer's written instructions. Coat bonding surfaces of existing stone and partial replacement, completely filling all crevices and voids. E. F. Apply partial replacement while adhesive is still tacky and hold securely in place until adhesive has cured. Use shims, clamps, wedges, or other devices as necessary to align face of partial replacement with face of stone unit being repaired. After adhesive has fully cured, further anchor partial replacements where indicated with 1/4- inch- (6-mm-) diameter, plain stainless-steel rods set into 1/4-inch- (6-mm-) diameter holes drilled at a 45-degree downward angle through face of stone.[ Center and space anchor rods between 3 and 5 inches (75 and 125 mm) apart and at least 2 inches (50 mm) from any edge. Insert rods at least 2 inches (50 mm) into backing stone and 2 inches (50 mm) into partial replacements with end countersunk at least 3/4 inch (19 mm) from exposed face of stone.] G. Clean residual adhesive from exposed surfaces and patch chipped areas and drill holes as specified in "Stone Patching" Article. 3.6 STONE PLUG REPAIR A. At locations indicated, remove cylindrical piece of damaged stone by core-drilling perpendicular to stone surface. B. Prepare a replacement plug by core-drilling replacement stone. Use a drill sized to produce a core that will fit into hole drilled in damaged stone with only minimum gap necessary for adhesive. C. Apply stone-to-stone adhesive to comply with adhesive manufacturer's written instructions. Coat bonding surfaces of existing stone and plug, completely filling all crevices and voids. D. Apply plug while adhesive is still tacky and hold securely in place until adhesive has cured. E. Clean residual adhesive from exposed surfaces. 3.7 STONE REPAIR A. Carefully remove loose stone fragments in areas indicated to be repaired. Reuse only stone fragments that are in sound condition. STONE RESTORATION AND CLEANING 04902 - 15 Copyright 2000 AIA MASTERSPEC 8/00 B. Remove soil, loose stone particles, mortar, and other debris or foreign material from fragment surfaces to be bonded and stone from which fragments were removed by cleaning with stiff- fiber brush. C. Apply stone-to-stone adhesive to comply with adhesive manufacturer's written instructions. Coat bonding surfaces of fragments and stone from which fragments were removed, completely filling all crevices and voids. Fit stone fragments onto building stone while adhesive is still tacky and hold fragment securely in place until adhesive has cured. After adhesive has fully cured, further anchor stone fragments where indicated with 1/4-inch- (6-mm-) diameter, plain stainless-steel rods set into 1/4-inch- (6-mm-) diameter holes drilled at a 45-degree downward angle through face of stone.[ Center and space anchor rods between 3 and 5 inches (75 and 125 mm) apart and at least 2 inches (50 mm) from any edge. Insert rods at least 2 inches (50 mm) into backing stone and 2 inches (50 mm) into stone fragments with end countersunk at least 3/4 inch (19 mm) from exposed face of stone.] F. Clean residual adhesive from exposed surfaces and patch chipped areas and drilled holes as specified in "Stone Patching" Article. 3.8 CRACK INJECTION A. General: Comply with cementitious crack filler manufacturer's written instructions. B. Drill 1/4-inch- (6-mm-) diameter, downward-sloping injection holes as follows: 1. 2. 3. 4. Transverse Cracks Less Than 3/8 inch (10 mm) Wide: Drill holes through center of crack at 12 to 18 inches (300 to 500 mm) o.c. Transverse Cracks More Than 3/8 inch (10 mm) Wide: Drill holes through center of crack at 18 to 36 inches (500 to 1000 mm) o.c. Delaminations: Drill holes at approximately 18 inches (500 mm) o.c. both vertically and horizontally. Drill holes 2 inches (50 mm) deep. Where possible drill holes in mortar joints. Clean out drill holes and cracks with compressed air and water. Remove dirt and organic matter, loose material, sealants, and failed crack repair materials. Place plastic injection ports in drilled holes and seal face of cracks between injection ports with clay or other nonstaining, removable plugging material. Leave openings at upper ends of cracks for air release. Inject cementitious crack filler through ports sequentially, beginning at one end of area and working to opposite end; where possible begin at lower end of injection area and work upward. Inject filler until it extrudes from adjacent ports. After port has been injected, plug with clay or other suitable material and begin injecting filler at adjacent port, repeating process until all ports have been injected. F. Clean cementitious crack filler from face of stone before it sets by scrubbing with water. D. E. C. D. E. STONE RESTORATION AND CLEANING 04902 - 16 Copyright 2000 AIA MASTERSPEC 8/00 G. After cementitious crack filler has set, remove injection ports, plugging material, and excess filler. Patch injection holes and surface of cracks as specified in "Stone Patching" Article. 3.9 STONE PATCHING A. Patch the following stone units: 1. 2. 3. 4. Units indicated to be patched. Units with holes. Units with chipped edges or corners. Units with small areas of deep deterioration. B. C. E. F. Remove and replace existing patches, unless otherwise indicated or approved by Architect. Cut out deteriorated stone and adjacent stone that has begun to deteriorate. Remove additional material so patch will not have feathered edges and will be at least 1/4 inch (6 mm) thick, but not less than recommended by patching compound manufacturer. 1. Remove loose particles, soil, debris, oil, and other contaminants from existing stone units at locations to be patched by cleaning with stiff-fiber brush. D. Mix patching compound in individual batches to match each stone unit being patched. Combine one or more colors of patching compound, as needed, to produce exact match. Brush-coat stone surfaces with slurry coat of patching compound according to manufacturer's written instructions. Place patching compound in layers as recommended by patching compound manufacturer, but not less than 1/4 inch (6 mm) or more than 2 inches (50 mm) thick. Roughen surface of each layer to provide a key for next layer. 1. 2. Trowel, scrape, or carve surface of patch to match texture and surface plane of surrounding stone. Shape and finish surface before or after curing, as determined by testing, to best match existing stone. Build patch up 1/4 inch (6 mm) above surrounding stone and carve surface to match adjoining stone after patching compound has hardened. G. Keep each layer damp for 72 hours or until patching compound has set. H. Remove and replace patches with hairline cracks or that show separation from stone at edges, and those that do not match adjoining stone in color or texture. 3.10 CLEANING STONE, GENERAL A. Proceed with cleaning in an orderly manner; work from top to bottom of each scaffold width and from one end of each elevation to the other. B. Use only those cleaning methods indicated for each material and location. STONE RESTORATION AND CLEANING 04902 - 17 Copyright 2000 AIA MASTERSPEC 8/00 1. 2. 3. 4. 5. 6. 7. Do not use wire brushes or brushes that are not resistant to chemical cleaner being used. Do not use plastic-bristle brushes if natural-fiber brushes will resist chemical cleaner being used. Use spray equipment that provides controlled application at volume and pressure indicated, measured at spray tip. Adjust pressure and volume to ensure that cleaning methods do not damage stone. a. Equip units with pressure gages. For chemical cleaner spray application, use low-pressure tank or chemical pump suitable for chemical cleaner indicated, equipped with cone-shaped spray tip. For water spray application, use fan-shaped spray tip that disperses water at an angle of 25 to 50 degrees. For high-pressure water spray application, use fan-shaped spray tip that disperses water at an angle of at least 40 degrees. For heated water spray application, use equipment capable of maintaining temperature between 140 and 160 deg F (60 and 71 deg C) at flow rates indicated. For steam application, use steam generator capable of delivering live steam at nozzle. C. D. E. Perform each cleaning method indicated in a manner that results in uniform coverage of all surfaces, including corners, moldings, and interstices, and that produces an even effect without streaking or damaging stone surfaces. Removing Plant Growth: Completely remove plant, moss, and shrub growth from stone surfaces. Carefully remove plants, creepers, and vegetation by cutting at roots and allowing to dry as long as possible before removal. Remove loose soil or debris from open joints to whatever depth they occur. Preliminary Cleaning: Before beginning general cleaning, remove extraneous substances that are resistant to cleaning methods being used. Extraneous substances include paint, calking, asphalt, and tar. 1. 2. Carefully remove heavy accumulations of material from surface of masonry with sharp chisel. Do not scratch or chip masonry surface. Remove paint and calking with alkaline paint remover. a. b. Comply with requirements for paint removal. Repeat application up to two times if needed. 3. Remove asphalt and tar with solvent-type paint remover. a. b. c. d. Apply only to asphalt and tar by brush without prewetting. Allow paint remover to remain on surface for 10 to 30 minutes. Rinse off with [cold] [hot] water using low-pressure spray. Repeat application if needed. F. Water Application Methods: 1. Water Soak Application: Soak stone surfaces by applying water continuously and uniformly to limited area for time indicated. Apply water at low pressures and low STONE RESTORATION AND CLEANING 04902 - 18 Copyright 2000 AIA MASTERSPEC 8/00 2. volumes in multiple fine sprays using perforated hoses or multiple spray nozzles. Erect a protective enclosure constructed of polyethylene sheeting to cover area being sprayed. Spray Applications: Unless otherwise indicated, hold spray nozzle at least 6 inches (150 mm) from surface of stone and apply water in horizontal back and forth sweeping motion, overlapping previous strokes to produce uniform coverage. Steam Wash: Apply steam to masonry surfaces at pressures not exceeding 80 psi (550 kPa). Hold nozzle at least 6 inches (150 mm) from surface of masonry and apply steam in horizontal back and forth sweeping motion, overlapping previous strokes to produce uniform coverage. Chemical Cleaner Application Methods: Apply chemical cleaners to stone surfaces to comply with chemical cleaner manufacturer's written instructions; use brush or spray application methods, at Contractor's option. Do not spray apply at pressures exceeding 50 psi (345 kPa). Do not allow chemicals to remain on surface for periods longer than those indicated or recommended by manufacturer. Rinse off chemical residue and soil by working upward from bottom to top of each treated area at each stage or scaffold setting. Periodically during each rinse, test pH of rinse water running off of cleaned area to determine that chemical cleaner is completely removed. 1. Apply neutralizing agent and repeat rinse, if necessary, to produce tested pH of between 6.7 and 7.5. G. H. I. J. After cleaning is complete, remove protection no longer required. Remove tape and adhesive marks. 3.11 PAINT REMOVAL A. Paint Removal with Alkaline Paste Paint Remover: Apply paint remover to dry, painted stone with brushes. Allow paint remover to remain on surface for period recommended by manufacturer. Rinse with [cold] [hot] water applied by [low] [medium] [high]-pressure spray to remove chemicals and paint residue. Repeat process, if necessary, to remove all paint. Apply acidic cleaner to stone, while surface is still wet, using low-pressure spray equipment or soft-fiber brush. Let cleaner remain on surface for period recommended by chemical cleaner manufacturer. Rinse with cold water applied by [low] [medium] [high]-pressure spray to remove chemicals and soil. B. Paint Removal with Covered or Skin-Forming Alkaline Paint Remover: Apply paint remover to dry, painted stone with trowel, spatula, or as recommended by manufacturer. Apply cover, if required by manufacturer, per manufacturer's written instructions. Allow paint remover to remain on surface for period recommended by manufacturer or as determined in test panels. Scrape off paint and remover and collect for disposal. 1. 2. 3. 4. 5. 6. 1. 2. 3. 4. STONE RESTORATION AND CLEANING 04902 - 19 5. 6. 7. 8. 1. 2. 3. 1. 2. 3. 4. Copyright 2000 AIA MASTERSPEC 8/00 Rinse with [cold] [hot] water applied by [low] [medium] [high]-pressure spray to remove chemicals and paint residue. Use alkaline paste paint remover according to "Paint Removal with Alkaline Paste Paint Remover" Paragraph, if necessary, to remove remaining paint. Apply acidic cleaner to masonry, while surface is still wet, using low-pressure spray equipment or soft-fiber brush. Let cleaner remain on surface for period recommended by chemical cleaner manufacturer. Rinse with cold water applied by [low] [medium] [high]-pressure spray to remove chemicals and soil. C. Paint Removal with Solvent-Type Paint Remover: Apply thick coating of paint remover to painted stone with natural-fiber cleaning brush, deep-nap roller, or large paint brush. Allow paint remover to remain on surface for period recommended by manufacturer. Agitate periodically with stiff-fiber brush. Rinse with cold water applied by [low] [medium] [high]-pressure spray to remove chemicals and paint residue. 3.12 CLEANING STONEWORK A. Cold-Water Soak: Apply cold water by prolonged spraying. Continue spraying until surface encrustation has softened sufficiently to permit its removal by water wash, as indicated by cleaning tests. Continue spraying for 72 hours. Remove soil and softened surface encrustation from stone with cold water applied by low-pressure spray. B. Hot-Water Wash: Use hot water applied by [low] [medium] [high]-pressure spray. C. Detergent Cleaning: 1. Wet stone with [cold] [hot] water applied by low-pressure spray. 2. Scrub stone with detergent solution using medium-soft brushes until soil is thoroughly dislodged and can be removed by rinsing. Use small brushes to remove soil from mortar joints and crevices. Dip brush in solution often to ensure that adequate fresh detergent is used and that stone surface remains wet. Rinse with [cold] [hot] water applied by [low] [medium] [high]-pressure spray to remove detergent solution and soil. Repeat cleaning procedure above where required to produce cleaning effect established by mockup. 3. 4. D. Mold, Mildew, and Algae Removal: 1. Wet stone with [cold] [hot] water applied by low-pressure spray. 2. 3. Apply mold, mildew, and algae remover by brush[ or low-pressure spray]. Scrub stone with medium-soft brushes until mold, mildew, and algae are thoroughly dislodged and can be removed by rinsing. Use small brushes for mortar joints and STONE RESTORATION AND CLEANING 04902 - 20 Copyright 2000 AIA MASTERSPEC 8/00 crevices. Dip brush in mold, mildew, and algae remover often to ensure that adequate fresh cleaner is used and that stone surface remains wet. Rinse with [cold] [hot] water applied by [low] [medium] [high]-pressure spray to remove mold, mildew, and algae remover and soil. Repeat cleaning procedure above where required to produce cleaning effect established by mockup. 4. 5. E. Nonacidic Gel Chemical Cleaning: 1. Wet stone with [cold] [hot] water applied by low-pressure spray. 2. Apply nonacidic gel cleaner in 1/8-inch (3-mm) thickness by brush, working into joints and crevices. Apply quickly and do not brush out excessively so area will be uniformly covered with fresh cleaner and dwell time will be uniform throughout area being cleaned. Let cleaner remain on surface for period indicated below: 3. a. b. As recommended by chemical cleaner manufacturer. As established by mockup. 4. 5. 6. Remove bulk of nonacidic gel cleaner by squeegeeing into containers for disposal. Rinse with [cold] [hot] water applied by [low] [medium] [high]-pressure spray to remove chemicals and soil. Repeat cleaning procedure above where required to produce cleaning effect established by mockup. Do not repeat more than once. If additional cleaning is required, use steam wash. F. Nonacidic Liquid Chemical Cleaning: 1. Wet stone with [cold] [hot] water applied by low-pressure spray. 2. Apply cleaner to stone[ in two applications] by brush[ or low-pressure spray]. Let cleaner remain on surface for period indicated below: a. b. c. As recommended by chemical cleaner manufacturer. As established by mockup. Two to three minutes. 3. 4. Rinse with [cold] [hot] water applied by [low] [medium] [high]-pressure spray to remove chemicals and soil. Repeat cleaning procedure above where required to produce cleaning effect established by mockup. Do not repeat more than once. If additional cleaning is required, use steam wash. G. [Mild Acidic] [Acidic] Chemical Cleaning: 1. Wet stone with cold water applied by low-pressure spray. 2. Apply cleaner to stone[ in two applications] by brush[ or low-pressure spray]. Let cleaner remain on surface for period indicated below: a. b. c. As recommended by chemical cleaner manufacturer. As established by mockup. Two to three minutes. STONE RESTORATION AND CLEANING 04902 - 21 Copyright 2000 AIA MASTERSPEC 8/00 3. 4. Rinse with cold water applied by [low] [medium] [high]-pressure spray to remove chemicals and soil. Repeat cleaning procedure above where required to produce cleaning effect established by mockup. Do not repeat more than once. If additional cleaning is required, use a steam wash. H. One-Part Limestone Chemical Cleaning: 1. Wet stone with [cold] [hot] water applied by low-pressure spray. 2. Apply cleaner to stone by brush[ or low-pressure spray]. Let cleaner remain on surface for period recommended by manufacturer. Immediately repeat application of one-part limestone cleaner as indicated above over the same area. Rinse with [cold] [hot] water applied by medium-pressure spray to remove chemicals and soil. 4. 3. I. Two-Part Limestone Chemical Cleaning: 1. Wet stone with [cold] [hot] water applied by low-pressure spray. 2. Apply alkaline prewash cleaner to stone by brush or roller. Let cleaner remain on surface for period recommended by cleaner manufacturer, unless otherwise indicated. Rinse with [cold] [hot] water applied by medium-pressure spray to remove chemicals and soil. Apply acidic afterwash cleaner to stone[ in two applications], while surface is still wet, using low-pressure spray equipment, deep-nap roller, or soft-fiber brush. Let neutralizer remain on surface for period recommended by manufacturer, unless otherwise indicated. Rinse with cold water applied by medium-pressure spray to remove chemicals and soil. Repeat cleaning procedure above where required to produce cleaning effect established by mockup. Do not repeat more than once. 3.13 REPOINTING STONEWORK A. Rake out and repoint mortar joints to the following extent: All joints in areas indicated. Joints where mortar is missing or where they contain holes. Cracked joints where cracks can be penetrated at least 1/4 inch (6 mm) by a knife blade 0.027 inch (0.7 mm) thick. Cracked joints where cracks are 1/8 inch (3 mm) or more in width and of any depth. Joints where they sound hollow when tapped by metal object. Joints where they are worn back 1/4 inch (6 mm) or more from surface. Joints where they are deteriorated to point that mortar can be easily removed by hand. Joints, other than those indicated as sealant-filled joints, where they have been filled with substances other than mortar. 3. 4. 5. 6. 1. 2. 3. 4. 5. 6. 7. 8. B. Do not rake out and repoint joints where not required. C. Rake out joints as follows: STONE RESTORATION AND CLEANING 04902 - 22 Copyright 2000 AIA MASTERSPEC 8/00 1. 2. 3. Remove mortar from joints to depth of [joint width plus 1/8 inch (3 mm)] [2 times joint width] [2-1/2 times joint width], but not less than 1/2 inch (13 mm) or not less than that required to expose sound, unweathered mortar. Remove mortar from stonework surfaces within raked-out joints to provide reveals with square backs and to expose stone for contact with pointing mortar. Brush, vacuum, or flush joints to remove dirt and loose debris. Do not spall edges of stone units or widen joints. Replace or patch damaged stone units as directed by Architect. a. b. Cut out mortar by hand with chisel and mallet. Do not use power-operated grinders without Architect's written approval based on submission by Contractor of a satisfactory quality-control program and demonstrated ability of operators to use tools without damaging stone. Quality-control program shall include provisions for supervising performance and preventing damage due to worker fatigue. Cut out center of mortar joints using angle grinders with diamond-impregnated metal blades. Remove remaining mortar by hand with chisel and mallet. Strictly adhere to written quality-control program. Quality-control program shall include provisions for demonstrating ability of operators to use tools without damaging stone, supervising performance, and preventing damage due to worker fatigue. D. Notify Architect of unforeseen detrimental conditions including voids in mortar joints, cracks, loose stone, rotted wood, rusted metal, and other deteriorated items. E. Point joints as follows: 1. 2. 3. Rinse stonework-joint surfaces with water to remove dust and mortar particles. Time rinsing application so, at time of pointing, joint surfaces are damp but free of standing water. If rinse water dries, dampen stonework-joint surfaces before pointing. Apply pointing mortar first to areas where existing mortar was removed to depths greater than surrounding areas. Apply in layers not greater than 3/8 inch (9 mm) until a uniform depth is formed. Fully compact each layer thoroughly and allow it to become thumbprint hard before applying next layer. After low areas have been filled to same depth as remaining joints, point all joints by placing mortar in layers not greater than 3/8 inch (9 mm). Fully compact each layer and allow to become thumbprint hard before applying next layer. Where existing stone has worn or rounded edges, slightly recess finished mortar surface below face of stone to avoid widened joint faces. Take care not to spread mortar over edges onto exposed stone surfaces or to featheredge mortar. 4. When mortar is thumbprint hard, tool joints to match original appearance of joints. Remove excess mortar from edge of joint by brushing. F. Cure mortar by maintaining in thoroughly damp condition for at least 72 hours, including weekends and holidays. 1. 2. Acceptable curing methods include covering with wet burlap and plastic sheeting, periodic hand misting, and periodic mist spraying using system of pipes, mist heads, and timers. Adjust curing methods to ensure that pointing mortar is damp throughout its depth without eroding surface mortar. STONE RESTORATION AND CLEANING 04902 - 23 Copyright 2000 AIA MASTERSPEC 8/00 G. Where repointing work precedes cleaning of existing stone, allow mortar to harden at least 30 days before beginning cleaning work. 3.14 STONE CONSOLIDATION TREATMENT A. Apply treatment to clean, dry surfaces according to manufacturer's written instructions. Remove areas of blind exfoliation and delamination before applying. B. Apply in cycles (repeated applications) to small sections of stonework, not more than 100 sq. ft. (9 sq. m) in area. Each cycle shall consist of 3 successive saturating applications, applied at 5- to 15-minute intervals, depending on drying conditions. C. Apply by low-pressure spray to point of rejection in each application. Apply from bottom of section to top. D. Apply 3 cycles, allowing treated surface to dry for 60 to 90 minutes between cycles. Protect treated surfaces from rain for 48 hours after treatment. Allow treated surfaces to dry for at least 21 days before repointing, patching, or applying water repellents or sealants. 3.15 FINAL CLEANING A. After mortar has fully hardened, thoroughly clean exposed stone surfaces of excess mortar and foreign matter; use wood scrapers, stiff-nylon or -fiber brushes, and clean water, spray applied at low pressure. 1. 2. Do not use metal scrapers or brushes. Do not use acidic or alkaline cleaners. B. Wash adjacent woodwork and other nonmasonry surfaces. Use detergent and soft brushes or cloths. Clean mortar and debris from roof; remove debris from gutters and downspouts. Rinse off roof and flush gutters and downspouts. Sweep and rake adjacent pavement and grounds to remove mortar and debris. Where necessary, pressure wash surfaces to remove mortar, dust, dirt, and stains. 3.16 FIELD QUALITY CONTROL Inspectors: Owner will engage qualified independent inspectors to perform inspections and prepare test reports. Allow inspectors use of lift devices and scaffolding, as needed, to perform inspections. B. Architect's Project Representatives: Architect will assign Project representatives to help carry out Architect's responsibilities at the site, including observing progress and quality of portion of E. F. C. D. A. STONE RESTORATION AND CLEANING 04902 - 24 Copyright 2000 AIA MASTERSPEC 8/00 the Work completed. Allow Architect's Project representatives use of scaffolding, as needed, to observe progress and quality of portion of the Work completed. C. Notify [inspectors] [and] [Architect's Project representatives] in advance of times when lift devices and scaffolding will be relocated. Do not relocate lift devices and scaffolding until [inspectors] [and] [Architect's Project representatives] have had reasonable opportunity to make [inspections] [and] [observations] of work areas at lift device or scaffold location. END OF SECTION 04902 STONE RESTORATION AND CLEANING 04902 - 25