B.4.1 - 3006 Hemphill Park - plans — original pdf
Backup
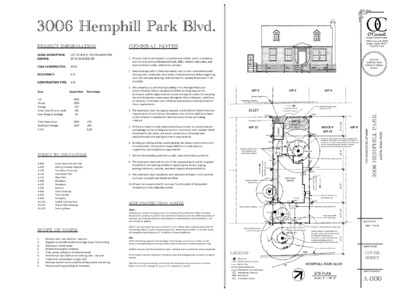
North West 3006 Hemphill Park Blvd. PROJECT INFORMATION GENERAL NOTES LEGAL DESCRIPTION: ZONING: LOT 11 BLK 9, FRUTH ADDITION SF-3-HD-NCCD-NP YEAR CONSTRUCTED: 1935 OCCUPANCY: R-1 CONSTRUCTION TYPE: V-B Area Square Feet Percentage Lot House Garage Exist. stone & conc. walks New Stoop & landings Total Impervious Building Coverage F.A.R. 5613 1609 220 196 68 2093 1897 37% 34% 0.29 INDEX TO DRAWINGS A-000 A-001 A-110 A-120 A-121 A-201 A-202 A-301 A-501 A-502 A-610 AS-120 AS-121 AS-122 Cover Sheet and Site Plan Zoning Envelope Diagrams Demolition Drawings Foundation Plan Floor Plan Elevations Elevations Sections Porch Drawings Porch Details Schedules Roof & Framing Plans Braced Wall Drawings Framing Notes SCOPE OF WORK 1. 2. 3. 4. 5. 6. 7. 8. 9. Remove later rear addition - see plan Regrade to provide positive drainage away from building Replace all rotted wood Restore the original windows Prep, prime, and paint all exterior wood Reconstruct rear addition on existing slab – see plan Install new composition shingle roof Relocate electric service and install new panel and wiring Replace existing plumbing as necessary 1. 2. 3. 4. 5. 6. All work shall be performed in a professional matter, and in accordance with the International Residential Code, 2021, related trade codes, and applicable local codes, ordinances and laws. Base drawings used in these documents may contain small dimensional discrepancies. Contractor shall verity critical dimensions before beginning work. Do not scale drawings. Ask Architect for needed dimensions if not provided. This property is a contributing building in the Aldridge Place Local Historic District. Historic designation of this building requires the South Contractor and his subcontractors to exercise special caution in executing the work to prevent unnecessary damage to historic features, conditions, or materials. Contractor shall inform all subcontractors and workmen of these requirements. The Contractor shall thoroughly example and familiarize himself with the requirements of the Contract Documents. Any conflicts shall be brought to the Architect's attention for resolution prior to the work being installed. Perform all work in a safe and conscientious manner to prevent injuries and damage to the building and workers. Contractor shall maintain OSHA Standards for job safety and worker protection, and comply with applicable state and local government requirements. Building permitting will be coordinated by the Owner and Architect prior to construction. Contractor is responsible for all trade permits, inspections, and compliance requirements. 7. Maintain the building and site in a safe, clean and orderly condition. 8. The Contractor shall visit the site of the proposed work and full acquaint himself with the existing conditions regarding site access, staging, parking limitations, security, and other aspects of constructibility. 9. The Contractor shall coordinate work between all trades in this contract to ensure a smooth and timely workflow. 10. All work to be warranted for one year from the date of Substantial Completion unless otherwise noted. SITE PROTECTION NOTES TREES: 1) Grading for positive drainage away from building will be performed within limitations placed on the property by Austin's tree protection ordinance and rules. Utility excavation, if required, must include additional tree protection as identified by a certified arborist, and may include air spading. 2) Erect tree protection fencing at perimeter of LOC. Where CRZ is unprotected outside of the fencing, install 6" mulch in unprotected area. Where fence is within 4" of trunk, install 2x4 strapped on planking up to 8', in addition to fence installation. SITE: 1) Should existing vegetation be damaged or lost during construction activities, install erosion and sedimentation controls per 25-8-181 of the Austin Land Development Code. 2) Debris disposal shall be provided by trailer, removed from site when full and on weekends. 3) The limited concrete needed for foundation pads will be bagged mix, no wash-out will be needed. 4) Protect existing outbuildings and fencing from damage during construction activities. Repair construction damage, if any, prior to completion of project. 3908 Avenue B, #309 Austin, Texas 78751 512|751-1374 East NOT FOR CONSTRUCTION TERESA O'CONNELL #15432 LOT 4 LOT 5 overhead electric e e e e e e e e e (N 30°00'00" E 44.00') N 29°24'12" E 43.70' Materials Staging Area shown hatched 570.6' e LOC 0 7 5 569.7' LOC LOT 3 power pole ALLEY Temporary Toilet LOT 12 Remove concrete and stone walkways and curbs shown dashed Replace Existing Wood Fence 16" Pecan New Limestone Pier at Corner of Property = LOC LEGEND Elevation Limits of Construction Fence Line Overhead Electric Wastewater (unconfirmed) Wastewater Cleanout Benchmark Critical Root Zone C (BM) CRZ e WW BLOCK 9 LOT 10 568.8' LOT 9 Protect 26" Sycamore per Site Protection requirements throughout construction. Do not disburb more than 4" of surface soil in 1/2 CRZ. No ground disturbance allowed in 1/4 CRZ. Pruning shall be performed by a licensed arborist, and shall not exceed 20% of the limbs. New Electric Meter location " 4 / 1 4 - ' 3 2 " 0 - ' 0 4 " 0 - ' 0 4 " 2 / 1 9 - ' 4 2 LOT 11 0.1288 acres 5,613 sq. ft. C O L 568.9' 569' 568 567.9' ) ' 0 0 . 8 2 1 W ' " 0 0 0 0 ° 0 6 N ( ' . 1 6 7 2 1 W ' " 0 0 0 0 ° 0 6 N C O L = C O L = = = = C O L E G A R A G 569 e e w w 4.7' 2 '4.8' 0 . 8.7' e 8 6 . ' ' 2 . 6 5 ONE STORY HOUSE 565.9' FF ELEV 568.5' 31.8' 567 = 6.0' = = = C O L 14" Pine ' . 6 4 2 8" Elm = = 565.8' 26" Sycamore C O L 568 11.4' = = = = 567.6' c / a ' 0 . 6 2 ' S 6 0 ° 1 1 3 9 " E 1 2 8 . 0 6 ' ' ( S 6 0 ° 0 0 0 0 " E 1 2 7 . 0 0 ' ) 566.8' ' 4 . 8 1.1' ' 8 4 . ' 4 . 8 5.0' 567 C O L C O L New 42" H Rail Fence at Property Line New Gravel Walk with Brick Edges 5 6 6 C W W LOC LOC S 29°59'24" W 44.13' as found (S 30°00'00" W 44.00') record call 26" Elm 565 (BM) New 42" H. Wood Rail Fence with Gate Verify condition of wastewater line through scoping. Should replacement be required, and prior to any excavation, consult with arborist to develop and implement tree protection plan for tree in city ROW " 9 - ' 6 3 Existing Curb & Gutter 5 6 4 HEMPHILL PARK BLVD SITE PLAN Scale: 1" = 20'-0" T N E M P O L E V E D S D R B E V I F I K R A L P L I H P M E H 6 0 0 3 K R A P L L I H P M E H 6 0 0 3 5 0 7 8 7 S A X E T , N I T S U A ISSUE DATE PRINT: 3/3/22 SHEET NAME COVER SHEET SHEET NUMBER A-000 Remove Stone Walkway New Brick Stoop with Porch F I V E B I R D S D E V E L O P M E N T A U S T I N , T E X A S 7 8 7 0 5 Front Yard Area 1 Area 2 Area 3 e n i L y t r e p o r P " 0 - ' 0 3 e n i L g n d i l i u B t n o r F 12 10 HEMPHILL PARK BLVD. 24'-6 1/2" High Pt. Area 1 = 567.9' 40'-0" 40'-0" High Pt. Area 2 = 568.9' High Pt. Area 3 = 570.6' 4 SETBACK PLANE COMPLIANCE – north property line Scale: 1/8" = 1'-0" 5'-0" Sideyard 5'-0" Sideyard 5'-0" Sideyard " 0 - ' 5 1 e n i L y t r e p o r P High Pt. Area 1 = 567.9' e n i L y t r e p o r P e n i L y t r e p o r P 3 SETBACK PLANES – East property line Scale: 1/8" = 1'-0" 2 SETBACK PLANES – west property line Scale: 1/8" = 1'-0" 10'-0" Rear Setback " 0 - ' 5 1 e n i L y t r e p o r P Area 3 Area 2 Area 1 t n o r F e n i L g n d i l i u B " 0 - ' 0 3 " 0 - ' 0 3 High Pt. Area 3 = 570.6' High Pt. Area 2 = 568.9' 1 SETBACK PLANE COMPLIANCE – south property line Scale: 1/8" = 1'-0" 40'-0" High Pt. Area 1 = 567.9' 40'-0" 24'-6 1/2" k c a b t e S r a e R e n i L y t r e p o r P " 0 - ' 5 1 3908 Avenue B, #309 Austin, Texas 78751 512|751-1374 NOT FOR CONSTRUCTION TERESA O'CONNELL #15432 5'-0" Sideyard " 0 - ' 0 3 " 0 - ' 5 1 e n i L y t r e p o r P High Pt. Area 3 = 570.6' e n i L y t r e p o r P HEMPHILL PARK BLVD. T N E M P O L E V E D S D R B E V I F I K R A L P L I H P M E H 6 0 0 3 K R A P L L I H P M E H 6 0 0 3 5 0 7 8 7 S A X E T , N I T S U A ISSUE DATE PRINT: 3/3/22 SHEET NAME ZONING ENVELOPE DIAGRAMS SHEET NUMBER A-001 F I V E B I R D S D E V E L O P M E N T A U S T I N , T E X A S 7 8 7 0 5 Remove Roofing for New Roof Remove Rear Addition Remove Roof and Framing Remove Rear Addition Remove Roof and Framing Remove Rear Addition 4 DEMOLITION NORTH ELEV. Scale: 1/8" = 1'-0" 3 DEMOLITION WEST ELEV. Scale: 1/8" = 1'-0" 2 DEMOLITION SOUTH ELEV. Scale: 1/8" = 1'-0" Remove Doors and Windows, and all decayed Siding Remove Exist. Stone Stoop 3908 Avenue B, #309 Austin, Texas 78751 512|751-1374 NOT FOR CONSTRUCTION TERESA O'CONNELL #15432 T N E M P O L E V E D S D R B E V I F I K R A L P L I H P M E H 6 0 0 3 K R A P L L I H P M E H 6 0 0 3 5 0 7 8 7 S A X E T , N I T S U A ISSUE DATE PRINT: 3/3/22 SHEET NAME DEMOLITION DRAWINGS SHEET NUMBER A-110 1 DEMOLITION PLAN Scale: 1/4" = 1'-0" 0 5 10 FT Temporarily Relocate Electric Service Remove Partitions as shown at Kitchen Remove Rear Addition Complete down to Slab Remove Baths, and Partitions as shown, Salvage Doors to owner F I V E B I R D S D E V E L O P M E N T A U S T I N , T E X A S 7 8 7 0 5 Excavate to below Floor Framing and Inspect for decay and insect damage. Report to architect conditions found. Install 1/2" dia. Anchor Bolts 4'-0" O.C. as per detail Verify Anchor Bolt sizes & locations, Report to Architect Existing Girder Line, typical Note: Not all Piers are shown on Foundation Plan. Repair/Replace exist. damaged Skirting ± 6'-5" " 0 - ' 1 " 8 - ' 5 " 0 - ' 1 " 8 - ' 7 Location of Existing Partitions above, typical 12" w. by min. 12" deep Poured Concrete Footing Beam, with 2-#5 bars cont. Align on center of Door. Construct new crawlspace access door 1 FOUNDATION PLAN Scale: 1/4" = 1'-0" 0 5 10 FT 3908 Avenue B, #309 Austin, Texas 78751 512|751-1374 NOT FOR CONSTRUCTION TERESA O'CONNELL #15432 T N E M P O L E V E D S D R B E V I F I K R A L P L I H P M E H 6 0 0 3 K R A P L L I H P M E H 6 0 0 3 5 0 7 8 7 S A X E T , N I T S U A ISSUE DATE PRINT: 3/3/22 SHEET NAME FOUNDATION PLAN SHEET NUMBER A-120 F I V E B I R D S D E V E L O P M E N T A U S T I N , T E X A S 7 8 7 0 5 7'-9" 47'-7" 11'-11" existing 20'-6 1/2" existing 6 1 A-301 5 4 13'-2" existing 7 2 A-301 8 KITCHEN DINING ROOM LIVING ROOM Align new Opening with Existing 4 3 4'-4 1/2" 1'-0" 1'-0" " 1 - ' 5 1 Stone Landing, 3' x 4' 2'-0" 2'-3" 2'-8" 8 1/2" 7 8 Laundry 5 3" S CO BACK HALL Align new Openings S CO 6 " 4 / 1 1 1 - ' 0 1 " 4 / 3 8 - ' 8 1 " 2 / 1 6 - ' 3 " 4 / 3 8 - ' 3 1 " 0 - ' 7 " 4 / 3 2 - ' 6 " 6 - ' 5 9 9 wetbar Existing Attic Pull-down Stair 1 New Electric Panel CLOSET 3'-0" 4'-11" 2'-0" 13 HALL 15 S CO shower 48"X 60" " 9 - ' 5 12 . S O L C T A O C S CO 14 3'-10" MASTER BEDROOM 10 11 MASTER BATH 16 BEDROOM " 2 / 1 7 - ' 7 " 2 / 1 3 - ' 9 2 " 2 / 1 4 - ' 3 " 0 - ' 4 " 4 - ' 3 " 2 / 1 2 - ' 5 " 2 / 1 5 - ' 5 3 2 1 " 8 - ' 1 3 g n i t s i x e New Brick Stoop See Dwg. A-501 " 8 " 4 - ' 6 " 8 " 1 - ' 5 1 9'-4 1/2" 7'-3 1/2" Equal Equal 2'-0" 2'-6 1/2" 4'-2 1/4" 10 16'-2" 11 12 6'-2 3/4" 9'-11 1/2" 55'-4" 6'-8 3/4" existing 13 13'-2" existing 1 FLOOR PLAN Scale: 1/4" = 1'-0" 0 5 10 FT 3908 Avenue B, #309 Austin, Texas 78751 512|751-1374 NOT FOR CONSTRUCTION TERESA O'CONNELL #15432 T N E M P O L E V E D S D R B E V I F I K R A L P L I H P M E H 6 0 0 3 K R A P L L I H P M E H 6 0 0 3 5 0 7 8 7 S A X E T , N I T S U A ISSUE DATE PRINT: 3/3/22 SHEET NAME FLOOR PLAN SHEET NUMBER A-121 M O D E L N U M B E R T R A D E N A M E P R O D U C T M A T E R I A L F I V E B I R D S D E V E L O P M E N T A U S T I N , T E X A S 7 8 7 0 5 New Marvin Casement Windows, with 4" wide Flat Exterior Casing and Drip Cap New Marvin Awning Window, with 4" wide Flat Exterior Casing and Drip Cap New Roof: Architectural Fiberglass Shingles over 15# Felt on 1/2" Plywood Sheathing, typical 6" Fascia Board with 1"x2" Shingle Mold and Drip Edge to match and align with existing Replace Flashings and repair all damage/decay at Existing Dormers 3908 Avenue B, #309 Austin, Texas 78751 512|751-1374 Existing Wood D/H Window, restore and refinish Proposed Porch at Front Door NOT FOR CONSTRUCTION TERESA O'CONNELL #15432 4'-2 1/2" 10 11 12 New Wood Siding, profile and coursing to match existing 13 Remove Rear Addition to top of slab, and Reconstruct as shown Marvin Awning windows, with 4" wide Flat Exterior Casings and Drip Cap, align window heads with existing Repair/Replace Existing skirting as necessary Construct New Crawlspace Access Door New Brick Stoop 2 SOUTH ELEVATION Scale: 1/4" = 1'-0" Repair Masonry at Chimney, Replace Flashings concurrent with Roof New Roof: Architectural Fiberglass Shingles over 15# Felt on 1/2" Plywood Sheathing, typical Repair all damage at existing Dormers, Replace Flashings and Roof, typ. for both Repair existing Wood Windows to remain, typ. Valley Flashing 1 Repair existing Wood Siding to remain, or Replace in kind to match existing ISSUE DATE PRINT: 3/3/22 1 2 3 Repair/Replace Skirting as necessary New Stoop and Porch – see detail drawings Repair existing Front Door and Transom to remain, Install New Door Hardware 1 EAST ELEVATION Scale: 1/4" = 1'-0" T N E M P O L E V E D S D R B E V I F I K R A L P L I H P M E H 6 0 0 3 K R A P L L I H P M E H 6 0 0 3 5 0 7 8 7 S A X E T , N I T S U A SHEET NAME ELEVATIONS SHEET NUMBER A-201 F I V E B I R D S D E V E L O P M E N T A U S T I N , T E X A S 7 8 7 0 5 Existing Chimney, Inspect and Repair Masonry and Flashings as necessary Existing Wood D/H Window, restore and refinish New Roof: Architectural Fiberglass Shingles over 15# Felt on 1/2" Plywood Sheathing, typical Replace Flashings and repair all damage/decay at Existing Dormers 12 10 Proposed Porch at Front Door Copper Rain Diverter Door Hood, refer Detail 6" Fascia Board with 1"x2" Shingle Mold and Drip Edge to match and align with existing Remove Rear Addition to top of slab, and Reconstruct as shown Door Hood, refer Detail 3908 Avenue B, #309 Austin, Texas 78751 512|751-1374 NOT FOR CONSTRUCTION TERESA O'CONNELL #15432 4 5 6 7 Repair/Replace Existing skirting as necessary Remove and Replace all Decayed and Damaged Siding and Framing, with new material to match original, typical New door to Mudroom, with 4" wide Flat Casing and Drip Cap to match 7 NOTE: REVISE GRADE PER PLANS 2 NORTH ELEVATION Scale: 1/4" = 1'-0" New Roof: Architectural Fiberglass Shingles over 15# Felt on 1/2" Plywood Sheathing, typical 6" Fascia Board with 1"x2" Shingle Mold and Drip Edge to match and align with existing Roof Rafter Roof Sheathing 2x4 Each Side, Spike to Rafter Copper Rain Diverter 8 " m i n . 3 " 3 1 / 2 " 5/4 Matched Boards, below Sheathing Shingle Mold 4" nom. Fascia ±1'-11 1/2" Door Hood, refer Detail 1x matched Boards Existing Wood D/H Window, restore and refinish Remove and Replace all Decayed and Damaged Siding and Framing, with new material to match original, typical 8 9 9 Corner Boards to Match Existing ISSUE DATE PRINT: 3/3/22 3 DOOR HOOD DETAIL Scale: 1" = 1'-0" New Marvin Door and Window with 4" flat Casings and Drip Caps to match existing 1 WEST ELEVATION Scale: 1/4" = 1'-0" T N E M P O L E V E D S D R B E V I F I K R A L P L I H P M E H 6 0 0 3 K R A P L L I H P M E H 6 0 0 3 5 0 7 8 7 S A X E T , N I T S U A SHEET NAME NORTH & WEST ELEVATIONS SHEET NUMBER A-202 F I V E B I R D S D E V E L O P M E N T A U S T I N , T E X A S 7 8 7 0 5 1 A-301 2 A-301 3 A-301 2x6 Rafters at 16" O.C. Post down at Partition between closet /Master Bedroom LVL Hip Rafter 2x Sleeper (2)2x6 Header in Ceiling 2x6 Rafters at 16" O.C. Dining Room Kitchen Hall Laundry ± " 1 1 - ' 8 East Ext. Wall of Kitchen R-15 Batts between floor joists 3 PARTIAL SECTION Scale: 1/4" = 1'-0" 2 A-610 2 SECTION Scale: 1/4" = 1'-0" 2x6 Ceiling Joists at 16in. O.C. New 2x4 Stud Wall, with 1/2" APA rated structural sheathing, moisture & vapor barrier under wood siding to match existing Exist. Concrete Slab 4 6 ° Min. Angle of Braces 45° 2x6 Ceiling Joists at 16in. O.C. Bearing Partition: 2x4 studs at 16in. O.C., with cats at midpoint R-38 continuous Insulation Batts 3908 Avenue B, #309 Austin, Texas 78751 512|751-1374 NOT FOR CONSTRUCTION TERESA O'CONNELL #15432 T N E M P O L E V E D S D R B E V I F I K R A L P L I H P M E H 6 0 0 3 K R A P L L I H P M E H 6 0 0 3 5 0 7 8 7 S A X E T , N I T S U A ISSUE DATE PRINT: 3/3/22 SHEET NAME SECTIONS SHEET NUMBER A-301 ± 9'-7" ± 4'-10" ± 5'-0" ± 9'-6" 2x6 Purlins 12 7.4 2x4 Purlin braces at max. 48" OC R-38 continuous Insulation Batts Install continuous R-15 Batts between Joists in Crawlspace, with Tyvek Vapor Barrier attached to bottom of Joists with lath battens at 24"O.C. perpendicular to framing 1 SECTION Scale: 1/4" = 1'-0" Roof Pitch to match existing. Align top surface with existing Install Simpson H2.5A ties (or eq.) at top plate with new rafters Install R-15 Batts in all exterior walls opened in the course of the work Install Tyvek Vapor Barrier between new siding and new sheathing F I V E B I R D S D E V E L O P M E N T A U S T I N , T E X A S 7 8 7 0 5 1 A-502 12 4.5 3 A-502 6 inch Fascia – Align with Existing ± " 2 / 1 6 4'-4" ± 2 A-502 New Wood Bench, each side. Ref. Details sheet A-502 5 A-502 2 A-502 Patch Siding where Light is removed Restore Existing Door, Transom and Trim to Remain 6" " 4 / 3 1 - ' 8 New Brick Stoop 7'-0" 6'-3 1/2" Brick Edge to Walkway 7'-8" 2 ENTRY PORCH DETAIL Scale: 1" = 1'-0" 1 FRONT ENTRY DETAIL Scale: 1" = 1'-0" 3908 Avenue B, #309 Austin, Texas 78751 512|751-1374 NOT FOR CONSTRUCTION TERESA O'CONNELL #15432 T N E M P O L E V E D S D R B E V I F I K R A L P L I H P M E H 6 0 0 3 K R A P L L I H P M E H 6 0 0 3 5 0 7 8 7 S A X E T , N I T S U A ISSUE DATE PRINT: 3/3/22 SHEET NAME FRONT PORCH DETAILS SHEET NUMBER A-501 F I V E B I R D S D E V E L O P M E N T A U S T I N , T E X A S 7 8 7 0 5 2x4 Rafters 2x4 Plate 3 A-502 Simpson H8 Rafter Ties, typ. 2x4 Rafters at 16" OC 2x4 Ceiling Joists 1/2" Plywood Sheathing 3908 Avenue B, #309 Austin, Texas 78751 512|751-1374 NOT FOR CONSTRUCTION TERESA O'CONNELL #15432 Bead Board Ceiling 1 1/2" Ø1 1/2" " 2 / 1 5 " 5 " 2 / 1 5 " 5 Shingle Mold to match & align with existing " 2 / 1 9 - ' 1 ± " 5 - ' 1 " 2 / 1 4 1'-2" 5 BENCH Scale: 1 1/2" = 1'-0" Bed Molding Blocking 1x6 1/4" reveal 2x4 Ceiling Joists Bead Board Ceiling 3/4" Cove 2x6's 3 PORCH EAVE Scale: 3" = 1'-0" 5/4" thk. Clear S4S, with Miter & Shoulder Joints at corners 4 A-502 Brick on Mortar Bed 4" Concrete Slab with 6x6, 10&10 WWF Reinf. Compacted Fill 8" CMU's, fill solid Brick Veneer " 6 Poured Concrete Footing, with (2x)-#5 bars 6" 2 POST DETAIL Scale: 3" = 1'-0" 4 BRICK STOOP DETAIL Scale: 2" = 1'-0" T N E M P O L E V E D S D R B E V I F I K R A L P L I H P M E H 6 0 0 3 K R A P L L I H P M E H 6 0 0 3 5 0 7 8 7 S A X E T , N I T S U A ISSUE DATE PRINT: 3/3/22 SHEET NAME FRONT PORCH DETAILS SHEET NUMBER A-502 1 SECTION PROPOSED PORCH Scale: 3/4" = 1'-0" F I V E B I R D S D E V E L O P M E N T A U S T I N , T E X A S 7 8 7 0 5 1/2" APA rated structural sheathing Fiberglass Roof Shingles as selected 15# Felt Double 2x4 Top Plate Fascia and Trim to Match Existing 2x4 Studs at 16 in O.C. 1/2" APA rated structural sheathing Moisture & Vapor Barrier Siding to match existing Adjust Birdsmouth cut as req'd to align roof with existing Gypsum Wall Board Continuous R-15 unfaced Batt Insulation 2 WALL SECTION Scale: 1" = 1'-0" Verify Existing Anchor Bolts: size, location and condition. Advise and consult with Architect for remedial work Pressure-Treated 2x4 plate over Termite Shield Existing Concrete Slab 3908 Avenue B, #309 Austin, Texas 78751 512|751-1374 NOT FOR CONSTRUCTION TERESA O'CONNELL #15432 T N E M P O L E V E D S D R B E V I F I K R A L P L I H P M E H 6 0 0 3 K R A P L L I H P M E H 6 0 0 3 5 0 7 8 7 S A X E T , N I T S U A ISSUE DATE PRINT: 3/3/22 SHEET NAME SCHEDULES, WALL SECTION & DETAILS SHEET NUMBER A-610 2x4 wall studs @16" O.C. Simpson STB2-50512 Anchor, as req'd., confer with Architect Exist. Conc. Slab, assumed 4" thk. 1 RETRO-FIT ANCHOR BOLTS Scale: 1 1/2" = 1'-0" No.LocationSash Opn'gConfig.LitesScope1Front Bedroom34"x 60"D/H6/6Existing: repair and refinish2Front Bedroom34"x 60"D/H6/6Existing: repair and refinish3Living Room34"x 60"(2x) D/H6/6-6/6Existing: repair and refinish4Living Room34"x 60"D/H6/6Existing: repair and refinish5Living Room34"x 60"D/H6/6Existing: repair and refinish6Dining Room24"-34"-24"x 60"(3x)D/H4/4-6/6-4/4Existing: repair and refinish7Kitchen34"x 60"(2x) D/H6/6-6/6Existing: repair and refinish8Kitchen34"x 48"D/HExisting: repair and refinish9Master Bedroom34"x 60"D/H6/6New: UWDH-G2 326010Master Bedroom34"x 30"(2x) Awningeach 6 liteNew: UWAWN 3632-211Master Bath30"x 21"(3x) Awningeach 4 liteNew: UWAWN 2032-312Bath #234"x 30"Awning6 liteNew: UWAWN 363213Front Bedroom34"x 60"(2x) D/H6/6-6/6Existing: repair and refinishWINDOW SCHEDULEFINISH SCHEDULERoom NameFloorBaseboardMaterialFinishMaterialHeightLiving RoomHardwoodGypsum Bd.Gypsum Bd.8'-10'Dining RoomHardwoodGypsum Bd.Gypsum Bd.8'-10'KitchenGypsum Bd.Gypsum Bd.8'-10'Back HallTileGypsum Bd.Gypsum Bd.8'-10'LaundryTileGypsum Bd.Gypsum Bd.8'-10'Master BedroomGypsum Bd.Gypsum Bd.8'-10'Master ClosetGypsum Bd.Gypsum Bd.8'-10'Master BathroomTileGypsum Bd.Gypsum Bd.8'-10'HallHardwoodGypsum Bd.Gypsum Bd.8'-10'Coat ClosetHardwoodGypsum Bd.Gypsum Bd.8'-10'BathTileGypsum Bd.Gypsum Bd.8'-10'Bedroom #2HardwoodGypsum Bd.Gypsum Bd.8'-10'ClosetHardwoodGypsum Bd.Gypsum Bd.8'-10'WallsCeilingNo.LocationTypeWidthScope1Front DoorSwing3'-0"Existing, refinish2Living RoomCased opening2'-8"New opening3Dining RoomCased opening5'-0"Existing4KitchenCased opening5'-0"New to match #35Back HallCased opening2'-8"New opening6Master BedroomSwing2'-8"New7Back DoorSwing3'-0"New8LaundryBi-fold2'-8"New9Master BedroomSwing3'-0"New10ClosetPocket2'-8"New11Master BathPocket2'-8"New12Water ClosetSwing2'-0"New13Coat ClosetSwing2'-8"14Bath #2Swing2'-6"Existing, refinish15Bedroom #2Swing2'-8"Existing, refinish16ClosetSwing2'-6"Existing, refinishSalvage existing door & frame in new openingDOOR SCHEDULEF I V E B I R D S D E V E L O P M E N T A U S T I N , T E X A S 7 8 7 0 5 Remove Roof and Roof Framing this Area - to line Remove Shingles for New Roof this portion Remove this portion to Slab 2 ROOF DEMOLITION PLAN Scale: 1/8" = 1'-0" 1 A-301 2 A-301 (2)2x6's 1 - 3 / 4 " x 9 - 1 / 2 " L V L H ip 1-3/4" x 9-1/2" LVL Hip g n i l i e c n i h s u l f L V L " 2 / 1 - 9 x " 2 / 1 - 3 3 A-301 s ' 6 x 2 ) 2 ( s ' 6 x 2 ) 2 ( 3 - 1 / 2 " x 1 1 - 1 / 4 " L V L H ip s ' 6 x 2 ) 2 ( 2 x 8 sle e p e r (2)2x6's Bearing Wall, typ. 4x4 Post 2x8 Ridge- align to Exist. 2x12 Hip Rafter Post from Header to Ridge/Hip intersection s ' 0 1 x 2 ) 2 ( 2x6 Roof Rafters @ 16" O.C., typical 4x4 Post in Window Mull (2)2x10's 2x Plate over Exist. 6" Ridge Board 2x6 Hip Rafter, ea. side 1 ROOF FRAMING PLAN Scale: 1/4" = 1'-0" 0 5 10 FT 3908 Avenue B, #309 Austin, Texas 78751 512|751-1374 NOT FOR CONSTRUCTION TERESA O'CONNELL #15432 T N E M P O L E V E D S D R B E V I F I K R A L P L I H P M E H 6 0 0 3 K R A P L L I H P M E H 6 0 0 3 5 0 7 8 7 S A X E T , N I T S U A ISSUE DATE PRINT: 3/3/22 SHEET NAME ROOF DEMO, & FRAMING SHEET NUMBER AS-120 F I V E B I R D S D E V E L O P M E N T A U S T I N , T E X A S 7 8 7 0 5 BWL 7'-9" BWL 26'-0" 21'-7" BWL " 0 - ' 2 BWL BWL Existing Braced Wall Line New Braced Wall Line CS-WSP Continuously Sheathed Wood Structural Panel: min. 7/16th's APA rated structural sheathing is applied to all sheathable surfaces along the braced wall line, including areas above and below openings, and at walls too short to be considered braced wall panels. APA rated structural sheathing panels shall be fastened with 6d common nails at 6" O.C. at edges and 12" O.C. in the field. Gypsum wall board of 1/2" min. thickness shall be installed on the interior of braced wall lines. GB Gypsum Board braced Wall Line: min. 1/2" Gypsum Board each side, fastened at 7" O.C. along the edges and 7" O.C. in the field with app'v'd fasteners as per table R702.3.5 4'-4" CS-WSP " 5 - ' 5 GB " 4 - ' 1 " 0 1 - ' 5 1 " 0 1 - ' 5 1 BWL BWL Edge of Panel Nailing 3908 Avenue B, #309 Austin, Texas 78751 512|751-1374 NOT FOR CONSTRUCTION TERESA O'CONNELL #15432 T N E M P O L E V E D S D R B E V I F I K R A L P L I H P M E H 6 0 0 3 K R A P L L I H P M E H 6 0 0 3 5 0 7 8 7 S A X E T , N I T S U A ISSUE DATE PRINT: 3/3/22 SHEET NAME BRACED WALL FRAMING SHEET NUMBER AS-121 " 2 - ' 4 CS-WSP CS-WSP 6'-3 1/2" Top Plate Corner Lap Stud-to-Stud/Abutting Corner Studs Vertical Joints of Sheathing shall occur over Studs. Horizontal Joints in Braced Wall Panel Sheathing shall be backed with 2x Blocking Edge of Panel Nailing 2 BRACED WALL PLAN Scale: 3/16" = 1'-0" LS24 Strap with (9)-10d nails in blocking and Header Double Top Plate with Edge Panel Nailing Header (2x)2x6 minimum, with Edge Nailing Double King Studs with Trimmer Stud, each side of openings, Sheathing with Edge Panel nailing Bottom Plate with Edge of Panel Nailing LS24 Strap with (9)-10d nails in blocking and Header Anchor Bolts TYPICAL SHEARWALL FRAMING 1 F I V E B I R D S D E V E L O P M E N T A U S T I N , T E X A S 7 8 7 0 5 3908 Avenue B, #309 Austin, Texas 78751 512|751-1374 NOT FOR CONSTRUCTION TERESA O'CONNELL #15432 T N E M P O L E V E D S D R B E V I F I K R A L P L I H P M E H 6 0 0 3 K R A P L L I H P M E H 6 0 0 3 5 0 7 8 7 S A X E T , N I T S U A ISSUE DATE PRINT: 3/3/22 SHEET NAME FRAMING NOTES SHEET NUMBER AS-122 OUTLINE SPECIFICATIONS AND GENERAL NOTES 1. Contractor shall verify all job and field conditions affecting work, and obtain all dimensions to ensure the proper strength, fit and location of the work. Report, in writing, to the Architect any conditions which may interfere with or otherwise affect, or prevent, the proper execution and completion of the work. Do not scale the drawings, any discrepancies shall be reported, in writing to the Architect for clarification. 2. All construction shall comply fully with the applicable provisions of the International Residen-tial Code for One and Two-Family Dwellings, 2021 Edition and all applicable local codes. All requirements specified in the code shall be adhered to as if they were called for, or shown, on the drawings. This shall not be construed to mean that any requirements set forth on the drawings may be modified because they are more stringent than the code requirements or because they are not specifically required by code. 3. Contractor shall provide all the necessary support, bracing, shoring, etc., (temporary and/or permanent) as required for the safe installation of new construction. DESIGN LOADS A. DEAD Loads include the self-weight of the structural members and all permanent superim-posed loads. Permanent superimposed loads include the following: 1. Ceiling and Mechanical at Roof 5 PSF 2. Ceiling and Mechanical at Floors 5 PSF 3. Roof(Architectural roof system and roof insulation) 8 PSF B. LIVE loads include the following uniformly distributed loads or concentrated loads, which-ever produces the greater load effects: Residential- Single/Two Family Dwellings UNIFORM CONCENTRATED 1. Uninhabitable Attics no storage 10 N/A 2. Uninhabitable Attics with Storage 20 N/A 3. Habitable Attics & Sleeping Areas 30 N/A 4. All other areas except balconies 40 N/A 5. Roof 12 to 20 N/A C. SNOW Loads 1. Ground Snow Load, Pg 5 PSF D. WIND Loads 1. Wind Lateral Load on structural frame is based on ASCE 7-10 using the following Design Criteria: a. Basic Wind Speed Vult 105 MPH b. Exposure Category B c. Internal Pressure Coefficient, Gcpi +/-0.18 d. Risk Category II FOUNDATION AND CONCRETE 1. All concrete shall be in accordance with ACI Building Code 7. Details and General provisions, for concrete construction, shall conform to the requirements of the latest ACI Buildings Code, ACI 318, and Manual ACI 315. 2. Concrete Mix Schedule: Concrete Class Strength PSI Agg. Type Agg. Size Slump (inches) Max W/C A 3000 NWT 1-1/2" 5-7 — NWT refers to Normal Weight Concrete with an air dry unit weight of ±145 PCF (ASTM C33 aggregate) Strength is the required compressive cylinder strength at 28 days. W/C ratio shall be as necessary to meet the required minimum strength. 3. Concrete exposed to weather shall be air entrained. 4. Footings shall bear a minimum of 1'-0" into undisturbed soil with a minimum allowable bear-ing capacity of two (2) tons per square foot minimum all in accordance with IRC. Exterior footings shall be 1'-0" minimum below finished grade. 5. Rod reinforcement shall be intermediate grade deformed bars, conforming to ASTM A615-60; reinforcement shall conform to ASTM A185 and A82. Reinforcing Steel clear cover shall be minimum 3" in footings and 2" in sides and tops of Sono-tubes. UNIT MASONRY All concrete masonry units shall conform to the Specifications, for hollow load bearing con-crete block masonry units ASTM C-90, and shall be hollow load bearing concrete block ma-sonry units grade N. All masonry units shall have a minimum compressive strength of 1000 PSI. Mortar shall conform to the Specifications for mortar, for unit masonry ASTM C-270 and shall be type N mortar. All concrete masonry unit walls to be laid up in running bond. Mortar to be type S or N and joints to be 3/8" thick tooled concave joints, full mortar bedding. Hori-zontal joint reinforcing to be truss type every second course. ENGINEERED LUMBER 1. All engineered lumber shall be either Laminated Veneer Lumber (LVL) or Parallel Strand Lum-ber (PSL) as shown on the drawings with the following properties. LVL Em= 1.9 x 106 lb/in2 Fb= 2600 lb/ft2 PSL Em= 2.0 x 106 lb/in2 Fb= 2900 lb/ft2 2. Engineered Lumber headers and girders shall not be cut or notched. Where multiple member units are indicated on the drawings, they shall be nailed together with minimum three (3) rows of 16d nails at 12” o.c. unless otherwise noted. 3. Installation shall conform to manufacturer’s standard details. Provide all backer blocks, filler blocks, web stiffeners, and hangers as required. Provide minimum 3 1/2” bearing length at ends of LVL or PSL girders. Where engineered lumber girders bear on steel columns, the col-umns shall have steel bearing caps of adequate size to provide full bearing beneath the girders. CARPENTRY 1. Termite protection shall be provided complying with the requirements of §R-318 of the IRC. Soil poisoning shall conform to Health Department and all applicable standards installed by licensed applicator. 2. All wall bearing beams to have standard angles, anchors and bearing plates, unless otherwise noted. All wood posts, resting on top of concrete walls, shall have clip angle anchorage to concrete base. All Posts, resting on top of steel beams, shall have clip angles bolted or welded to the flanges of the steel beam. 3. All structural framing lumber shall be #2 or better SOUTHERN YELLOW PINE or DOUG-FIR, un-less otherwise noted on the drawings, and/or shown, with SPF utility shoes and plates, stud grade FPF. Wood headers, Beams and Top Plates shall be #2 or better SOUTHERN YELLOW PINE or DOUG-FIR. 4. All roof and wall plywood panels shall be exterior CDX grade, with exterior glue, shall meet the requirements of the latest edition of the U.S. Products Standard PS-1, and shall be identified with the appropriate grade trademark of the American Plywood Association. All Plywood sub-floor panels shall be of same as above, and shall meet the requirements of the latest edition of the U.S. Product Standard PS-l, and shall be identified with the appropriate grade trademark of the American Plywood Association. 5. All exterior exposed posts, girders and joists shall be wood pressure treated in accordance with the requirements of the current AWPA Standards U2, Use Category UC3B for water-borne preservative treatment. All wood must be labeled certifying conformance to requirements. Wood structural members in contact with masonry, or concrete, must be preservative treated in accordance with the requirements of the current AWPA Standards C-1 and C-2 for oil-borne chemical preservative treatment. Bearing plates, and moisture barrier, shall be provided be-tween wood members and wall. 6. All lumber and connections shall be in accordance with the Wood Frame Construction Manual for One- and Two-Family Dwellings (WFCM) and with the National Design Specifications for Stress Graded Lumber and its fastenings. Lumber is to be furnished and installed, complete with all fastenings, anchors, blocking, bridging, saddles, hangers, etc. required to complete the job. All steel bolts connecting wood members shall be supplied with and tightened against steel washers or plates. Joist hangers and connectors, steel bridging and other special con-nections and hardware must be installed in accordance with WFCM requirements. Where fasteners are not specifically indicated or specified they shall be furnished in adequate number and size. 7. All carpentry work shall be performed in concordance with good trade practice, recommen-dations of manufacturers' and in conformance with the WFCM and these Specifications. ! Fasten securely all parts of carpentry work in their proper place, brace, plumb and level all members and secure with sufficient nails, spikes and bolts to insure rigidity. ! Nail lapped joists over any bearing together with two 10d nails, secure butted joists with 1 inch wide by 18 inch metal straps and two 8d nails to each joist. ! Provide solid surfaces at least 1-1/4 inches wide, in both directions, at all corners for securing sub-flooring, drywall, etc. Form surfaces with framing members, or with 2-inch wood blocking secured at least two 8d nails at each end. ! Floor trusses and joists shall be doubled under partitions parallel to trusses & joists. Pro-vide, at least, double joists or trusses, and headers, at water closet drain bends, and at all vent and mechanical openings 2' or more in width, unless otherwise shown on the draw-ings. ! Tail joists, over 4 feet long, and header joists shall be hung in approved metal stirrups, or hangers, and spiked securely unless supported on a wall or girder. ! All studs shall be provided and secured to supporting members in strict accordance with WFCM and as noted herein: " Secure sole plates with 16d nails 15" O.C. through sub-flooring and into framing or blocking, and provide suitable splice plate at end, securely nailed in place. " Studs not less than 2 x 4 16" O.C. doubled around openings and tripled at corners. " Plates and blocking same width as related studs or wider. " Framing to suit work of other trades. " Provide (2) 2 x 4 studs at the ends of beams unless otherwise noted on drawings. " Provide solid bearing for full width of trusses, rafters, girders, etc.. ! Sub-flooring shall be installed with face grain across supports; glued and nailed with 6d common nails 6 inches O.C. along supported edges and 10 inches O.C. at intermediate supports; break joints in adjacent courses; locate end joints over supports and drive nails flush or slightly below surface. Underlayment, where required, shall be similarly installed. ! Roof sheathing, shall be laid with face grain at right angles to supports; locate end joints over supports; stagger joints. ! Furring, where required, shall be true to line, not over 16" O.C. and fastened securely. 8. Provide wood bridging (7' -0" on center maximum spacing) for all wood joists and solid bridg-ing between joists at bearing on wood stud bearing walls. Secure bottom of bridging after sub-floor has been nailed. 9. Where rafters and joists frame, into other wood beams, provide galvanized steel Joist Hang-ers of Type“LU” as manufactured by the SIMPSON Strong-Tie Co. or equal. Hangers shall be sized and installed in accordance with the manufacturers' recommendations for the size of the member supported. 10. Provide fireblocking as per IRC §R302.11 requirements. 11. Insulation in all exterior frame walls shall be fiberglass type, and thickness as shown on draw-ings. Insulation shall be in roof, ceilings living space and at unheated to heated spaces. 12. All lumber shall be protected from the weather with a tarpaulin or heavy gauge plastic. All wood material shall be stock piled on wood dunnage, In a relatively flat dry area. The same protection shall be provided during shipping and installation. All material to be installed as per manufacturer's recommendations and specifications. 13. Blind flash all junctions where vertical meets horizontal (roof, chimneys, windows, doors, etc.) Skylights to be double insulated, self flashing with curb. 14. All interior partitions shall be 2" x 4" wood studs 16" on center with 1/2" gypsum board, unless otherwise shown on drawings. FINISHES 1. All glazing at glass doors, entrance sidelights, tub and shower enclosures and other hazardous locations shall comply with the requirements of IRC §R308. Safety glazing to be identified. 2. All partitions, exterior walls and ceilings, will be covered with 1/2" thick gypsum wall board, Moisture resistant gypsum wall board to be used at bathrooms and other "wet" areas with cementious backer board, Durock or equal, under all tile and marble. Fastener Schedule as per IRC Table R602.3(1)Descrip(on of Framing Elements No. and Type of fastenerSpacing and Loca(onJoist to sill or girder 4-8d boxToe Nail3-8d common3-10d boxTop or Bo<om Plate to Stud3-16d boxToe Nail4-8d box3-16d boxEnd Nail2-16d common3-10d boxStud to Bo<om Plate3-8d or 2-16dToe NailStud to Stud16d common24” o.c. face nailBo<om plate to joist, rim joist, band joist or blocking , not at braced wall panels16d common16” o.c. face nail16d box12” o.c. face nailBo<om Plate to Joist, rim joist, band joist or blocking, at Braced Wall Panels3-16d box16” o.c. face nail2-16d commonTop Plate to Top Plate16d common16” o.c. face nailDouble Top Plate splice8-16d commonFace nail on each side of end joint – minimum 24’ lap splice length each side of end joint12-16d box12-10d boxRim Joist, band joist or blocking to sill or top plate, toe nail8d box4” o.c. Toe Nail8d common6” o.c. toe Nail10d boxTop plates, laps at corners and intersecQons2-16d common Face nail3-10d boxBuilt-up header, 2 pieces with 1/2” spacer16d common16” o.c. along each edge face nail16d box12” o.c. along each edge face nailStud to Stud and abuSng corner Studs at braced wall lines16d box12” o.c. face nail16d common16” o.c. face nailBuilt-up girders and beams, 2” lumber layers10d boxEach Layer at 24” o.c., top and bo<om staggered, with 3-10d box nails at ends and splicesBlocking between joists or raVers to top plate3-8d commonToe Nail4-8d box3-10d commonCeiling Joists, laps over parQQons4-10d boxFace nail3-16d commonCeiling Joists to parallel raVers, 5:12 Pitch, RaVers 16”o.c.6-16d commonRoof Spans to 36 V., Live Load of 20 psfCeiling Joists to parallel raVers, 7:12 Pitch, RaVers 16”o.c.5-16d commonRoof Spans to 36 V., Live Load of 20 psfCeiling Joists to parallel raVers, 9:12 Pitch, RaVers 16”o.c.4-16d commonRoof Spans to 36 V., Live Load of 20 psfCeiling Joists to parallel raVers, 12:12 Pitch, RaVers 16”o.c.3-16d commonRoof Spans to 36 V., Live Load of 20 psfRaVer to Plate3-16d box2 toe nails on one side and 1 toe nail on the opposite side of each raVer3-10d common4-10d boxRoof RaVers to Ridge, valley or hip raVers4-16d boxToe Nail3-10d common4-10d boxRoof RaVers to Ridge, valley or hip raVers3-16d boxEnd Nail2-16d common3-10d boxCollar Ties to RaVers, face nail3-10d commonFace nail each raVer4-10d box1/2” Plywood subfloor, wall and roof sheathing to framing members8d common12” o.c. field 6” o.c. along panel edges 4” o.c. at gable end wall framing5/8” Plywood subfloor, wall and roof sheathing to framing members10d common12” o.c. field 6” o.c. along panel edges 4” o.c. at gable end wall framingNote: This schedule has been condensed from tables R602.3(1) through R602.3(4) and R802.5.2(1)of the IRC showing only the most common framing connecQons. ConnecQons not shown here, should be consulted in the tables of the IRC, chapters 6 & 8.1F I V E B I R D S D E V E L O P M E N T A U S T I N , T E X A S 7 8 7 0 5