A.1.2 - 3009 Bowman Avenue - Lead paint report — original pdf
Backup
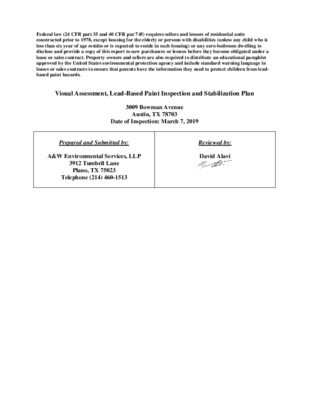
Federal law (24 CFR part 35 and 40 CFR par 745) requires sellers and lessors of residential units constructed prior to 1978, except housing for the elderly or persons with disabilities (unless any child who is less than six year of age resides or is expected to reside in such housing) or any zero-bedroom dwelling to disclose and provide a copy of this report to new purchasers or lessees before they become obligated under a lease or sales contract. Property owners and sellers are also required to distribute an educational pamphlet approved by the United States environmental protection agency and include standard warning language in leases or sales contracts to ensure that parents have the information they need to protect children from lead- based paint hazards. Visual Assessment, Lead-Based Paint Inspection and Stabilization Plan 3009 Bowman Avenue Austin, TX 78703 Date of Inspection: March 7, 2019 Prepared and Submitted by: A&W Environmental Services, LLP 3912 Tumbril Lane Plano, TX 75023 Telephone (214) 460-1513 Reviewed by: David Alavi TABLE OF CONTENTS I II Cover Letter Executive Summary III Scope of Inspection A. Building Background E. Inspection Company B. Preface C. Training D. Equipment F. Methods G. Findings H. Conclusions V XRF Results VI License/Certification VII Drawings/Floor Plans IX Glossary I. Paint Stabilization Recommendations and Cost Estimate IV Disclosure Responsibility and Disclaimer VIII XRF Performance Characteristic Sheets (PCS) Sheets Lead-Based Paint Inspection Report for March 7, 2019 Re: Single Family Property Located at: 3009 Bowman Avenue Austin, TX 78703 Dear Client: Please find enclosed the lead inspection report for the single-family home located at 3009 Bowman Avenue, Austin, TX 78703. The XRF survey was performed within the current acceptable industry guidelines, Housing and Urban Development (HUD) Guidelines Chapter 7 (revised 1997) and Texas regulations. During a visual assessment of the property A&W Environmental Services, LLP (License number: 2110404, Expiration date: February 17, 2020), observed that deteriorated paint was present at the property. In association with those findings, we performed a Lead-Based Paint (LBP) Inspection and have determined that all surfaces containing lead-based paint are intact and hence no stabilization plan is required. A&W Environmental Services, LLP used a Niton XLP300A X-Ray fluorescence (XRF) serial# 12249 with a Cd-109 sourced on August 2014 to sample paint for lead based paint at the property. Licensed Texas Lead Risk Assessor, Mohammad Alavi (License number: 2070687 - Expiration date: December 12, 2020) performed the inspection. If you have any questions or concerns regarding this report, please feel free to contact us at (214) 460-1513. Sincerely, Mo Alavi Project Manager A. Building Background II Scope of Inspection The property located at 3009 Bowman Avenue, Austin, TX 78703 is a single-family home (one unit). A&W Environmental Services, LLP was authorized by the client to perform lead-based paint testing of the above referenced single-family home to determine the possible presence, condition, location and amount of lead paint. The testing was conducted on March 7, 2019. B. Preface C. Training All inspectors utilized by A&W Environmental Services, LLP have EPA/State licensure and are licensed Lead Risk Assessors, or Inspectors who have passed the “HUD Visual Assessment Course”. All technicians utilized by A&W Environmental Services, LLP have also been trained in the use, calibration and maintenance of the X-Ray Fluorescence (XRF) equipment they currently use, along with necessary principles of Radiation Safety. A Niton XLP300A X-Ray fluorescence (XRF) lead paint analyzer, serial # 12249, was used on this job. The inspection was performed by an inspector employed by A&W Environmental services, LLP, 3912 Tumbril Lane, Plano, TX 75023, telephone Number (214) 460-1513. D. Equipment E. Inspection Company F. Methods The calibration of the NITON XLP 300 X-Ray fluorescence (XRF) is done in accordance with the Performance Characteristic Sheet (PCS) for this instrument. These XRF instruments are calibrated using a calibration standard block of known lead content. Three calibration readings are taken before and after each property is tested to insure manufacturer’s standards are met. If the inspection is longer than 4 hours, a set of 3 calibration readings must be taken before the 4 hours expires, and then an additional three calibration readings taken at the end of the inspection. If for any reason the instruments are not maintaining a consistent calibration reading within the manufacturer’s standards for performance on the calibration block supplied by the manufacturer, manufacturer’s recommendations are used to bring the instrument into calibration. If the instrument cannot be brought back into calibration, it is taken off the site and sent back to the manufacturer for repair and/or re-calibration. G. Findings 3009 Bowman Avenue Austin, TX 78703 Summary and Distribution Table Reading Room Number Side Component Substrate Color Condition DOOR DOOR JAMB DOOR FRAME WINDOW SASH WINDOW CASING WINDOW SILL WINDOW CASING WINDOW SILL DOOR JAMB DOOR FRAME BASEBOARD WOOD WOOD WOOD WOOD WOOD WOOD WOOD WOOD WOOD WOOD WOOD WHITE WHITE WHITE WHITE WHITE WHITE WHITE WHITE WHITE WHITE WHITE WHITE CEILING DRYWALL INTACT INTACT INTACT INTACT INTACT INTACT INTACT INTACT INTACT INTACT INTACT INTACT Lead Conc. (mg/cm2) 1 14.5 1.9 1 1.1 2.1 1 2.8 2.7 1 3.4 1.3 XRF 56 57 58 65 66 67 90 98 99 101 102 136 Interior Components A A A C C C B B A A A SHOP 3 SHOP 3 SHOP 3 BATH 4 BATH 4 BATH 4 BEDROOM 6 (LOLA) BEDROOM 6 (LOLA) BEDROOM 6 (LOLA) BEDROOM 6 (LOLA) BEDROOM 6 (LOLA) KITCHEN 9 Inaccessible Areas INTERIOR/EXTERIOR INACCESSIBLE AREAS TABLE Location Component Reason not tested or not accessible/Notes None Number of Positives12Total number of Readings146Percent Positive8.22% H. Conclusions The components listed in Section 3.4 were found “positive” for lead, as defined by the EPA and HUD as containing lead in concentrations equal to or greater than 1.0 mg/cm2. All surfaces containing lead-based paint are intact and hence do not require a stabilization plan. According to Chapter 7 HUD guidelines (Second Edition, July 2012), if one testing combination (i.e. window, door) is positive for lead in an interior or exterior room equivalent, then all other similar testing combinations in those areas are also assumed to be positive for lead. Likewise, the same is true for negative readings. All inaccessible areas are assumed to be positive, even though they were not tested. Any inaccessible areas encountered during the LBP evaluation are noted in Section 3.2. Given that the lead evaluation results indicated the presence of lead-based paint, the prospective owner may wish to obtain, at the prospective owner’s expense, additional services of a lead-based paint risk assessor, certified for the State in which the property is located, to help understand the positive results. This person would review the report provided by the M & M and might re- in question and/or additional areas and might make additional evaluate any area(s) recommendations about lead hazard control actions. If there were a small number of results with positive lead-based paint, the prospective owner may wish to obtain additional services from a lead-based paint risk assessor to help explain how to address the limited number of positive findings in developing the paint stabilization plan that would result in the reduction of hazards. This evaluation was completed in accordance with Lead Safe Housing Rule 24 CFR Part 35 subpart F as amended (2004). The sampling results are presented in Appendix A and notes are presented in Appendix B. The outline of dwelling is drafted in Appendix C. Appendix D contains photographs of the property. Appendix E contains the personal certifications of the inspector. Appendix F contains the PCS sheets for the XRF instrument and Appendix G contains a glossary of terms. HUD, for whom this report is prepared, has the option to evaluate the quality of this LBP inspection and visual assessment per Chapter 7 of the HUD guidelines (Second Edition, July 2012). These evaluation methods can include direct observation, immediate provision of results, repeated testing, and time-and-motion analysis. Those components which were found to contain LBP, and which were in intact condition should be monitored by the owner of the dwelling. In addition, some painted surfaces may contain levels of lead below 1.0 mg/cm2; these components could create lead dust or lead-contaminated soil hazards if the paint is turned into dust by abrasion, scraping, sanding or friction. If conditions of intact paint surfaces become destabilized, these conditions will need to be addressed in the future. If any construction or modernization work is done on the premises, this report should be given to the contractors, as well as to any future tenants. In compliance with HUD’s Final Rule, potential hazards resulting from LBP must be subjected to corrective action to stabilize all deteriorated LBP in housing built before 1978, unless the property is exempt. Paint stabilization repairs any defect in the substrate and/or in building components that are causing the paint deterioration, removes all loose paint and other material from the surface to be treated utilizing lead-safe work practices, and, in most cases, applies a new protective coating or paint. Any stabilization/construction activities which affect the existing paint films (including sanding and demolition) must be initiated by workers who have received proper training in the handling of lead-contaminated materials. Upon completion of paint stabilization activities, HUD requires a clearance examination to determine that the paint stabilization efforts were performed adequately. A clearance examination will include a visual assessment of all surfaces that were determined to be defective during the initial evaluation, and collection of dust and soil composite samples. It should be determined that the deteriorated paint surfaces have been eliminated and that no settled dust hazards or paint chips exist in the interior or exterior. The clearance report must be signed by a Certified/Licensed Lead Inspector or Risk Assessor. The HUD housing management company will determine whether lead hazard reduction will be performed at the property. DISCLOSURE RESPONSIBILITY A copy of this report must be provided to new lessees (tenants) and purchasers of this property under Federal Law (24 CFR part 35 and 40 CFR part 745) before they become obligated under a lease or sales contract. The complete report must also be provided to new purchasers and it must be made available to new tenants. Landlords (lessors) and sellers are also required to distribute an educational pamphlet and include standard warning language in their leases or sales contracts to ensure that children and pregnant women are protected from LBP hazards. The Occupational Safety and Health Administration (OSHA) Lead in Construction Standard states that “negative” readings (i.e. those below the HUD/EPA definition of what constitutes LBP [1.0 mg/cm2]) do not relieve contractors from performing exposure assessments (personal air monitoring) on their employees per the OSHA Lead Standard and should not be interpreted as lead free. Although a reading may indicate “negative”, airborne lead concentrations still may exceed the OSHA Action Level or the OSHA Permissible Exposure Limit (PEL) depending on the work activity. DISCLAIMER This is our report of a visual survey, and X-Ray Fluorescence (XRF) analysis of the readily accessible areas of this building and tested component. The presence or absence of LBP or LBP hazards applies only to the tested or assessed surfaces on the date of the field visit and it should be understood that conditions may change due to deterioration or maintenance. The results and material conditions noted within this report were accurate at the time of the evaluation and in no way reflect the conditions at the property after the date of the evaluation. No other environmental concerns or conditions were addressed during this evaluation. Paint Stabilization Recommendations and Cost Estimate 3009 Bowman Avenue, Austin, TX 78703 A&W Environmental Services, LLP recommends no remedial action at this time. IV DISCLOSURE RESPONSIBILITY AND DISCLAIMER Disclosure Responsibility Disclaimer A copy of this report must be provided to new lessees (tenants) and purchasers of this property under Federal Law (24 CFR part 35 and 40 CFR part 745) before they become obligated under a lease or sales contract. The complete report must also be provided to new purchasers and it must be made available to new tenants. Landlords (lessors) and sellers are also required to distribute an educational pamphlet and include standard warning language in their leases or sales contracts to ensure that parents have the information they need to protect their children from lead-based paint hazards. This is our report of a visual survey, and X-Ray Fluorescence (XRF) analysis of the readily accessible areas of this building and tested component. The presence or absence of lead-based paint or lead-based paint hazards applies only to the tested or assessed surfaces on the date of the field visit and it should be understood that conditions noted within this report were accurate at the time of the inspection and in no way, reflect the conditions at the property after the date of the inspection. Reading Number Room Location Address Room Number Side Structure Substrate Color Condition Sq. Ft. PbC Result INTERIOR INTERIOR INTERIOR INTERIOR INTERIOR INTERIOR INTERIOR INTERIOR INTERIOR INTERIOR INTERIOR INTERIOR INTERIOR INTERIOR INTERIOR INTERIOR INTERIOR INTERIOR INTERIOR INTERIOR INTERIOR INTERIOR INTERIOR INTERIOR INTERIOR INTERIOR 1 2 3 4 5 6 7 8 9 10 11 12 13 14 15 16 17 18 19 20 21 22 23 24 25 26 27 28 29 3009 BOWMAN, AUSTIN, TX 3009 BOWMAN, AUSTIN, TX 3009 BOWMAN, AUSTIN, TX 3009 BOWMAN, AUSTIN, TX 3009 BOWMAN, AUSTIN, TX 3009 BOWMAN, AUSTIN, TX 3009 BOWMAN, AUSTIN, TX 3009 BOWMAN, AUSTIN, TX 3009 BOWMAN, AUSTIN, TX 3009 BOWMAN, AUSTIN, TX 3009 BOWMAN, AUSTIN, TX 3009 BOWMAN, AUSTIN, TX 3009 BOWMAN, AUSTIN, TX 3009 BOWMAN, AUSTIN, TX 3009 BOWMAN, AUSTIN, TX 3009 BOWMAN, AUSTIN, TX 3009 BOWMAN, AUSTIN, TX 3009 BOWMAN, AUSTIN, TX 3009 BOWMAN, AUSTIN, TX 3009 BOWMAN, AUSTIN, TX 3009 BOWMAN, AUSTIN, TX 3009 BOWMAN, AUSTIN, TX 3009 BOWMAN, AUSTIN, TX 3009 BOWMAN, AUSTIN, TX 3009 BOWMAN, AUSTIN, TX 3009 BOWMAN, AUSTIN, TX 3009 BOWMAN, AUSTIN, TX 3009 BOWMAN, AUSTIN, TX 3009 BOWMAN, AUSTIN, TX V: XRF Results CALIBRATE CALIBRATE CALIBRATE A B C D D D D C C C C C D D B B B A B C D A A A CEILING WALL WALL WALL WALL FIRE PLACE DOOR JAMB DOOR FRAME CHAIR RAIL BASEBOARD WINDOW SASH WINDOW CASING WINDOW SILL DOOR JAMB DOOR FRAME DOOR DOOR JAMB DOOR FRAME CEILING WALL WALL WALL WALL CROWN MOLDING BASEBOARD WINDOW SASH LIVING 1 LIVING 1 LIVING 1 LIVING 1 LIVING 1 LIVING 1 LIVING 1 LIVING 1 LIVING 1 LIVING 1 LIVING 1 LIVING 1 LIVING 1 LIVING 1 LIVING 1 LIVING 1 LIVING 1 LIVING 1 BEDROOM 2 BEDROOM 2 BEDROOM 2 BEDROOM 2 BEDROOM 2 BEDROOM 2 BEDROOM 2 BEDROOM 2 DRYWALL DRYWALL DRYWALL DRYWALL DRYWALL DRYWALL WOOD WOOD WOOD WOOD WOOD WOOD WOOD WOOD WOOD WOOD WOOD WOOD DRYWALL DRYWALL DRYWALL DRYWALL DRYWALL WOOD WOOD WOOD WHITE WHITE WHITE WHITE WHITE WHITE WHITE WHITE WHITE WHITE WHITE WHITE WHITE WHITE WHITE WHITE WHITE WHITE WHITE WHITE WHITE WHITE WHITE WHITE WHITE WHITE INTACT INTACT INTACT INTACT INTACT INTACT INTACT INTACT INTACT INTACT DETERIORATED DETERIORATED DETERIORATED INTACT INTACT INTACT INTACT INTACT INTACT INTACT INTACT INTACT INTACT INTACT INTACT INTACT 1 1.1 1 0 0 0 0.05 0 0.17 0.13 0.01 0 0.4 0.4 0.28 0.5 0 0.09 0.05 0.2 0.3 0 0 0 0 0.06 0 0.3 0.17 Positive Positive Positive Negative Negative Negative Negative Negative Negative Negative Negative Negative Negative Negative Negative Negative Negative Negative Negative Negative Negative Negative Negative Negative Negative Negative Negative Negative Negative Address Room Number Side Structure Substrate Color Condition Sq. Ft. PbC Result Reading Number 30 31 32 33 34 35 36 37 38 39 40 41 42 43 44 45 46 47 48 49 50 51 52 53 54 55 56 57 58 59 60 61 62 Room Location INTERIOR INTERIOR INTERIOR INTERIOR INTERIOR INTERIOR INTERIOR INTERIOR INTERIOR INTERIOR INTERIOR INTERIOR INTERIOR INTERIOR INTERIOR INTERIOR INTERIOR INTERIOR INTERIOR INTERIOR INTERIOR INTERIOR INTERIOR INTERIOR INTERIOR INTERIOR INTERIOR INTERIOR INTERIOR INTERIOR INTERIOR INTERIOR INTERIOR 3009 BOWMAN, AUSTIN, TX 3009 BOWMAN, AUSTIN, TX 3009 BOWMAN, AUSTIN, TX 3009 BOWMAN, AUSTIN, TX 3009 BOWMAN, AUSTIN, TX 3009 BOWMAN, AUSTIN, TX 3009 BOWMAN, AUSTIN, TX 3009 BOWMAN, AUSTIN, TX 3009 BOWMAN, AUSTIN, TX 3009 BOWMAN, AUSTIN, TX 3009 BOWMAN, AUSTIN, TX 3009 BOWMAN, AUSTIN, TX 3009 BOWMAN, AUSTIN, TX 3009 BOWMAN, AUSTIN, TX 3009 BOWMAN, AUSTIN, TX 3009 BOWMAN, AUSTIN, TX 3009 BOWMAN, AUSTIN, TX 3009 BOWMAN, AUSTIN, TX 3009 BOWMAN, AUSTIN, TX 3009 BOWMAN, AUSTIN, TX 3009 BOWMAN, AUSTIN, TX 3009 BOWMAN, AUSTIN, TX 3009 BOWMAN, AUSTIN, TX 3009 BOWMAN, AUSTIN, TX 3009 BOWMAN, AUSTIN, TX 3009 BOWMAN, AUSTIN, TX 3009 BOWMAN, AUSTIN, TX 3009 BOWMAN, AUSTIN, TX 3009 BOWMAN, AUSTIN, TX 3009 BOWMAN, AUSTIN, TX 3009 BOWMAN, AUSTIN, TX 3009 BOWMAN, AUSTIN, TX 3009 BOWMAN, AUSTIN, TX BEDROOM 2 BEDROOM 2 BEDROOM 2 BEDROOM 2 BEDROOM 2 BEDROOM 2 BEDROOM 2 BEDROOM 2 BEDROOM 2 BEDROOM 2 SHOP 3 SHOP 3 SHOP 3 SHOP 3 SHOP 3 SHOP 3 SHOP 3 SHOP 3 SHOP 3 SHOP 3 SHOP 3 SHOP 3 SHOP 3 SHOP 3 SHOP 3 SHOP 3 SHOP 3 SHOP 3 SHOP 3 BATH 4 BATH 4 BATH 4 BATH 4 A A A A A D D D D D A B C D B B B B B B B D D D D A A A A B C WINDOW CASING WINDOW SILL CLOSET DOOR CLOSET DR JAMB CLOSET DR FRAME DOOR JAMB DOOR FRAME DOOR DOOR JAMB DOOR FRAME CEILING WALL WALL WALL WALL BASEBOARD WINDOW SASH WINDOW CASING WINDOW SILL CROWN MOLDING CLOSET DR JAMB CLOSET DR FRAME DOOR DOOR JAMB DOOR FRAME THRESHOLD DOOR DOOR JAMB DOOR FRAME CEILING WALL WALL WALL WOOD WOOD WOOD WOOD WOOD WOOD WOOD WOOD WOOD WOOD DRYWALL WOOD WOOD WOOD WOOD WOOD WOOD WOOD WOOD WOOD WOOD WOOD WOOD WOOD WOOD WOOD WOOD WOOD WOOD DRYWALL DRYWALL DRYWALL DRYWALL WHITE WHITE WHITE WHITE WHITE WHITE WHITE WHITE WHITE WHITE LT BLUE WHITE WHITE WHITE WHITE WHITE WHITE WHITE WHITE WHITE WHITE WHITE WHITE WHITE WHITE WHITE WHITE WHITE WHITE WHITE WHITE WHITE WHITE INTACT INTACT INTACT INTACT INTACT INTACT INTACT INTACT INTACT INTACT INTACT INTACT INTACT INTACT INTACT INTACT INTACT INTACT INTACT INTACT INTACT INTACT INTACT INTACT INTACT INTACT INTACT INTACT INTACT INTACT INTACT INTACT INTACT 0.28 0.01 0.2 0.01 0.17 0.18 0.3 0.12 0.5 0.25 0 0 0.03 0 0.04 0.12 0 0 0.01 0 0.04 0.02 0 0 0.07 0.5 1 1.9 1 0 0 0.13 0 Negative Negative Negative Negative Negative Negative Negative Negative Negative Negative Negative Negative Negative Negative Negative Negative Negative Negative Negative Negative Negative Negative Negative Negative Negative Negative Positive Positive Positive Negative Negative Negative Negative Address Room Number Side Structure Substrate Color Condition Sq. Ft. PbC Result Reading Number 63 64 65 66 67 68 69 70 71 72 73 74 75 76 77 78 79 80 81 82 83 84 85 86 87 88 89 90 91 92 93 94 95 Room Location INTERIOR INTERIOR INTERIOR INTERIOR INTERIOR INTERIOR INTERIOR INTERIOR INTERIOR INTERIOR INTERIOR INTERIOR INTERIOR INTERIOR INTERIOR INTERIOR INTERIOR INTERIOR INTERIOR INTERIOR INTERIOR INTERIOR INTERIOR INTERIOR INTERIOR INTERIOR INTERIOR INTERIOR INTERIOR INTERIOR INTERIOR INTERIOR INTERIOR 3009 BOWMAN, AUSTIN, TX 3009 BOWMAN, AUSTIN, TX 3009 BOWMAN, AUSTIN, TX 3009 BOWMAN, AUSTIN, TX 3009 BOWMAN, AUSTIN, TX 3009 BOWMAN, AUSTIN, TX 3009 BOWMAN, AUSTIN, TX 3009 BOWMAN, AUSTIN, TX 3009 BOWMAN, AUSTIN, TX 3009 BOWMAN, AUSTIN, TX 3009 BOWMAN, AUSTIN, TX 3009 BOWMAN, AUSTIN, TX 3009 BOWMAN, AUSTIN, TX 3009 BOWMAN, AUSTIN, TX 3009 BOWMAN, AUSTIN, TX 3009 BOWMAN, AUSTIN, TX 3009 BOWMAN, AUSTIN, TX 3009 BOWMAN, AUSTIN, TX 3009 BOWMAN, AUSTIN, TX 3009 BOWMAN, AUSTIN, TX 3009 BOWMAN, AUSTIN, TX 3009 BOWMAN, AUSTIN, TX 3009 BOWMAN, AUSTIN, TX 3009 BOWMAN, AUSTIN, TX 3009 BOWMAN, AUSTIN, TX 3009 BOWMAN, AUSTIN, TX 3009 BOWMAN, AUSTIN, TX 3009 BOWMAN, AUSTIN, TX 3009 BOWMAN, AUSTIN, TX 3009 BOWMAN, AUSTIN, TX 3009 BOWMAN, AUSTIN, TX 3009 BOWMAN, AUSTIN, TX 3009 BOWMAN, AUSTIN, TX BATH 4 BATH 4 BATH 4 BATH 4 BATH 4 BATH 4 BATH 4 BATH 4 BATH 4 BATH 4 BATH 4 FAMILY 5 FAMILY 5 FAMILY 5 FAMILY 5 FAMILY 5 FAMILY 5 FAMILY 5 FAMILY 5 FAMILY 5 FAMILY 5 FAMILY 5 FAMILY 5 FAMILY 5 FAMILY 5 FAMILY 5 FAMILY 5 BEDROOM 6 (LOLA) BEDROOM 6 (LOLA) BEDROOM 6 (LOLA) BEDROOM 6 (LOLA) BEDROOM 6 (LOLA) BEDROOM 6 (LOLA) D C C C C C D D B B B A B C D A A A A A D D C C C C A B C D B WALL BASEBOARD WINDOW SASH WINDOW CASING WINDOW SILL CROWN MOLDING CABINET CABINET DOOR DOOR JAMB DOOR FRAME CEILING WALL WALL WALL WALL BASEBOARD WINDOW SASH WINDOW CASING WINDOW SILL CROWN MOLDING DOOR JAMB DOOR FRAME FIRE PLACE DOOR DOOR JAMB DOOR FRAME CEILING WALL WALL WALL WALL CHAIR RAIL DRYWALL WOOD WOOD WOOD WOOD WOOD WOOD WOOD WOOD WOOD WOOD DRYWALL DRYWALL DRYWALL DRYWALL WOOD WOOD WOOD WOOD WOOD WOOD WOOD WOOD WOOD WOOD WOOD WOOD DRYWALL DRYWALL DRYWALL DRYWALL DRYWALL WOOD WHITE WHITE WHITE WHITE WHITE WHITE WHITE WHITE WHITE WHITE WHITE OFF-WHITE WHITE WHITE WHITE WHITE WHITE WHITE WHITE WHITE WHITE WHITE WHITE WHITE WHITE WHITE WHITE WHITE WHITE WHITE WHITE WHITE WHITE INTACT INTACT INTACT INTACT INTACT INTACT INTACT INTACT INTACT INTACT INTACT INTACT INTACT INTACT INTACT INTACT INTACT INTACT DETERIORATED INTACT INTACT INTACT INTACT INTACT INTACT INTACT INTACT INTACT INTACT INTACT INTACT INTACT INTACT 0 0 1.1 2.1 1 0.04 0 0 0.19 0.17 0.1 0 0 0 0 0.01 0.4 0.1 0.22 0.23 0.12 0 0 0 0 0.07 0 14.5 0 0.03 0 0 0 Negative Negative Positive Positive Positive Negative Negative Negative Negative Negative Negative Negative Negative Negative Negative Negative Negative Negative Negative Negative Negative Negative Negative Negative Negative Negative Negative Positive Negative Negative Negative Negative Negative Address Room Number Side Structure Substrate Color Condition Sq. Ft. PbC Result Reading Number 96 97 98 99 100 101 102 103 104 105 106 107 108 109 110 111 112 113 114 115 116 117 118 119 120 121 122 123 124 125 126 127 128 Room Location INTERIOR INTERIOR INTERIOR INTERIOR INTERIOR INTERIOR INTERIOR INTERIOR INTERIOR INTERIOR INTERIOR INTERIOR INTERIOR INTERIOR INTERIOR INTERIOR INTERIOR INTERIOR INTERIOR INTERIOR INTERIOR INTERIOR INTERIOR INTERIOR INTERIOR INTERIOR INTERIOR INTERIOR INTERIOR INTERIOR INTERIOR INTERIOR INTERIOR 3009 BOWMAN, AUSTIN, TX 3009 BOWMAN, AUSTIN, TX 3009 BOWMAN, AUSTIN, TX 3009 BOWMAN, AUSTIN, TX 3009 BOWMAN, AUSTIN, TX 3009 BOWMAN, AUSTIN, TX 3009 BOWMAN, AUSTIN, TX 3009 BOWMAN, AUSTIN, TX 3009 BOWMAN, AUSTIN, TX 3009 BOWMAN, AUSTIN, TX 3009 BOWMAN, AUSTIN, TX 3009 BOWMAN, AUSTIN, TX 3009 BOWMAN, AUSTIN, TX 3009 BOWMAN, AUSTIN, TX 3009 BOWMAN, AUSTIN, TX 3009 BOWMAN, AUSTIN, TX 3009 BOWMAN, AUSTIN, TX 3009 BOWMAN, AUSTIN, TX 3009 BOWMAN, AUSTIN, TX 3009 BOWMAN, AUSTIN, TX 3009 BOWMAN, AUSTIN, TX 3009 BOWMAN, AUSTIN, TX 3009 BOWMAN, AUSTIN, TX 3009 BOWMAN, AUSTIN, TX 3009 BOWMAN, AUSTIN, TX 3009 BOWMAN, AUSTIN, TX 3009 BOWMAN, AUSTIN, TX 3009 BOWMAN, AUSTIN, TX 3009 BOWMAN, AUSTIN, TX 3009 BOWMAN, AUSTIN, TX 3009 BOWMAN, AUSTIN, TX 3009 BOWMAN, AUSTIN, TX 3009 BOWMAN, AUSTIN, TX BEDROOM 6 (LOLA) BEDROOM 6 (LOLA) BEDROOM 6 (LOLA) BEDROOM 6 (LOLA) BEDROOM 6 (LOLA) BEDROOM 6 (LOLA) BEDROOM 6 (LOLA) BATH 7 BATH 7 BATH 7 BATH 7 BATH 7 BATH 7 BATH 7 BATH 7 BATH 7 BATH 7 BATH 7 BATH 7 BATH 7 BATH 7 BATH 7 BATH 7 BATH 8 BATH 8 BATH 8 BATH 8 BATH 8 BATH 8 BATH 8 BATH 8 KITCHEN 9 KITCHEN 9 B B B B A A A A B C D B D D D C C C C C C C A B C D B B B A CROWN MOLDING WINDOW SASH WINDOW CASING WINDOW SILL DOOR DOOR JAMB DOOR FRAME CEILING WALL WALL WALL WALL CABINET DOOR DOOR JAMB DOOR FRAME BASEBOARD DOOR DOOR JAMB DOOR FRAME DOOR DOOR JAMB DOOR FRAME CEILING WALL WALL WALL WALL DOOR DOOR JAMB DOOR FRAME CEILING WALL WOOD WOOD WOOD WOOD WOOD WOOD WOOD DRYWALL DRYWALL DRYWALL DRYWALL DRYWALL WOOD WOOD WOOD WOOD WOOD WOOD WOOD WOOD WOOD WOOD WOOD DRYWALL WOOD WOOD WOOD WOOD WOOD WOOD WOOD DRYWALL DRYWALL WHITE WHITE WHITE WHITE WHITE WHITE WHITE WHITE WHITE WHITE WHITE WHITE WHITE WHITE WHITE WHITE WHITE WHITE WHITE WHITE WHITE WHITE WHITE WHITE WHITE WHITE WHITE WHITE WHITE WHITE WHITE WHITE WHITE INTACT INTACT INTACT INTACT INTACT INTACT INTACT INTACT INTACT INTACT INTACT INTACT INTACT INTACT INTACT INTACT INTACT INTACT INTACT INTACT INTACT INTACT INTACT INTACT INTACT INTACT INTACT INTACT INTACT INTACT INTACT INTACT INTACT 0 0.19 2.8 2.7 0 1 3.4 0 0 0 0 0 0.09 0 0 0 0 0.01 0.05 0 0 0.03 0 0.02 0 0.2 0 0 0 0.01 0 0 0.09 Negative Negative Positive Positive Negative Positive Positive Negative Negative Negative Negative Negative Negative Negative Negative Negative Negative Negative Negative Negative Negative Negative Negative Negative Negative Negative Negative Negative Negative Negative Negative Negative Negative Address Room Number Side Structure Substrate Color Condition Sq. Ft. PbC Result Reading Number 129 130 131 132 133 134 135 136 137 138 139 140 141 142 143 144 145 146 147 148 149 150 151 152 Room Location INTERIOR INTERIOR INTERIOR INTERIOR INTERIOR INTERIOR INTERIOR INTERIOR INTERIOR INTERIOR INTERIOR INTERIOR INTERIOR INTERIOR INTERIOR INTERIOR INTERIOR INTERIOR INTERIOR INTERIOR INTERIOR 3009 BOWMAN, AUSTIN, TX 3009 BOWMAN, AUSTIN, TX 3009 BOWMAN, AUSTIN, TX 3009 BOWMAN, AUSTIN, TX 3009 BOWMAN, AUSTIN, TX 3009 BOWMAN, AUSTIN, TX 3009 BOWMAN, AUSTIN, TX 3009 BOWMAN, AUSTIN, TX 3009 BOWMAN, AUSTIN, TX 3009 BOWMAN, AUSTIN, TX 3009 BOWMAN, AUSTIN, TX 3009 BOWMAN, AUSTIN, TX 3009 BOWMAN, AUSTIN, TX 3009 BOWMAN, AUSTIN, TX 3009 BOWMAN, AUSTIN, TX 3009 BOWMAN, AUSTIN, TX 3009 BOWMAN, AUSTIN, TX 3009 BOWMAN, AUSTIN, TX 3009 BOWMAN, AUSTIN, TX 3009 BOWMAN, AUSTIN, TX 3009 BOWMAN, AUSTIN, TX 3009 BOWMAN, AUSTIN, TX 3009 BOWMAN, AUSTIN, TX 3009 BOWMAN, AUSTIN, TX KITCHEN 9 KITCHEN 9 KITCHEN 9 KITCHEN 9 KITCHEN 9 KITCHEN 9 KITCHEN 9 KITCHEN 9 KITCHEN 9 KITCHEN 9 KITCHEN 9 KITCHEN 9 KITCHEN 9 KITCHEN 9 KITCHEN 9 KITCHEN 9 KITCHEN 9 KITCHEN 9 KITCHEN 9 KITCHEN 9 KITCHEN 9 B C D A A A A A A A A A B B D D A A A CALIBRATE CALIBRATE CALIBRATE WALL WALL WALL CROWN MOLDING WINDOW SASH WINDOW CASING WINDOW SILL BASEBOARD WINDOW CASING WINDOW SILL CABINET CABINET DOOR JAMB DOOR FRAME DOOR JAMB DOOR FRAME DOOR DOOR JAMB DOOR FRAME ATTIC ACCESS DOOR HEADER DRYWALL DRYWALL DRYWALL WOOD WOOD WOOD WOOD WOOD WOOD WOOD WOOD WOOD WOOD WOOD WOOD WOOD WOOD WOOD WOOD WOOD WOOD WHITE WHITE WHITE WHITE WHITE WHITE WHITE WHITE WHITE WHITE WHITE WHITE WHITE WHITE WHITE WHITE WHITE WHITE WHITE WHITE WHITE INTACT INTACT INTACT INTACT INTACT INTACT INTACT INTACT INTACT INTACT INTACT INTACT INTACT INTACT INTACT INTACT INTACT INTACT INTACT INTACT INTACT 0 0 0 0.01 0.05 0 0 1.3 0 0 0 0 0 0 0 0.09 0.01 0 0.02 0.01 0.03 1.1 1 1 Negative Negative Negative Negative Negative Negative Negative Positive Negative Negative Negative Negative Negative Negative Negative Negative Negative Negative Negative Negative Negative Positive Positive Positive Inspection Date: March 7, 2019 3009 Bowman Avenue Austin, TX 78703 Report Date: March 7, 2019 Abatement level: 1.0 Report No: 1 Total Readings: (146) Actionable (0) VI: License/Certification PERFORMANCE CHARACTERISTIC SHEETS Glossary Abatement: A measure or set of measures designed to permanently eliminate lead-based paint hazards or lead-based paint. Abatement strategies include the removal of lead-based paint, enclosure, encapsulation, replacement of building components coated with lead-based paint, removal of lead contaminated dust, and removal of lead contaminated soil or overlaying of soil with a durable covering such as asphalt (grass and sod are considered interim control measures). All of these strategies require preparation; cleanup; waste disposal; post-abatement clearance testing; recordkeeping; and, if applicable, monitoring. See also Complete abatement and Interim controls. Accreditation: A formal recognition certifying that an organization, such as a laboratory, is competent to carry out specific tasks or types of tests. Accuracy: The degree of agreement between an observed value and an accepted reference value (a “true” value); a data quality indicator. Accuracy includes a combination of random errors (precision) and systematic errors (bias) due to sampling and analysis. Bare soil: Soil not covered with grass, sod, some other similar vegetation, or paving, including the sand in sandboxes. Building component: Any element of a building that may be painted or have dust on its surface, e.g., walls, stair treads, floors, railings, doors, windowsills, etc. Certification: The process of testing and evaluating against certain specifications the competence of a person, organization, or other entity in performing a function or service, usually for a specified period of time. Certified: The designation for Contractors who have completed training and other requirements to safely allow them to undertake risk assessments, inspections, or abatement work. Risk assessors, inspectors, and Abatement Contractors should be certified by the appropriate local, State, or Federal agency. Chewable surface: See Chewed surface. Chewed surface: Any painted surface that shows evidence of having been chewed or mouthed by a young child. A chewed surface is usually a protruding, horizontal part of a building, such as an interior windowsill. Cleaning: The process of using a vacuum and wet cleaning agent to remove leaded dust; the process includes the removal of bulk debris from the work area. OSHA prohibits the use of compressed air to clean lead-contaminated dust from a surface. Clearance examination: Visual examination and collection of environmental samples by an inspector or risk assessor, or, in some circumstances, a Sampling Technician, and analysis by an accredited laboratory upon completion of an abatement project, interim control intervention, or maintenance job that disturbs lead-based paint (or paint suspected of being lead-based). The clearance examination is performed to ensure that lead exposure levels do not exceed standards established by the EPA Administrator pursuant to Title IV of the Toxic Substances Control Act, and that any cleaning following such work adequately meets those standards. Common area: A room or area that is accessible to all residents in a community (e.g., hallways or lobbies); in general, any area not kept locked. Composite sample: A single sample made up of individual subsamples. Analysis of a composite sample produces the arithmetic mean of all subsamples. Containment: A process to protect workers and the environment by controlling exposures to the lead contaminated dust and debris created during abatement. Deteriorated lead-based paint: Any lead-based paint coating on a damaged or deteriorated surface or fixture, or any interior or exterior lead-based paint that is peeling, chipping, blistering, flaking, worn, chalking, alligatoring, cracking, or otherwise becoming separated from the substrate. Disposal (of waste): The discharge, deposit, injection, dumping, spilling, leaking, or placement of solid or liquid waste on land or in water so that none of its constituents can pollute the environment by being emitted into the air or discharged into a body of water, including groundwater. Environmental Intervention Blood-Lead Level (EIBL) child: A child who has a blood lead level at or above 20 μg/dL (micrograms of lead per deciliter of blood) in a single test or at 15-19 μg/dL in two tests taken at least three months apart. Encapsulation: Any covering or coating that acts as a barrier between lead-based paint and the environment, the durability of which relies on adhesion and the integrity of the existing bonds between multiple layers of paint and between the paint and the substrate. See also Enclosure. Enclosure: The use of rigid, durable construction materials that are mechanically fastened to the substrate to act as a barrier between the Lead-based paint and the environment. Evaluation: Risk assessment, paint examination, or risk assessment screen. Examination: See Clearance examination. Federal Register (FR): A daily Federal publication that contains proposed and final regulations, rules, and notices. Impact surface: An interior or exterior surface (such as surfaces on doors) subject to damage by repeated impact or contact. Inspection (of paint): A surface-by-surface investigation to determine the presence of lead- based paint (in some cases including dust and soil sampling) and a report of the results. investigation, clearance reevaluation, inspection, Interim controls: A set of measures designed to temporarily reduce human exposure or possible exposure to lead-based paint hazards. Such measures include specialized cleaning, repairs, maintenance, painting, temporary containment, and management and resident education programs. Monitoring, conducted by Owners, and reevaluations, conducted by professionals, are integral elements of interim control. Interim controls include dust removal; paint film stabilization; treatment of friction and impact surfaces; installation of soil coverings, such as grass or sod; and land use controls. See also Monitoring, Reevaluation, and Abatement. Interior windowsill: The portion of the horizontal window ledge that protrudes into the interior of the room, adjacent to the window sashes when the window is closed; often called the window stool. Latex: A waterborne emulsion paint made with synthetic binders, such as 100 percent acrylic, vinyl acrylic, terpolymer, or styrene acrylic; a stable emulsion of polymers and pigment in water. Lead: Lead includes metallic lead and inorganic and organic compounds of lead. Lead-based paint: Any paint, varnish, shellac, or other coating that contains lead equal to or greater than 1.0 mg/cm2 (milligrams of lead per square centimeter of surface) as measured by XRF or laboratory analysis, or 0.5 percent by weight (5,000 μg/g, 5,000 ppm (parts per million), or 5,000 mg/kg) as measured by laboratory analysis. (Local definitions may vary.) Lead-based paint hazard: A condition in which exposure to lead from lead-contaminated dust, lead contaminated soil, or deteriorated lead-based paint would have an adverse effect on human health (as established by the EPA Administrator under Title IV of the Toxic Substances Control Act). Lead-based paint hazards include, for example, deteriorated lead-based paint, leaded dust levels above applicable standards, and bare leaded soil above applicable standards. Lead-based paint hazard control: Activities to control and eliminate lead-based paint hazards, including interim controls, abatement, and complete abatement. Lead-contaminated dust: Surface dust in residences that contain an area concentration of lead in excess of the standard established by the EPA Administrator, pursuant to Title IV of the Toxic Substances Control Act. EPA standards for leaded dust for risk assessments are 40 μg/ft2 (micrograms of lead per square foot) on floors and 250 μg/ft2 on interior windowsills. The EPA standards for clearance are 40 μg/ft2 on floors, 250 μg/ft2 on interior windowsills and 400 μg/ft2 on window troughs. The recommended standard for lead hazard screens for floors is 25 μg/ft2 and for windowsills is 125 μg/ft2. Lead-contaminated soil: Bare soil on residential property that contains lead in excess of the standard established by the EPA Administrator, pursuant to Title IV of the Toxic Substances Control Act. The standard is 400 μg/g in play areas and 1200 μg/g in the rest of the yard. Leaded dust: See Lead-contaminated dust. Licensed: Holding a valid license or certification issued by EPA or by an EPA-approved State program pursuant to Title IV of the Toxic Substances Control Act. The license is based on certification for lead-based paint hazard control work. See also Certified. Maintenance: Work intended to maintain adequate living conditions in a dwelling, which has the potential to disturb lead-based paint or paint that is suspected of being lead-based. Mean: The arithmetic average of a series of numerical data values; for example, the algebraic sum of the data values divided by the number of data values. Microgram (μg): 1/1,000,000 of a gram; used to measure weight. Monitoring: Surveillance to determine (1) that known or suspected lead-based paint is not deteriorating; (2) that lead-based paint hazard controls, such as paint stabilization, enclosure, or encapsulation have not failed; and (3) that structural problems do not threaten the integrity of hazard controls or of known or suspected. Owner: A person, firm, corporation, guardian, conservator, receiver, trustee, executor, government agency or entity, or other judicial officer who, alone or with others, owns, holds, or controls the freehold or leasehold title or part of the title to property, with or without actually possessing it. This definition includes a vendee who possesses the title, but does not include a mortgagee or an Owner of a reversionary interest under a ground rent lease. Paint inspector: An individual who has completed training from an accredited program and been licensed or certified by the appropriate State or local agency to (1) perform inspections to determine and report the presence of lead-based paint on a surface-by-surface basis through onsite testing, (2) report the findings of such an inspection, (3) collect environmental samples for laboratory analysis, (4) perform clearance testing, and optionally (5) document successful compliance with lead-based paint hazard control requirements or standards. Paint removal: An abatement strategy that entails the removal of lead-based paint from surfaces. For lead hazard control work, this can mean using chemicals, heat guns below 1,100° F, and certain contained abrasive methods. Open-flame burning, open-abrasive blasting, sandblasting, extensive dry scraping, and stripping in a poorly ventilated space using a volatile stripper are prohibited paint removal methods. Hydro blasting is not recommended. Plastic: See Polyethylene plastic. Polyethylene plastic: All references to polyethylene plastic refer to 6 mil plastic sheeting or polyethylene bags (or doubled bags if using 4 mil polyethylene bags), or any other thick plastic material shown to demonstrate at least equivalent dust containment performance. Plastic used to contain waste should be capable of completely containing the waste and, after being properly sealed, should remain leak tight with no visible signs of discharge during movement or relocation. Polyurethane: An exceptionally hard and wear-resistant coating (created by the reaction of polyols with a multifunctional isocyanate); often used to seal wood floors following lead-based paint hazard control work and cleaning. Reevaluation: In lead hazard control work, the combination of a visual assessment and collection of environmental samples performed by a certified risk assessor to determine if a previously implemented lead-based paint hazard control measure is still effective and if the dwelling remains lead-safe. Removal: See Paint removal. Renovation: Work that involves construction and/or home or building improvement measures such as window replacement, weatherization, remodeling, and repainting. Replacement: A strategy of abatement that entails the removal of building components coated with lead-based paint (such as windows, doors, and trim) and the installation of new components free of lead-based paint. Resident: A person who lives in a dwelling. Risk assessment: An onsite investigation of a residential dwelling to discover any lead-based paint hazards. Risk assessments include an investigation of the age, history, management, and maintenance of the dwelling, and the number of children under age 6 and women of childbearing age who are residents; a visual assessment; limited environmental sampling (i.e., collection of dust wipe samples, soil samples, and deteriorated paint samples); and preparation of a report identifying acceptable abatement and interim control strategies based on specific conditions. Risk assessor: A certified individual who has completed training with an accredited training program and who has been certified to (1) perform risk assessments, (2) identify acceptable abatement and interim control strategies for reducing identified lead-based paint hazards, (3) perform clearance testing and reevaluations, and (4) document the successful completion of lead- based paint hazard control activities. Site: The land or body of water where a facility is located, or an activity is conducted. The site includes adjacent land used in connection with the facility or activity. Soil: See Bare soil. Spectrum analyzer: A type of XRF analyzer that provides the operator with a plot of the energy and intensity, or counts of both K and L x-ray spectra, as well as a calculated lead concentration. See also XRF analyzer. Standard deviation: A measure of the precision of a reading; the spread of the deviation from the mean. The smaller the standard deviation, the more precise the analysis. The standard deviation is calculated by first obtaining the mean, or the arithmetic average, of all of the readings. A formula is then used to calculate how much the individual values vary from the mean—the standard deviation is the square root of the arithmetic average of the squares of the deviation from the mean. Many hand calculators have an automatic standard deviation function. See also Mean. Subsample: A representative portion of a sample. A subsample may be either a field sample or a laboratory sample. A subsample is often combined with other subsamples to produce a composite sample. See also Composite sample. Substrate: A surface on which paint, varnish, or other coating has been applied or may be applied. Examples of substrates include wood, plaster, metal, and drywall. Substrate effect: The radiation returned to an XRF analyzer by the paint, substrate, or underlying material, in addition to the radiation returned by any lead present. This radiation, when counted as lead x-rays by an XRF analyzer contributes to substrate equivalent lead (bias). The inspector may have to compensate for this effect when using XRF analyzers. See also XRF analyzer. Substrate Equivalent Lead (SEL): The XRF measurement taken on an unpainted surface; used to calculate the corrected lead concentration on a surface by using the following formula: Apparent Lead Concentration–Substrate Equivalent Lead = Corrected Lead Concentration. See also XRF analyzer. Target housing: Any residential unit constructed before 1978, except dwellings that do not contain bedrooms or dwellings that were developed specifically for the elderly or persons with disabilities—unless a child younger than 6 resides or is expected to reside in the dwelling. In the case of jurisdictions that banned the sale or use of lead-based paint before 1978, the Secretary of HUD may designate an earlier date for defining target housing. Test location: A specific area on a testing combination where XRF instruments will test for lead-based paint. Trained: Successful completion of a training course in a particular discipline. For lead hazard control work, the training course must be accredited by EPA or by an EPA-approved State program, pursuant to Title IV of the Toxic Substances Control Act. Treatment: In residential lead-based paint hazard control work, any method designed to control lead-based paint hazards. Treatment includes interim controls, abatement, and removal. Window trough: For a typical double-hung window, the portion of the exterior windowsill between the interior windowsill (or stool) and the frame of the storm window. If there is no storm window, the window trough is the area that receives both the upper and lower window sashes when they are both lowered. Sometimes inaccurately called the window “well.” Worker: An individual who has completed training in an accredited program to perform Lead- based paint hazard control in housing. Worksite: Any interior or exterior area where lead-based paint hazard control work takes place. XRF analyzer: An instrument that determines lead concentration in milligrams per square centimeter (mg/cm2) using the principle of x-ray fluorescence (XRF). Two types of field portable XRF analyzers are used — direct readers and spectrum analyzers. For this lead-based paint inspection, the term XRF analyzer only refers to portable instruments manufactured to analyze paint that have a HUD Performance Characteristic Sheet and are interpreted in accordance with the Performance Characteristic Sheet; it does not refer here to laboratory grade units or portable instruments designed to analyze soil.