D.4.1 - 201 W 30th St - Summary of Reports — original pdf
Backup
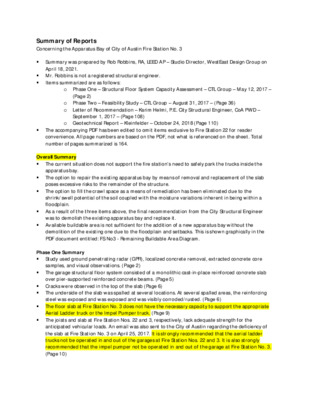
Summary of Reports Concerning the Apparatus Bay of City of Austin Fire Station No. 3 § § § § § § § § § § § Summary was prepared by Rob Robbins, RA, LEED AP – Studio Director, WestEast Design Group on April 18, 2021. § Mr. Robbins is not a registered structural engineer. § Items summarized are as follows: o Phase One – Structural Floor System Capacity Assessment – CTL Group – May 12, 2017 – (Page 2) o Phase Two – Feasibility Study – CTL Group – August 31, 2017 – (Page 36) o Letter of Recommendation – Karim Helmi, P.E. City Structural Engineer, CoA PWD – September 1, 2017 – (Page 108) o Geotechnical Report – Kleinfelder – October 24, 2018 (Page 110) The accompanying PDF has been edited to omit items exclusive to Fire Station 22 for reader convenience. All page numbers are based on the PDF, not what is referenced on the sheet. Total number of pages summarized is 164. Overall Summary § The current situation does not support the fire station’s need to safely park the trucks inside the apparatus bay. The option to repair the existing apparatus bay by means of removal and replacement of the slab poses excessive risks to the remainder of the structure. The option to fill the crawl space as a means of remediation has been eliminated due to the shrink/swell potential of the soil coupled with the moisture variations inherent in being within a floodplain. As a result of the three items above, the final recommendation from the City Structural Engineer was to demolish the existing apparatus bay and replace it. Available buildable area is not sufficient for the addition of a new apparatus bay without the demolition of the existing one due to the floodplain and setbacks. This is shown graphically in the PDF document entitled: FS No3 - Remaining Buildable Area Diagram. Phase One Summary § Study used ground penetrating radar (GPR), localized concrete removal, extracted concrete core samples, and visual observations. (Page 2) The garage structural floor system consisted of a monolithic cast-in-place reinforced concrete slab over pier-supported reinforced concrete beams. (Page 5) Cracks were observed in the top of the slab (Page 6) The underside of the slab was spalled at several locations. At several spalled areas, the reinforcing steel was exposed and was exposed and was visibly corroded/rusted. (Page 6) The floor slab at Fire Station No. 3 does not have the necessary capacity to support the appropriate Aerial Ladder truck or the Impel Pumper truck. (Page 9) The joists and slab at Fire Station Nos. 22 and 3, respectively, lack adequate strength for the anticipated vehicular loads. An email was also sent to the City of Austin regarding the deficiency of the slab at Fire Station No. 3 on April 25, 2017. It is strongly recommended that the aerial ladder trucks not be operated in and out of the garages at Fire Station Nos. 22 and 3. It is also strongly recommended that the impel pumper not be operated in and out of the garage at Fire Station No. 3. (Page 10) § Misalignment of the truck could cause a failure of the slab. As a safety precaution, this vehicle § § should no longer be parked in this fire station. (Page 10) The longitudinal cracking in the top of the slap at Fire Station No. 3 may have been caused by negative moment flexural cracking at the slab-to-beam interface, which is further evidence that the slab at this garage may have been overloaded. (Page 10) The observed cracking in the foundation walls adjacent to the north and south ends of the beams at Fire Station No. 3 are concerning. (Page 11) Phase Two Summary § Phase Two obtained additional core samples for compressive strength testing and carbonation depth testing. (Page 36) Phase Two evaluated the feasibility of various repair options. (Page 36) § § No discernible shear reinforcing was detected in the middle beams at Fire Station No. 3. (Page 37) § Carbonation is a reaction that converts the CH to calcium carbonate (CaCO3) which reduces the pH of the concrete and can lead to the depassivation of the steel. Depassivation of the steel allows corrosion to occur. Carbonation depth testing indicates that the bottom portion of the slab concrete in the garage areas at Fire Station No. 3 is significantly carbonated. The carbonation depths exceed the bottom concrete cover in the slab (i.e. distance from the underside of the slab to the surface of the bottom layer of reinforcing steel) (Page 38) Based on our analyses, various elements of both fire stations lack the necessary capacity to support the anticipated vehicular loads. The Demand Capacity Ratios (DCR) are shown in Table 4 below. A DCR greater than 1.0 indicates a strength deficiency. (Page 40) § § § § § The underside of the slab was spalled at several locations. At several spalled areas, the reinforcing steel was exposed and visibly corroded/rusted, likely indicative of carbonation-induced corrosion. Carbonation depth testing performed further confirms that carbonation is an issue of concern in the garage area at Fires Station No. 3. Due to the depth of carbonation, the future service life of the garage floor system could be limited. (Page 42) Considering the slab thickness, it would be difficult to repair existing areas of corroded reinforcing without the repair extending through the full depth of the slab. (Page 42) Preventing future carbonation-induced corrosion would add considerable cost to any repair/strengthening program. (Page 42) The slab and middle beams at Fire Station No. 3 are considerably deficient with respect to supporting the anticipated vehicular loads as shown in Table 4 above in this summary. The slab is overloaded by nearly 150% in flexure. The middle beams are overloaded by nearly 300% in shear and nearly 100% in flexure. Due to the degree to which the slab and middle beams are overloaded in conjunction with the presence of carbonation-induced corrosion, we do not believe the repair/strengthening of the garage floor system at Fire Station No. 3 can be accomplished in a cost- effective manner without substantial replacement of framing elements. (Page 42) Two options were considered: § o Remove and replace large portions of the existing floor system. This will require the removal of the slab and middle beams in the garage area. The west beam, perimeter foundation walls, and columns can likely remain in place. A new monolithic slab/beam system would be designed and constructed such that it would tie into these existing elements. o Fill the crawlspace beneath the garage area with a cementitious flowable fill material. The existing garage floor system at Fire Station No. 3 would remain in place and the crawlspace area beneath the garage would be filled with a cementitious flowable fill material. In this scenario, the garage floor system would generally function as a slab-on- grade type system. The slab and middle beams would no longer be suspended, and as a result the strength deficiencies in these elements would no longer be a concern. This is likely the fastest and least disruptive remedy. However, depending on the soil characteristics at the subject site, this option may not be possible. Specifically expansive soil is common in the Austin area. The void underneath the slab systems provides protection against differential soil movement due to moisture variations in the soil. Filling the void beneath the slab could compromise this protection. Geotechnical borings and a soil evaluation would be needed to determine the precise characteristics of the foundation subgrade. (Page 42) Letter of Recommendation Summary § The existing elevated foundations for Fire Station 3 and Fire Station 22 are not capable of safely supporting the higher loads of the new fire trucks. (Page 108) Three options were considered: § o Remove large portions of the existing foundation and replace with a new foundation that is designed to support the new loads. This is costly due to accessing and demolishing the existing foundation without damaging the remaining structure. There is a high risk associated with this recommendation. o Replacing the entire bay area. The new bay design will address the current new vehicular loads of the fire Station and could be planned and implemented in a manner to fulfill the future needs of the Austin Fire Department. o Fill the crawlspace with flowable fill material. Fire Station is located in an area that has expansive soils, this is why the existing foundation system is suspended. Additional geotechnical investigation will be required to determine if adding the additional load of the flowable material will cause the soil to settle and create a void between the bottom of the existing foundation and the flowable fill. The soils can then rebound pushing upward against the bottom of the existing foundation causing it to move upward. (Page 108) § It is recommended that selective demolition be performed and replace the entire bays of fire station 3 and Fire Station 22. (Page 109) Geotechnical Report Summary § Geotechnical report drilled and sampled 2 borings to a depth of approximately 45 feet below grade and 1 boring to a depth of 50 feet below grade. Hand-augered one boring south of the existing bay building to a depth of 5 feet below grade. (Page 114) § § § § The site of FS #3 is situated within an outcropping of the Austin Chalk Formation. The Austin Chalk formation typically consists of clays overlaying chalky limestone. The thickness of the clay above the limestone varies but is generally encountered at a shallow depth. The upper portions of the limestone are generally weathered, fractured, and very light brown to light yellow brown in color. Some zones of severely weathered limestone that are clay-like can be present above the weathered material. The underlying primary limestone is generally harder than the weathered limestone and is light to medium gray in color. The boring at FS #3 indicates the presence of moderate to high plasticity clay of depths varying from 26 to 28 feet. The clay overlays light gray limestone to the boring termination depth of approximately 50 feet below grade. (Page 119) An estimate of the potential vertical movement (PVM) is summarized below in Table 4.1. (Page 121) The high plasticity clay soils remain stable with constant moisture contents; however a change in the moisture content will cause the soil to swell or shrink thereby potentially causing movement and damage in the overlaying structure. (Page 125) It is our understanding that the proposed bay reconstruction project includes structurally suspended floor slabs and crawl space. Based on this, potential shrink/swell movements associated with the near-surface highly-plastic clays should not affect the performance of the selected bay floor system. The crawl space will provide the necessary separation between the slab and soil movements associated with shrink/swell behavior. Similarly, structurally suspended grade beams will be isolated from soil movements by the crawl space. (Page 126)