ITEM10 C15-2025-0015 ADV PACKET MAY12 — original pdf
Backup
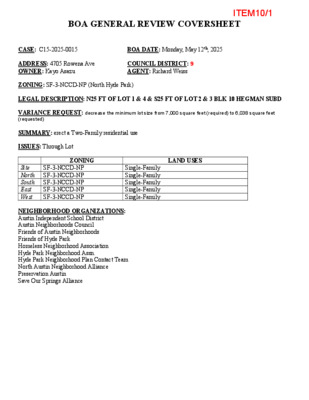
BOA GENERAL REVIEW COVERSHEET CASE: C15-2025-0015 BOA DATE: Monday, May 12th, 2025 ADDRESS: 4705 Rowena Ave OWNER: Kayo Asazu COUNCIL DISTRICT: 9 AGENT: Richard Weiss ZONING: SF-3-NCCD-NP (North Hyde Park) LEGAL DESCRIPTION: N25 FT OF LOT 1 & 4 & S25 FT OF LOT 2 & 3 BLK 10 HEGMAN SUBD VARIANCE REQUEST: decrease the minimum lot size from 7,000 square feet (required) to 6,038 square feet (requested) SUMMARY: erect a Two-Family residential use ISSUES: Through Lot ZONING LAND USES Site North South East West SF-3-NCCD-NP SF-3-NCCD-NP SF-3-NCCD-NP SF-3-NCCD-NP SF-3-NCCD-NP Single-Family Single-Family Single-Family Single-Family Single-Family NEIGHBORHOOD ORGANIZATIONS: Austin Independent School District Austin Neighborhoods Council Friends of Austin Neighborhoods Friends of Hyde Park Homeless Neighborhood Association Hyde Park Neighborhood Assn. Hyde Park Neighborhood Plan Contact Team North Austin Neighborhood Alliance Preservation Austin Save Our Springs Alliance ITEM10/1April 30, 2025 Richard Weiss 4705 Rowena Ave Austin TX, 78751 Property Description: N25 FT OF LOT 1 & 4 & S25 FT OF LOT 2 & 3 BLK 10 HEGMAN SUBD Re: C15-2025-0015 Dear Richard, Austin Energy (AE) has reviewed your application for the above referenced property, requesting that the Board of Adjustment consider a variance request from LDC Section 25-2-774 at 4705 Rowena Ave Austin Energy does not oppose the request, provided that any proposed or existing improvements follow Austin Energy’s Clearance & Safety Criteria, the National Electric Safety Code, and OSHA requirements. Any removal or relocation of existing facilities will be at the owner’s/applicant’s expense. Please use this link to be advised of our clearance and safety requirements which are additional conditions of the above review action: https://library.municode.com/tx/austin/codes/utilities_criteria_manual?nodeId=S1AUENDECR_1 .10.0CLSARE If you require further information or have any questions regarding the above comments, please contact our office. Thank you for contacting Austin Energy. Ashley Robinson, Project Assistant Infrastructure Support Services | Austin Energy 4815 Mueller Blvd Austin, TX 78723 Ashley.robinson@austinenergy.com ITEM10/2ITEM10/3Portion of the City of Austin Land Development Code applicant is seeking a variance from: 20050818-064 PART 7. 4. A TWO FAMILY RESIDENTIAL OR DUPLEX USE IS PERMITTED ____________________________________________________________________________ ON A LOT THAT IS 7000 SF OR LARGER. We would like to request to amend 7,000 s.f. to ____________________________________________________________________________ 6,038 sf (the size of the lot according to the survey). 7,000 sf previously aligned with 25-2-774 ____________________________________________________________________________ TWO FAMILY RESIDENTIAL USE (B), which now states that two family residential or duplex ____________________________________________________________________________ use is permitted on a lot that is 7000 sf (5750) sf or larger Section 2: Variance Findings The Board must determine the existence of, sufficiency of, and weight of evidence supporting the findings described below. Therefore, you must complete each of the applicable Findings Statements as part of your application. Failure to do so may result in your application being rejected as incomplete. Please attach any additional supporting documents. NOTE: The Board cannot grant a variance that would provide the applicant with a special privilege not enjoyed by others similarly situated or potentially similarly situated. I contend that my entitlement to the requested variance is based on the following findings: Reasonable Use The zoning regulations applicable to the property do not allow for a reasonable use because: The current lot does not allow reasonable use based on the surrounding lots because it is one ____________________________________________________________________________ of only 7 mid-block lots that face 2 public streets front and back and it is one of only 2 lots in the ____________________________________________________________________________ neighborhood with this condition that does not either have the square footage for 2 unit ____________________________________________________________________________ residential or already has 2 units despite not meeting the square footage requirement. We are ____________________________________________________________________________ requesting the ability to match the footprint of the existing garage and add a loft unit above that ____________________________________________________________________________ will be 440sf - the adjacent garage to the south has a similar condition with a second story over the garage, and the one of the properties to the north is a smaller lot with a detached garage ____________________________________________________________________________ that has a 2nd story loft (window, bathroom and unit # but not permitted as a 2nd unit) ____________________________________________________________________________ Hardship a) The hardship for which the variance is requested is unique to the property in that: THIS PROPERTY IS UNIQUE BECAUSE IT IS ONE OF ONLY 2 MID BLOCK PROPERTIES ____________________________________________________________________________ THAT FACE ROWENA ON THE WEST SIDE AND AVENUE F ON THE EAST SIDE AND DO ____________________________________________________________________________ NOT HAVE A 2 FAMILY ENTITLEMENT. BOTH ARE RESIDNTIAL STREETS THAT SHOULD ____________________________________________________________________________ HAVE HOUSES FORNTING THE STREET. THE GARAGE WAS EXISITNG WHEN THE ____________________________________________________________________________ PROPERTY WAS BUILT AND THE REQUEST IS TO BUILD OVER THE EXISTING GARAGE ____________________________________________________________________________ AND ONLY INCREAS THE BUILDING ENVELOPE WITH A SET OF EXTERIOR STAIRS b) The hardship is not general to the area in which the property is located because: THIS IS ONE OF ONLY 7 LOTS IN THE NCCD THAT FACE 2 RESIDENTAIL STREETS ON ____________________________________________________________________________ THE FRONT AND BACK. 3 HAVE BEEN SUBDIVIDED IN TO MICRO LOTS WITH 2 ____________________________________________________________________________ HOUSES. 1 HAS 2 UNITS BUT DOES NOT MEET THE SF REQUIREMENT. WHEN THE ____________________________________________________________________________ HOUSE WAS PURCHASED IN 2014 THE HOUSE AND GARAGE WERE EXSTING. THE ____________________________________________________________________________ HEIGHT OF THE GARAGE WITH THE APARTMENT ABOVE WILL BE NO TALLER AT THE ____________________________________________________________________________ PEAK THAN NEIGHBORING HOUSES/ GARAGES City of Austin | Board of Adjustment General/Parking Variance Application (cid:21)(cid:18)(cid:28)(cid:18)(cid:21)(cid:21) | Page 5 of 8 ITEM10/4Area Character The variance will not alter the character of the area adjacent to the property, will not impair the use of adjacent conforming property, and will not impair the purpose of the regulations of the zoning district in which the property is located because: THERE ARE SEVERAL DUPLEXES AND 2 FAMILY RESIDENTIAL UNITS VISIBLE FROM ____________________________________________________________________________ THE PROPERTY. THE ADJACENT HOUSE TO THE NORTH HAS A GARAGE W/ A ____________________________________________________________________________ BATHROOM & "STORAGE" LOFT ABOVE THAT IS SIMILAR IN CHARACTER TO WHAT IS ____________________________________________________________________________ BEING PROPOSED. THE ADDITON WILL SIT WITHIN THE FOOTPRINT ABOVE THE ____________________________________________________________________________ EXISTING GARAGE & THE ONLY CHANGE TO IMP. COVER WILL BE THE ADDITION OF A ____________________________________________________________________________ 35SF STAIR. THE ADJACENT HOUSE TO THE SOUTH HAS A GARAGE W/ A SECOND STORY THAT MATCHES THE EXACT CHARACTER OF WHAT IS BEING PROPOSED. ____________________________________________________________________________ Parking (additional criteria for parking variances only) Request for a parking variance requires the Board to make additional findings. The Board may grant a variance to a regulation prescribed in the City of Austin Land Development Code Chapter 25-6, Appendix A with respect to the number of off-street parking spaces or loading facilities required if it makes findings of fact that the following additional circumstances also apply: 1. Neither present nor anticipated future traffic volumes generated by the use of the site or the uses of sites in the vicinity reasonably require strict or literal interpretation and enforcement of the specific regulation because: ____________________________________________________________________________ ____________________________________________________________________________ ____________________________________________________________________________ ____________________________________________________________________________ 2. The granting of this variance will not result in the parking or loading of vehicles on public streets in such a manner as to interfere with the free flow of traffic of the streets because: ____________________________________________________________________________ ____________________________________________________________________________ ____________________________________________________________________________ ____________________________________________________________________________ 3. The granting of this variance will not create a safety hazard or any other condition inconsistent with the objectives of this Ordinance because: ____________________________________________________________________________ ____________________________________________________________________________ ____________________________________________________________________________ ____________________________________________________________________________ 4. The variance will run with the use or uses to which it pertains and shall not run with the site because: ____________________________________________________________________________ ____________________________________________________________________________ ____________________________________________________________________________ ____________________________________________________________________________ City of Austin | Board of Adjustment General/Parking Variance Application (cid:21)(cid:18)(cid:28)(cid:18)(cid:21)(cid:21) | Page 6 of 8 ITEM10/5ITEM10/6/ / / / / / // // // PLANTER PLANTER PLANTER / / / / / / / / / / / / / / / / / / / / / / / / / / / / / / / / / / / / / / / / / / / / / / / / / / / / / / / / / / / / / / / / / / / / / / / / / / / / / / / / / / / / / / / / / / / / / / ' 2 3 . 0 2 1 W " 5 0 6 4 ° 9 7 N ' ) ' 0 0 . 0 2 1 ( (50.00') N 10°11'55"E 49.99' UL UL UL UL UL UL UL CONC. APRON UL UL UL // // // // // // // // // // // // / / / / / / / / / / // / / // 10' B.L. [1] / / / / / / // // // // / / / / / / / / / / . C N O C // / / // . C N O C . C N O C 21.3' // 75.0414 // 2 1 . 2 ' WOOD DECK UNCOVERED CONC. PAVERS PLANTER WOOD DECK COVERED 27.4' 3 . 5 ' 7.8' 1 8 . 2 ' ] 1 [ . L . B ' 5 4.1' 2 7 . 7 ' 2 9 . 6 ' 4.1' ] 1 [ . L . B ' 5 71.8885 1 1 . 5 ' 30.4' 1 . 0 ' 4.6' 121.5794 68.7895 COV. CONC. 25' B.L. [1] CONC. PAVERS 241.5174 2 5 . 0 ' 73.8438 72.0109 ' 7 0 . 0 2 1 E " 0 0 0 0 ° 0 8 ' ) ' 0 0 . 0 2 1 ( S I I S S A B G N R A E B D E M U S S A / / / / / / / / / / / / / / / / / / / / / / / / / / / / / / / / / / / / / / / / / / / / / / / / / / / / / / / / / / / / / / / / / / / / / / / / / / / / / / / / / / / / / / / / / / / / / / / / / / / / / / / / / / / / / / / / UL UL UL UL UL UL UL UL UL UL UL UL UL UL UL UL UL UL S 09°54'54"W 50.48' (50.00') ITEM10/7 (708)715-94031103 Lambie St. Unit B, Austin TX 78702HIGGINSDESIGNSoffice@higgins-designs.comwww.higgins-designs.comDATEREVDESCRIPTIONSTATUSADDRESSDRAWING NO.SCALEDATEDRAWN BYPROJECT NO.TITLEIf printed on 22x34 sheet, scale is as indicated. If printed on 11x17, the scale is reduced by half.Permit Set4705 RowenaAustin, TX 7875101/08/2025B. Higgins25001Permit Set01/08/202501/08/2025F-23989General NotesAs NotedS0.0GENERAL REQUIREMENTSGOVERNING CODE: The design and construction of this project is governed by the "International Residential code (IRC)", 2021 edition, hereafter referred to as the IRC, as adopted by the CITY OF AUSTIN building department understood to be the Authority Having Jurisdiction (AHJ). REFERENCE STANDARDS: Refer to chapter 35 of the IBC. Where other standards are noted in the drawings, use the latest edition of the standard unless a specific date is indicated. Reference to a specific section in a code does not relieve the contractor from compliance with the entire standard. NOTE PRIORITIES: Plan and detail notes and specific loading data provided on individual plans and detail drawings supplements information in the structural general notes. DISCREPANCIES: In case of discrepancies between the general notes, specifications plan/details or reference standards, the architect/engineer shall determine which shall govern. Discrepancies shall be brought to the attention of the architect/engineer before proceeding with the work. Should any discrepancy be found in the contract documents, the contractor will be deemed to have included in the price the most expensive way of completing the work, unless prior to the submission of the price, the contractor asks for a decision from the architect as to which shall govern. Accordingly, any conflict in or between the contract documents shall not be a basis for adjustment in the contract price. COORDINATION: The contractor is responsible for coordinating details and accuracy of the work; for confirming and correlating all quantities and dimensions; for selecting fabrication processes; for techniques of assembly; and for performing work in a safe and secure manner. MEANS, METHODS, AND SAFETY REQUIREMENTS: The contractor is responsible for the means and methods of construction and all job-related safety standards such as OSHA and dosh (department of occupational safety and health). contractor is responsible to adhere to OSHA regulations regarding steel erection items specifically addressed in the latest OSHA regulations. TEMPORARY SHORING, BRACING: The contractor is responsible for the strength and stability of the structure during construction and shall provide temporary shoring, bracing and other elements required to maintain stability until the structure is complete. It is the contractor's responsibility to be familiar with the work required in the construction documents and the requirements for executing it properly. SITE VERIFICATION: The contractor shall verify all dimensions and conditions at the site. Conflicts between the drawings and actual site conditions shall be brought to the attention of the architect/engineer before proceeding with the work. ADJACENT UTILITIES: The contractor shall determine the location of all adjacent underground utilities prior to earthwork, foundations, shoring, and excavation. Any utility information shown on the drawings and details is approximate and not necessarily complete. ALTERNATES: Alternate products of similar strength, nature, and form for specified items may be submitted with adequate technical documentation to the arch/engineer for review. Alt. materials that are submitted without adequate documentation or that significantly deviate from the design intent of materials specified may be rejected. Alts. that require substantial effort to review will not be reviewed unless authorized by the owner. DESIGN CRITERIAWind Design Data Risk Category II Ultimate Design Wind Speed (3 Sec Gust), Vult 115 MPH Exposure Category B Risk Category II Internal Pressure Coefficient, CPI +/- 0.18 Topographic Factor, KZT 1.0 Analysis Procedure Directional Live Loads Roof 20 PSF Floors 40 PSF Handrails & Pedestrian Guardrails 50 PLF (Uniform) 200 LBS (Concentrated) Stairs & Exits 100 PSF (Uniform) 300 LBS (Concentrated) Elevated Platforms & Walkways 60 PSF Snow Loads Ground Snow Load 5 PSF Snow Importance Factor 1.0 CAST-IN-PLACE CONCRETEREFERENCE STANDARDS: • ACI 301-16 "Specifications for Structural Concrete"• ACI 305.1-10 "Specifications for Hot Weather Concreting"• ACI 306.1-10 "Specification for Cold Weather Concreting"• ACI 318-14 "Building Code Requirements for Structural Concrete"• ACI 117-10 "Specification for Tolerances for Concrete Construction and Materials"CONCRETE MIX DESIGN REQUIREMENTS Strength F’c (PSI) Max. Aggregate Size (IN) Exposure Class W/CM Ratio Air Content (+/- 1.5%) Slump Spread Footings 3,000 1 F2/S0/W0/C1 0.45 6.0 3 Foundation Walls 3,000 1 F1/S0/W0/C1 0.45 4.5 3 Slabs on Grade 3,000 1 F2/S0/W0/C1 0.45 6.0 4 Slabs on Metal Deck 3,000 1 F0/S0/C0 0.45 <3 4 MIX DESIGN REQUIREMENT NOTES: 1.Fly ash: the use of fly ash, other pozzolans, silica fume or slag shall conform to ACI 318table 26.4.2.2(b) and section 26.4.2.2 maximum amount of fly ash shall be 25% oftotal cementitious content unless reviewed and approved otherwise by SER.2.Aggregates shall conform to ASTM C33.3.Non-chloride accelerator: Non-chloride accelerating admixture may be used inconcrete placed at ambient temperatures below 50°F at the contractor's option.4.Recommended slump apply when vibration is used to consolidate the concrete andmay be increased by 1" for other consolidation methods. Slump may be increasedwhen chemical admixtures are used, provided that the treated concrete has the sameor lower water/cement ratio and does not show segregation potential or excessivebleeding. Measured slump tolerance shall be +/-1.5" maximum.CONCRETE CURING: Provide curing compounds for concrete as follows: 1.Use membrane curing compounds that are compatible with and will not affectsurfaces to be covered with finish materials applied directly to concrete.2. Apply curing compounds at a rate equivalent to the rate of application at which curingcompound was originally tested for in conformance to the requirements of ASTM C 309-18 and the manufacturer's recommendations.CONCRETE REINFORCEMENTREFERENCE STANDARDS: • ACI 301-16 "Standard Specifications for Structural Concrete", section 3"Reinforcement and Reinforcement Supports.• SP-66-04 "ACI Detailing Manual" including ACI 315-99 "Details and Detailing ofConcrete Reinforcement. • CRSI MSP-09, 28th edition, "Manual of Standard Practice".• ANSI/AWS D1.4-18 "Structural Welding Code-Reinforcing Steel.• IRC chapter 19-concrete.• ACI 318-14.• ACI 117-10.PLACING: Conform to ACI 301 section 3.3.2 "Placement." Placing tolerances shall conform to ACI 117. Materials Reinforcing Bars ASTM A615 Grade 60 Deformed Bars Weldable Reinforcing Bars A706 Grade 60 Deformed Bars Smooth Welded Wire Fabric ASTM A185 Deformed Welded Wire Fabric ASTM A497 Bar Supports CRSI MSP-09, Chapter 3 “Bar Supports” Tie Wire 16 GA. or heavier, Black Annealed Stud Rails ASTM A1044 Decon or Approved Equivalent Headed Deformed Bars ASTM A970 Concrete Cover Concrete Caste Against Earth 3” Concrete Exposed to Weather 2” Ties in Columns and Elevated Beams 1-½”Bars in Slabs ¾” Bars in Walls ¾” STRUCTURAL STEELREFERENCE STANDARDS: • ANSI/AISC 303-16 - Code of Standard Practice for Steel Buildings & Bridgeshereafter referenced as AISC 303.• ANSI/AISC 360-16 - Specification for Structural Steel Buildings hereafter referencedas AISC 360.• RCSC - Specification for Structural Joints using High-Strength Bolts, 2014.• AWS D1.1-15 - Structural Welding Code - Steel hereafter referenced as AWS D1.1.SUBMITTALS: 1.Shop drawings shall be prepared in accordance with AISC 360 section m.1 and AISC303 section 4.2.Submit welders’ certificates verifying qualification within the past 12 months.3.Affidavit stating the steel provided meets the requirements of the grade(s) specified.Materials Wide Flange (W), Tee (WT) Shapes ASTM A992 FY = 50 KSI Structural (S), (M) & (HP) Shapes ASTM A36 FY = 36 KSI Channel (C) & Angle (L) Shapes ASTM A36 FY = 36 KSI Structural Bars & Plates (PL) ASTM A36 FY = 36 KSI Hollow Structural Section-Square/Rectangle (HSS) ASTM A500 Grade B FY = 46 KSI Structural Pipe (PIPE) 12” Diameter and Less ASTM A53 Grade B FY = 35 KSI Hollow Structural Section-Round (HSS) ASTM A500 Grade B FY = 42 KSI High-Strength Bolts ASTM A325/F1952 Type 1, Plain Nuts ASTM A563 Washers (Flat or Beveled) ASTM F436-Req’d @ Slotted & Oversized Holes Anchor Rods (Anchor Bolts) F1554 GR. 55 (Weldable) per Supplement NO. 1 Mild Threaded Rods ASTM A36 FY = 36 KSI Threaded Rods (Anchor B) ASTM A307 FY = 35 KSI Welded Headed Studs (WHS) ¾” OR 7/8” ASTM A108- NELSON/TRW S3L or Equal Welded Headed Studs (WHS) ½” OR 5/8” ASTM A108 – Nelson/TRW H4L or Equal Dowel Bar Anchor ASTM A496- Nelson/TRW D2L or equal Welding Electrodes E70XX, E70TXX Unless noted otherwise with a minimum toughness of 20 FT-LBS at 40 deg Fareignheit. WELDING: 1.Welding shall conform to AWS D1.1 and visually conform to AWS section 6 and table6.1. Fabrication/erection inspections by the contractor per AWS D1.1 section 6 shallbe by associate/certified inspectors (AWI/CWI) per AWS QC1 or AWS B5.1. specialinspections (verification inspections) shall be by a certified welding inspector (CWI) orsenior welding inspector (SWI) per AWS b5.1.2.Welders shall be qualified for the specific prequalified joints required by the designand certified in accordance with AWS requirements.3.Welding shall be in accordance with appropriate weld procedure specifications(WPS's) welders shall be familiar with the applicable WPS's.4.Welder qualifications and WPS's shall be maintained at the site of the work and shallbe readily available for inspection upon request both in the shop and in the field. 5.Use E70 or E71t, 70 KSI strength electrodes appropriate for the process selected.6.Prior to the start of work, special inspector or, if "AIUSC Certified" or otherwise"approved" shop, a shop certified weld inspector (CWI) certified in accordance withprovisions of AWS QC1 shall inspect and document compliance with the following:• Confirm welder qualifications prior to the start of work.• Review all WPS prior to the start of work.• Confirm materials in fabrications conform to the specifications.• Periodically observe joint preparation, fit-up and welder techniques.• Identify on plans all multi-pass fillet welds, single pass fillet welds greater than5/16", and complete-and partial-joint penetration (CJP or PJP) groovewelded butt joints that requires continuous (special) inspection.• Visually inspect all welds per special inspection requirements for steel andAWS section 6.5 and table 6.1.7.Welding of high strength anchor rods (F1554-50, F1154-105) is prohibited unlessapproved by Engineer.8.Welding of shear studs on steel beams: headed shear studs welded to tops of wideflange beam shall be welded in accordance with AWS D1.1 chapter 7 "Stud Welding".9.Welding of headed studs on embedded steel plates for anchorage to concrete:headed studs welded to steel embedment plates cast monolithic with concrete andshall be welded in accordance with AWS d11 chapter 7 "Stud Welding" unless notedotherwise on plans.HIGH-STRENGTH BOLTING: High strength bolts shall be of the ASTM grade and type specified in the materials section. Unless noted otherwise, install bolts in joints in accordance with the RCSC specification as joint type ST, "snug tight'', - per RCSC specification table 4.1 and section 8.1. Inspection is per RCSC section 9.1. bolts have been designed as ASTM A325-N bolts - "threads included in the shear plane". EXISTING CONDITIONS1.Except in demotion plans, and where otherwise noted, all new construction is shown withsolid black lines, and existing construction is shown with solid greyed lines.2.Existing conditions on these drawings are reproduced, in whole or in part, from existingdrawings and/or limited visual observations of the existing structure and shall be verified inthe field by the contractor prior to the commencing of work.3.The contractor shall carry contingency in pricing for differences in the conditions shown,including but not limited to:• different framing conditions.• different foundation conditions.• hidden damage or deterioration in structural members.• additional framing to support mechanical equipment and penetrations throughsteel beams due to encountered conditions. 4.Where discrepancies between the design drawings and field conditions are found, orexisting structural members and connections are found to be damaged or deteriorated toa diminished capacity and are not shown on these drawings, the contractor shall submitdetailed sketches of the existing conditions to the owner and engineer for review prior tocommencing with work. Modifications to current details or additional new details may berequired based on the actual field conditions.5.Existing framing members shown on these drawings are designated based on visualobservations of existing structure. actual member sizes shall be verified in the field.PREFABRICATED METAL PLATE CONNECTED WOOD TRUSSESREFERENCE STANDARDS: Trusses shall be designed by the contractor in accordance with the truss plate institute "Design Standard for Metal Plate Connected Wood Truss Construction" (ANSI/TPI 1-95) and shall conform to the IRC. SUBMITTALS: Submit product data and proof of ICBO approval for framing members and fasteners that have been designed by others. Submit calculations prepared by an engineer licensed in the state of Texas for all members and connections designed by others along with their respective shop drawings. All necessary bridging, blocking, and blocking panels and web stiffeners shall be detailed and furnished by the supplier. temporary and permanent bridging shall be installed in conformance with the manufacturer's installation requirements. a.Metal plate connected roof truss shop drawings shall provide detailed descriptionof shapes, bearing points, hips, and valleys as shown in the drawings. Providespecial trusses such as jack-trusses, girder trusses and step-down trusses to matchdrawings. provide all truss connection details and required connection materials.Provide all truss reactions on shop drawings.b.Metal plate connected floor truss shop drawings shall provide detailed descriptionof shapes, bearing points, and step downs. Provide all truss connection detailsand required connection materials. Provide all truss reactions on shop drawings.1.Truss members shall be clamped in a mechanical or hydraulic jig with sufficient pressureto bring members into reasonable contact at all joints during application of connectorplates.2.Provide adequate erection bracing in accordance with truss plate institute publicationHIB-91.3.Truss manufacturer shall provide permanent bracing as required by the design of thetrusses. Erection bracing may remain in place as permanent bracing where it does notinterfere with the architectural finishes.4.All timber truss members shall be southern yellow pine with a maximum moisture contentof 19%. Chord members shall be no. 2 or better and web members shall be no. 3 orbetter.5.Connection plates shall be manufactured by a WTCA member plate manufacturer.Plates shall be 20 gauge minimum, ASTM A446 grade a steel, with a G60 galvanizedcoating.6.Trusses shall be designed in accordance with the following requirements:a.Top chords shall be designed to resist the local bending induced by the floor orroof uniform load on the top chord.b.Limit live load deflection of floor trusses to L/480. total load deflections shall belimited to L/360.c.Truss members and connections shall be proportioned with a maximum allowablestress increase for duration of load as follows:i.Roof loads25% ii.Trusses shall be designed for the superimposed dead and live loads as notedin the structural notes and as indicated in the drawings. Dead loads shall notbe less than the following:Floor top chord 15 PSF Floor bottom chord 5 PSF Roof top chord 8 PSF Roof bottom chord 5 PSF 7.Connect roof trusses to bearing wall or beam support at each end with a type H2.5framing anchor as manufactured by the Simpson company or approved equal.WOOD FRAMINGREFERENCE STANDARDS: ANSI/AF&PA NDS-2015 “National Design Specification for Wood Construction with 2015 Supplement”; American Forest and Paper Association 1.All sawn lumber and pre-manufactured wood products shall be identified by the grademark or a certificate of inspection issued by the certifying agency.2.Unless otherwise noted, all structural framing lumber shall be clearly marked no. 2 gradesouthern yellow pine (SYP), except that non-loadbearing interior walls may be studgrade SYP, Douglas Fir-larch (Doug Fir), or Spruce-Pine-Fir (SPF).3.All wood stud walls shall be full height without intermediate plate line. Exterior, load-bearing wood stud walls shall be sized and spaced according to the following table:WALL FRAMING SCHEDULE Min. Size Min. Spacing Max. Height Supporting Roof Only 2X4 16” O.C. 12’-0” 2X6 16” O.C. 18’-0” 2X6 12” O.C. 20’-0” 2X6 8” O.C. 24’-0” Supporting One Floor and a Roof 2X4 16” O.C. 10’-0” 2X6 16” O.C. 18’-0” 2X6 12” O.C. 20’-0” 2X6 8” O.C. 24’-0” Supporting Two Floors and a Roof 2X6 16” O.C. 14’-0” 2X6 12” O.C. 16’-0” 2X6 12” O.C. 18’-0” 2X6 8” O.C. 20’-0” 4.Finger jointed studs are acceptable at interior, non-load bearing stud walls only.5.All load bearing walls greater than 10'-0" in height shall have solid 2x blocking at 4'-0"OC maximum vertically. End nail with 2-16D nails or side toenail with 2-16D nails.6.Provide double studs at all wall corners and on each side of all openings, unless noted ordetailed otherwise.7.Place a single plate at the bottom and a double plate at the top of all stud walls.Exterior sill plates shall be bolted to the foundation with 1/2" anchor bolts with a minimumembedment of 8" spaced at 4'-0" on center. Provide a minimum of two bolts per platesegment. Sill plates in contact with concrete or masonry shall be pressure treated with apreservative.8.Where shown, wood connectors shall be Simpson Strong-Tie as specified in the latestcatalog. Connectors by other manufacturers may be substituted provided suchconnectors have the current ICC approval for equal or greater load capacities and issubmitted for approval by the engineer of record. Connectors shall be installed per themanufacturer's directions.a.Where connectors are used in exposed or exterior applications, and whenconnectors are in contact with preservative treated (PT) lumber, connectors are tobe hot dipped galvanized (HDG), mechanically galvanized (ASTM B695, class 40or greater) stainless steel, or zinc galvanizing equal or greater to zmax Simpsonfinish.9.Fasteners shall conform to IRC 602 “fastener schedule” unless otherwise noted. nailaccording to IRC. nails shall be common. Alternate nails may be used upon review andapproval by Structural Engineer of Record. Staples for the nailing or rated sheathing issubject to review and approval by the Structural Engineer of Record.10.Moisture content of all sawn lumber shall have a maximum of 19%, except for pressuretreated wood sill plates. Moisture content can be lower than 19%. Refer to architect'sdrawings and project specifications and with cladding installer for maximumrecommended moisture content.11.Preservative treated (PT) wood materials are to be used per IRC. “Decay and TermiteProtection” shall conform to the appropriate standards of the American WoodPreservers Association (AWPA) for sawn lumber. Fasteners, anchors, and connectorstouching treated wood shall be either stainless steel or hot-dipped galvanized.12.Refer to the architectural drawings for additional wood framing members. provideadditional wood framing members shown on the architectural drawings even though theymay not be shown on the structural drawings.WOOD STRUCTURAL PANEL SHEATHINGREFERENCE STANDARDS: PA form D510C “Panel Design Specification”; American PlywoodAssociation. See table below for sheathing thicknesses and nailing sizes and patterns. 1.See table below for sheathing thicknesses and nailing sizes & patterns.2.Floor sheathing shall be glued to the wood support members with a wet use adhesive, inaddition to being nailed to the supports per wood framing typical details. stagger jointsin sheathing.3.Roof sheathing shall be continuous over two or more spans with the long dimensionoriented perpendicular to the framing members.4.Wall sheathing: all exterior wall framing shall be braced by 4'-0" wide x 1/2" thickpanels of APA rated sheathing with an exposure 1 rating extending from the top plate tothe sill plate. where wall is taller than 8'-0", provide multiple panels as required toextend from sill plate to top plate. provide 2x blocking as required to support all paneledges. Refer to wall bracing plan for additional information.SHEATHING & FASTENING REQUIREMENTS Use Min Nominal Thickness Nail Size Nail Spacing Roofs 5/8” 8D Common (2-1/2”x0.131”) 6” OC Edge 12” OC Field Walls Ref. Wind Bracing Ref. Wind Bracing Ref. Wind Bracing Floors 3/4” 8D Common (2-1/2”x0.131”) 6” OC Edge 12” OC Field BUILDING PAD1.Prior to excavating for building pads or placing any fill soils, all organic materials,existing pavements, and otherwise unsuitable materials shall be removed from plannedbuilding areas to a depth of Site stripping shall include the limits of any proposed building and abutting sidewalks or flatwork, plus a horizontal distance of 3 feet beyond. Site Stripping in the protected tree’s ½ CRZ is limited to 4”. No site stripping is permitted in the protected tree’s ¼ CRZ. 2.Bottom of grade beams shall have a slope less than or equal to 1 in 10. Under nocircumstances shall concrete beams be placed on sloping grade greater than 1 in 10.The bottom of grade beams shall be free of loose deleterious fill material includingtopsoil, loose rocks, crushed rock, base material, water, or moist soil.3.Place imported select fill in approximately 8-inch loose lifts, watered as required andcompacted to 95 percent of maximum dry density (as defined in ASTM D698) at amoisture content within -3 to +3 percent of optimum moisture content. The compactedthickness of each lift should not exceed 6 inches.4.Grade adjustments within the building limits shall be accomplished with select fill soilsmeeting TXDOT standard specifications item 247, type a, grade 4 (crushed limestonebase material). All structural fill shall be placed on prepared surfaces in lifts not toexceed eight inches loose measure with compacted thickness not to exceed six inches.The fill shall be compacted to at least 95 percent of the ASTM 698 maximum dry densityat a moisture content ranging between -2 and +3 percent of optimum moisture content.5.Structural fill shall be hard durable particles of gravel or crushed stone, with no organicmaterial.6.Where not covered by concrete flatwork or pavements, provide 2-foot-thick clay capsat overbuild areas along the perimeters of slabs-on-grade over building pads, toprotect from moisture intrusion. Caps shall slope away from buildings. Site fill withinprotected tree’s ½ CRZ is limited to 4”. No fill is permitted within the protected tree’s ¼CRZ.7.Provide a 10-mil vapor barrier placed according to manufacturer's recommendationsbetween the bottom of slab and the top of the select fill. Moisture barrier shall not bedraped continuously across the bottom of grade beams.8. Foundation slab concrete should be placed within 2 weeks of the completion of trenchexcavations and the moisture barrier should be installed before any notable rainfallevent. If the bearing soils are softened by surface water intrusion or disturbance, thesoftened soils must be removed from the foundation excavation bottom prior toconcrete placement. Exposure to the environment may weaken the soils at the gradebeam bearing level if the foundation excavations remain open for an extended duration.8" bel. grade.SUBMITTALSSUBMIT FOR REVIEW: SUBMITTAL REVIEW PERIOD: Submittals shall be made in time to provide a minimum of two weeks for review by the architect/engineer prior to the onset of fabrication. GENERAL CONTRACTOR'S PRIOR REVIEW: Prior to submission to the architect/engineer, the contractor shall review the submittal for completeness. Dimensions and quantities are not reviewed by the SER, and therefore must be verified by the general contractor. Contractor shall provide any necessary dimensional details requested by the detailer and provide the contractor's review stamp and signature before forwarding to the architect/engineer. SHOP DRAWING REVIEW: Once the contractor has completed his review, the SER will review the submittal for general conformance with the design concept and the contract documents of the building and will stamp the submittal accordingly. markings or comments shall not be construed as relieving the contractor from compliance with the project plans and specifications, nor departures there from. Pre-engineered Truss Shop Drawings3355 BEE CAVE RDSTUDIO #303AUSTIN TX 78746(512) 447-6806 TELWEISSARC.COMWEISS ARCHITECTUREITEM10/8(708)715-94031103 Lambie St. Unit B, Austin TX 78702HIGGINSDESIGNSoffice@higgins-designs.comwww.higgins-designs.comDATEREVDESCRIPTIONSTATUSADDRESSDRAWING NO.SCALEDATEDRAWN BYPROJECT NO.TITLEIf printed on 22x34 sheet, scale is as indicated. If printed on 11x17, the scale is reduced by half.Foundation/Framing Plans1/4":12"S1.0CONCRETE CONTRACTOR MUST VERIFY ALL DIMENSIONS AND COORDINATE STRUCTURAL PLANS AND DETAILS WITH ARCHITECTURAL DRAWINGS BEFORE CONCRETE WORK.THE ENGINEER OF RECORD AND PROJECT ARCHITECT SHALL BE NOTIFIED OF ANY DISCREPANCIES PRIOR TO CONSTRUCTION.REFER TO ARCHITECTURAL DRAWINGS FOR SLAB DROPS & ACCESSIBILITY REQUIREMENTS.ALL [NEW] FOUNDATIONS TO BE 24" MIN. DEPTH, ORMATCH [EXISTING] FOUNDATION DEPTH (WHICHEVER ISGREATER).1.4.3.2.PRE-POUR OBSERVATION REQUIRED BY ENGINEERALL NEWGRADEBEAMS12"NOTE"A"12" MIN.2-#5 T&BW/ #3 TIES@ 18" O.C.----------NOTE "A": ALL [NEW] GRADE BEAMS TO BE 24" MIN.DEPTH, OR MATCH [EXISTING] FOUNDATION DEPTH(WHICHEVER IS GREATER).FOUNDATION DESIGN SUMMARY (TABLE 1)CONCRETE COMPRESSIVE STRENGTH SLAB THICKNESS SLAB REINF.DESIGN PI SOIL BEARING CAP. 3000 PSI--603,000 PSFHEADER SCHEDULELABELSIZEJAMB STUDSH62-2x6 1 JACK, 2 KINGH82-2x8 2 JACK, 2 KINGH102-2x10 2 JACK, 2 KINGH122-2x12 2 JACK, 2 KINGHEADER SCHEDULELABELH12H10H8H6SIZE2 - 2x62 - 2x122 - 2x102 - 2x8JAMB STUDS2 JACK, 2 KING1 JACK, 2 KING2 JACK, 2 KING2 JACK, 2 KINGWOOD/STEEL BEAM(FL. INDICATES BEAM ISFLUSH W/ FLOORFRAMING)STEEL BEAM W/MOMENT CONNECTIONWOOD 2x HEADERNO. STUDS @BEAM BEARINGWOOD/STEEL COLUMNH62x HEADER SIZEPER TABLEFRAMING LEGEND FRAMING LEGENDSTEELCOL.C1COL. CALLOUT (REF. TABLE 3)WOODCOL.C1WOOD/STEEL BEAM(FL. INDICATES BEAM ISFLUSH W/ FLOORFRAMING)WOOD/STEELFLUSH BEAMWOOD/STEELDROPPED BEAMXXFRAMING LEGENDWOOD/STEEL COLUMNSSTEEL BEAM W/ MOMENT CONNECTIONWOOD/STEEL FLUSH BEAMWOOD/STEEL DROPPED BEAMWOODCOL.STEELCOL.COL. CALLOUT(REF. TABLE 3)NO. STUDS @BEAM BEARINGLOO G) BEA LOOXXLOO G) BEA LOOXX2x HEADER SIZEPER TABLEH6[NEW] 12" WIDEGRADE BEAMSNOTE: ALL [NEW]FOUNDATIONS TO BE 24" MIN.DEPTH, OR MATCH [EXISTING]FOUNDATION DEPTH(WHICHEVER IS GREATER)C1C1ATTACH [NEW]GRADE BEAMS TO[EX] SLAB W/ (4) #4x 18" DOWELS (2)T&B AT EA. GRADEBEAM (TYP.)C1Foundation PlanSCALE 1/4"=1'-0"A[NEW] 12" WIDEGRADE BEAMSREBARREINFORCEMENT(REF. TABLE 2)BEAM WIDTH(REF. TABLE 2)WOOD COL.& BASE PERPLANSCUT BARS @ CENTEROF SLAB OPENING &BENDNEW CONC. TO BE1" THICKER THANEXISTINGSAW CUT 1" DEEP & CHIPCONCRETE TO REMOVE. DO NOTCUT THROUGH SLAB OR BEAMREINF.BEND EXISTING BARS BACKIN PLACE & TIE TOGETHERW/ BARS TO MATCH EA.WAYCOMPACTEDSTRUCTURAL FILL, REF.GENERAL NOTESC1---6x6 DF/SYP---ABU66Z POST BASE---JOIST SCHEDULE (TABLE 4) LABELSIZEMAX. SPACINGREMARKS JOIST SCHEDULE (TABLE 4)LABELSIZEMAX. SPACINGREMARKSJ118" PRE-ENG.FLOOR TRUSSES24"DESIGN BY OTHERSJ22x1216"-J32x624"-J42x616"---------GIRDER TRUSS UWA100 PLF DL + 100 PLF LLJ12-18" LVLC12-2x12 PT. STRINGER2-2x122-2x122-2x12INSTALL [NEW]MSTC66 STRAPS(SIM. DETAIL 1/S4.0)H82-2x12 PT. STRINGER2x12 LEDGERC12x12 DIAG.2k DL4k RLLJ2J2INSTALL [NEW]MSTC66 STRAPS(SIM. DETAIL 1/S4.0)First Floor Framing PlanSCALE 1/4"=1'-0"BH6H6H6H6H6H6H6H6H6H6PROVIDE DBL.JOISTS AROUNDATTIC HATCH2-2x102-2x12J4J3Second Floor Framing PlanSCALE 1/4"=1'-0"C9.25" LVL9.25" LVL9.25" LVL9.25" LVL1/2" MIN. PLY/OSBROOF DECK OVER 2x6TYP. RAFTERS @ 24"O.C. SIMPSON H2.5A@ EA. RAFTER/TOP PL.CONNECTIONRoof Framing PlanSCALE 1/4"=1'-0"DALL CONSTRUCTION PER CURRENT EDITION OF THEINTERNATIONAL RESIDENTIAL CODE (IRC).VERIFY PLAN DIMENSIONS AND FLOOR/CEILINGELEVATIONS (T.O.P.) WITH ARCHITECTURAL PLANS. NOTIFYENGINEER OF RECORD OF DISCREPANCIES. REFER TO GENERAL NOTES (S0) FOR MATERIAL PROPERTIESAND CONSTRUCTION RECOMMENDATIONS.AT A MINIMUM, DOUBLE JOISTS AT HVAC UNIT LOCATIONS.NOTIFY THE ENGINEER OF RECORD IF FIELD CONDITIONSDON'T ALLOW FRAMING MEMBERS TO BE PLACED ASSHOWN ON PLANS.1.5.4.3.2.FRAMING OBSERVATION REQUIRED BY ENGINEERROOF FRAMING LEGEND LABELDESCRIPTION PURLINBRACE RIDGE, RAFTER, OR PURLINW/ BEARING POINT LOCATIONBRACE RIDGE, RAFTER, OR PURLINW/ BEARING POINT DIRECTLYBELOWPURLIN BRACING LINEBEAM BELOWROOF FRAMING LEGENDLABELDESCRIPTIONBRACE RIDGE, RAFTER, OR PURLINW/ BEARING POINT LOCATIONBRACE RIDGE, RAFTER, OR PURLINW/ BEARING POINT DIRECTLYBELOWPURLIN BRACING LINEBEAM BELOWPURLINFoundation DetailSCALE 3/4"=1'-0"1Typ. Slab TrenchingSCALE 3/4"=1'-0"23/4" MIN.PLYWOODSUBFLOOR1S1.0TYP.[EXISTING]SLAB-ON-GRADEFOUNDATION TOREMAIN1S1.13S1.12S1.12S1.1VERIFY SHOWERDROP W/ ARCH'LPermit Set4705 RowenaAustin, TX 7875101/08/2025B. Higgins25001Permit Set01/08/202501/08/2025F-23989ITEM10/9(708)715-94031103 Lambie St. Unit B, Austin TX 78702HIGGINSDESIGNSoffice@higgins-designs.comwww.higgins-designs.comDATEREVDESCRIPTIONSTATUSADDRESSDRAWING NO.SCALEDATEDRAWN BYPROJECT NO.TITLEIf printed on 22x34 sheet, scale is as indicated. If printed on 11x17, the scale is reduced by half.Wind Bracing Plans1/4":12"S1.1PRIOR TO CONSTRUCTION OF SHEARWALLS, REVIEW LATEST DIMENSIONED ARCHITECTURAL DRAWINGS AND NOTIFY STRUCTURAL ENGINEER OF ANY LOCATIONS WHEREMINIMUM SHEARWALL LENGTHS ARE NOT MET. MINIMUMLENGTHS BASED ON OUT-TO-OUT FACE OF TIEDOWN POSTS.SEE PLANS FOR SHEARWALL TIE DOWNS, SIZES AND LOCATIONS. PLACE SHEATHING ON SIDE OF WALL WHERE SHEARWALL SYMBOL OCCURS.HORIZONTAL PLYWOOD SPLICES TO OCCUR AT RIBBON BAND. WHERE WALL HEIGHT DICTATES HORIZONTAL SPLICE AT WALL, PROVIDE 2x BLOCKING. DO NOT SPLICE AT DOUBLE 2x TOP PLATE. USE 2x STUDS, DOUBLE TOP PLATE AND SINGLE SILL PLATE, U.N.O.SHEATHING THICKNESS IS NOMINAL, ACTUAL THICKNESS EQUIVALENTS ARE 1/2"= 15/32", 5/8" = 19/32", 3/4"= 23/32"INSTALL (2)-2x STUDS OR 3x STUD AT EDGE OF PLYWOOD PANELS WHERE EDGE NAILING IS LESS THAN 6" O.C.1.1.7.6.5.4.3.2.WIND BRACING LEGEND (TABLE 9) LABEL DESCRIPTION EDGE NAILING SILL PLATE NAILING REF. DETAIL 7/16” APA RATED CDX 8d @ 6” O.C. 16d @ 6” O.C. 2/S4.0 7/16” APA RATED CDX 8d @ 3” O.C. 16d @ 3” O.C. 2/S4.0 1x4 DIAG. LET-IN OR 18 Ga. X 1 ¼” “X” STRAPS - 16d @ 6” O.C. 5/S4.0 STEEL FRAME PER FRAMING PLANS - - - 7/16” APA RATED CDX 8d @ 3” O.C. 8d @ 3” O.C. 1/S4.0 CONC. SHEAR WALL - - - AACONCSTLLIBWSPCS-PF2"2"First Floor Wind Bracing PlanSCALE 1/4"=1'-0"EBWLBWLBWLBWL[NEW]WSP[NEW]WSP[NEW]WSP[NEW]WSP[NEW]WSPBWLBWLBWLBWLHDU-4HDU-4[EX]WSP[EX]WSP[EX]WSP[EX]WSP[EX]WSPCONTRACTOR TO VERIFY THEPRESENCE OF 1/2" MINIMUMSTRUCTURAL SHEATHING AT ALL[EXISTING] EXTERIOR WALLS TOREMAIN. PROVIDE NEW 1/2"PLY/OSB SHEATHING AT ALLEXTERIOR WALLS IF NONEPRESENTFirst Floor Wind Bracing PlanSCALE 1/4"=1'-0"F2x RAFTERSPER PLANSDBL. TOP PL.H2.5A @EA.RAFTERCONT. 2xBLOCKINGCLG. JOISTSPER PLANS2nd FL. T.O. DECK(REF. ARCH'L)T.O. 1ST FLOOR PLATE(REF. ARCH'L)FLOOR DECKPER SCHEDULE2ND FL. WALL FRAMING1ST FL. WALLFRAMINGDBL. TOP PLATE (TYP.)WALL SHEATHINGPER WINDBRACING PLANFraming DetailSCALE 1"=1'-0"1Framing DetailSCALE 1"=1'-0"22x DECK JOISTSPER PLAN[EX] WALLFRAMING TOREMAIN[NEW] PRE-ENG.FL. TRUSSES (BYOTHERS)SUBFLOOR PERGEN. NOTES2x LEDGER PER PLANS,ATTACH TO BLOCKINGIN WALL W/ (2) #12 x 31/2" WOOD SCREWS @16" O.C.DECK FLASHING &WATERPROOFINGPER ARCH/BUILDERFraming DetailSCALE 1"=1'-0"3Permit Set4705 RowenaAustin, TX 7875101/08/2025B. Higgins25001Permit Set01/08/202501/08/2025F-23989ITEM10/10(708)715-94031103 Lambie St. Unit B, Austin TX 78702HIGGINSDESIGNSoffice@higgins-designs.comwww.higgins-designs.comDATEREVDESCRIPTIONSTATUSADDRESSDRAWING NO.SCALEDATEDRAWN BYPROJECT NO.TITLEIf printed on 22x34 sheet, scale is as indicated. If printed on 11x17, the scale is reduced by half.FULL-HEIGHT 716" OSBOR 1532" PLYWOODPONY WALLHEIGHT(IF APPLICABLE)HEIGHT (H)10' MAX.TOTALWALL HEIGHT12' MAX.SHEATHING TO HEADER: 8DCOMMON NAILS (0.131"x2.5") IN3" O.C. GRID PATTERN AS SHOWNCONTINUOUS WOOD HEADERMIN. 3"X11¼"(WITH 12" SPACER ON BACKSIDE)2 ROWS 16D SINKER NAILS(0.148"x3.25") AT 3" O.C.MIN. DOUBLE2X END POSTS8D COMMON NAILS(0.131"x2.5") AT3" O.C. SPACING INTO ALLFRAMING MEMBERSKING STUD TO HEADER: 6-16DSINKER NAILS (0.148"x3.25")HOLDOWNSPER WINDBRACINGPLANSMSTC66 STRAPS OPPOSITE SITEOF SHEATHINGSHEATHING OPPOSITE SIDE OFBRACING MATERIAL:12" MIN. GYPSUM WALL BOARDWITH TYPE W SCREWS SPACED 8"O.C. AT PANEL EDGES AND 16" O.C.IN THE FIELD (12" O.C. IN THE FIELDFOR STUDS SPACED AT 24" O.C.)OR NAILED PER IRC TABLE R702.3.545° TO 60°BRACING MATERIAL:1X4 WOODLET-IN-BRACE OR18 Ga. x 114" "X"STRAPSTOP & BOTTOM PLATE NAILING:2-8D COMMON NAILS(0.131"x2.5") FOR 1X4, 2-16DCOMMON NAILS (0.162"x3.5")FOR METAL STRAPSSTUD NAILING:2-8D COMMON NAILS (0.131"x2.5")FOR 1X4, 1-8D COMMON NAIL FORMETAL STRAPS2X SILL PLATE ATFLOOR FRAMING2X SILL PLATE ATFLOOR FRAMINGDBL. 2x TOP PL.T.O. DECKINGSHEAR WALLSHEATHINGSEE SCHEDULEFIELD NAILINGSEE SCHEDULEPANEL EDGENAILINGSEE SCHEDULE2x BLOCKING ATHORIZONTALPANEL EDGESSILL ANCHORS AT 48"O.C. AND AROUNDWINDOW/DOOROPENINGSFLOOR OR ROOFFRAMING PER PLANSIMPSON STRAPWHERE OCCURS PERWIND BRACING PLANREF.BRACINGPLANREF.BRACINGPLANTYPICAL WALL STUDPER SCHEDULEHOLDOWN POSTPER SCHEDULESIMPSONHOLDOWNWHERE OCCURS,SEE WINDBRACING PLAN7" MIN.OPTION: 12" Ø X 4 14"EMBED SIMPSONTITEN HD ANCHOROPTION: 1/2" DIA. x 41/4" EMBED SIMPSONTITEN HD ANCHOR7" MIN.TOP PLATE TO BECONNECTED AT SPLICE W/2 ROWS OF 16d NAILS @4" O.C. (EA. SIDE OFINTERSECTION)TYPICAL DBL. TOPPLATEMIN. 48" LAPSTANDARD WASHER ND NUT (SNUG-TIGHT)1/2' DIA. J BOLT W/ MIN.EMBEDMENT INTOCONC. AS SHOWN1 3/4" MIN. FROMEDGE OFCONCRETE.Typ. Wood Portal Frame (CS-PF)SCALE NTS1Typ. Wood Shear WallSCALE NTS2Typ. Sill AnchorSCALE NTS3Typ. Let-in-braceSCALE NTS5Typ. Top Pl. LapSCALE NTS4Wind Bracing DetailsAs NotedS4.0Permit Set4705 RowenaAustin, TX 7875101/08/2025B. Higgins25001Permit Set01/08/202501/08/2025F-23989ITEM10/11(708)715-94031103 Lambie St. Unit B, Austin TX 78702HIGGINSDESIGNSoffice@higgins-designs.comwww.higgins-designs.comDATEREVDESCRIPTIONSTATUSADDRESSDRAWING NO.SCALEDATEDRAWN BYPROJECT NO.TITLEIf printed on 22x34 sheet, scale is as indicated. If printed on 11x17, the scale is reduced by half.D/6 max.outer 1/3 of spaEffects of notches can be reduced byusing a gradual tapered notch insteadof a square-cornered notch.D/3 max.D = actual dimensionouter 1/3 of spanmax. length = D/3D/6 max.2" min. from topand bottom of joisD/4 max. at endsNotching not permitted in middle 1/3 of spMAX. LENGTH = D/3D/6 MAX.D = BEAM DEPTH2" MIN. FROM TOP& BOT. OF JOISTD/4 MAX. AT ENDSOUTER 1/3 OF SPANNOTCHING NOT PERMITTED IN MIDDLE1/3 OF SPANOUTER 1/3 OF SPAND/6 MAX.D/3 MAX.TAPER ENDS OF NOTCHES 45DEGRESS 0.25W MAX. NOTCH@ EXTERIOR &BEARING WALLS0.4W MAX.ELSEWHERE0.4W MAX. DIA.HOLE @ EXTERIOR &BEARING WALLS0.6W MAX.ELSEWHERESTUDWIDTH"W"IF LIMITS AREEXCEEDED, USESIMPSON HSS STUDSHOE, DO NOT ALTERSTUDS SUPPORTINGBEAMSNOTCH GREATER TH50% OF THE PLATE W H16 GAGE (0.054") AND 1.5"WIDE METAL TIE FASTENACROSS AND TO THE PL@ EA. SIDE OF THE NOTW/ (8) 16d NAILS EA. SIDTOP PLATESPIPE BY OTHERSPIPEPENETRATIONDBL. TOP PL.16 Ga. x 1 1/4" WIDEMETAL TIE ATTACHEDTO EA. 2x PLATE W/(8) 16d NAILS EA. SIDENOTCH GREATERTHAN 50% OFPLATE WIDTH2"2"134"ASSEMBLY A: 3 ROWS12d NAILS @ 12" O.C.OR 2 ROWS OF 12"BOLTS @ 12" O.C.ASSEMBLY B: 3 ROWS12d NAILS @ 12" O.C.OR 2 ROWS OF 12"BOLTS @ 12" O.C.ASSEMBLY C: 2 ROWSOF14"X6" SCREW @ 12"O.C. OR 12" THROUGHBOLTSALL MULTIPLE PLY-MEMBERS TO BE BOLTED OR NAILED TOGETHER. AS PER DETAILASSEMBLY "A"2 PLY OF 134"ASSEMBLY "B"3 PLY OF 134"ASSEMBLY "C"4 PLY OF 134"2"2"2"2"double headerjack rafterdouble rafterjoist hangersvalley rafterside studsize window to allowproper flashing, det nand finishing of rooroof sheathing applied pto construction of dormDBL. RAFTERJACK RAFTERDBL. RAFTER MIN.AT WALL FRAMINGJOIST HANGERSPER SCHEDULEVALLEY RAFTERSTUD FRAMINGOPENING PER ARCH'LROOF SHEATHING PERWIND BRACING PLANEXTERIOR ORBEARINGWALLBored/Notched JoistSCALE NTSTyp. Bored/Notched StudSCALE NTSTyp. Top Pl. NotchSCALE NTSTyp. Multiple Member Connx.SCALE NTSTyp. Dormer FramingSCALE NTSTyp. Framing DetailsAs NotedS4.1Permit Set4705 RowenaAustin, TX 7875101/08/2025B. Higgins25001Permit Set01/08/202501/08/2025F-23989ITEM10/124705 ROWENA EXHIBIT- ROWENA/ AVENUE F MID BLOCK PROPERTIES NORTH 2 UNITS ON SMALLER LOT 5968 SF 2 HOUSES ON SIM LAND SIZE 4705 ROWENA (SUBJECT PROPERTY- 6038SF) ONLY OTHER MID BLOCK PROPERTY THAT FACES 2 STREETS AND CANNOT BUILD A DUPLEX GARAGE WITH SECOND STORY AND BATHROOM DUPLEX DUPLEX 7,200 SF LOT (DUPLEX SIZE) THE EASTERN BLOCK OF ROWENA IS THE ONLY BLOCK IN HYDE PARK THAT FACES A STREET ON BOTH THE FRONT AND BACK FACADES- THERE ARE A TOTAL OF 7 FRONT TO BACK MID BLOCK LOTS- 3 HAVE BEEN SUBDIVIDED IN TO MICROLOTS CONTAINING 6 HOUSES (2 PER LOT) – OF THE REMAINING 4, ONE IS LARGE ENOUGH FOR A DUPLEX. OF THE REMAINING 3 LOTS, ONE IS SMALLER THAN 4705 ROWENA BUT HAS 2 DWELLING UNITS AND HAS A CONDO REGIME. THEREFORE, 4705 ROWENA AND 4810 AVENUE F ARE THE ONLY 2 MID BLOCK PROPERTIES FACING 2 ROADS IN HYDE PARK THAT DO NOT HAVE A 2 UNIT ENTITLEMENT- ADDITIONALLY, THE HOUSE NEXT DOOR TO 4705 HAS A 2 STORY GARAGE WITH A BATH ITEM10/13