2.2_Backup_Water Loss Report — original pdf
Backup
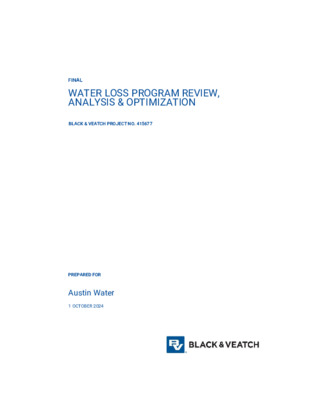
WATER LOSS PROGRAM REVIEW, ANALYSIS & OPTIMIZATION BLACK & VEATCH PROJECT NO. 415677 FINAL PREPARED FOR Austin Water 1 OCTOBER 2024 2.0 Introduction and Initial Audit Analysis ..................................................................................... 2-1 AUSTIN WATER | Water Loss Program Review, Analysis & Optimization Table of Contents Abbreviations and Definitions ................................................................................................................ vi Key Terms ............................................................................................................................................. vii 1.0 Executive Summary ................................................................................................................. 1-1 1.1 1.2 2.1 2.2 2.3 2.4 3.2 3.3 1.2.1 2.2.1 2.2.2 2.3.1 1.2.2 1.2.3 2.3.2 2.3.3 2.3.4 2.3.5 2.3.6 2.3.7 2.3.8 2.4.1 State Audit Requirements ..................................................................................... 2-2 Determination of Real Losses .............................................................................. 2-8 Determine Authorized Consumption ................................................................... 2-6 Outline of AWWA Audit Approach ........................................................................ 2-3 Gather Data and System Information .................................................................. 2-4 Determination of Water Loss ............................................................................... 2-7 Determination of Non-Revenue Water ................................................................. 2-9 Determining Apparent Loss .................................................................................. 2-7 Determine System Input ....................................................................................... 2-5 Real Loss (Leakage) ............................................................................................. 1-3 Production Metering ............................................................................................. 1-3 AW’s Water Auditing and Loss Control Programs .............................................. 2-2 Apparent Loss ....................................................................................................... 1-3 Water Loss Audit Approach .................................................................................................. 2-2 Summary of Recommended Strategies ............................................................................... 1-2 Trends and Key Performance Indicators ............................................................................. 1-1 City of Austin System Profile ................................................................................................ 2-1 Introduction ............................................................................................................................ 2-1 Water Loss Audit Results .................................................................................................... 2-10 Performance Indicators and Data Validity ......................................................... 2-10 Performance Indicators ...................................................................................... 2-12 Data Validity ........................................................................................................ 2-12 Mayfield ............................................................................................................... 3-10 Davis WTP Summary and Recommendations .................................................. 3-10 Ulrich WTP ........................................................................................................................... 3-12 Ullrich Low Service Pump Station ...................................................................... 3-12 Ullrich Medium Service Pump Station ............................................................... 3-13 Ullrich High Service Pump Station ..................................................................... 3-13 Ullrich WTP Summary and Recommendations ................................................. 3-13 i Davis WTP .............................................................................................................................. 3-5 Handcox WTP ........................................................................................................................ 3-1 Davis High Service Pump Station ......................................................................... 3-7 Davis Raw Water Pump Station............................................................................ 3-5 Handcox WTP Summary and Recommendations ............................................... 3-3 Davis Medium Service Pump Station ................................................................... 3-6 Handcox Raw Water Meters ................................................................................. 3-1 Handcox Finished Water Production Meter 1 ..................................................... 3-2 3.2.2 3.2.3 3.2.4 3.2.5 3.3.1 3.3.2 3.3.3 3.3.4 3.1.2 3.1.3 3.2.1 2.4.2 2.4.3 3.1.1 3.0 Production Metering Analysis .................................................................................................. 3-1 3.1 BLACK & VEATCH | Table of Contents AUSTIN WATER | Water Loss Program Review, Analysis & Optimization 5.3 5.4 6.1 6.2 6.3 6.4 6.5 3.4 Water Exports ...................................................................................................................... 3-14 4.0 Apparent Loss Analysis ........................................................................................................... 4-1 4.1 Customer Metering Inaccuracies ......................................................................................... 4-1 Meter Testing Staffing .......................................................................................... 4-3 Meter Testing Equipment and Methodologies .................................................... 4-3 Meter Testing Reporting ....................................................................................... 4-4 4.2 Systematic Data Handling Errors ......................................................................................... 4-4 Billing Data Investigation ...................................................................................... 4-4 4.3 4.4 Unauthorized Consumption .................................................................................................. 4-5 Apparent Loss Cost ............................................................................................................... 4-6 5.0 Real Loss Analysis ................................................................................................................... 5-1 5.1 City of Austin Leakage Detection ......................................................................................... 5-1 Leakage Detection Staffing .................................................................................. 5-1 Leakage Detection Equipment and Methodologies ............................................ 5-2 Leakage Detection Reporting ............................................................................... 5-4 5.2 Real Loss Component Analysis ............................................................................................ 5-4 4.1.1 4.1.2 4.1.3 4.2.1 5.1.1 5.1.2 5.1.3 5.2.1 5.2.2 Step 1: Background Leakage, Reported Leakage, and Unreported Leakage from Reservoirs ...................................................................................... 5-5 Step 2: Background Leakage on Mains and Services ......................................... 5-6 6.2.1 5.2.3 5.3.1 6.2.2 6.3.1 5.3.2 5.3.3 5.3.4 Actionable Improvement Goals ............................................................................ 6-2 Infrastructure Leakage Index ............................................................................... 6-2 Failure Frequency Analysis ................................................................................... 5-8 Step 4: Unreported Failures .................................................................................. 5-7 Results ................................................................................................................................... 5-8 AW Progress To-Date ............................................................................................................ 6-1 Production Metering .............................................................................................................. 6-3 Target Goals & KPIs .............................................................................................................. 6-2 Awareness, Location and Repair Time Reduction Options .............................. 5-10 Economic Intervention Frequency for Proactive Leak Detection ..................... 5-11 Component Analysis Recommendations .......................................................... 5-12 Real Loss Cost Analysis ...................................................................................................... 5-14 Unauthorized Consumption ................................................................................ 6-12 Systematic Data Handling Errors ....................................................................... 6-12 Real Loss .............................................................................................................................. 6-14 Leak Detection – Distribution ............................................................................. 6-14 Leak Detection – Training .................................................................................. 6-17 ii Apparent Loss........................................................................................................................ 6-8 Production Metering Capital Improvements ....................................................... 6-8 Meter Inaccuracy .................................................................................................. 6-8 Production Data Handling .................................................................................... 6-8 Calibration and Verification Processes ............................................................... 6-3 Secondary Meter Testing Program ...................................................................... 6-4 6.3.2 6.3.3 6.3.4 6.4.1 6.4.2 6.4.3 6.5.1 6.5.2 6.0 Goals and Recommended Strategies ....................................................................................... 6-1 BLACK & VEATCH | Table of Contents AUSTIN WATER | Water Loss Program Review, Analysis & Optimization 6.5.3 Leak Detection – Transmission ......................................................................... 6-17 6.5.4 6.5.5 6.5.6 6.6.1 Pressure Transients ............................................................................................ 6-19 Software and Event Management ...................................................................... 6-20 District Metered Areas (DMAs) and PMAs ........................................................ 6-21 Unbilled Authorized Consumption ...................................................................................... 6-21 Flushing ............................................................................................................... 6-22 Fire Fighting ......................................................................................................... 6-22 Unbilled Unmetered Accounts ............................................................................ 6-22 Annual Water Audit and Validation Training ...................................................................... 6-23 Participation in National Water Loss Control Conferences .............................................. 6-23 Improve Data for Water Audit Input Data Validity Scores ................................................. 6-23 Cost Estimate Tables .......................................................................................................... 6-25 6.6.2 6.6.3 6.6 6.7 6.8 6.9 6.10 LIST OF TABLES Table 3-1 Table 3-2 Table 4-1 Table 4-2 Table 5-1 Table 5-2 Table 5-3 Table 5-4 Table 5-5 Table 6-1 Table 6-2 Table 6-3 Table 6-4 Table 6-5 Table 6-6 Table 6-7 Table 6-8 Table 6-9 Handcox Raw Water Meter Differential Pressure Cell Verification .................................... 3-2 AW Export Volumes ............................................................................................................. 3-14 2022 Customer Metering Inaccuracies as Reported by AW ............................................... 4-2 Meter Test Results by Size: July 2021-2023 ........................................................................ 4-4 AW Leakage Detection Equipment ....................................................................................... 5-2 2022 Tank Overflow Events .................................................................................................. 5-5 Average Water Loss Time for 2021 and 2022 Main Break Events ..................................... 5-6 Service Connection Failures Recorded in 2022 ................................................................... 5-7 Infrastructure Failure Frequency Analysis ........................................................................... 5-8 Current (2022) NRW KPIs and Future Goals ........................................................................ 6-3 Handcox Production Meter Recommendations .................................................................. 6-5 Davis Production Meter Recommendations ........................................................................ 6-6 Ullrich Production Meter Recommendations Summary ..................................................... 6-7 Meter Testing Program Validation Scope and Cost Estimate ............................................ 6-9 Apparent Loss Strategy Costs ............................................................................................ 6-25 Real Loss Strategy Costs .................................................................................................... 6-26 Real Loss Strategy Projected MGD Savings ...................................................................... 6-27 Unbilled Authorized Consumption Strategy Costs ............................................................ 6-28 BLACK & VEATCH | Table of Contents iii AUSTIN WATER | Water Loss Program Review, Analysis & Optimization LIST OF FIGURES Figure 1-1 Figure 1-2 Figure 2-1 Figure 2-2 Figure 2-3 Figure 2-4 Figure 2-5 Figure 2-6 Figure 2-7 Figure 2-8 Figure 2-9 Figure 2-10 Figure 2-11 Figure 2-12 Figure 2-13 Figure 2-14 Figure 2-15 Figure 3-1 Figure 3-2 Figure 3-3 Figure 3-4 Figure 3-5 Figure 3-6 Figure 3-7 Figure 3-8 Figure 3-9 Figure 3-10 Figure 3-11 Figure 3-12 Figure 3-13 Figure 3-14 Figure 3-15 Figure 3-16 Figure 4-1 Figure 4-2 Figure 4-3 Figure 4-4 Figure 4-5 Figure 4-6 Figure 5-1 Austin Water Non-Revenue Water Trends ........................................................................... 1-1 City of Austin Historic Infrastructure Leakage Index (ILI) ................................................... 1-2 City of Austin Water Sources ................................................................................................ 2-1 AWWA Water Balance ........................................................................................................... 2-3 Data Validity Score Example from the AWWA Audit ........................................................... 2-4 AWWA City of Austin Water Supplied .................................................................................. 2-6 AWWA Authorized Consumption .......................................................................................... 2-6 AWWA City of Austin Annual Water Loss ............................................................................ 2-7 AWWA Audit City of Austin Apparent Losses ...................................................................... 2-8 AWWA Audit City of Austin Real Losses .............................................................................. 2-9 AWWA Audit City of Austin Non-Revenue Water Total ....................................................... 2-9 AWWA Audit City of Austin System Data Summary ............................................................ 2-9 AWWA Audit City of Austin Cost Data................................................................................ 2-10 AWWA Audit City of Austin Non-Revenue Water Summary .............................................. 2-10 AWWA Audit City of Austin Key Performance Indicators ................................................. 2-11 City of Austin NRW Components Summary....................................................................... 2-12 AWWA Audit City of Austin Data Validity Score ............................................................... 2-13 Handcox Water Treatment Plan Flow Diagram, May 2020 (Source: Vector Report 2021) ...................................................................................................................................... 3-1 Handcox WTP Finished Water .............................................................................................. 3-3 Handcox WTP Metering Summary Data as of 7/24/23, 7:24 AM....................................... 3-4 Davis Water Treatment Plan Flow Diagram, May 2020 (Source: Vector Report 2021) ...................................................................................................................................... 3-5 Davis Raw Water Meter Flow (%) .......................................................................................... 3-6 Daily Avg MGD Raw Water 1-3 .............................................................................................. 3-6 Davis HSPS Treated Water Flows ........................................................................................ 3-7 HSP 23 Daily Average Flow (MGD) 2022 ............................................................................. 3-8 HSP 24 Daily Average Flow (MGD) 2022 ............................................................................. 3-8 HSP 25 Daily Average Flow (MGD) 2022 ............................................................................. 3-8 HSP 26 Daily Average Flow (MGD) 2022 ............................................................................. 3-9 HSP 23 Daily Average Flow 2023-2024 ................................................................................ 3-9 HSP 26 Daily Average Flow 2023-2024 .............................................................................. 3-10 Davis WTP Metering Summary Data as of 7/24/23, 7:24 AM .......................................... 3-11 Ullrich Water Treatment Plan Flow Diagram, May 2020 (Source: Vector Report 2021) .................................................................................................................................... 3-12 Ullrich WTP Metering Summary Data as of 7/24/23, 7:24 AM ....................................... 3-13 City of Austin 2010-2022 Apparent Losses ......................................................................... 4-1 Customer Meter Inaccuracy 2010-2022 .............................................................................. 4-2 Large Customer Meter Inaccuracy Analysis ........................................................................ 4-3 Billed Metered Consumption (MG/Yr) 2022 ........................................................................ 4-5 Unauthorized Consumption (Gallons) 2022 ........................................................................ 4-6 Cost Trends of Apparent Losses .......................................................................................... 4-6 AW Real Losses ..................................................................................................................... 5-1 BLACK & VEATCH | Table of Contents iv AUSTIN WATER | Water Loss Program Review, Analysis & Optimization Figure 5-2 Figure 5-3 Figure 5-4 Figure 5-5 Figure 5-6 Figure 5-7 Figure 5-8 Figure 5-9 Figure 5-10 Figure 6-1 Figure 6-2 Background, Unreported, and Reported Leakage Visual Examples. .................................. 5-5 City of Austin Mains Failure Frequency 2022 ...................................................................... 5-9 City of Austin Service Connections Failures 2022 .............................................................. 5-9 Reported and Unreported Failure Events 2022 .................................................................. 5-10 Variable Costs of Real Losses for AW ............................................................................... 5-11 Current Real Losses vs. Recoverable Leakage based on Recommended Strategies ............................................................................................................................. 5-12 Additional Recommendations ............................................................................................ 5-13 City of Austin Pressure Management Opportunities ......................................................... 5-14 Cost Trends of Real Losses ................................................................................................ 5-14 Non-Revenue Water Reduction Strategy Overview .............................................................. 6-1 Pressure Transient Monitoring Example............................................................................ 6-19 BLACK & VEATCH | Table of Contents v Abbreviations and Definitions The following acronyms and abbreviations are used in this document. Acronym AWWA AOP BMAC BUAC CMI CRUC CY DVS FWAS Lm ICF ILI Lp IDG M36 Nc NRW SDHE TWDB UARL UC UMAC UUAC VPC WRF Average length of (private) customer service line Interactive Data Grading (in the FWAS) AWWA Manual M36 Water Audits and Loss Control Programs Description American Water Works Association Average Operating Pressure Billed Metered Authorized Consumption Billed Unmetered Authorized Consumption Customer Metering Inaccuracies Customer Retail Unit Charge Calendar Year Data Validity Score (AWWA) Free Water Audit Software Length of mains Infrastructure Condition Factor Infrastructure Leakage Index Number of service connections Non-Revenue Water Systematic Data Handling Errors Texas Water and Development Board Unavoidable Annual Real Loss Unauthorized Consumption Unbilled Metered Authorized Consumption Unbilled Unmetered Authorized Consumption Variable Production Cost Water Research Foundation vi Key Terms Authorized Consumption Unauthorized Consumption Non-Revenue Water Authorized consumption is the volume of metered and/or unmetered water taken by registered customers, the water supplier, and others who are authorized to do so by the water supplier, for residential, commercial, and industrial purposes. Authorized consumption may include items such as firefighting and training, flushing of mains and sewers, street cleaning, public fountains, frost protection, building water, etc. These may be billed or unbilled, metered, or unmetered. Unauthorized Consumption (UC) includes water that is taken in violation of the policies of the water utility. Unauthorized consumption results in uncaptured revenue and understates customer consumption. NRW is the volume of water that is treated to potable standards and pressurized in the distribution system but does not generate any revenue for the water system. The formula for calculating Non-Revenue water is as follows: Non-Revenue Water = Apparent Loss + Real Loss + Unbilled Metered Consumption + Unbilled Unmetered Consumption. Apparent Loss Apparent water losses are non-physical losses; they result from unauthorized consumption (theft of service), inaccurate customer metering, and systematic data handling errors. Recommended Metric: Gallons per connection per day. Real Water Loss Real water loss is the physical loss through leakage on mains or service lines, or tank over-flows. This includes all physical losses from the pressurized system between the point of distribution and the customers’ meters. Variable Production Cost (VPC) is used to apply a value to the real loss volume. The VPC reflects the costs associated with, energy and maintenance costs for transmission and distribution pumping, and chemical treatment costs. Recommended Metric 1: Gallons per connection per day. Recommended Metric 2: Infrastructure Leakage Index. Meter Calibration and Verification (Production Meters) Production meters must regularly be tested to validate their accuracy. Both meter calibration and meter verification compare the measurements of an operative flow meter to a standard flow measurement device. Calibration is more often performed in controlled conditions on a test bench, most notably prior to installation, where deviations in accuracy can be addressed. Verification, which measures and verifies meter accuracy, can be performed on-site, but does not re-calibrate the meters. Recommended Metric 1: Percentage Accuracy of Meter (net after all conversions). vii 1.0 Executive Summary Austin Water (AW) within the City of Austin retained Black & Veatch (B&V) to conduct an analysis of the existing water loss program after staff noted increasing losses in recent years. Black & Veatch (B&V) performed the Water Loss Control Program Review, Analysis & Optimization to address Austin Water’s NRW issues and to meet goals as part of AW’s Water Forward program. This document outlines the analyses conducted and recommendations for future work by AW to monitor, evaluate, and reduce all non-revenue water (including water loss) in the system. Non-Revenue Water (NRW) is water that is treated and pumped into the distribution system but does not generate revenue by being physically lost or not properly accounted for. To address NRW, B&V reviewed the best available data from AW including (but not limited to) meter testing and accuracy, water production volumes and calibration, billing exceptions, and leakage analysis. The team utilized detailed data as well as Texas Water Development Board (TWDB) audits from 2010-2021 to analyze trends in apparent and real losses. B&V synthesized a PowerBI dashboard which displayed trends in both the volume and cost of real and apparent losses. The team also conducted an AWWA Water Audit and a Real Loss Component Analysis to more accurately determine the source(s) of real and apparent loss in the system and potential mitigation strategies. The Water Loss Control Program Review, Analysis, & Optimization utilizes these analysis and the City’s current NRW reduction strategies to develop a 10-year plan of recommended strategies. 1.1 Trends and Key Performance Indicators B&V conducted analysis in 2022 as a focus, but TWDB audits were also evaluated for the period of 2010 through 2022. Non-revenue water trends can be seen in Figure 1-1. Figure 1-1 Austin Water Non-Revenue Water Trends 1-1 This trend analysis does suggest a relatively steady increase in real water loss (leakage – the grey bar) and increasing apparent loss (light blue bar) over the past ten years. This equates to approximately 8,000 million gallons per year of total water loss and to an annual financial cost of approximately $12 million. One of the major metrics that AW is seeking to reduce is its overall Infrastructure Leakage Index (ILI) over the next 10 years. The ILI is defined by the American Water Works Association (AWWA) as the ratio of current annual real losses to unavoidable annual real losses. The 2018 Water Forward plan defined a short- term Infrastructure Leakage Index (ILI) goal of 2.7 by 2020 and a long-term goal of 2.0 from 2040 to 2115. As part of the 2024 update to the Water Forward Plan, AW has adjusted their long-term ILI goal to 3.0. The Austin Water Conservation Plan also projects a short-term ILI goal of 3.31 by 2034. B&V analyzed this water use and loss data to determine the ILI for AW from 2010-2022. As shown in Figure 1-2, AW’s ILI has trended upwards since 2010, remaining above the Water Forward goal of 2.7 since 2013. AW’s ILI in 2022 was 4.1. Figure 1-2 City of Austin Historic Infrastructure Leakage Index (ILI) B&V’s analysis of AW’s historic and current water audit data indicates an increase of losses year over year beginning as early as 2010. This document will outline why these trends are occurring and provide recommendations for addressing the key areas of water loss. 1.2 Summary of Recommended Strategies The focus below is on the four main areas studied during this project. • Production Metering and Calibration • Data Management 1-2 • Real Loss (Leakage) Reduction • Unbilled Authorized Consumption The following summary outlines three recommendations for each of the major project areas. Additional recommendations around the focus areas and data management and standardization of procedures and reporting are outlined in the final recommendations chapter. 1.2.1 Production Metering To improve the accuracy and confidence of the system input volume within the water audit, it is important to ensure that all production flows from the water treatment plants are measured with a flow metering device that is properly calibrated and maintained. 1. Ensure that all production meters are regularly maintained and verified at least annually. a. Resolve (and record resolution for) any meters that test outside of expected ranges (e.g., ±3%). b. Conduct semi-annual calibration on the meters with highest flow volumes. 2. Implement more frequent secondary flow testing (using a second in-line meter) on meters across the system. 3. Refine data trending and analysis dashboards that enable daily review of hourly production data. These dashboards can assist in identifying data anomalies and suspected production meter errors through visualization, trend analysis, and frequent monitoring. This approach will improve the overall accuracy and reliability of the water audit data, which will ultimately lead to better decision-making and improved non-revenue water reduction efforts. As noted in AWWA Manual M36, the production volumes are the most important quantities in ensuring the accuracy of the annual water audit. 1.2.2 Apparent Loss To ensure accurate understanding of apparent loss and to reduce non-revenue water, AW can improve billing and large-diameter meter accuracy reporting. This will enable more accurate understanding and targeting of non-revenue water and optimize system performance. 1. Enhance the large customer meter testing program. This program should consider standardizing annual testing of all meters 3-inch and larger. 2. Create a meter testing database to collect and analyze meter test data in a consistent format over the long term. By implementing a meter testing database, Austin Water can improve the individual meter and weighted (full population) meter accuracy calculations to enable targeting and optimizing of system performance. 1.2.3 Real Loss (Leakage) AW has conducted proactive leakage detection for more than a decade. This has likely been a positive influence in managing real losses (leakage) during this time. However, the performance with respect to water loss reduction volumes continues to be difficult to assess and may be degrading. The following are some improvements which should be initiated to allow further improvement. 1. Improved supervision of contractor-led proactive leakage detection programs by Engineering Services Program Area employees. 1-3 2. Improved data management to record, trend and monitor leakage detection surveying and leaks found and fixed should be developed. a. Performance metrics should be developed, trended and utilized for leakage detection programs going forward. 3. Additional interaction between Austin Water staff within the Operations Program Area and contract teams is recommended to improve validation of leakage detection results and to improve visibility and accountability of the program. 4. To identify economic options for real loss reduction, it is recommended that AW conducts an annual Real Loss Component Analysis using data for main, service line, appurtenance, and reservoir breaks and leaks. These main recommendations should improve efficiency of analysis and operation for implementing and sustaining AW’s leakage control programs. 1-4 2.0 Introduction and Initial Audit Analysis Introduction 2.1 A Non-Revenue Water (NRW) Audit analysis was conducted for Austin Water (AW) in the City of Austin, TX to help understand, target, and recommend methods to control the water losses in the distribution system. This was accomplished by using the standard American Water Works Association (AWWA) Water Audit Spreadsheet (Version 6) and Water Balance through distinct tasks as outlined in this document. The Audit is designed to help determine probable areas of non-revenue water and allow for an initial review of water department practices for water accounting, as well as provide recommended strategies for mitigation. It is especially important to be able to locate areas of water loss in the system including potential leakage and inaccurate meters, as well as potential issues with the accounting and billing data by utilizing an audit for evaluation. B&V staff conducted this audit for Calendar Year 2022 as part of the City of Austin’s Water Loss Program Review, Analysis and Optimization. 2.2 City of Austin System Profile AW serves approximately 1.1 million customers across 548 square miles through more than 250,000 service connections. In 2022, the utility was composed of 4,026 miles of mains with an average operating pressure of approximately 78 PSI. AW supplies all its water from its own sources at three water plants, which accounted for approximately 55,073.17 MG/yr in 2022 with an error adjustment of 1.64%. AW exported 2,950 million gallons/year (MG/yr) with an error adjustment of 2.0% to wholesale customers, bringing its total water supplied for 2022 to 52,983 MG/yr. The distribution system consists of 44 pump stations and 38 tanks and reservoirs across nine different pressure zones. A schematic of the water system in Figure 2-1 indicates the approximate locations of the treatment plants. Figure 2-1 City of Austin Water Sources The three water treatment facilities, Handcox, Davis, and Ullrich, are gravity fed through the Lake Travis and Lake Austin reservoirs, which store water from the Colorado River. These WTPs produce approximately 20%, 30%, and 50% of Austin’s finished water, respectively. AW is capable of processing up to 335 million gallons (MG) of water per day The utility has secured access to these water sources by obtaining water rights and entering a fixed water backup contract with the Lower Colorado River Authority (LCRA). 2-1 2.2.1 AW’s Water Auditing and Loss Control Programs Austin Water has been conducting water audits to the AWWA methodology since the inception of the State requirements back in 2005 and has conducted loss control through leakage detection and meter replacements throughout the water system history. The auditing process has become more active over the past 15 years and AW does have a good understanding of its supply, demand and water loss dynamics. True optimization of a water system with respect to water loss and the wider non-revenue water components does require an active, consistent and dedicated effort. This report and analysis add to that in-house work conducted over the last twenty years. 2.2.2 State Audit Requirements All public water suppliers in Texas with over 3,300 connections must submit an annual water audit of the previous calendar year to the Texas Water and Development Board (TWDB) by May 1. As such, AW has a regulatory requirement to annually report on their water loss performance. The reporting methodology is fundamentally the same as the methodology recommended by the American Water Works Association (AWWA) and much of the data reported is the same. There are some slight differences – notably, the AWWA water audit begins at the point of distribution, whereas the TWDB requires reporting to include production data, or water from the source of supply. As part of this project, B&V imported the 2010-2022 TWDB audits into the AWWA format to compare their reported key performance indicators (KPIs) against national benchmarks from other utilities. This information is presented later in this document. 2.3 Water Loss Audit Approach The Water Loss Audit program is a multi-phase program encompassing a selected group of data and methodology designed to assist the Utility in improving water accountability and optimizing the distribution system’s operational performance. This water audit is a foundation to the Non-Revenue Water (and water loss) reduction program recommendations. The AWWA Water Audit Format was used to track the finished water amounts through the uses of water – metered, unmetered, and potential leakage in the distribution system – to the water customer properties. This analysis allowed for the various segments of water use to be examined based on available data supplied by the utility. The desired end results were to uncover potential areas of water loss that can be mitigated in the short- and medium-term but also provide long-range planning goals to be put into place for sustainability of the system. As shown in the IWA/AWWA Water Balance (Figure 2-2), all water entering a water distribution system can be accounted for as it flows through the distribution system to customers. The most meaningful information developed from a water audit is quantity (gallons) of water loss components shown in the Water Balance and the monetary value of these components. Consequently, utilities can assess the effectiveness of existing water loss management efforts, evaluate the potential for improved performance, and prioritize activities specifically designed to address deficiencies. 2-2 Figure 2-2 AWWA Water Balance The key concept of the water balance shown in Figure 2-2 is to move from left to right as one progresses through the audit process with the knowledge that all columns sum to the same volume. All water can be accounted for, even the losses. Once the losses are quantified, steps can be taken to mitigate them. AWWA uses Water Loss described by Apparent Loss (metering/accounting issues) and Real Loss (leakage) issues. This report is based on the analysis of the water produced and consumed by the City of Austin and its customers. 2.3.1 Outline of AWWA Audit Approach The following tasks were conducted as part of this water audit Task; • Gather Data and System Information • Determine System Input • Determine Authorized Consumption • Determine Apparent Loss • Estimate Real Losses • Quantify Non-Revenue Water • Identify Performance Indicators and Data Validity. • Provide Conclusions • Provide Recommendations for Water Loss Control Initiatives determined by the audit To perform the audit, data from the 2022 TWDB Water Loss Audit Draft Report was input into the AWWA Free Water Audit Spreadsheet (Version 6). As the spreadsheet was completed with input from City of Austin staff, data was then analyzed segment-by-segment and the data was researched and validated. Once the data was verified, grading scores were applied to each of the data entries based on the integrity of the 2-3 information per the Interactive Data Grading criteria contained in the AWWA audit software. Those grading scores were then calculated by the software, using a weighted scale, to create what is known as the Data Validity Score. Data Validity Scores are a way of providing a check on how robust the data used in the audit is. The grade provides a way to check individual data entries, and this helps provide a basis for suggested improvements. At each data entry point this score is input based on answers to specific questions, defined for each individual component of the Audit Spreadsheet. An example is illustrated in Figure 2-3 below. Each data input has its own grading criteria on a scale of 1-10 and the score is derived by completing the Interactive Data Grading questionnaire for each data input in the audit. Figure 2-3 outlines the “volume from own sources” input value from the 2022 water audit analysis. Volume from Own Sources: n Water Imported: n Water Exported: n g 7 g n/a g 4 55,073.717 MG/Yr 0.000 MG/Yr 2,950.349 MG/Yr Austin Water 2022 White = incomplete Orange = complete Use acronyms for navigation go to input AWWA Free Water Audit Software: Interactive Data Grading VOS VOSEA WI WIEA WE WEEA BMAC BUAC UMAC UUAC SDHE CMI UC Lm Nc Lp AOP CRUC VPC FWAS v 6.0 American Water Works Association. Copy right © 2020, All Rights Reserv ed. Volume from Own Sources (VOS) - Data Grading Criteria vos vos.0 Criteria Question Did the w ater utility supply any w ater from its ow n sources during the audit year? vos.1 What percent of ow n supply volume is metered? Yes >99% Select Best-Fit Answers to All Visible Questions For questions 2-10 below : Choose the answ er that applies for those m eters that m easure >90% of the finished w ater volum e. In-situ flow accuracy testing = a test process that confirms the flow measuring accuracy of the primary device (the flow meter), in its installed location, using an independent reference volume. Electronic calibration = a process that checks for error in the metering secondary device(s) and/or the tertiary device(s). Secondary device can include conversion to mA, meter transmitter or similar instrumentation. Tertiary device can include SCADA, historian or other computerized archival system. What is the frequency of electronic calibration? Annually What level of data transfer errors are checked as part of the electronic calibration process? Data transfer errors are checked at secondary device(s) AND tertiary device(s) vos.2 vos.3 vos.6 vos.7 vos.8 vos.4 Is the most recent electronic calibration documentation available for review ? Yes vos.5 What is the frequency of in-situ flow accuracy testing? Less than annual but w ithin last 5 years Is the most recent in-situ flow accuracy testing documentation available for review ? Yes What are the total volume-w eighted average results of in-situ flow accuracy testing (during or closest to audit year)? Have testing and calibration procedures been closely scrutinized for compliance w ith procedures described in the AWWA M36 and/or M33 Manual(s)? Yes Betw een ±3% to ±6% vos.9 Which best describes the frequency of finished w ater meter readings? Continuous vos.10 Which best describes the frequency of data review for anomalies/errors? These can include numbers that are outside of typical patterns, and zero or 'null' values that may reflect a gap in data recording. More frequently than monthly, but not every day FINAL DATA GRADE FOR THIS AUDIT INPUT: 7 acronym key Limiting criteria (see Start Page for details) go to notes Limiting Limiting Figure 2-3 Data Validity Score Example from the AWWA Audit The data grade illustration above demonstrates how questions about each data input are used to define and derive the specific data grade based on the answers. This takes the guesswork out of the data grade assignments. 2.3.2 Gather Data and System Information In March 2023, a data request was submitted to AW. The data was supplied in Excel tables that contained total water produced, amounts of water sold to all the water customers, including: metered water, unmetered water, billed water and unbilled water, physical information on the water system such as miles of water main, numbers of water connections, operating costs of the water utility, etc. This data helped determine how and where water was being used, if it was being accounted for, and/or billed for at each step of the way from production to consumption. 2-4 The Audit spreadsheet was compiled utilizing the information provided. Data was cross checked from dataset to dataset to verify the information. AW also provided historical water audits using the Texas Water Development Board (TWDB) format back to 2010. This information is very similar in structure to the AWWA structure and so was used to develop trends and gain a better understanding of the changes in demands, consumption, and losses over those years. The audit should be considered a “living document” and a valuable tool for overall water loss control planning. The audit process should be performed annually as a way for the utility to review past performance and set new goals. 2.3.3 Determine System Input The first phase of the Water Audit was to evaluate water production through the master finished water meters to ensure the input into the system had been accurately measured and documented in the audit year. All water audits should start with verification of the distribution system input to ensure reliable water production amounts. AW’s supply comes from the Colorado River (Lake Travis and Lake Austin). AW produces all its own water at three water treatment plants (Davis, Handcox, and Ullrich) and does not import from other sources. All three plants were visited during the data collection portion of this project. Data for the selected audit period of January 1, 2022-December 31, 2022 were taken from the 2022 records supplied by AW. This volume was included in the calculation of total Volume from Own Sources (VfOS). 2.3.3.1 Master Meter Accuracy for Volume from Own Sources An important aspect of the water introduced into the distribution system includes whether the production meters are accurate. This is especially important when attempting to calculate water loss in the water system. If the finished water meters are inaccurate, then that inaccuracy will cause the result of the audit to be inaccurate. That inaccuracy can be compounded through the entire audit. It is rare that any production or wholesale meter is 100% accurate. In the audit spreadsheet there is an adjustment for meter accuracy that is applied to the total finished water produced. There are “acceptable” limits to the accuracy level of water meters (such as 98.5%-101.5%), and AWWA has a table of suggested accuracy limits in the M6 manual for water meters for specific types and sizes of water meters. This accuracy limit, however, is intended for customer meters (residential and commercial accounts) and does not always apply to production meters and wholesale flow meters. Production flow meters have no real defined accuracy limits per AWWA, and the accuracy limits can vary per the local or any other regulatory agency, and by meter type. Some jurisdictions are currently looking at defining rules for master meter accuracy limits but as of this report, nothing has been defined. It cannot be overstated that it is in the best interest for utilities to make sure the production flow meters are as accurate as possible for several reasons; the primary reason is that the entire water audit assumes that the water supplied amounts are accurate and can be relied upon. Estimations of master meter accuracy were chosen as 100% accuracy at Handcox and 98% accuracy at both Davis and Ullrich. These estimates were developed by City staff through anecdotal knowledge of the setups and operations at each plant. A weighted average of these values (weighted by flow volumes) allowed a calculation of 98.36% accuracy or under registration by 1.64% from these production meters. Figure 2-4 is a copy of the Water Supplied inputs from the Audit. 2-5 Figure 2-4 AWWA City of Austin Water Supplied 2.3.4 Determine Authorized Consumption Traditionally there are four data inputs within the audit where water has been authorized to be used. The following is how water is normally consumed in a utility. Figure 2-5 shows the four categories of authorized consumption in the AWWA Water Audit Format and AW’s volumes for those categories in 2022. Figure 2-5 AWWA Authorized Consumption 2.3.4.1 Billed Metered Billed Metered Authorized Consumption is water that is metered during consumption by customers and billed according to an approved rate structure. Per a data request submitted to City water staff, Austin meters almost all water use types. Bills are generated based on approximately 250,000 meters as identified from the billing records provided. The total for the Billed Metered Authorized Consumption (BMAC) was 44,290.93 MG in 2022. This is the totalized amount of water that was billed by Austin for the 2022 Audit period. A “lag time” adjustment was not applied to the BMAC total. Data for this calculation was not included in the consumption tables provided. “Lag time” is the period between the time the production meters are read and time the customer billing meters are read. The adjustment allows for the alignment of the two volumes at the beginning of the audit year and at the end of the audit year. AW is in the process of installing an Advanced Metering Infrastructure (AMI) system across all its customers. Once this is complete (due in 2024) then the billing lag will become negligible as the comparison will be enabled on an hourly basis. 2.3.4.2 Billed Unmetered Billed Unmetered Authorized Consumption (BUAC) is water that is billed for but not metered. Examples of this might include such uses as unmetered hydrant uses, landscape or construction crew use, or where water use is estimated based on house size or building size. The total BUAC was 9.625 MG in 2022. 2.3.4.3 Unbilled Metered Unbilled Metered Authorized Consumption (UMAC) water use might include such items as water used by the City such as parks, municipal pools, utility buildings, fire departments where water use is metered, etc. 2-6 but not billed. In AW’s case, this includes three accounts: Texas A&M Forestry Service, Austin Downtown Alliance, and AW accounts. The total unbilled metered volume was 63.619 MG in 2022. 2.3.4.4 Unbilled Unmetered Unbilled Unmetered Authorized Consumption (UUAC) is sometimes hard to develop estimates for. Usually, this area of water use can be attributed to water main flushing, hydrant flushing, firefighting, or a number of other uses where the water is not metered or billed, but the use is authorized. Water utilities can use a “default” value of 0.25% of the Water Supplied that is allowed for this data input for the Water Audit. However, AW did document estimated water use in this category and an estimated volume of 119.723 MG in 2022. This documented use included: work orders for flushing, and fire hydrant testing by the Fire Department (18,000 tests annually). 2.3.5 Determination of Water Loss By taking the Water Supplied and subtracting the Authorized Consumption, the total Water Loss can be determined. The Audit Spreadsheet for total water loss calculation is shown in Figure 2-6. Figure 2-6 AWWA City of Austin Annual Water Loss These losses can now be further defined as “Apparent losses” (accounting or billing errors, meter inaccuracy, etc.) and “Real losses” (water lost to leakage on service lines or water mains). 2.3.6 Determining Apparent Loss Apparent losses are the nonphysical losses that occur when water is successfully delivered to the customer but is not measured or recorded accurately. Apparent losses have several undesirable effects on utility operations. They distort customer consumption data and cost water utilities revenue when accounts are underbilled. Conversely, reductions in apparent losses tend to increase water system revenue from a given water rate structure and improve equity among customers. Apparent losses comprise of three areas: Systematic Data Handling Errors, Meter Inaccuracies, and Unauthorized Use. 2.3.6.1 Systematic Data Handling Errors The City of Austin presently evaluates billing data annually for general errors across all meter types. Specific systematic data handling errors have not been evaluated. AW is in the process of upgrading from a manual-read to an AMI system of meter reading. Even during this transition, meter reading and usage reports are run and analyzed by City personnel to catch any anomalies that may be occurring and address them when located. For the systematic data handling error water audit input, a “placeholder” value was assigned as the Finance Department felt that they had very little error. The water audit software will not allow a zero value; therefore, AW chose a minimum value. This does need to be re-evaluated in future years as it is (in our experience) very rare for utilities to have data handling errors this low. The volume of loss associated with systematic data handling errors was recorded as 0.001 MG/year. 2.3.6.2 Meter Inaccuracies Customer metering inaccuracies are often a major source of Apparent Loss. The water “lost” due to inaccurate meters is not really lost, just the ability to measure consumption properly has been compromised by inaccurate meters. Austin has about 250,385 active metered accounts per the data provided for 2022. 2-7 Meters are generally not 100% accurate throughout a water system. Given the acceptable ranges of meter accuracy for 5/8” displacement meters are 95%-101% for low flows (1/4 gpm), 98.5%-101.5% for intermediate (2 gpm) and high flows (15 gpm), there is a strong likelihood that some water loss is occurring as a result of meter inaccuracy. Other sizes will exhibit similar issues. AW conducted significant meter testing in previous years and this data has been utilized for this audit as well (even though the testing was conducted prior to 2022). Many small meters have been recently replaced as part of AW’s AMI program (Advanced Metering Infrastructure). Large meters are proactively tested approximately every 18 months, although the goal is for annual testing. The percentage of inaccuracy was set at 3.22% by AW in their 2022 TWDB audit. The volume of loss associated with this inaccuracy was calculated as 1,475.735 MG in 2022. 2.3.6.3 Unauthorized Consumption Unauthorized Consumption or theft of service is a tough area to determine and usually requires some estimates to be made. However, reviewing customer service requests and reporting of open hydrants, etc., can usually help validate this information. The International Utility Revenue Protection Agency estimates that many utilities worldwide lose 1% to 2% of their revenue to theft of water (per Neptune Meter Co.). However, this value is expected to be lower in North America. For the audit, the default value from the spreadsheet was used. This default value is set at 0.25% or 110.751 MG/year for the audit year. Typically, theft of water from the water system in a north American utility is not usually a huge loss, in terms of both actual amounts of water or revenue, unless an illegal tap is located, or a commercial account has a meter bypass line open that should be closed and secured. 2.3.6.4 Total Apparent Losses The total for Apparent Losses is shown in Figure 2-7. 1,586.488 Million gallons in 2022 can be attributed to unauthorized uses, metering inaccuracies and systematic data handling issues using the default values and the metering inaccuracy levels. Figure 2-7 AWWA Audit City of Austin Apparent Losses 2.3.7 Determination of Real Losses The determination of Real losses (losses attributed to leakage) was attained by input of all the water supplied, consumption data, and estimated apparent losses into the water audit spreadsheet. The Real loss amounts are obtained by subtracting the Apparent Losses from the Total Losses to yield Real Losses. Real losses are defined as water lost to actual leakage or system overflows and are shown in Figure 2-8. 2-8 Figure 2-8 AWWA Audit City of Austin Real Losses This Real loss calculation of 6,913.450 MG in 2022 can be averaged to a daily loss of 75.66 gallons lost per connection per day. 2.3.8 Determination of Non-Revenue Water In a water system, the utility makes money on the water it supplies and sells to water customers, but it does not make money on lost water, whether apparent losses or real losses. Additionally, the Unbilled Unmetered and Unbilled Metered water uses, although classified as an Authorized use, do not generate revenue. The total amount of Non-Revenue water was calculated based on Total Water Loss added to the Unbilled Metered and Unbilled Unmetered water and was 8,683.279 MG in 2022 as shown in Figure 2-9. Figure 2-9 AWWA Audit City of Austin Non-Revenue Water Total 2.3.8.1 System Data In order to be able to calculate the Performance Indicators for the water system, certain key information is needed about the water distribution system. Such needed information includes miles of water main, average operating pressure of the system, average overall length of service line (from the customer service valve to the water meter) and number of active and inactive connections. This information was part of the Audit questionnaire provided to AW at the beginning of the audit. The data was also cross checked with the data sheets and spreadsheets supplied. These figures were input into the Audit sheet. A summary of the System Data is shown in Figure 2-10. SYSTEM DATA Lm Nc Lp AOP Length of mains: n Number of service connections: n Service connection density: g g 8 8 4,026.0 miles 250,385 62 conn./mile main (including fire hydrant lead lengths) (active and inactive) Are customer meters typically located at the curbstop/property 10 Average length of (private) customer service line: n g (average distance between property line an Average length of customer service line has been set to zero and a data grading of 10 has been applied Average Operating Pressure: n g 8 Yes ft 78.0 psi Figure 2-10 AWWA Audit City of Austin System Data Summary 2.3.8.2 Cost data Cost information for the audit spreadsheet consists of two specific areas, customer retail unit cost and variable production cost. The two costs are used to help calculate the total cost of water lost as well as unit costs on the ‘Dashboard” tab of the audit spreadsheet. The customer retail unit cost of $5.50 /$1000 gallons was applied here. It was calculated by blending the rates supplied from AW finance department records. The rates match the rate structure listed on AW website data for 2022. 2-9 The variable Production Cost was taken from the Annual Report that AW provided for cost of water produced by AW. That figure was $479 / MG in 2022. Figure 2-11 AWWA Audit City of Austin Cost Data The purpose of putting these costs together is so that performance indicators can be derived showing the cost of the specific areas of loss. 2.4 Water Loss Audit Results 2.4.1 Performance Indicators and Data Validity The “Dashboard” tab of the FWAS V6 contains the quantification and analysis of the Performance Indicators for the water system. This is where the Non-Revenue Water Components Summary is illustrated along with the Key Performance Indicators displayed in 8 graphs showing losses quantified in Total losses and Unit Losses. The Non-Revenue Components Summary consists of bar graphs and a short summary table that show levels of volume losses and costs of losses. The Non-Revenue Water (NRW) Summary table for AW’s 2022 audit is shown in Figure 2-12. Figure 2-12 AWWA Audit City of Austin Non-Revenue Water Summary This specific breakdown of costs will help with targeting specific remediation measures that will be discussed in future tasks. However, a quick review indicates that Real Losses (leaks) are costing the utility $3,311,542 annually (using Variable Production Costs), and Apparent Losses (metering/accounting and billing issues) are costing the utility $8,715,054 annually. The Key Performance Indicators (KPIs) in Figure 2-13 offer a perspective of looking at the losses in terms of normalized metrics obtained through the AWWA Water Audit Reference Dataset (WARD). Percentiles for several of the KPIs allow utilities that complete the audit to gauge their performance. The WARD includes Level 1 validated water audits for calendar year 2018 from 1,124 utilities in Quebec, Canada, and the states of California and Georgia. This comparison presents the losses so that these metrics are consistent for each water system that conducts an audit. The top row indicates the Loss Costs Rate in Total costs, then by Apparent losses (metering & billing issues) and then by Real Losses (leakage). The next row indicates the losses in terms of unit losses. The Apparent and Real loss unit is based on the number of connections and not the number of meters. 2-10 Figure 2-13 AWWA Audit City of Austin Key Performance Indicators AW falls above the 90th percentile for both unit apparent costs and apparent loss cost rate. However, as this data was developed for the 2022 Audit, these are lagging indicators. AW has already put significant efforts in place to further reduce apparent losses. AW will need to reduce their unit real losses from 75.6 gallons/connection/day to 55.60 gallons/connection/day to reach goals defined in Section 6.2. A calculation is then made based on the physical parameters of the system for the Unavoidable leakage. This unavoidable leakage equates to leaks that every water system will have despite all reasonable efforts to stop them. The Unavoidable Annual Real Losses (UARL) is a theoretical number defined as the technical low limit of leakage that could be achieved if all available leakage technology were to be applied to the distribution system to stop leakage, based on the baseline data of the system. The math used to determine the UARL is indicted below. UARL (gallons/day) = (5.41Lm + 0.15Nc + 7.5Lc) x P 2-11 Where: Lm Nc Lc P = length of mains (miles) = number of service connections = total length of customer service lines (miles or km) or = Nc multiplied by the average distance of customer service line, Lp (miles) = Pressure (psi) By taking the calculated Real losses for the year (Current Annual Real Losses or CARL) and dividing that by the Unavoidable Annual Real Losses (UARL), a ratio is calculated called the Infrastructure Leakage Index or ILI. The ILI is a Benchmarking indicator that indicates the performance of the Utility for real water loss, considering all the variables as stated above in the UARL math. It is unique for each utility since the math used is derived for each utility’s individual characteristics. The ILI for Austin is calculated as 4.1 in 2022. The ILI can be used to help determine what Real losses the Utility has that are truly recoverable if an aggressive leak detection and leak prevention program were applied to the system. 2.4.2 Performance Indicators With the Calculated ILI at 4.1, AW is operating in what could be considered a workable position, but with potential for real water loss reductions from leakage. The apparent water losses measured at 17.4 gallons per connection per day also suggest potential for loss reductions. There are several issues with some of the data as well. When these items are clarified that will more than likely alter the picture slightly once this data is refined. However, there is almost certainly potential for NRW reduction, given that about 8,683 MG of the water pumped is calculated as Non- Revenue Water. The Real loss accounts for about 6,913 MG of the total loss and the Apparent loss accounts for about 1,586 MG of the total loss. The Dashboard from the audit software shown in Figure 2-14 gives a view of the operational conditions of the water system per the audit. The volume chart clearly demonstrates the spread of the losses by volume and cost. Figure 2-14 City of Austin NRW Components Summary 2.4.3 Data Validity Data Validity Grades are assigned for each of the 19 audit inputs by answering a set of specific questions for each data input. The purpose behind the Data Validity Grading is to demonstrate how robust the data supplied for the audit is. It serves as a self-check to make sure the audit was supplied with the best available data AW had at that given point in time when the audit was being performed. The criteria for assignment of the grading scores is set so that the Utility can have the data “validated” with the end aim of using the grades as a tool for self-improvement. 2-12 There are five tiers defined for the aggregated Data Validity Score. Each tier has a set of generalized suggested activities for Water Loss Control Planning. These suggested activities will assist AW in setting reachable goals in a step-by-step process. AW can expand on these goals depending on their individual needs and ability to fund the activities. 2.4.3.1 Validation Score This score is the total of the scores assigned to each component of the audit to describe the confidence and accuracy of the data input into the system. The assignment of validity scores was based on experiences with other water systems and knowledge of how the Audit format works as well as using the guidelines set in the Audit format Grading Matrix. For each component, there is a corresponding listing in the Grading Matrix (supplied in the Excel Water Audit Software). Figure 2-15 AWWA Audit City of Austin Data Validity Score The Audit validation score was 77 out of 100 for 2022. Leaders from the AWWA Water Loss Control Committee suggest that it is rare that a validity score of over 90 (Tier Level 5) is ever achieved. To attain that high of a score, the water system would need to be up to date, robust, and qualify as a “world class water system” with all the latest technology and practices applied for water data management. The quality and depth of the data AW supplied for this audit was extensive which contributed to this score. 2-13 3.0 Production Metering Analysis Evaluating finished water production amounts ensures that AW is using reliable and accurate water volumes in the water audit. AW production meters at Handcox were estimated at 100% while Ullrich and Davis were estimated at 98% for the 2022 audit. These estimates were based on limited testing to provide a baseline for this analysis. these plants from March 2021 Production meters are owned by AW and electronically calibrated at least annually. A partial set of physical flow testing was conducted in 2021 by Chiang, Patel & Yerby (CP&Y) and Vector Controls on production meters. Vector Controls visited to conduct calibration/verification and validation of production meters. Not all the meters were able to be tested however, so the work was of limited value. The meter accuracy percentages listed in the subsequent sections are from the 2021 Vector Report. Since the report was published, AW has replaced its medium service meters at Davis. AW performs their own verification at these meters as well (annually or semi- annually depending on the meter and the plant). This is conducted through an in-field verification methodology, which is not of the same accuracy as laboratory calibration. AW utilizes venturi meters for measurement in some of the finished water volumes and these meter differential pressure cells were calibrated and verified. to June 2021 Due to the importance of the production volume input and its overall contribution to understanding total system NRW, B&V has analyzed AW’s production meters and provided recommendations for immediate in- line secondary flow testing. Utilizing a secondary in-line flow meter in the field allows AW to identify meters with potentially degrading accuracy. 3.1 Handcox WTP At Handcox WTP, two raw water production meters measure flow from Lake Travis and one finished water meter measures flow sent to distribution. Handcox WTP accounts for approximately 20% of AW’s total production of finished water. Figure 3-1 shows a schematic of the Handcox WTP. Figure 3-1 Handcox Water Treatment Plan Flow Diagram, May 2020 (Source: Vector Report 2021) 3.1.1 Handcox Raw Water Meters The two raw water meters, UFC1 and UFC2, are Venturi flow meters on 48” lines. AW verifies calibration of these meters annually. The Raw Water production meter differential pressure cells were verified in January of 2023, as shown in Table 3-1. 3-1 Table 3-1 Handcox Raw Water Meter Differential Pressure Cell Verification (FIT-108) UFC1 Flow Range = 0 – 56.36 in H2O = 0 – 40 MGD Transmitter Input Transmitter Output Notes: 0% 25% 50% 75% 0% 25% 50% 75% 0.00 in 3.53 in Initial mA 4.00 Final mA 4.00 Initial mA 7.96 Final mA 7.96 14.09 in Initial mA 12.00 Final mA 12.00 No Changes Needed 31.71 in Initial mA 15.98 Final mA 15.98 100% 56.36 in Initial mA 19.99 Final mA 19.99 (FIT-109) UFC2 Flow Range = 0 – 56.58 in H2O = 0 – 40 MGD Transmitter Input Transmitter Output Notes: 0.00 in 3.54 in Initial mA 3.99 Final mA 3.99 Initial mA 8.00 Final mA 8.00 14.15 in Initial mA 12.01 Final mA 12.01 No Changes Needed 31.83 in Initial mA 16.02 Final mA 16.02 100% 56.58 in Initial mA 20.02 Final mA 20.02 The verification results suggest that the differential pressure cells were performing adequately and very close to the expected range during the calibration. The variation between expected and actual was less than 1%. In development of the 2021 Vector Report, these meters were tested with a secondary ultrasonic flow meter, the Endress+Hauser Proline Prosonic 93T, upstream of the respective meter. The report provided test data with the following accuracy ranges: • UFC1 = -9.39% accurate • UFC2 = -13.87% accurate Both UFC1 and UFC2 were reported to be under registering their flow capacities and operating well outside of the acceptable range of +/- 5%. 3.1.2 Handcox Finished Water Production Meter 1 Located underground is one electromagnetic flow production meter, called the “TAP” flow meter by AW staff. This meter measures finished water on a 42” line as shown in Figure 3-2. 3-2 Figure 3-2 Handcox WTP Finished Water The finished water production meter was calibrated on 11/03/2022 per the Hexagon Calibration Testing report. However, the Hexagon report only indicated the test was completed, and there was no identifiable information with respect to the verification or calibration conducted. Testing for the 2021 Vector Report utilized a GWF Model Ductus M test meter for validation, the results of which provided an accuracy range of -0.84% for the Handcox finished water meter. The Vector Report suggested that there were no accuracy issues with this meter. 3.1.3 Handcox WTP Summary and Recommendations Comparing raw water intake and finished water production, Figure 3-3 shows a difference of 13.8% throughout the treatment process from May 2021 to April 2023. In the data provided, it was observed that the volumes for RWF 1 and 2 were provided separately, as well as with a combined value. The sum of RWF 1 and 2 did not equal the reported volume of finished water, so B&V utilized the sum value of RWF 1 + RWF 2 to calculate finished water volumes. 3-3 Figure 3-3 Handcox WTP Metering Summary Data as of 7/24/23, 7:24 AM These differences in measured volumes at Handcox could be attributed to treatment processes such as filter backwashing, surface water evaporation from open-air basins, and line breaks throughout the system. Conventional plants utilize anywhere between 5%-10% of the plant’s intake for treatment purposes, which is in line with AW’s usage. This indicates other areas of potential loss, such as metering issues or evaporation in storage. Recommended strategies for raw and finished water meters are shown in Table 6-2 and indicates the need for secondary flow testing to validate meter accuracy and related flow volumes. 3-4 3.2 Davis WTP The Davis WTP has six raw water intake pumps at Lake Austin, and finished water is distributed through five medium service pumps and six high service pumps, each individually metered. Davis WTP accounts for 30% of AW production. A schematic of the Davis WTP is shown in Figure 3-4. Figure 3-4 Davis Water Treatment Plan Flow Diagram, May 2020 (Source: Vector Report 2021) Notes: 1. The meter on the Mayfield line is now in service. 2. The MSPS shown here has been replaced by a new pump station. 3.2.1 Davis Raw Water Pump Station Six pumps intake raw water from Lake Austin and split into three 48” headers that enter the raw water valve vault. There are electromagnetic flow meters (Raw 1-3) on each of the three 48” lines. There is also one ultrasonic flow meter attached to a 16” line (Raw 4). During development of the 2021 Vector Report, Raw 1-3 were not tested with secondary flow meters because the valve vault could not be accessed. The graphics shown in Figure 3-5 and Figure 3-6Figure 3-6 Daily Avg MGD Raw Water 1-3 outline which flow meters are most actively used on the piping to individual rapid mix basins, rather than meters placed directly after the low service pumps. AW utilizes Rapid Mix 3, which has a capacity of 70 MGD, as the primary basin 3-5 (and primary meter) during normal times of production and demand. Rapid Mix 1 and 2 have a capacity of 60 MGD each but are only utilized when increased capacity is required. Figure 3-5 Davis Raw Water Meter Flow (%) Through conversations with AW, B&V concluded that raw water pumps were installed with a dead band instrument that silences small changes up to 0.2 MGD. Since the Raw Water pumps flow to rapid mix basins, the flow rates do not show demand fluctuations as expected in other pump stations. Figure 3-6 Daily Avg MGD Raw Water 1-3 The Vector Report also notes that Raw Water Meters 1-3 passed meter verification and did not indicate an accuracy range for each meter. 3.2.2 Davis Medium Service Pump Station The Davis Medium service pump station is a new facility commissioned in December 2023. The meters for Davis were calibrated on 12/28/2021 on the old pump station prior to their installation per the InforEAM Testing report. This InforEAM report only indicated the test was completed, and there was no identifiable information with respect to the verification or calibration recorded. As a result, four meters or 20% of flow were not tested by Vector. The medium service pump stations use venturi flow meters. The results of the 2021 Vector Report were as follows: 3-6 • MSPS 13: 3.01% • MSPS 12: -3.34% • MSPS 17: 8.06% 3.2.3 Davis High Service Pump Station There are six 24” high service lines at the Davis WTP that are fitted with Ultrasonic Flow meters. An example sequence of meter readings is indicated in Figure 3-7. Four of the six meters at Davis HSPS experienced flatlining in 2022. Flatlining is where the meter does not measure to its full range due to technical or setup issues and so under reports the actual flow. Multiple Meters at Davis WTP were flatlining for extended periods of time in 2022. B&V confirmed flatlining has occurred due to power limitations and calibration of meters during initial installation. “Dampeners”, as described by AW staff, were installed on HSP’s to achieve the desired flow range registering on each meter. Austin identified dampeners on HSPs 23 and 26, which were subsequently removed in 2024. Figure 3-7 Davis HSPS Treated Water Flows The flatlining occurring at Davis HSPS occurred on HSP 23, HSP 24, HSP 25, and HSP 26. All four pumps have a flow capacity of 22 MGD when in use, however Figure 3-8 through Figure 3-11 show that the high service pumps reach an average maximum flow of approximately 19.50 MGD. The flatlining occurred throughout the year at Davis. HSP 23 flatlined intermittently throughout the entire year. Figure 3-8 indicates that HSP 23 flatlined most consistently October through December. HSP 24 began flatlining most consistently in August through September (Figure 3-9). HSP 25 experienced the most severe flatlining at Davis WTP. Figure 3-10 indicates that HSP 25 read 19.50 MGD from May-July 2022, despite a capacity of 22 MGD. This flatlining occurred intermittently again from July through December. 3-7 Figure 3-8 HSP 23 Daily Average Flow (MGD) 2022 Figure 3-9 HSP 24 Daily Average Flow (MGD) 2022 Figure 3-10 HSP 25 Daily Average Flow (MGD) 2022 3-8 Figure 3-11 HSP 26 Daily Average Flow (MGD) 2022 There were several flatlining issues which were researched during the project by AW staff. These were addressed in 2024 and the flatlining does appear to have been resolved as shown in Figure 3-12 and Figure 3-13. Re-evaluation of the data for previous years was discussed, but not re-calculated due to the complexity of the calculations for this project scope. It was noted that this discrepancy would add additional water to the finished water production inputs from the Davis WTP for years prior to 2024, which would result in increased NRW, all other things being equal. Figure 3-12 HSP 23 Daily Average Flow 2023-2024 3-9 Figure 3-13 HSP 26 Daily Average Flow 2023-2024 In addition, the Vector Report from 2021 indicated the following flow test results (inaccuracy) for the six HSPS Lines at Davis WTP: • HSPS 21: 1.08% • HSPS 22: 8.69% • HSPS 23: -4.49% • HSPS 24: 1.70% • HSPS 25: -2.33% • HSPS 26: -0.93% High service pump stations 22 and 23 were over and under-registering respectively according to the 2021 Vector Report. This, as well as persistent flatlining of meter readings across the water treatment plant suggested that relatively significant volumes of finished water may not have been accounted for in years prior to 2024. 3.2.4 Mayfield While not a major contributor to the finished water volumes for AW, the Mayfield line pulls up to 33 GPM from a connected distribution line for plant processes. AW began metering the Mayfield line in 2023. 3.2.5 Davis WTP Summary and Recommendations According to internal data provided by AW, the Davis Water Treatment Plant treated more water than it withdrew from 2019 to present. AW has narrowed down this issue to be primarily attributed to Instrumentation & Controls (I&C) and/or SCADA issues within the DWTP. Figure 3-14 Davis WTP Metering Summary Data as of 7/24/23, 7:24 AM shows Raw Water, as well as Medium and High Service flows, as well as % Raw Water for each of these services. From May 2021 to May 2023, Davis WTP reportedly treated anywhere between 4%-13% more water than it withdrew. As noted, this could be attributed to the I&C and/or SCADA issues at the WTP or volume accounting processes. Overall, approximately 72% of flow on meters at Davis WTP were testing +/-5%. However, historic reporting from medium service is not relevant, as none of the new meters on the medium service facility have been tested. 3-10 Figure 3-14 Davis WTP Metering Summary Data as of 7/24/23, 7:24 AM As evidenced in the previous discussion, the meters at Davis WTP appeared to have difficulties with measurements and controls and operating structures. Some of these issues appear to have been addressed in early 2024. Recommended strategies for raw and finished water meters are shown in Table 6-3. 3-11 3.3 Ulrich WTP Ulrich Water Treatment Plant has three raw water meters, six high service meters, and four medium service meters. Ullrich accounts for approximately 50% of AW production. However, Ullrich’s Raw Water 2 and 3, as well as Medium Service Pump Station were not tested for the Vector Report. Figure 3-15 Ullrich Water Treatment Plan Flow Diagram, May 2020 (Source: Vector Report 2021) 3.3.1 Ullrich Low Service Pump Station Ullrich WTP has two 54” raw water lines and one 48” line with Venturi flow meters at Low Service Pump Station 1. Raw Water 1--Low and High were tested using an Endress+Hauser Model 93T validation test meter. Raw Water 2 and 3 did not have validation test results in the 2021 Vector Report. Vector Validation Test Results: • Ullrich Raw Water 1 High and Low: 12.24% 3-12 The verification calibration results indicate that both high and low raw water meters were testing well above of the acceptable range at the time of the testing. 3.3.2 Ullrich Medium Service Pump Station The four medium service pump stations at Ulrich are 24” lines with Venturi flow meters. Flow sensors were replaced in 2021/22, but these meters were not tested by Vector. 3.3.3 Ullrich High Service Pump Station The High Service Pump Station at Ullrich has six venturi flow meters, which range from 6” to 36” which were tested during the vector study. • HSPS 1: -4.46% • HSPS 2: -3.05% • HSPS 3: -11.51% • HSPS 4: 16.57% • HSPS 5: 3.16% • HSPS 6: 13.02% • HSPS 7: -19.08% All seven high service pump station meters tested outside of the acceptable range of +/-3% as indicated on the 2021 Vector report. 3.3.4 Ullrich WTP Summary and Recommendations From May 2021 to May 2023, the Ullrich WTP experienced around 7% loss within the treatment process. 40% of volume on meters tested at Ullrich WTP are testing >+13%. Based on the verification and calibration results, as well as the calculated apparent losses from the treatment processes. Table 6-4 outlines the strategies recommended to AW to further test and verify their production meters. Figure 3-16 Ullrich WTP Metering Summary Data as of 7/24/23, 7:24 AM 3-13 3.4 Water Exports AW exported 2,950 MG to their Wholesale customers from January to December 2022. A list of wholesale customers is shown in Table 3-2. Table 3-2 AW Export Volumes ENTITY TOTAL GALLONS (JAN 2022 – DEC 2022) CREEDMOOR MAHA WATER SUPPLY CO 74,891,800 AQUA UTILITIES INC CITY OF ROLLINGWOOD CITY OF SUNSET VALLEY HIGH VALLEY WATER SUPPLY CORP MARSHA WATER SUPPLY CORP NORTH AUSTIN MUD #1 NORTHTOWN M U D SHADY HOLLOW M U D SWWC SERVICES INC TRAVIS COUNTY WCID # 10 VILLAGE OF SAN LEANNA 181,312,300 161,869,100 94,869,200 4,931,300 11,888,900 429,835,400 324,146,000 206,915,200 89,733,000 920,297,000 3,964,000 2,950,349,200 WELLS BRANCH MUNICIPAL UTILITY DISTRICT 445,693,000 WINDEMERE UTILITY COMPANY 3,000 TOTAL These meters should also be considered for analysis and testing in future studies. 3-14 4.0 Apparent Loss Analysis Apparent water losses are non-physical losses; they result from unauthorized consumption (theft of service), inaccurate customer metering, and systematic data handling errors. Within the AWWA audit methodology, the components of real losses are not calculated directly; instead, real loss is a balancing volume once all other volumetric components have been measured or estimated. The AWWA audit methodology requires input for the three components of apparent loss, which are outlined in the following sections. In 2022, AW experienced 1,586 MG of apparent losses as reported in their 2022 TWDB Audit. B&V analyzed AW’s historic TWDB audits from 2010-2021 to understand how AW’s apparent losses have changed over time. The unit apparent losses were calculated for AW and compared these volumes to the Water Audit Data Initiative (WADI) median. WADI is a 2018 dataset compiled to compare water loss across North American utilities. Figure 4-1 City of Austin 2010-2022 Apparent Losses AW has seen an increase in annual losses from 2018-2022 with unit apparent losses peaking at 18 gallons/conn/day in 2020 (Figure 4-1); this increase can be attributed to the 2019 meter testing program, which led to a more accurate dataset. However, AW’s unit annual real losses have remained well above the WADI median of 5.3 gallons/conn/day. AW’s total reported volume of losses due to customer metering inaccuracies, systematic data handling errors, and unauthorized consumption was reported as 1,586 MG in 2022. 4.1 Customer Metering Inaccuracies Since the implementation of AW’s system-wide meter accuracy study in 2019, AW has targeted the replacement of outdated or inaccurate meters. The 2022 AW meter testing, shown in Table 4-1 reports an average customer metering inaccuracy of 3.22%. It is important to note that AW only currently tests meters below 2” at customer request. 4-1 Table 4-1 2022 Customer Metering Inaccuracies as Reported by AW METER SIZE 2022 METERED VOLUME (GALLONS) % OF TOTAL GALLONS METER ACCURACY WEIGHTED AVERAGE METER INACCURACY 1 1/2" 2,594,013,000 15,428,108,300 3,908,308,100 2,123,409,100 6,049,249,500 2,733,306,200 3,073,964,300 3,248,055,600 2,911,173,800 4,003,832,800 913,186,600 5/8" 3/4" 1" 2" 3" 4" 6" 8" 10" 12" 32.84% 8.32% 4.52% 5.52% 12.87% 5.82% 6.54% 6.91% 6.20% 8.52% 1.94% 94% 98% 97% 98% 98% 98% 98% 98% 98% 98% 98% 30.94% 8.17% 4.40% 5.43% 12.63% 5.70% 6.41% 6.77% 6.07% 8.35% 1.90% 96.78% 3.22% TOTAL 46,986,607,300 100.00% Average Customer Meter Accuracy Average Customer Meter Inaccuracy Historic TWDB audits from 2010-2022 record reported customer meter inaccuracies, as shown in Figure 4-2. The increase in CMI from 2018-2019 is due to improved reporting practices and extensive testing in those years by AW on their customer meters. AW is replacing smaller meters to transition to Advanced Metering Infrastructure (AMI) through the My ATX Water program, resulting in anticipated changes in future customer metering inaccuracy. Figure 4-2 Customer Meter Inaccuracy 2010-2022 4-2 For 2022, B&V calculated the weighted average of customer meter accuracies by utilizing raw meter testing data provided by AW. The team performed an anomaly analysis to screen the data to remove any duplicate and inconsistent readings, with the purpose of improving data quality to better understand the average meter inaccuracy. Figure 4-3 shows the results of B&V’s analysis which indicates an average inaccuracy of 3.06% and a weighted inaccuracy of 2.88% for meters above 3”. The weighted inaccuracy is obtained by taking the average inaccuracy and applying a volumetric weight based on the volume of water billed from that meter size. Figure 4-3 Large Customer Meter Inaccuracy Analysis 4.1.1 Meter Testing Staffing AW utilizes both its own staff and Vanguard Utility Services to perform its meter testing throughout the system. AW performs small meter testing and replacement and utilizes Vanguard to assist in testing meter accuracy for approximately 2,500 large commercial and multifamily customers. Large commercial and multifamily meters account for approximately 40% of AW’s revenue. This testing contract expires in December of 2026. Vanguard was also contracted to perform large meter replacement services to help in replacing the 450 large diameter meters of the nearly 250,000 analog meters scheduled for replacement. This contract began in December 2020 and ended in December 2023. 4.1.2 Meter Testing Equipment and Methodologies Vanguard and AW perform volumetric flow testing to verify meter accuracy. Vanguard performed testing for meters 3” and greater. AW performed a system-wide meter accuracy study in 2019 and regularly tests smaller customer meters at customers’ requests. Volumetric flow testing gauges a meter’s accuracy by passing a known volume of water through the meter and comparing it to the volume measured by the meter. The volumetric flow testing occurs in-situ at the site of installation using a test truck that is compatible with up to four-inch pipes and meters. The test truck is connected to a test port on the water meter. This is connected to a hose which is connected into the validated flow meter. This process is repeated for a range of flow volumes and allows for testing of large meters without having to remove, transport, lab test, and reinstall these meters. For smaller meters, AW utilizes a Mars Gravimetric Test Bench, which is located at the Webberville Service Center. Here, AW removes meters from their installation site and tests units en-masse. This process allows AW to test up to 10 meters at a time. 4-3 4.1.3 Meter Testing Reporting Meter testing results were received indicating the meter testing methodology, and tester assigned. All data is self-reported by the tester, whether it be an AW employee or Vanguard. B&V reviewed AW’s meter testing data from July 2021 to July 2023, as shown in Table 4-2. Testing data included meter type, number of tests, and tester assigned to the meter. Accuracy testing methodologies were provided by AW for Hersey, Badger, and Sensus customer meters. B&V found that tests were inconsistently applied compared to the provided testing methodologies. For example, required meter testing frequencies were inconsistent for the corresponding meter type and size, leading to a discrepancy in meter testing results by both AW and Vanguard. Table 4-2 Meter Test Results by Size: July 2021-2023 Meter Size 0.625 0.75 1 1.5 2 3 4 6 8 10 12 Total Unique Meters Tested 158 7 7 2 5 793 508 309 273 94 3 2,159 Total Inspections 474 21 21 6 15 4,863 3,045 2,089 1,703 1,023 9 13,269 Inspection PASS 252 15 18 6 3 3,388 2,232 1,656 1,482 799 9 9,860 Inspection FAIL 222 6 3 - 12 1,475 813 433 221 224 - 3,409 4.2 Systematic Data Handling Errors Systematic Data Handling Errors (SDHE) lead to apparent loss caused by accounting omissions, computer programming errors, gaps in policy, procedures, permitting/activation of new accounts, and any type of data lapse that result in under-stating or over-stating customer consumption. A “placeholder” value was assigned to the 2022 audit as staff reported that they had very little error in this category. The water audit software will not allow a zero value; therefore, AW chose a minimum value. This does need to be re-evaluated in future years as it is (in our experience) very rare for utilities to have data handling errors this low. The volume of loss associated with systematic data handling errors was recorded as 0.001 MG/year. 4.2.1 Billing Data Investigation AW’s Water Loss Calculations Worksheet for 2022 indicates that the total volume billed by AW in 2022 was 44,290 MG as shown in Figure 4-4. 4-4 Figure 4-4 Billed Metered Consumption (MG/Yr) 2022 4.3 Unauthorized Consumption Unauthorized Consumption (UC) includes water that is taken in violation of the policies of the water utility and may include: • Illegal connections; • Open bypasses; • Unknown meters; • Water withdrawn illegally from fire hydrants; • Unauthorized connections into (unmetered) fire lines; • Vandalized or bypassed consumption meters; • Tampering with metering or meter reading equipment; • Unauthorized opening of intentionally closed valves or curb stops on customer service piping; • Unauthorized opening of intentionally closed valves to neighboring water distribution system designed for emergency use. Unauthorized consumption results in uncaptured revenue and understates customer consumption. From 2010-2019 AW reported calculated volumes of unauthorized consumption ranging between 102-156 MG/year as shown in Figure 4-5. In 2020, AW began utilizing the default value of 0.25% of billed authorized consumption volume to determine their unauthorized consumption, which was 111 MG in 2022, an increase from 102 MG in 2021. 4-5 Figure 4-5 Unauthorized Consumption (Gallons) 2022 4.4 Apparent Loss Cost Figure 4-6 Cost Trends of Apparent Losses losses, which The cost of apparent losses was analyzed utilizing AW’s customer retail unit charge per 1,000 gallons for 2010-2022. In 2022, AW experienced approximately $8.7 million in apparent is approximately $500,000 more than in 2021. This value should be decreasing with the large-scale replacement of meters currently ongoing, but this will need to be evaluated further in future years. There was a large increase noted in 2019, this was due to better data which was derived from the extensive meter accuracy testing that was conducted at that time. This work (and the understanding that these losses were extensive) drove the meter replacement program which is actively nearing completion in 2024. It is expected that AW will see a significant reduction in apparent loss costs in future audits. 4-6 5.0 Real Loss Analysis Real water loss is the physical loss through leakage on mains or service lines, or tank over-flows. This includes all physical losses from the pressurized system between the point of distribution and the customers’ meters. Real losses represent water that has been pressurized and treated but does not reach the customer; therefore, the Variable Production Cost (VPC) is used to apply a monetary value to the real loss volume. The VPC reflects the costs associated with any water purchase, energy costs for distribution pumping, chemical treatment costs, and maintenance of the equipment used. B&V performed two separate analyses to determine the approximate rate, volume, and cost of the real losses. The historic TWDB audits from 2010-2022 were analyzed to determine the volume of real losses over time, and how these losses are reported year over year. Figure 5-1 shows the total and unit real losses for AW and compared these volumes to the Water Audit Data Initiative (WADI) median. In 2022, AW reported 6,913 MG of real losses or 76 gallon/conn. per day. B&V then performed a real loss component analysis to validate the volume of real losses through leakage detection and repair data. Figure 5-1 AW Real Losses The component analysis (see Section 5.2) is used to gain an understanding of real losses with more accuracy than a basic system audit, where the remainder after water supply, demand and apparent losses are calculated is apportioned to real loss. The Component Analysis is a mid-level analysis with more detail than the audit, but less detail as compared to District Metering or field-based analysis. 5.1 City of Austin Leakage Detection 5.1.1 Leakage Detection Staffing AW utilizes its own Leakage Detection staff to primarily respond to reported leaks; however, due to the growing size and scale of the system, AW has sought third party contractors to ensure reliable proactive leakage detection. AW entered multiple contracts with Xylem to fully cover their entire system proactively over time. Through Xylem, Wachs Water Services conducts leak detection and reporting throughout the system. Wachs is contracted to survey approximately 500 miles of pipe per year. Xylem has also been contracted to conduct large diameter leak detection and assessments. 5-1 AW currently has five full time and one part time staff on their in-house leakage detection team, as well as nine line-location staff. The leak detection and line locator teams are a multi-responsibility team, actively assisting in water sampling, flushing, non-leak related investigations, and line locating for AW. This is not uncommon, although it can reduce team effectiveness. The AW leakage detection team receives service calls from the public leakage reporting line, from the line location team and directly from AW customers. A team of two to three team members can respond to a call at any given time. The team’s goal is to inspect 150 miles of line proactively per year in addition to their reactive responsibilities. In 2022 they were able to survey 147 miles. 5.1.2 Leakage Detection Equipment and Methodologies AW and Wachs use various devices to detect leaks. Leak detection on smaller diameter lines is conducted using an array of ground microphones, correlators, and acoustic loggers. AW’s leakage detection equipment is listed in Table 5-1. Wachs utilizes two staff in Austin (although not on a permanent basis). The team investigates using visual inspection and an L-mic ground microphone. If there is a potential leak, the area is marked using the Collector App for ArcGIS. The team will then follow-up and go out to find specific leaks using more advanced technology. This includes the SEBA KMT Hydrolux HL7000 and HL6000 PC correlators. Xylem utilizes the Sahara Inline tethered inspection and the SmartBall Inline Free-Swimming Inspection platforms for large diameter leak investigations. Table 5-1 AW Leakage Detection Equipment EQUIPMENT TYPE MANUFACTURER MODEL INVENTORY Ground Microphone Subsurface LD-18 Ground Microphone Fluid Conservation X-Mic¹ Correlator Correlator Subsurface LD-2500¹ Systems FCS 6 2 1 2 2 Tri-Cor Touch Leak Finder ST Correlator Echologics Logger FCS Permalog + 119 ¹ Product has been discontinued Austin is installing 250,000 digital meters, as part of the My ATX Water Program. Besides providing usage metrics and conservation tips, the smart meters will actively report leaks, and failures on the customer side of the meter. These are not considered further in this section as the fact that they identify leakage on the customer-side of the meters means that these are not considered real losses within the distribution system as estimated in the AWWA water loss methodology. 5-2 B&V had the opportunity to join the leakage detection teams in November 2023 to observe how leakage detection, reporting, and response are conducted. Wachs and AW each have their own methodologies for detecting leaks. The following sub- sections outline the equipment used by Wachs for large and small diameter leaks and their methods of operation in the AW system. Ground microphones An acoustic ground microphone detects and amplifies the noises within the water distribution system. The sensors on this equipment can be placed directly onto a valve nut or hydrant via a magnetic connection or they can be placed onto road or dirt with different fittings. In circumstances where there is significant road or wind noise an “Elephants Foot” can be connected to the unit to reduce this noise. Some of the more advanced ground microphones also have the capability to dampen or filter out specific noise frequencies to improve the listening potential for the technician. These units are also used in the very first phase of leak detection by experienced operators who want to get a fast read on whether there may be a leak and whether other more advanced equipment should be considered. They are often used in the last stages of pinpointing as well and for confirmation of a leak determined by a correlator or correlating logger. Correlators A leak noise correlator is a two-channel microprocessor (which can be connected to a laptop or a separate, dedicated device) that measures the time delay of a leak noise registered at two contact points on the water main. By obtaining leak sounds at two points on either side of a suspected leak, the correlator analyzes the leak sounds and, knowing the system characteristics that are input by the operator, determines the exact location of the leak between the two sensors. Correlators are generally considered the “high-end” of leakage detection equipment and are the most accurate means of pinpointing a leak. They need experienced operators and detailed system inputs to allow for accurate readings. They are more time-consuming than the other devices, and so are often used in the pinpointing and complex verification phases only. Smart Ball and Sahara (for mains 24” and larger) Tethered equipment uses a parachute and neutral buoyancy to allow the acoustic sensor to travel down the main. The finite range of these units is about 2,500 feet per insertion with perfect conditions. This will be significantly reduced if there are any bends in the main tested or if the flow reduces below 1 foot per second. Generally, the units will cease forward movement after 270 degrees of bends, or at flows less than 0.5 feet per second. 5-3 Sahara (above) uses a tethered parachute to navigate through the flow and can be deployed even in no flow conditions. SmartBall (Right) is a free-swimming tool and can accommodate low flow conditions. Both tools can be used without interrupting the service. 5.1.3 Leakage Detection Reporting AW utilizes an active Leak Response Map in ArcGIS to track and provide live updates for reported leaks in the City of Austin. Leaks phoned into AW Dispatch are uploaded and updated in real time. This allows crews to closely track reported leaks and failures throughout the 4,000 miles of water pipeline in the system. Once a leak is pinpointed by Wachs, the location is identified in a layer in GIS Collector. A current map indicated that approximately 4,700 miles have been investigated and 1,500 leaks found since 2011. The location will be reported through the Wachs system. An administrator provides a weekly report to AW staff, and this is uploaded to an AW SharePoint folder. If a leak is found on the site, Wachs will report this leak to the reactive leakage detection and repair team through the public reporting line. Over the past few years, there appears to have been a reduction in leaks reported overall and especially a small number of main line leaks which were reported in 2022. Upon review of Leakage Detection data from it was determined that a significant number of identified leaks were not entered with a work order or service request. This was noted during the project and protocols are being actively put into place to organize renewed oversight, management of the reporting, data collection, and validation of results. There is also currently only minimal interaction or collaboration between AW and contractor staff. Each can benefit from interaction and sharing of information. 5.2 Real Loss Component Analysis The Water Research Foundation (WRF) developed the component analysis model (model), a software tool, to assist in conducting leakage component analysis and economic leakage evaluation. The WRF 4372a manual (Real Loss Component Analysis: A Tool for Economic Water Loss Control) outlines the development and usage of the model. This manual and the associated software have been used to conduct the following component analysis. AW staff has conducted the component analyses from 2015-2019. AW did not perform a component analysis in 2020 due to COVID-19 but continued through 2022. By continuing the component analysis into the future, AW will be able to closely track real loss KPI targets and track improvements in leak detection and response. The tool was developed to provide utilities with a computer-based model for leakage analysis, failure frequency analysis, economic leakage control intervention strategy evaluation, and display key water loss performance indicators. The model is a complementary analysis tool to the AWWA Free Water Audit Software, which AW uses for its water audit. Snapshots of the completed component analysis are included in Appendix A. A leakage component analysis breaks down the total volume of real losses into three components: Background leakage: These are the collective weeps and seeps at joints and fittings that occur at very low flow rates but may exist pervasively across the water distribution system, particularly if the piping and service connections are old, or are in poor condition. This type of leakage is not currently acoustically detectable, so it will not be addressed by conventional leak detection work. Background leakage can often be addressed by improved pressure management or by pipeline 5-4 renewal. Background leakage can be quantified by using the step-testing technique in the distribution system. Unreported leakage: These leaks escape public knowledge and are only identified through the active leakage control work of the water utility. The leak detection survey is the most common means currently used in North America to identify unreported leaks. Reported leakage: These are leaks that are reported by customers, traffic authorities, or any other outside party because of their visible and/or disruptive nature. Also, those leaks detected by high flows and/or noticeable drops in water pressure in supervisory control and data acquisition systems can be categorized as reported leaks. Figure 5-2 Background, Unreported, and Reported Leakage Visual Examples. The WRF 4372 model utilizes leakage detection and repair data provided by AW from FY 2022. Detailed steps undertaken for the exercise are outlined in the subsequent sub-sections. Unless noted otherwise, the default average failure flow rate was utilized to estimate the volume of water loss. 5.2.1 Step 1: Background Leakage, Reported Leakage, and Unreported Leakage from Reservoirs The first entries into the model evaluate reservoir and tank leakage. This volume is usually relatively minor; however, it is still an important part of the calculation. In 2022, AW reported six leakage events as presented in Table 5-2. The sum of leakage volume from the six events of 701,500 Gallons was inputted to the model. The total leakage for reservoirs and tanks was then totaled to be 0.7 MG. A snapshot of the model is presented in Appendix A, Figure A-1 Step 1; Background Leakage, Reported Leakage, and Unreported Leakage from Reservoirs. Table 5-2 2022 Tank Overflow Events RESERVOIR OR TANK NAME OVERFLOW (GALLONS) Forest Ridge Pump Sta. & Res. 50,000 Pond Springs Reservoir Thomas Springs Reservoir 189,000 22,500 Guildford Cove Pump Sta. & Res. 150,000 Howard Lane Pump Sta. & Res. 190,000 5-5 RESERVOIR OR TANK NAME OVERFLOW (GALLONS) Leuthan Lane Pump Sta. & Res. 100,000 Combined Total (Gallons) 701,500 5.2.2 Step 2: Background Leakage on Mains and Services The background leakage on all the mains and service connections is calculated in this step. The length of mains and the number of connections were from 2022 Texas Water Development Board (TWDB) 2022 Water Audit Data. Applying a system age of less than 50 years for this analysis and an Infrastructure Condition Factor of 1, the total background leakage on mains and service connections was calculated as 1,190 MG as shown in Figure A-2. This comprises 17.2% of real loss components. 5.2.2.1 Step 3A: Reported Failures on Mains For this step, data was analyzed that outlined reported failures and their associated work order. This spreadsheet was utilized to complete this portion of the Component Analysis. There were 370 reported failures on mains in 2022. Since an awareness duration was not recorded for 2” and 3” mains, 30 days was assumed. 4” mains have an average awareness duration of seven days, while mains 6” through >60” have a duration of one day. The water loss time recorded in the data provided by AW was utilized to calculate the average duration for location and repair/shutoff failure for each pipe size. It should be noted that the water loss time recorded in the spreadsheet is likely underestimated. The location to shutoff water loss time recorded from 2021 was higher than in 2022 as presented in Table 5-3. Table 5-3 Average Water Loss Time for 2021 and 2022 Main Break Events YEAR NUMBER OF MAIN BREAKS AVERAGE LOCATION TO SHUTOFF 2021 2022 418 370 WATER LOSS TIME (DAYS) 2.46 Days 2.25 days The length of main per pipe size was calculated using GIS data. Most of the loss from reported failures on mains came from failures on 2”, 6”, and 24” lines, accounting for 83 MG of the total annual water loss from reported main failures. The total annual water loss associated with reported main failures was calculated to be 108.32 MG. A screenshot of the model is shown in Figure A-3 Reported Failures on Mains. 5.2.2.2 Step 3B: Reported Failures on Distribution System Appurtenances This step calculates the volume of loss due to system appurtenance failures. AW reported 18 hydrant breaks and 20 valve breaks in 2022. Similar to the main breaks, a few events suspected to be maintenance activities rather than breaks (e.g. new valve installation, hydrant relocation) were excluded from the analysis. Since the awareness duration was not recorded, an average duration of 30 days was used. The water loss time recorded in the break’s spreadsheet was used to calculate the average duration for location and repair/shutoff. Using the default average failure flow rate, the water loss from reported leaks on system appurtenances was calculated to be 70.59 MG. 5-6 5.2.2.3 Step 3C: Reported Failures on Service Connections This step calculates water loss associated with reported failures on service connections. The failures on service connections are divided between services less than one inch and services greater than or equal to 1-inch. 1,142 service connection failures were recorded. The size of service connections was not recorded and is unknown; therefore, it was estimated based on the distribution main size. The service connection size was estimated to be greater than or equal to 1-inch if its respective distribution main size was equal to or above 12 inches. If the main size was below 12 inches, the service connection size was estimated to be less than 1-inch. The recorded water loss time was utilized to calculate the average duration for location and repair/shutoff presented in the table below. Since the awareness duration was unknown, an average duration of 45 days was used. The number of service connection failures is shown in Table 5-4. Table 5-4 Service Connection Failures Recorded in 2022 SERVICE CONNECTION SIZE NUMBER OF FAILURES AVERAGE DURATION FOR LOCATION AND REPAIR/SHUTOFF (DAY) <1-inch >=1-inch 1056 86 1.58 2.20 The service connection failures from these data sources were entered into the model. Using the default average failures flow rate, the water loss associated with reported leaks on service connections was calculated to be 635.13 MG. A screenshot of the model is shown in Figure A-5 Reported Failures on Service Connections The total volume of water loss associated with reported failures from Step 3A, 3B, and 3C was 814.03MG. . 5.2.3 Step 4: Unreported Failures Unreported failures show failure events found through AW’s proactive leakage detection program. Unreported leaks or break are events that are found during active leakage detection programs. AW conducts proactive main leak detection annually. The third-party leak detection contractor (Wachs) found four main leaks, one leaking hydrant, and two leaking meters in their 2022 evaluation. 5.2.3.1 Step 4A: Unreported Failures on Mains There were four unreported main failures on 2” line in 2022 as noted in the 2022 Component Analysis. The average awareness duration was set at a default of 365 days because of AW’s annual leakage detection program. The average duration for location and shutoff for these four failures on the 2” main was 0.17 days. The annual loss for these unreported main failures amounts to 32.56 MG in 2022. A screenshot of the Step 4A can be found in Figure A-6 Unreported Failures on Mains. There were no other unreported failures on mains documented for 2022. 5.2.3.2 Step 4B: Unreported Failures on Distribution System Appurtenances One leaking hydrant was identified from AW’s proactive detection efforts. Under the assumption that the system is surveyed once a year, the average awareness time of 182.50 days was used. An average duration for location and repair/shutoff was estimated to be 1 day. The volume of water loss associated with unreported failures on system appurtenances was calculated to be 1.17 MG. A screenshot of the model for Step 4B is shown in Figure A-7 Unreported Failures on Distribution System Appurtenances. 5-7 5.2.3.3 Step 4C: Unreported Failures on Service Connections There were three unreported service connection failures in 2022 on services <1”. The service connection failures were entered into the model. Using the default average failures flow rate, the water loss associated with unreported leaks on service connections was calculated to be 12.12 MG. The total volume of water loss associated with reported failures from Step 4A, 4B, and 4C was 45.86 MG. 5.3 Results 5.3.1 Failure Frequency Analysis The failure frequency analysis calculates and compares the failure frequency on mains (number/100 miles/yr), the service connection failure frequency (number/1000 connections/yr), and the ratio of failure frequency to UARL break frequency. These values, shown in Table 5-5, are calculated by the model and compared to other utilities. Table 5-5 Infrastructure Failure Frequency Analysis CATEGORY VALUE TYPICAL VALUE Total Number of Mains Failures Reported for 2022 Total Length of Mains (miles) Mains Failure Frequency (number/100 miles/yr) 370 9.2 4,026 miles Total Number of Service Connection Failures Reported for 2021 1,142 Total Number of Service Connections 250,385 Service Connection Failure Frequency (number/1000 conns/yr) 4.6 Ratio of Failure Frequency to UARL Break Frequency 2.0 Footnote: 1) Average Failure Frequency in North America, Based on Literature Review-WaterRF 4372 2) Failure Frequency for Optimized Systems, Friedman 2010 3) AWWA UARL Component of Reported Service Line Failures N/A N/A 251, 152 N/A N/A 3.753 N/A Figure 5-3 and Figure 5-4 show the variations in the mains and service line failures in AW and compares them against averages developed during the WRF 4372 process. 5-8 Figure 5-3 City of Austin Mains Failure Frequency 2022 Figure 5-4 City of Austin Service Connections Failures 2022 With 9.2 failures per 100 miles per year, the main failure frequency is lower than the average in North America and that for optimized systems. This may be due to good main line leakage detection control, or main leaks not being found due to a number of factors (geology, proactive leak detection practices, etc.). The service connection failure frequency is significantly greater that the average at 4.6 failures per 1,000 service connections. Therefore, the components do suggest that there are leakage efficiencies that can be generated from additional focus on leakage detection and repair. It is also possible that there may still be a significant portion of hidden leaks in the system. Once the leak detection practices are altered and data with the additional operating procedures and oversight are 5-9 incorporated then data trending can be re-instated to allow more accurate analysis of the effectiveness of leak detection. 5.3.2 Awareness, Location and Repair Time Reduction Options The analysis model shown in Figure 5-5 provides a calculation of the sensitivity on the volume of real loss if the location and repair durations are reduced. Since the water loss time recorded for the main failures and system appurtenances are already very low, this analysis was not completed for the main and system appurtenance failures. It should be noted that the actual water loss time is likely higher than what is being recorded. Educating the field staff on what and how parameters should be recorded would improve the quality of the data collected. For the service line failures, the average time for location and repair was 1.6 days. As a “what if” scenario, a theoretical value of 1 day was used to calculate potential related savings in leakage volume cost. The potential savings for reducing the time for service line failures was calculated as 8.7 MG and $4,188 / year for reported failures. As this value is very low, further consideration of time reduction does not appear to be advantageous. Figure 5-5 Reported and Unreported Failure Events 2022 5-10 5.3.3 Economic Intervention Frequency for Proactive Leak Detection In this part of the analysis, a cost of comprehensive leak detection survey (excluding leak repair cost) and the average rate of rise of unreported leakage are entered to calculate a potentially recoverable leakage value. A cost of $300.00/mile for leakage surveying and a rate of rise value of 0.10 kgal/mile of mains/day was used. Real losses are divided into unavoidable annual real losses (UARL), real losses not economical to recover, and economically recoverable annual real losses. The performance metrics also outline that with this data, the economic intervention frequency is approximately 70 months, or 6 years to complete a total system survey. This is approximately the amount that AW currently completes annually through proactive leakage detection as described in Section 4.1. Improvements to this program are suggested in Section 6.5. Figure 5-6 Variable Costs of Real Losses for AW Of the current annual real losses (6,913 MG), 4,431.7 MG is calculated to be potentially recoverable through proactive leak detection annually as shown in Figure 5-7. 5-11 Figure 5-7 Current Real Losses vs. Recoverable Leakage based on Recommended Strategies 5.3.4 Component Analysis Recommendations A key recommendation for the real loss component analysis is to improve the quality and consistency of the failure data collected. Like a water audit, a component analysis should be conducted annually to build more detailed knowledge and understanding. A number of inconsistencies were noted upon reviewing the failure data: The number of proactive leaks noted in 2022 was low considering the proactive program currently in operation. This program should be refocused to concentrate on active detection, reporting and validation of results. The recorded water loss time for 2022 failure data is significantly lower than what is expected and compared to previous years’ data For some service connection failure events, the service connection size was not recorded, and its corresponding main size was recorded instead. AW is currently enacting polybutylene service line replacement through the Renewing Austin Program. The systemwide rate of replacement is approximately 10-15 service lines per week. Service line replacement should be accounted for in subsequent component analyses. Educating field staff (including contractors) on what data needs to be collected and utilizing the WRF 4372 standard spreadsheet will improve the quality of the failure data used for the 4372 model for the future years. Figure 5-8Error! Reference source not found. shows the WRF guideline on main failure data collection. 5-12 Figure 5-8 Additional Recommendations 5.3.4.1 Pressure Management Opportunities Evaluation of Pressure Management Opportunities looks at Results of Reduced Pressure on the Volume of Real Losses. Pressure Management has additional benefits and impacts such as: reduced number of new infrastructure failures, reduced annual repair costs, extended infrastructure life, reduction in residential consumption (mainly for pressure dependent outdoor consumption such as irrigation) which are not quantified in this model. However, these additional benefits and impacts should be evaluated before implementing a new or updated pressure management policy. If this initial assessment of pressure management options indicates that pressure reduction could provide cost effective means of reducing and controlling real losses in the system, then it is recommended to conduct a detailed pressure management study. Such a study should collect pressure data from the field, assess the presence of pressure transients, identify pressure zones with excessive pressures and prioritize pressure management in parts of the system where its most feasible. In addition, a more detailed assessment of costs for implementing the new pressure management policy should be assessed. This study should further consider the potential revenue impact a change in pressure management policy might have on residential consumption (mainly for pressure dependent outdoor consumption such as irrigation). 5-13 Typical pressure management options include introduction of pressure controlled areas, fixed outlet pressure control, time or demand based pressure control, transient control, altitude and level control at reservoirs and tanks etc. Figure 5-9 City of Austin Pressure Management Opportunities 5.4 Real Loss Cost Analysis AW’s annual real loss costs have increased over past years as noted in Figure 5-10. There have been significant increases reported in 2014 and in 2022. The 2022 increase does correspond with both an increase in the variable production cost (from $400 per MG to almost $500 per MG) and the reduction in leaks found proactively in the year. AW reported $3,311,542 of real loss in 2022. While not all of this in recoverable, it is expected that a significant portion could be reduced by leakage focusing on detection data management, and validation of the leakage detection conducted. the utility proactive practices, monitoring, Figure 5-10 Cost Trends of Real Losses 5-14 6.0 Goals and Recommended Strategies The following section outlines the recommended strategies to validate, monitor, manage and reduce non-revenue water within AW. Each of the recommended strategies are discussed in more detail in the subsequent subsections. Based on the review of NRW by B&V, several recommendation areas have been identified. Each area contains specific recommendations to improve either data quality, direct intervention strategies, or improve coordination. 6.1 AW Progress To-Date AW's efforts to manage non-revenue water are carried out through a partnership between designated utility staff and contracted parties. The AWWA pillars of leakage management, which involve active leakage control, pipeline and asset management, and the speed and quality of repairs, are considered by AW to effectively manage water losses. Many of AW’s efforts are outlined in detail in the Water Forward plan for Austin and serve as a comprehensive guide to the management of non-revenue water. Overview Figure 6-1 Non-Revenue Water Reduction Strategy AW utilizes both its own staff and Vanguard Utility Services to perform its meter testing throughout the system. AW performs small meter testing and replacement and utilizes Vanguard to assist in testing meter accuracy for approximately 2,500 large commercial and multifamily customers. Vanguard was also contracted to replace 450 large diameter meters of the nearly 250,000 analog meters scheduled for replacement. AW is installing 250,000 digital meters as part of the My ATX Water Program which will actively report leaks and failures on the customer side of the meter. Vector Controls conducted calibration/verification and validation of approximately 50% of the WTP production flow meters. The meter accuracy results provided by Vector proved to be useful, however; inconsistent calibration/verification and validation practices, has produced undesirable results. These results and recent meter replacement lead B&V to recommend secondary testing at all Water Treatment Plants. Xylem is currently contracted by AW to proactively cover their system and detect leaks. Wach’s contract is to survey around 500 miles of pipe per year. AW has an in-house leakage detection team with five full- time and one part-time staff, as well as nine line-location staff. The team is responsible for assisting in water sampling, flushing, non-leak related investigations, and line locating for AW. AW utilizes an active Leak Response Map in ArcGIS to track and provide live updates for reported leaks throughout the 4,000 miles of water pipeline in the system. AW has a regulatory requirement to annually report on their water loss performance and is taking a proactive approach to replace aging water and wastewater pipelines in their system through the Renewing Austin program. In conjunction with a yearly system audit, AW has designated water loss staff who performs an annual component analysis on the entire system. 6-1 6.2 Target Goals & KPIs 6.2.1 Actionable Improvement Goals While sections 6.3 through 6.9 detail recommended strategies to mitigate real and apparent losses across the system, listed below are actionable improvement goals for AW to consider: • Production meter flow testing was conducted in 2021 by Chiang, Patel & Yerby (CP&Y) and Vector Controls at the three water treatment plants. Not all meters were able to be tested, however, so the work was of limited value. As outlined in 6.3.1, AW should commission another report to gain a complete understanding of production meter accuracy to identify needed capital improvements. • As referenced in Section 6.4.1.1, AW should continue to test customer meters in the field including those installed as part of the My ATX Water Program. This should continue to validate meter accuracy and create a baseline to track program successes. Sample testing of new meters will improve the individual meter and weighted meter accuracy calculations to enable targeting and optimizing of system performance. • To remain in-line with AW’s current meter testing practices, AW should expand its field-testing large meters 3” and above at least every 18 months. This recommendation is further outlined in Section 6.4.1.1. • AW should consider additional staff (internal and/or contractor) to focus on distribution main leak detection. This will renew oversight, improve management of the reporting, data collection, and validation completed by leak detection staff. Proactive main line leaks found by these staff should be recorded and reported at least monthly. Goals will be determined 6-12 months after data collection. Key Performance Indicators for additional distribution main leak detection can be found in Section 6.5.1.1. • AW’s leak detection and response efforts should continue incorporating the Real Loss Component Analysis as part of their annual auditing process. An annual component analysis provides the leak detection team with recommendations for improved speed and quality of leak repair, proactive leak detection, and pressure management. The continuation of the Real Loss Component Analysis will allow for the effective implementation of recommendations outlined in Section 6.5. • As evidenced by the data in Section 5.3.1, AW’s mains experience failures at a lower rate that even “optimized distribution systems,” but AW’s service lines experience failures at a much higher frequency than the industry average. Therefore, AW should increase its efforts to replace failing water service lines. Infrastructure Leakage Index 6.2.2 AW has defined goals in previous years and memorialized these in the Water Forward plan. The 2018 Water Forward plan defined a short-term ILI goal of 2.7 and a long-term goal of 2.0. As part of the 2024 update to this plan, AW revised their 2040 ILI goal to 3.0. In conjunction with this long-term goal, AW has also set a short-term ILI goal of 3.31 by 2034. To reduce the 2022 ILI of 4.1 to 3.0, AW needs to save 20 gallons/connection/day or 5 MGD in real loss strategy savings. 6-2 Table 6-1 outlines the key NRW performance indicators as reported for 2022 and the proposed 2030 goals. 2022 AUDIT 2030 GOAL (THIS PROJECT) Table 6-1 Current (2022) NRW KPIs and Future Goals KPI Real Loss (ILI) Real Loss (gal/conn/day) 75.60 Apparent Loss (gal/conn/day) 17.40 Data Validity 4.1 77 3.0 55.60 7.40 85 While apparent loss strategies will not reduce the ILI, AW’s data validity score will improve, ensuring the audit is supplied with the best available data. Production Meter Improvements and Validation Review and discussion on usage and measurement expectations 6.3 Production Metering A full analysis of the raw and finished water inputs at the water treatment plants themselves provides the data to perform a mass balance across the whole system and to define system input volume. To improve the accuracy and confidence of the system input volume within the water audit, production meter verification, secondary testing, consistent data management and capital improvements will enable the establishment of a trusted baseline. Raw water volumes will be utilized for state withdrawal reporting to the TWDB as well as secondary meter testing and validation of finished water volumes. Finished water volumes will be utilized in auditing such as the AWWA Audit performed by B&V. Total Investment $6,000,000- 12,000,000 FY 2026-2033 Initial Investment $800,000 FY 2025 6.3.1 Calibration and Verification Processes Enhancement of AW’s existing calibration and verification processes will improve the overall accuracy and reliability of the water audit data, which will ultimately lead to better decision-making and improved confidence improve non-revenue water reduction efforts. Recommendations include: input volumes and therefore in the 1) Maintenance and Verification of Calibration a) Ensure meters are regularly maintained and verified [sometimes described as calibration] in the field at least annually. Semi-annual (twice per year) verification of calibration is recommended (especially on finished water meters) and will achieve a higher certainty and data validation. i) AW currently conducts regular verification. However, this recommendation is designed to both standardize the action and the reporting across all sites so that trends of accuracy can be understood and drive standardized maintenance, secondary testing, etc. ii) Resolve (and record resolution for) any meters that test outside of expected ranges. 6-3 6.3.2 Secondary Meter Testing Program AW should continue and expand the secondary testing program utilizing a second in-line meter to evaluate in-the-field accuracy at all production sites over time. a) AW should develop a plan of which meters are most at risk of degrading accuracy (determined by age, configuration, calibration, volume throughput, annual volume, etc.) and then develop, initiate, and standardize the sequence for secondary testing. B&V recommends secondary testing at all WTPs. Initial efforts should be focused on Davis WTP, which commissioned a new medium service facility in December 2023. As noted in section 3.2, this review and additional AW staff notes suggested metering accuracy issues from May 2021 to early 2024. 6-4 Table 6-2 Handcox Production Meter Recommendations Plant Meter Tag Meter Type Average Recorded Flow (MGD) Equipment Range (MGD) Vector Test Result Flatlining (MGD) In Service (Y/N) Most Recent Calibration Calibration Max Deviation Result Test Method Recommendation Handcox Finished Water 1 Venturi 21.18 0-120 Handcox Raw UFC 1 Handcox Raw UFC 2 Venturi Venturi 0-40 0-40 -0.84% -9.39% -13.87% Y Y Y - - - 11/3/2022 - Ultrasonic 3/24/2021 0.15% Ultrasonic 3/26/2021 -0.08% Ultrasonic Test in 3-5 years Secondary flow test Secondary flow test 6-5 Table 6-3 Davis Production Meter Recommendations Plant Meter Tag Meter Type Average Recorded Flow (MGD)1 Equipment Range (MGD) Vector Test Result In Service (Y/N) Flatlining (MGD) Most Recent Calibration Test Method Recommendation Davis RWP 1 Mag Davis RWP 2 Mag Davis RWP 3 Mag - - - Davis HSP 21 Ultrasonic 0.00 Davis HSP 22 Ultrasonic 4.41 Davis HSP 23 Ultrasonic 7.57 Davis HSP 24 Ultrasonic 4.60 Davis HSP 25 Ultrasonic 5.70 Davis HSP 26 Ultrasonic 5.71 0-60 0-60 0-70 0-22 0-10 0-22 0-22 0-22 0-22 Passed Meter Verification Passed Meter Verification Passed Meter Verification 1.09% 8.67% -4.49% 1.70% -2.33% -0.93% Davis MSP 11 Venturi 0.00 - Not Tested Y Y Y N Y Y Y Y Y Y Y Y N N N Y 21.99 N/A 19.53 19.50 19.5 19.46 - - - - - - - - - - - - - - - - - - - - - - - - - - Ultrasonic Ultrasonic Ultrasonic Ultrasonic Ultrasonic Ultrasonic Test in 3-5 years Test in 3-5 years Test in 3-5 years Out of service Secondary flow test. Test in 12-24 Months Test in 3-5 years Test in 12-24 Months Test in 3-5 years Transition to New MSPS Transition to New MSPS Transition to New MSPS Transition to New MSPS Transition to New MSPS Transition to New MSPS Transition to New MSPS 6-6 Davis MSP 12 Venturi 0.89 0-25 Not Tested 12/28/2021 Ultrasonic Davis MSP 13 Venturi 9.75 0-15 Not Tested 12/28/2021 Ultrasonic Davis MSP 14 Venturi 4.18 0-25 Not Tested Ultrasonic Davis MSP 15 Venturi 3.48 0-25 Not Tested 12/28/2021 Ultrasonic Davis MSP 16 Venturi 2.46 0-25 Not Tested Ultrasonic Davis MSP 17 Venturi 0.00 0-25 Not Tested 12/28/2021 Ultrasonic Table 6-4 Ullrich Production Meter Recommendations Summary Average Recorded Flow (MGD)1 Equipment Range (MGD) Vector Test Result In Service (Y/N) Flatlining (MGD) Most Recent Calibration Calibration Maximum Deviation Test Method Recommendation Plant Meter Tag Meter Type Ullrich RWP High 1 Venturi Ullrich RWP Low 1 Venturi Ullrich RWP High 2 Venturi Ullrich RWP Low 2 Venturi Ullrich RWP High 3 Venturi Ullrich RWP Low 3 Venturi 0-165 0-165 0-165 0-165 0-165 0-165 12.24% 12.24% Passed Meter Verification Passed Meter Verification Passed Meter Verification Passed Meter Verification -4.46% -3.05% Ullrich MSP 1 Venturi Ullrich MSP 2 Venturi 13.77 Ullrich MSP 3 Venturi 18.92 Ullrich MSP 4 Venturi - - Y Y N Y Y Y Y Y Y Y Y Y N Y Y N - - - - - - - - - - - - - - - - 4/7/2021 0.526% 4/7/2021 4/6/2021 0.097% 4/6/2021 -0.116% Ultrasonic Ultrasonic Ullrich HSP 1 Venturi 2.87 0-10 4/5/2021 -96.96% Ultrasonic Ullrich HSP 2 Venturi 11.41 0-20 4/5/2021 0.038% Ultrasonic Ullrich HSP 3 Venturi 0.82 0-10 -11.51% 4/5/2021 -80.425% Ultrasonic Ullrich HSP 4 Venturi 14.39 0-20 16.57% 3/26/2021 0.17% Ultrasonic Ullrich HSP 5 Venturi 9.58 0-40 3.62% 4/5/2021 0.050% Ultrasonic Ullrich HSP 6 Venturi 14.76 0-40 13.02% 4/6/2021 0.288% Ultrasonic Test in 12 months Test in 12 months Test in 12 months Test in 12 months Test in 12 months Test in 12 months 6-7 6.3.3 Production Data Handling Centralizing SCADA data for these meters into a singular dashboard would streamline information on all water treatment plants. Dashboards incorporate data trending and analysis that enables daily review of hourly production data. These dashboards can also assist in identifying data anomalies and suspected production meter errors through visualization, trend analysis, and frequent monitoring. For example, during this analysis, a dashboard populated with data provided by AW, showed the volumes at Handcox WTP for RWF 1 and 2 were provided separately, as well as with a combined value. The sum of RWF 1 and 2 did not equal the reported volume of finished water; AW should determine where the data error originates. “Degradation triggers” should be set using the available SCADA or metering data to detect anomalies and provide early warning for meter or system degradation. These should be memorialized, and reasons (and procedures for mitigation) established, if necessary. 6.3.4 Production Metering Capital Improvements Multiple meters were confirmed by AW as being improperly configured. Improvements to mitigate limitations with piping and metering configurations are expected to require capital works programs. This needs to be a long-term consideration as meter vault or meter upgrade programs are generally time consuming and relatively expensive. AW needs to initiate an engineering report to properly review the design of finished water meters and raw water intakes at Davis and Ullrich Water Treatment Plants. A placeholder cost of $800,000 has been estimated for this study. Upon completion of the engineering report, AW should move to consider recommended improvements, which would be designed and constructed under a separate capital improvement project; preliminary cost estimates range improvements at $6 to $12 million. 6.4 Apparent Loss 6.4.1 Meter Inaccuracy 6.4.1.1 Priority Meter Testing A metered system is the best way to equitably spread the cost of water service. Therefore, it is important to ensure that the meters are functioning accurately to not only recover revenues owed to the utility but also prevent inequities among the customers. The 2022 AWWA water audit estimated that customer metering inaccuracies caused under- registered consumption of 1,476 MG/yr (valued at $8.5M). Accounting for 93% of apparent loss costs, this amount represents most of the revenue recovery potential in apparent losses. AW began replacing all 2” and smaller residential meters with new meters through the My ATX meter replacement program. These meters will be less than three years old by 2025, and it is expected that this will already have improved meter accuracy. However, a focus on the larger meters, which have not been replaced, should be considered. Meter operations within AW currently tests all large meters approximately once every 18 months. It is important for AW to investigate efforts into additional large meter testing for further apparent loss reductions. 6-8 6.4.1.2 Meter Testing Program Validation To validate the meter testing program (for any size), AW is advised to re-test up to 5% of the meters tested by a third-party Contractor. Even though this comes at an added cost, it is critical to verify the competency of the meter testing staff or vendor and the testing results early in the program to ensure successful outcomes. If the testing isn’t conducted properly, the capital spent on the testing program could be wasted with inaccurate test results misguiding important meter replacement decisions. To ensure meters are properly tested, contract language should include requirements for the contractor to follow AW guidance for meter testing. Annual Investment $25,000 FY 2025 Meter Testing Program Validation Meter Testing Validation select meters Total Investment $225,000 FY 2026-2033 Scope: Retest a total of 50 large meters as shown in Table 6-5 by a third-party Contractor. AW can randomly select the meters to retest. The retest results aren’t expected to exactly match with the initial test results. Therefore, AW should seek a review from an experienced consultant to evaluate the patterns and trends of the re-test results and validate the accuracy of the Priority Meter Testing Program test results. Cost: $25,000 per year as outlined in Table 6-5. Table 6-5 Meter Testing Program Validation Scope and Cost Estimate METER SIZE (INCH) NUMBER OF METERS TO RETEST COST PER TEST ($) SUBTOTAL COST ($) 3 4 6 8 10 Total 10 10 10 10 10 50 5,000 5,000 5,000 5,000 5,000 25,000 500 - 6.4.1.3 SOP Development on Meter Testing, Sizing, and Replacement Vanguard and AW both perform volumetric flow testing on customer meters. Vanguard is responsible for proactively testing meters 3” and above, while AW reactively tests smaller customer meters. To ensure consistency and quality of the meter testing program, AW should define and procedures standard operating implement (SOPs). This is especially important for AW as all large meter testing is contracted out to Vanguard Utility Services. AW staff should develop the SOPs following the AWWA M6 Manual on Water Meters – Selection, Installation, Testing, and Maintenance. AW may seek guidance from external subject matter 6-9 experts in developing the procedures. Once the SOP is developed, Austin should proactively review and update the procedures on an annual basis. Scope: Develop the Standard Operating Procedure documentation on meter testing, sizing, and replacement for Badger and MFM2 Hersey meters. Update the documentation annually. Cost: The estimated cost in developing the SOP is $40,000 with an annual cost of $10,000 estimated in maintaining and updating the SOP. A non-exhaustive list of items to include in the SOP is presented below, with details of each item discussed in the following pages. • Meter testing methods o Bench testing for small meters (up to 2’’) o In situ testing for large meters (3’’ and above) • Meter testing schedule • Meter testing sampling • Meter sizing • Meter replacement Meter testing methods Tests can be conducted using volumetric tanks (volumetric method) or weight scales (gravimetric method). The gravimetric method should be chosen as the testing method when possible as it yields more accurate results. Accuracy standards for new meters are contained in the latest revisions of the following AWWA standards: C700, C701, C702, C703, C704, C708, and C710, C712, and C713. It should be noted that depending on the size of the test-rig, the maximum (safe) flow maybe be approximately 400 gpm. Therefore, the largest meters cannot be tested at the high flow limits. Since most of the degradation occurs at the low-flow ranges, testing is usually good enough for the purpose. If a utility wishes to test the high-flow regime, then the meter will need to be removed and tested on a test bench that can produce these flows. Meter testing sampling To track meters losing their accuracy with time or usage, utilities should follow a targeted sampling approach rather than a randomized one when it comes to selecting meters to test. Meter total throughput values should be compared to approximate warranties to identify meters reaching the end of their life cycles. B&V recommends building a Power BI dashboard with AW’s meter inventory to assist in systematically selecting meters to be tested. Periodic surveys testing a statistically representative random sample of meters should also be conducted to calculate the overall meter accuracy. The results can then be used in calculating the apparent losses in the water loss audit. While AW is replacing smaller meters to transition to Advanced Metering Infrastructure (AMI) through the My ATX Water program, AW conducts testing on newly purchased residential meters to confirm their accuracy. AW should review its testing program against the following recommendations and make revisions as necessary. A small number of new meters should be tested with their test results compared to the ones provided by the manufacturer. If the test results are outside the 2% range of the manufacturer’s results, then the meters should be sent back to the manufacturer for re-testing. If the manufacturer re-tests the meter and states that it does test within accuracy, AW should send the meter in question to a neutral third party (who does not have access to any of the previous test information) for testing. Depending on 6-10 the results from the third-party test, the manufacturer should be contacted to determine the reason for any proven discrepancy and the number of new meters to be tested should be increased. 6.4.1.4 Meter Sizing Analysis The right sizing of meters is critical in capturing accurate consumption data as most meters are less accurate at the low end of their flow range and oversized meters can cause utilities to under- report consumption data. Many water utilities have recovered considerable water and revenue from right-sizing of oversized customer meters. If the meter is undersized, the high consumption flow past the design flow causes a more rapid degradation of meters, shortening the life of meters. Data screening can be used to identify a subset of meters that may not be sized appropriately based on consumption patterns from the billing data. Meters can then be selected for a meter sizing analysis using high frequency data loggers with data collection interval of 20 seconds or less to determine the consumption profile. The consumption profile should be then reviewed and analyzed to assess whether the size and type of a meter are appropriate. AWWA Manual M22, Sizing Water Service Lines and Meters, provides good guidance on sizing of meters using data logger data. Included in Figure 4-3 in section 4.1 are customer metering inaccuracies for large size meters. The overall inaccuracies of 3.06% (average) and 2.88% (weighted average) are relatively close to an acceptable range but still outside for customer meter inaccuracy. The 6” meters tested had an average inaccuracy of 5.97% and weighted average inaccuracy of 5.13%. As M36 Water Loss Control Manual recommends secondary testing for meters that test outside of +/- 6.00%, secondary testing is recommended. The recommendation is to conduct meter sizing analysis using high frequency data loggers in FY2026. Data logging technology involves attaching a logging device to the meter to obtain a detailed consumption profile through the pulses (signal) registered by the meter. The consumption profile can be developed for a range of time intervals: from hourly logging to establish a basic consumption profile, to fractions of a second using high-resolution data loggers in order to capture transient peak flow rates. Austin is advised to collect data with 20 seconds or less intervals to capture accurate consumption data. Austin is recommended to conduct the analysis on a randomly selected sample of 50 meters, then to re-evaluate the continuation of the program based on the results. The consumption profile should also be used to analyze whether the meter type is appropriate for the customer. Different types of meters are appropriate for specific flow ranges. Turbine meters are designed to capture continuous moderate and high flows, but if the user has periodic or frequent low flows, a considerable portion of the regular water usage may not be registered by the meter. Variations in flow from low to high can be measured by compound, electromagnetic (“mag”), single-jet, and ultrasonic meters and floating ball technology. AWWA Manual M22, Sizing Water Service Lines and Meters, provides good guidance for the use of logged data to specify meter type and sizing. 6-11 Scope: Conduct meter sizing analysis on 50 randomly selected meters using a high frequency data logger with capability of collecting data within 20 seconds or less intervals. Evaluate the data to replace oversized or undersized meters and confirm the meter type is appropriate for the customer profile. Cost: The estimated budget required for this initiative is $100,000 with $50,000 associated with the purchase or rental of high frequency loggers (2-month rental cost of 25 loggers at $1,000 per logger per month) and $50,000 of staff hours (wage estimated at $50 per hour; total 300 hour including 4 hour per site on installation and removal of loggers, 50 hour of administrative and data management, and 50 hour on report writing). 6.4.2 Unauthorized Consumption Unauthorized consumption can occur in many ways and that can be a challenge in controlling it. Every utility experiences some level of unauthorized consumption in their system and the default value set by AWWA is often used to estimate due to its complex nature. For AW, unauthorized consumption volume was estimated to be 183.30 MG/year (valued at $87,821) for the 2022 audit using the default AWWA percentage value. Initiatives recommended to control unauthorized consumption are presented in the following section. 6.4.2.1 SOP Development on Unauthorized Consumption Mitigation Austin is advised to develop an SOP on unauthorized consumption mitigation. Unauthorized consumption occurrences in AW’s system such as open bypass lines and illegal use of private hydrants have been recorded in past investigations. The purpose of SOP is to help Austin identify unauthorized consumption and to develop a procedure for recording and back billing of unauthorized consumption. Scope: Review other utilities’ study on unauthorized consumption mitigation. Analyze the billing database to identify anomalies, verify through field visits, then record and/or back-bill on the billing database. Cost: $35,000 estimated in billing dataset evaluation and field verification for year 1 (2024). If AW chooses to link this initiative with the “Water Services Verification for ICI Properties” project, this cost may be incorporated in the project cost. Annual cost of $10,000 in later years on maintaining and updating the SOP. 6.4.3 Systematic Data Handling Errors Systematic data handling errors refer to any errors that occur between when the meter is read, and the customer is billed. The 2022 water audit systematic data handling errors estimate was 0.001 MG/year. 6-12 6.4.3.1 Billing System Process Evaluation Understanding the billing system workflow from when the meter is read through to when the customer receives their bill is paramount for understanding and reducing this NRW factor. This is true both of automated (AMI/AMR) systems as well as manual read systems such as that currently managed by AW. Understanding this process and identifying any lapses or loopholes that allow apparent losses to occur are fundamental to the management of all apparent loss components. Billing System Process Evaluation Development of Billing System Flowchart Initial Investment $150,000 FY 2026 Total Investment $480,000 FY 2026-2033 Scope: Review the billing processes and develop a meter reading and billing workflow. AW should engage a consultant knowledgeable in both billing system data, integration and NRW. An initial analysis of the possible gaps should be conducted with City staff, including Billing. A report on the potential issues and challenges should be developed and recommendations for improvements included. This should be updated annually. Cost: Will require initial consultant guidance due to the interaction with Billing / CIS and understanding of how this data relates to and affects NRW. Year 1 and Year 2 expectation $150,000 consulting services and $30,000 each year thereafter to provide guidance and training to AW staff on data analysis, management and how the information can be utilized to reduce water loss. AW staff time was estimated at approximately 200 hours per year at $75 per hour ($15,000 per year). 6.4.3.2 SOP Development on Data Handling Errors Mitigation SOP Development on Systematic Data Handling Errors Mitigation Data Handling Errors continues to be a poorly understood apparent loss. The goal of this SOP would be both to better explain what this water loss is as well as to provide guidance on how to monitor and mitigate it. This apparent loss would probably have an initial focus on the register constants the in subsection above. This will also include the recording of water volume evaluation and “waivers” from customer leaks that were forgiven as well as other issues such as data entry inconsistencies, etc. In time this would include validation of data handling anomalies and recording of reasons, plus automation of analysis and monitoring/reporting in the Billing / CIS. Initial Investment $80,000 FY 2027 Total Investment $140,000 FY 2026-2033 (meter multipliers) noted Scope: Develop the Standard Operating Procedure documentation for Data Handling Errors. This document should include explanation of what these data handling errors are, how they should be monitored and guidance on how to reduce/mitigate them. This should be a living document and updated annually with more information. Cost: Will require initial consultant guidance due to the complex and poorly understood nature of this water loss. Year 1 (2027) expectation $80,000 consulting services and $10,000 each year thereafter. AW staff time approximately 200 hours per year at $75 per hour ($15,000 per year). 6-13 6.4.3.3 Advanced Metering Infrastructure Implementation Data Management AMI Data Management Development of SOP Scope: As part of their contract with AW, Aclara Technologies is building a module for District Metered Areas (DMAs) to develop its data management, visualization and monitoring to enable evaluation for this specific are of NRW reduction. Aclara will set up fully metered DMA data structures and to provide AW with methods to monitor and fix any NRW-related anomalies. Once AMI data is collected across the utility, data analysis and guidance can be extrapolated from the DMAs and applied to non-DMA boundaries to analyze meter accuracy. This recommendation is designed to add to that project (which is already budgeted) to allow integration of other systems (such as SCADA or pressure monitoring) to further enable and enhance the data management. Total Investment $375,000 FY 2026-2033 Initial Investment $50,000 FY 2025 Cost: Will require initial consultant guidance due to the complex data sets and back-end data management that would be required. AW would likely have a project manager who would continue after implementation to manage, visualize, and provide operational intelligence out of the dataset. Year 1 and Year 2 (during implementation) expectation $50,000 consulting services and $25,000 each year thereafter to provide guidance and training to AW staff on data analysis, management and how the information can be utilized to reduce water loss. AW staff time approximately 200 hours per year at $75 per hour ($15,000 per year). 6.5 Real Loss Real Loss Recommendations includes initiatives for Leak Detection, Pressure Transients, Software/Event Management, DMAs and PMAs. 6.5.1 Leak Detection – Distribution 6.5.1.1 Optimized Proactive Leak Detection In order to create a true baseline for leakage detection in AW’s system, a full system proactive survey should be conducted over a number of years. These surveys should be continued and expanded to the total system as a first focus. Key Performance Indicators for leak detection should include: Optimized Proactive Leak Detection Annual Investment $250,000 FY 2025 1.13 MGD Saved touched • Time conducting leakage detection. • Miles covered • Appurtenances valves, meters) • Leak noises found • Leaks pinpointed (Separated by: mains, services, hydrants, valves, meters) • Accuracy (% correct vs dry holes) • Technician / crew name (separate hydrants, Additional information may be requested, but this should not significantly slow down the process. 6-14 Once the total system survey is completed, locations of interest reviewed and any found leakage repaired, then additional surveys can be considered. Areas with an elevated amount of leak noise and/or appurtenance leaks should continue to get some level of priority after the first pass as they will be the areas with higher potential leakage. Scope: Conduct a leakage detection survey on all the valves/hydrants/meters in the system (30,985 hydrants + any private hydrants AW has access to). Cost: Year 1 and Year 2 will cost $110,000 and $250,000. Then it will cost $450,000 annually to improve leak detection on the entire system. These costs are associated with the addition of one AW leak detection staff and two external contracted personnel. 6.5.1.2 Repair/Replacement Focus on Service Lines As evidenced by the data in section 5.3.1. AW’s mains experience failures at a lower rate that even “optimized distribution systems,” but AW’s service lines experience failures at a higher frequency than the industry average. Therefore, AW should increase its efforts to replace failing water service lines. Part of this focus will be to determine the areas where service line issues are known to be prevalent and to utilize the data from the proactive leakage detection program (including the District Metered Areas once they are operational) and AMI data for customer-side issues to enhance the analysis. This project would be conducted in collaboration with Proactive Leakage Detection. Repair/Replacement Focus on Service Lines Initial Investment $200,000 FY 2025 0.50 MGD Saved Scope: Determine areas of service line failure risk through data management of leak and AMI data. Field truthing of areas considered as higher risk through the program such as proactively evaluating and replacing lines may be included in the works. Cost: Year 1 and Year 2 will cost $200,000 and $300,000 to conduct data analysis, risk prioritization and validation fieldwork. Once this is completed follow-on work may be considered but is not specified here. These costs do not include the repair of replacement costs that would be associated with any infrastructure changes. 6.5.1.3 SOP Development on Proactive and Reactive Leak Detection SOP Development on Proactive and Reactive Leak Detection AW should develop SOPs for proactive and reactive leak detection to ensure consistency in leak surveys conducted and to allow AW to supervise/oversee contractors. This SOP should include the development of contract language that outlines specific leak detection guidelines such as frequent reporting of performance metrics and determining the most efficient survey routes. It is recommended that detailed line location be conducted, and a correlator used to pinpoint the locations. It is expected that AW (or its contractor) will need to utilize correlators for more complex pinpointing rather than drill and locate. Setting up guidelines like this one can reduce the time repair crews spend on site. Initial Investment $75,000 FY 2025 0.10 MGD Saved 6-15 Scope: Define and implement SOPs (contract language, methodologies, and related equipment) for conducting active (proactive) leak detection, as well as improving leak detection reporting. Seek information and guidance of subject matter experts (leak detection contractors, vendors, consultants, etc.) to match the methodologies with the equipment that AW and its contractors will be using. Cost: Will require initial consultant (or contractor) guidance due to the technical details around the leakage detection equipment and methodologies that would be required. Year 1 (during design and initial implementation) expectation $75,000 consulting/contractor services and $10,000 each year thereafter to provide guidance and training to AW staff on leakage detection equipment and practices and how the infrastructure can be utilized to reduce water loss. A non-exhaustive list of items to include in the SOP is presented below: • Leak detection methods: o Ground microphones o Correlators o Hydrophones 6.5.1.4 Pilot Project with Innovative Leak Detection Technologies Traditional acoustic leak detection is the most widely used real water loss reduction technology adopted in the industry; however, it can be labor intensive with varying results depending on the contractors’ competency and the equipment used. Many innovative leak detection technologies piloted by AW have been introduced in the past years such as satellite leak detection and transient monitoring. This funding would be for similar but emerging technologies that AW hasn’t utilized. Pilot Projects with Innovative Leak Detection Technologies Initial Investment $150,000 FY 2025 0.35 MGD Saved Scope: Pilot projects for AW to explore innovative leak detection technologies. Cost: Year 1 will be an initial investment of $150,000 and a future annual budget of $125,000. It is recommended that AW review the performance of any innovative technologies implemented in the system prior to deploying more. 6.5.1.5 Baseline Leak Detection Validation Many leakage detection programs become less effective over time. This can sometimes be because all the major leaks are found and fixed at the beginning of the program. However, in most cases a drop off in production (of finding leaks) is due to inexperienced technicians being placed on the project and a lack of visibility of metrics to trend and provide visualization into performance. These metrics should be designed to both give AW an understanding of contractor and technician performance, but also to provide feedback to the technician regarding training that should help improve them in their work. 6-16 Scope: This project will utilize initial data from leakage detection work conducted by AW and its contractors to develop trends and key performance indicators at the technician level. These will then be used going forward to benchmark both technicians and companies conducting leakage detection work for AW, plus AW’s own staff if appropriate. Cost: Development of key performance metrics and the monitoring data structures will likely require consultant assistance. Knowledge of leakage detection projects and methods will be optimal for this development. 6.5.2 Leak Detection – Training 6.5.2.1 Annual Leakage Detection Training Leakage detection has been conducted by contractors in the past in AW with varying results. It is anticipated that AW should gain an improved and internal methodologies so that they can supervise and assess the contractor effectiveness. knowledge equipment of Annual Leakage Detection Training Leak Detection Training for new and current employees. Annual Investment $40,000 FY 2025 0.18 MGD Saved Scope: An initial training and annual refreshers for field crews involved in finding and fixing leaks should be conducted. Cost: Approximately $20,000 in Year 1, $40,000 in Year 2, and $20,000 per year thereafter. 6.5.3 Leak Detection – Transmission 6.5.3.1 Vault Evaluation AW should conduct an annual review of all meter vaults, system valves (24” or larger and all blow-off valves), air valves and control vaults to ensure none are leaking or in poor condition, risking failure. This work should also be expanded to include basic asset condition assessment. A tracking system to report vault visits should be developed if one does not already exist. The technician, time and date of inspection, condition information and any follow ups should be recorded. Each site should be visually evaluated, and basic photographs (consistent locations and aspect) taken, and any condition issues documented. All the data should be collected and documented in the field rather than needing to be written up and uploaded back at the office. A suggested frequency for vault inspections is as follows: Meter vaults - every 6 months Control vaults - every 6 months Critical air valve vaults - every 2 years Valve vaults - every 5 years All critical air valves and valve vaults should be visited in the first two years of the program. This will provide a baseline with which to determine future frequency of inspections. Vault Evaluation Leak Detection – Transmission Annual Investment $100,000 FY 2025 0.16 MGD Saved 6-17 Scope: Review of 50% of all vaults in Year 1, then annual review of 25% of vaults thereafter. AW should also develop a tracking system to record vault visits. Cost: The annual budget will be determined by the number of sites visited and this would be considered after the first year of analysis. A placeholder cost of $100,000 annually was assumed. 6.5.3.2 Large Diameter Leak Detection Transmission mains generally do not leak as much (number of leaks, not volume of leaks) as distribution mains or service lines, however, when they do, the volume of leakage can be significant, but it is typically only for a short duration. Acoustic leak detection method is difficult to apply on transmission mains for several reasons: the mains are deeper, they do not have as many fittings at the surface to allow for use of acoustic equipment, and they tend to attenuate acoustic leakage signals due to their large pipe sizes. Large Diameter Leak Detection Leak Detection - Transmission Annual Investment $800,000* FY 2025 0.22 MGD Saved The recommended approach is to place leak detection equipment (Sahara and SmartBall shown in Error! Reference source not found.) into the transmission lines. Sahara uses a tethered parachute (upper image) to navigate through the flow and can be deployed even in no flow conditions. SmartBall (lower image) is a free-swimming tool and can accommodate low flow conditions. Both tools can be used without interrupting the service. These are good tools with a long track history. However, they are also comparatively expensive and should be used sparingly for targeted locations and for specific reasons. Scope: Specific problem areas of large diameter main should be evaluated. For example, it was noted that the Jollyville transmission main from Handcox WTP to the Jollyville reservoir could be contributing to large quantities of real losses, as the line runs deep and leaks would not present on the surface. A plan for leakage detection should be considered and if appropriate, developed and implemented. Figure 6-2 Sahara and SmartBall 1 Cost: AW is currently budgeting $1 million annually on large diameter leak detection. The recommended costs of $800,000 is a re-evaluation of AW’s current large diameter leak detection costs. Tethered equipment uses a parachute and neutral buoyancy to allow the acoustic sensor to travel down the main. The finite range of these units is about 2,500 feet per insertion with perfect conditions. This will be significantly reduced if there are any bends in the main tested or if the flow reduces below 1 foot per second. Generally, the units will cease forward movement after 270 degrees of bends, or at flows less than 0.5 feet per second. Since these works are relatively costly) it would be prohibitively expensive to conduct this analysis on the whole length of pipeline every year. There are also additional costs associated with insertion and extraction which need to be included in any cost analysis. Obviously one major break can have a huge effect downstream so this needs to be addressed, but the expectation is that there are relatively few leaks on the largest mains and so extensive assessments would not be cost effective. 6-18 6.5.4.1 Utilize High Frequency Loggers and Develop Pressure Transient Models 6.5.4 Pressure Transients AW has previously experienced pressure transients which caused major breaks. To improve pressure transient monitoring, AW should conduct research, purchase, and install transient monitors in selected locations within the system. The goal is to build up a signature of events such as valve closures, water usage, and breaks, among others. By adopting these measures, AW can gain insight into the behavior of the system, identify potential issues before they escalate, and improve the response time to incidents. Utilize High Frequency Loggers and Develop Pressure Transient Models Implementation and data analysis of loggers and pressure transient monitors Initial Investment $195,500 FY 2026 0.21 MGD Saved This approach can lead to better water resource management, reduced water loss, and improved customer service. An example of monitoring for pressure transients is provided in Figure 6-2. Figure 6-2 Pressure Transient Monitoring Example The data generated should be integrated with SCADA where appropriate to better understand the flow and pressure dynamics within the system. Scope: Research pressure transient monitors and pilot locations. Purchase and implement 5 pressure transient monitors. Analyze and monitor pressure transient data monthly and set automated alerts to monitor and report on specific transient events. Cost: Initial Cost of $195,500 in Year 1, $125,000 Year 2, and an annual cost of $40,000 each year after. 6.5.4.2 Monitor Pressure Relief Valves (PRVs) AW already has a number of PRVs in its system to manage pressure and to delineate pressure zones. All these sets of infrastructure provide locations to monitor pressure, flow and transients. The data generated should be integrated with SCADA where appropriate to better understand the flow and pressure dynamics within the system. Scope: Research AW’s PRV infrastructure and develop requirements to create and enhance a monitoring Monitor Pressure Relief Valves (PRVs) Initial Investment $50,000 FY 2025 0.10 MGD Saved 6-19 network focused on the PRVs. Purchase and implement pressure monitoring equipment to provide information to AW’s SCADA system. Analyze and monitor pressure data actively once available and set automated alerts to monitor and report on specific pressure or flow events at the PRVs. Cost: Initial Cost of $50,000 in the first year, and an annual cost of $20,000 each year after. 6.5.5 Software and Event Management 6.5.5.1 Enhance AW Enterprise Power BI Reports (Leak Detection) To truly understand and improve real loss management, some level of automation and active alerting when parameters change significantly is necessary. This is paramount within DMAs for example so that any leaks can be reported quickly and dealt with before they become a problem and result in a larger outage. It does, however, require active datasets to be managed and in the context of real loss this would generally mean flow and/or pressure (pressure transient data as an example) datasets. Therefore, this would be a program that would be initiated after some of the previously mentioned programs that set up relevant data streams are active. Scope: Once relevant streaming datasets are available, AW staff should review available event management software and determine the value for this kind of software going forward. If the value proposition is good enough, then AW should purchase or develop an RFP to allow competitive bids and make a selection. Cost: Cost will depend on the amount of data incorporated and the functionality of the system, so that cost is not discussed here. There would be a component of staff time to review available data and research the possible software. Estimate of 200 hours at $200/hour for this review. Approximately $75,000 for this activity in Year 1, with an annual cost of roughly $27,000 thereafter. 6.5.5.2 Integration of SCADA, AMI, GIS, Logger Detection Software Whether AW purchases event management software or not, there will still most likely be a need for integrating relevant datasets to make the analysis and monitoring of non-revenue water more efficient and proactive. Automation of the water audit by matching the water purchases versus the sales to city customers can be done even with monthly or bi-monthly data. Integration with other datasets such as contractor and/or internal leakage detection records, work orders, GIS etc. should also be included in this recommended strategy. Scope: Staff time for integration of import and customer metering data to enable a more automated water audit and non-revenue water analysis. Cost: Anticipate approximately 200 hours in staff time at $200 per hour to conduct metering integrations and approximately 80 hours per year to keep the system maintained – $140,000 in Year 1 and $35,000 each year afterwards. 6-20 6.5.6 District Metered Areas (DMAs) and PMAs 6.5.6.1 Develop Methodology to Improve DMA Usefulness Scope: Develop a standard on DMA implementation and data management. AW continues to pursue DMAs in conjunction with AMI and standardize the methodology on the implementation and management. When creating this standard document, AW should consider automation of flow data with alerts set up to notify AW (or contractors) of potential leak events. AW should also set a standard on the frequency in which flow data is gathered. AWWA M36 guideline provides good information on how DMAs should be implemented and managed. Cost: $30,000 consulting plus $30,000 AW staff cost. 6.5.6.2 Consider up to 5 Temporary DMAs Following the standard developed in the previous initiative, Austin should consider implementation of 5 Implementation of in FY2025. temporary DMAs temporary DMAs are proposed to be conducted every two years, with data analysis and review conducted annually. By conducting a thorough review and making the necessary adjustments, Austin can enhance the success rate of DMAs, resulting in better water resource management and reduced water loss. Consideration of up to 5 Temporary DMAs Cost of DMA equipment, implementation and data analysis Initial Investment $200,000 FY 2025 0.64 MGD Saved Scope: Implementation of 5 temporary DMAs every two years, starting in FY2025. Annual evaluation and review of temporary DMA data. Cost: Total cost of $200,000 in Year 1 (2025). $310,000 in Year 2. 6.5.6.3 Consider Permanent DMAs and PMAs Depending on the outcome of temporary DMAs, AW may want to implement permanent DMAs or Pressure Management Areas (PMAs). The data from temporary DMAs can be analyzed to flag any problematic areas that might be worth incorporating permanent flow meters to. DMAs can be converted into PMAs with the addition of pressure reducing valves. A major benefit of PMAs is the ability to monitor and minimize pressure transients with the opportunity to reduce leakage by decreasing the pressure of the area. A hydraulic model exercise should be conducted prior to PMA implementation to assess the impact of pressure variations in the system. Scope: Consider permanent DMAs and PMAs depending on the outcome of temporary DMAs evaluation. Cost: To be determined once decision is made on permanent DMAs and PMAs. 6.6 Unbilled Authorized Consumption The plan consists of initiatives on Flushing, Fire Fighting, and other Unbilled Unmetered Accounts. 6-21 6.6.1 Flushing AW already monitors flushing volumes and records this information. AW should continue to refine the best locations and volume measurement methods and monitor and meter flushing volumes, and review and establish trends of flushing volumes. Comparison of flushing volumes with total system volumes should also be performed to improve volume evaluation for the 2023 water audit and for establishing recommendations for reducing volume flushed if appropriate. 6.6.1.1 Conduct Metered Analysis of Flushing Volumes AW should research and purchase additional logging units and/or meters to enable more active measurement and analysis of flushing volumes. AW should consider using cellular AMI systems to fit on the meter register to allow active reading of meters rather than manually reading these sites. Scope: Research and report upon best equipment to monitor flushing volumes. Purchase relevant logging units and/or meters and install and set up automated monitoring. Staff should review and analyze data on a regular (monthly) basis and report at least every quarter. Cost: To be determined depending on how many flushing locations might need a meter and how many similar flushing cycles various locations have. 6.6.2 Fire Fighting To resolve unbilled authorized water uses with the fire department, it is suggested to work with Austin Fire Department to set up a method for monitoring fire truck usage and install meters in fire department testing locations. A methodology to estimate non-metered volumes and a review of hydrant valve exercising may also be necessary. However, it is not expected that firefighters will need to spend extra time monitoring flows. 6.6.2.1 Update Fire Department Usage Expectations and Measurement Needs The Fire Department usage is an important component of the unbilled authorized water audit component. If possible, the uses should be measured, but this should also not get in the way of any dedicated firefighting. An SOP was developed for Fire Department Usage in 2013 but changes in the system require an update to this SOP. Standardizing operational practice will need to be evaluated in collaboration between the Department and AW to work out the most effective way to measure water use without affecting the services provided by the Fire Department. Scope: Conduct meetings with the Fire Department to discuss potential best practice for metering and the possibilities for reducing Fire Department workload through proactive metering. This work will guide any purchases for metering or logging systems. Cost: Staff time to discus and report upon the needs of both groups and recommendations for metering and/or estimation of Fire Department uses going forward. Anticipate 240 hours at $100 per hour. $24,000 in Year 1 and no other costs. 6.6.3 Unbilled Unmetered Accounts AW does not have any recorded unbilled unmetered accounts. 6-22 6.7 Annual Water Audit and Validation Training Water Audit training was conducted in 2022 by AW and through consulting services as part of this project in 2023. It is recommended that AW utilize a third- party to validate the annual water audit training. It is a valuable annual reminder partly because AW staff have many other tasks and there will probably not be a single staff member who is totally focused on non- revenue water management. Scope: An annual refresher should be coupled with validation of each year’s audit during the period of this contract. However, it should be continued every year thereafter as well. This cost assumes five to six staff from Engineering, Operations, and Finance/Customer Experience. Cost: Approximately $10,000 per year. 6.8 Participation in National Water Loss Control Conferences Water Loss Control is a relatively niche water utility business area, but it does have dedicated subject matter expert community and there are active conferences and workshops. The American Water Works Association (AWWA) puts on a “North American Water Loss” conference every two years. The next one (at the time of writing) will be in December 2025. In addition, the AWWA Annual Conference and Water Infrastructure Conferences, plus the Water Smart Innovations conference all have water loss components. The International Water Association (IWA) also has a very active Water Loss Control Task Force which is active in Canada. The possibilities for learning are extensive, but utility participation is always welcomed, and AW would be able to both showcase their work, but also gain from the expert community that would be present. As an example, Halifax Water (NS) has become a major player in both the AWWA and IWA water loss organizations. They have both gained from the expertise and become recognized as a world-leading utility in water loss control over the past 20 years. Scope: AW should continue to send at least one person (directly connected to the water audit and water loss control work) to the North American Water Loss conference and preferably the water loss sessions at the AWWA annual conference each year. If the IWA conferences are held in the US or Canada in any year, then these should be considered as well. The staff sent should work toward presenting Austin-specific projects in 2025 and beyond. Cost: Approximately $5,000 per year for travel, accommodation, and time (salary) of the individual sent. Improve Data for Water Audit Input Data Validity Scores 6.9 Based on the findings from various NRW control initiatives in this strategy, AW should update the AWWA water audit input data as they gain a better understanding of the NRW in the system through the initiatives. This can include updating the customer metering inaccuracy percentage value based on the meter testing 6-23 for results and assigning custom values unauthorized consumption if deemed necessary. The audit should be considered as a “living document” and a viable tool for overall water loss control planning. AW can take this opportunity to improve on the audit data validity score by updating the audit based on field findings. Additional review should be conducted annually to evaluate other areas where data validity could be improved by actively assessing the gradings as part of the annual water audit process. Scope: Annual review and update of AWWA water audit document based on the results of NRW control initiatives. Cost: $10,000 per year (133 hours of AW staff at $75 hourly wage). 6-24 6.10 Cost Estimate Tables Table 6-6 Apparent Loss Strategy Costs 6-25 Table 6-7 Real Loss Strategy Costs 6-26 Table 6-8 Real Loss Strategy Projected MGD Savings 6-27 Table 6-9 Unbilled Authorized Consumption Strategy Costs 6-28 A Appendix A: Austin 2022 Component Analysis Step 1: BACKGROUND LEAKAGE, REPORTED LEAKAGE AND UNREPORTED LEAKAGE FROM RESERVOIRS Instructions: First enter the capacity of all distribution system reservoirs and tanks in use during the audit period. In case the system input volume is based on raw water meters located upstream of the Water Treatment Plant (WTP) then also include the capacity of the WTP reservoirs. Next select a reservoir background leakage rate - either the default value provided by the model or a utility specific flow rate. If reservoirs and tanks are well maintained and the utility does not suspect any background leakage from the reservoirs and tanks then enter zero as the utility specific flow rate. In case a reservoir or tank was reported leaking or has overflowed, enter the estimated volume in cell G27 . If a proactive investigation/inspection of the system reservoirs and tanks has discovered a leaking reservoir or tank then enter the estimated annual volume lost in cell G28. Capacity (MG) Background Leakage Rate (gpm/MG) Annual Volume (MG) Select Reservoir Background Leakage Rate Reported Reservoir Leakage and any recorded Reservoir and Tank Overflows Total Reservoir/Tank Capacity Unreported Reservoir Leakage 0.25 0.00 0.70 OR Total Background Leakage, Reported and Unreported leakage from Reservoirs 0.70 0.25 (gpm/MG) - (gpm/MG) Figure A-1 Step 1; Background Leakage, Reported Leakage, and Unreported Leakage from Reservoirs A-1 A Figure A-2 Background Leakage on Mains and Services A-2 Mains by Size Diameter 2'' Diameter 3'' Diameter 4'' Diameter 6'' Diameter 8'' Diameter 10'' Diameter 12'' Diameter 14'' Diameter 16'' Diameter 18'' Diameter 20'' Diameter 24'' Diameter 30'' Diameter 36'' Diameter 42'' Diameter 48'' Diameter 54'' Diameter 60'' Diameter >60'' Other Diameter A STEP 3A: REPORTED FAILURES ON MAINS Instructions: Enter the total number of failures by main size that were reported to and repaired by the water utility during the audit period in cells C58 to C77. Next enter the total length of mains for each mains size group in cells D58 to D77 (Note: this information is not required for the real loss component analysis but serves to calculate failure frequencies by mains size). Next enter the average awareness duration for reported failure events by mains size in cells I58 to I77 (Awareness duration is the average time from the occurrence of the failure event until the water utility becomes aware of its existence). Next enter the average duration of locating and containing reported failure events by mains size in cells K58 to K77. Next select either the default average leak flow rate provided by the model in cells P58 to P77 or select and enter your own utility specific average leakage flow rates in cells Q58 to R77. Average failure flow rates are based on AWWA M36 recommended flow rates and flow rates collected by the research team Number of Leaks & Failures per Year Length of Main Failure Frequency Average Failure Flow Rate @ (number / 100miles / yr) Average System Pressure Average Pressure N1 (Leakage- Pressure Exponent) Value (gpm) (psi) (days) (days) (MG) (MG) Average Failure Duration Average Awareness Duration (days) Average Duration for Location and Repair/Shutoff Failure Total Duration Average Annual Loss per Failure Total Annual Loss Use Default Average Failure Flow Rate Use Utility Specific Average Failure Flow Rate 27 14 196 81 27 1 miles 58.8 2.5 76.4 0.1 24.5 31.7 58.7 21.1 13.5 2.5 24.3 0.0 46 13.90 78.0 - 13.90 78.0 18 44.00 78.0 1,100.2 18 35.00 78.0 1,314.9 6 35.00 78.0 6.3 - 35.00 78.0 672.9 4 35.00 78.0 7.4 13 222.00 78.0 281.9 - 222.00 78.0 - 222.00 78.0 - 222.00 78.0 - 222.00 78.0 - 222.00 78.0 - 222.00 78.0 100.9 - 222.00 78.0 - 222.00 78.0 - 222.00 78.0 - 222.00 78.0 - 35.00 78.0 1.00 1.00 1.00 1.00 1.00 1.00 1.00 1.00 1.00 1.00 1.00 1.00 1.00 1.00 1.00 1.00 1.00 1.00 1.00 1.00 30.00 30.00 7.00 1.00 1.00 1.00 1.00 1.00 1.00 1.00 1.00 1.00 1.00 1.00 1.00 1.00 1.00 1.00 1.00 1.00 3.04 33.04 0.74 19.90 30.00 - - 2.06 9.06 0.64 8.96 1.45 2.45 0.12 24.20 1.41 2.41 0.12 9.84 1.00 - - 1.57 2.57 0.13 3.50 2.46 3.46 1.23 1.23 1.00 - - 1.00 - - 1.00 - - 1.00 - - 1.00 - - 1.00 - - 1.00 - - 1.00 - - 1.00 - - 1.00 - - 24 194.6 12 222.00 78.0 3.76 4.76 1.70 40.69 Figure A-3 Reported Failures on Mains 1.00 - - Enter avg flow rate 35.0 SUB-TOTAL REPORTED FAILURES ON MAINS 108.32 Average Failure Flow Rate @ Average System Pressure (gpm) - - 22.0 35.0 35.0 35.0 35.0 - - - - - - - - - - - - A-3 A STEP 3B: REPORTED FAILURES ON DISTRIBUTION SYSTEM APPURTENANCES Instructions: Enter the total number of failures by distribution system appurtenance type that were reported to and repaired by the water utility during the audit period in cells C86 to C89. Next enter the total number of appurtenances for each system appurtenance group in cells D86 to D89 (Note: this information is not required for the real loss component analysis but serves to calculate failure frequencies by appurtenance type). Next enter the average awareness duration for reported failure events by system appurtenance type in cells I86 to I89 (Awareness duration is the average time from the occurrence of the failure event until the water utility becomes aware of its existence). Next enter the average duration of locating and containing reported failure events by system appurtenance type in cells K86 to K89. Next select either the default average leak flow rate provided by the model in cells P86 to P89 or select and enter your own utility specific average leakage flow rates in cells Q86 to R89. Average failure flow rates are based on AWWA M36 recommended flow rates and flow rates collected by the research team. System Appurtenances by Type Average Failure Duration Number of Failures per Year Total Number of Appurtenances Average Pressure N1 (Leakage- Pressure Exponent) Value Failure Frequency Average Failure Flow Rate @ Number of Failures per 1000 Appurtenances 70psi Average Awareness Duration Average Duration for Location and Repair/Shutoff Failure Total Duration Average Annual Loss per Failure Total Annual Loss Use Default Average Failure Flow Rate Use Utility Specific Average Failure Flow Rate (gpm) (psi) (days) (days) (days) (MG) (MG) Hydrants Valves Meters 18 20 144 30,985 1 3.50 78.0 7,700 3 6.90 78.0 235,000 1 0.25 78.0 1.00 1.00 1.00 1.00 182.00 182.00 182.00 182.00 0.90 182.90 1.03 18.49 5.66 187.66 2.08 41.55 0.58 182.58 0.07 10.55 SUB-TOTAL REPORTED LEAKS ON SYSTEM APPURTENANCES 70.59 Other (e.g. Blow-offs, etc.) - 6.90 78.0 182.00 - - Enter avg flow rate 6.9 Figure A-4 Reported Failures on Distribution System Appurtenances STEP 3C: REPORTED FAILURES ON SERVICE CONNECTIONS Instructions: Enter the total number of failures by service connection size (<1" or >=1") that were reported to and repaired the water utility during the audit period in cells C98 to C99. Next enter the total number of service connections for each service connection size group in cells D98 to D99 (Note: this information is not required for the real loss component analysis but serves to calculate failure frequencies by service connection size group). Next enter the average awareness duration for reported failure events by service connection size group in cells I98 to I99 (Awareness duration is the average time from the occurrence of the failure event until the water utility becomes aware of its existence). Next enter the average duration of locating and containing reported failure events by service connection size group in cells K89 to K99. Next select either the default average leak flow rate provided by the model in cells P98 to P99 or select and enter your own utility specific average leakage flow rates in cells Q98 to R99. Average failure flow rates are based on AWWA M36 recommended flow rates and flow rates collected by the research team. Service Connections by Size Number of Failures per Year Total Number of Service Connections Average Pressure N1 (Leakage- Pressure Exponent) Value Failure Frequency Average Failure Flow Rate @ Number of Failures per 1000 Service Connections 70psi Average Failure Duration Average Awareness Duration Average Duration for Location and Repair/Shutoff Failure Total Duration Average Annual Loss per Failure Total Annual Loss Use Default Average Failure Flow Rate Use Utility Specific Average Failure Flow Rate (gpm) (psi) (days) (days) (days) (MG) (MG) Services < 1'' Services >= 1'' 1,056 86 225,347 5 6.90 78.0 25,038 3 13.90 78.0 1.00 1.00 45.00 45.00 1.58 46.58 0.52 544.59 2.20 47.20 1.05 90.53 SUB-TOTAL REPORTED LEAKS ON SERVICE CONNECTIONS 635.13 GRAND TOTAL REPORTED FAILURES 814.03 Figure A-5 Reported Failures on Service Connections Average Failure Flow Rate @ Average System Pressure (gpm) - - - Average Failure Flow Rate @ average system pressure (gpm) - - A-4 A Figure A-6 Unreported Failures on Mains A-5 A Figure A-7 Unreported Failures on Distribution System Appurtenances Figure A-8 Unreported Leaks on Service Connection A-6